2019 Pharma Innovation Awards
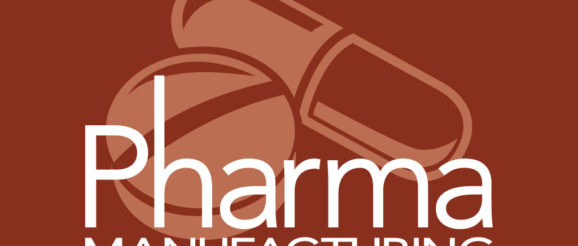
Ironically, the phrase used to praise an innovative new product — “the greatest thing since sliced bread” — has become so unoriginal that it’s cliché.
In the 1920s, however, the convenience of commercialized pre-sliced bread was what the American food consumer wanted — and after the first machine appeared in 1928, equipment manufacturers and bakery industry experts got to task, improving and adding to the existing designs.
This forward leap in the baking industry could not have happened without rethinking what equipment can do, and the persistent efforts of those looking to incrementally improve on this innovation.
Here at Pharma Manufacturing, we understand and appreciate the investment pharmaceutical equipment vendors put into developing and improving their products. All types of innovation, whether earth-shattering or incremental, should be recognized. This month’s cover story is a tribute to those who listen to the needs of the market and their customers, and a result, have distinguished themselves as leaders in pharmaceutical equipment and technology.
With that said, we are proud to introduce this year’s Pharma Innovation Award winners: recently launched or updated technologies and systems that, based on their technical and practical merits, were selected by Pharma Manufacturing’s editors and reviewers.
It’s an exciting time of growth for biopharmaceuticals. The number of biopharma players, marketed products and classes of therapies continues to expand. With this expansion comes new demands for the industry. Intuitive vendors are recognizing that their biopharma customers are juggling regulatory uncertainty, cost pressures, and growing pipelines of molecules.
Univercells’ NevoLine platform
As much of the industry is looking towards more continuous manufacturing and more modular construction, our bioprocessing category winners are those who are helping their customers meet these challenges — offering solutions that are compact, flexible and speed products to market.
Our first winner truly embraces the idea of next-generation bioprocessing. MilliporeSigma has a reputation for listening to its customers and developing products accordingly, and the BioContinuum Platform delivers on that promise.
Next-generation bioprocessing is about targeting high productivity, high intensity processes. This platform is a unique and holistic approach to next-gen bioprocessing that allows users to realize the benefits of process intensification throughout the entire process. The platform is an evolving and convergent portfolio of advanced processing and software, automation and analytics technologies, applications and expertise that will enable customers to confidently enter this new era of manufacturing.
What makes it especially flexible is that MilliporeSigma recognized that not all biomanufacturers are on the same path. For some, the focus is on improving unit operation’s interoperability. For others, the goal is fully continuous processing. No matter what your path, the BioContinuum Platform aims to provide the building blocks for success.
Our next winner is the result of two industry vets teaming up. IPS-Integrated Project Services and G-CON Manufacturing collaborated to produce the ÜBERcellFLEX — a pre-fabricated modular cleanroom infrastructure for the manufacturing of autologous cell therapies.
Available in both 12- and 24-foot wide POD configurations, the processing suites enable faster and more predictable project schedules for new facility construction and a standardized solution to meet speed to market requirements — filling a major need in the cell therapy arena. Multiple units can be installed to scale up/out from phase one clinical production to commercial manufacturing. The PODs can also be ready to order, in either open or closed-processing format, with little engineering time and no additional engineering when PODs are reproduced as part of scale up.
ÜBERcellFLEX is part of the iCON product line, which also offers platforms for other applications, including fill/finish and monoclonal antibodies.
Our final winner is a newer kid on the block. Univercells announced the commercial launch of its proprietary NevoLine bioproduction platform for vaccines in early 2019. The technology platform was developed by Univercells, and was part of a $12 million Grand Challenges grant awarded by the Bill & Melinda Gates Foundation to apply it for the production of affordable inactivated polio vaccines (sIPV).
By designing integrated process architecture to reach miniaturized, high-capacity production capabilities, the NevoLine platform enables sustainable and flexible production. Through intensification and chaining of unit steps into a continuous process, users achieve high yields with less time and money invested.The system is self-contained into a 10m² series of isolators. To put it in perspective, a facility designed with four NevoLine units would deliver up to 50 million sIPV doses per year for an estimated capital cost of $20 million.
The company also recently announced it had been awarded a second grant by the Bill & Melinda Gates Foundation and will be adapting the process design of the NevoLine platform to deliver affordable measles and rubella vaccines.
Smart pharma gives biopharma a run for its money in the competition for the industry topic with the most hype (and certainly wins for the most buzz words). Industry 4.0, digital transformation, IIoT — whatever terms you want to use, the movement toward a more digital industry is slowly but surely underway. But there are still significant hurdles that need to be overcome for the benefits of digitalization to be captured across the highly regulated, traditionally risk-averse pharmaceutical industry.
Piab’s piLIFT SMART
The concept of smart pharma is broad and the winners in this category run the gamut from virtual reality to material handling, but all are united by the integration of smart technology into their products to help manufacturers on their digital transformation journeys.
As pharma looks to build sustainable digital manufacturing solutions, two challenges they face are making data generated by legacy assets and operational technology (OT) systems ready for artificial intelligence (AI) and acquiring the right data science and programming skills. To this end, the first winner in this category comes from Quartic.ai — a newcomer founded by a veteran team of process manufacturing and data scientists determined to make AI deployment easy.
The Quartic Platform delivers on this mission, offering an AI-powered smart manufacturing platform built specifically for OT users. Operating on the premise that AI application can only deliver results for manufacturing if it is built and used by those who understand the manufacturing equipment and processes best, the new platform looks, feels, and behaves like the OT systems with which manufacturing experts are familiar.
The platform, which supports distributed deployment at the Edge, Fog and Cloud, is comprised of two key components: the Quartic illuminator — an IIoT data pipeline that dynamically creates asset context for data from IIoT, OT, MES and ERP information and makes its analytics ready; and the Quartic eXponence — an engine that creates asset intelligence through advanced analytics combined with the power of automated machine learning.
Next up is another example of a company that used its expertise to develop a product specifically suited to fill a need in the pharma industry. The Virtuosi education platform is the brainchild of Quality Executive Partners (QxP), a management and compliance consulting company.
Virtuosi is an educational platform, featuring multifaceted digital technologies including immersive virtual reality (VR) interactive experiences. Digital courses, called “episodes,” include knowledge and process checks across a progression of topics. The powerful impact of VR on enhanced learning is based in behavioral learning theory. Interactive immersive VR experiences with the body and not just the mind allows learning to be embedded into the long-term memory centers of the brain, increasing recall.
Software containing the digital courses are downloaded from a central server, allowing continuous updates as regulations and life science technology changes. Each VR workstation includes a high-speed gaming computer, virtual reality headset and hand controllers, and two motion sensing devices. The first series available focuses on sterile products manufacturing and microbiology, but future series will offer education in regenerative medicine,, biotech, combination products, solid dose, semi-solid and liquid products, and APIs.
Manufacturing excellence requires fully digitized production records and processes so that all departments can seamlessly be connected. Yet, survey after industry survey reveals that most pharma production environments still depend on error prone paper-based production records, contributing to poor resource utilization, inefficient processes, higher deviation rates and delayed product releases.
MasterControl’s new Manufacturing Excellence solution (so new that is still has that new software smell) aims to bridge the gap between operational excellence and smart manufacturing by automating the last mile of production. The software enables manufacturers to remove remaining paper from the shop floor to ensure that production record reviews and releases are fully digital, connected and accelerated. The cloud-based solution eliminates preventable errors, long review cycles and costly waste created by manual data entry processes.
The Manufacturing Excellence solution has a patent-pending builder tool allowing organizations to configure the digital solution to their existing processes, streamlining both implementation and adaptability. The builder tool houses the global elements of the manufacturing processes, allowing users to update once and have information propagated throughout the system.
HERMA US’ HERMA 500
Ceremoniously bumped out of the packaging category, our next winner offers an incremental, yet important next step in labeling technology. Helping the packaging sector take strides towards adopting smart factory technologies, the HERMA 500 label applicator from HERMA U.S. is an IIoT-enabled machine utilizing real-time metrics to optimize production efficiency and consistency, even in a multi-factory setting.
The next-generation label applicator builds upon its predecessor’s best features and integrates Industry 4.0 connectivity. Remote access via web browsers allows for off-site operation and, on-site, the machine’s user interface displays intuitive pictograms on a 4.3-inch touchscreen. A variety of optional upgrades can be accessed by simple code activation, and the unit’s firmware is automatically uploaded via ethernet.
Fittingly, the machines are being produced in HERMA’s new state-of-the-art Labeling Machinery Division facility, recently relocated to its headquarters site in Germany.
Our final winner also brings smart technology to new areas in pharma. Touting itself as the market’s first Industry 4.0 ready vacuum lifter, PIAB’s piLIFT SMART delivers on the promises of Industry 4.0. by offering smart data features based on internet connectivity.
Sensing and monitoring movements and responding quickly to user intentions, the vacuum lifter will lift and weigh loads simultaneously, collect and log data, making process statistics and analyses immediately accessible to the user through web platform log-in.
With capacity to lift objects weighing 90 pounds, the piLIFT SMART offers top-notch vacuum lifting technology to customers in a broad range of industries.
Monitoring and analytical devices
As one of the world’s most heavily regulated industries, pharma has always required accuracy, reliability and repeatability. Today’s complex products are driving new trends in manufacturing, such as single-use and continuous. This transformation requires new points of measurement delivered by improved instrumentation.
Our first nod in this small but vitally important category goes to Endress+Hauser’s iTHERM TrustSens, touted as the world’s first self-calibrating temperature sensor. New quality standards in biopharma mean calibration of critical measurement points is typically required every six to 12 months. E+H’s technology makes it possible for a sensor to perform a self-calibration that will automatically detect drift and determine if manual attention and adjustment is warranted. This can significantly reduce risk and increase efficiency for the facility.
Endress+Hauser’s iTHERM TrustSens
The technology relies on the Curie point physics principle and fixed-point calibration method normally employed in lab environments. It enables reliable, secure automated calibration monitoring and electronic record management, including record creation, archiving, and transmission as specified in the FDA 21 CFR Part 11 — effectively eliminating the need for manual intervention.
A facility’s calibration monitoring solution can be comprised of up to 20 iTHERM TrustSens TM371 or TM372 temperature sensors, all connected via HART communication.
Sharing the accolades in this category is Emerson’s Rosemount 550pH sensor.
As the industry shifts from traditional stainless-steel bioreactors to disposable plastic bags, facilities need reliable sensors for vital liquid analysis. Pharma wants the flexibility of single-use methods, but also wants to achieve process control in the same way as with stainless-steel methods, with no degradation in performance. Emerson, with a long history of producing innovative technology, has stepped in provide a possible solution.
The 550pH sensor is an electrochemical, fully disposable device with sensor stability of less than 0.005 pH change per day verified by extensive testing. The single-use sensors perform as well as or better than those used in stainless-steel bioreactors. Wherever possible, Emerson maintained industry-standard designs, eliminating the need for additional training. Added features, such as wet storage, overcome challenges that have long been plaguing single-use processing.
Facilities can now experience all the benefits of single-use bioreactors without having to compromise in liquid analytical instrumentation.
Plant operations
When it comes to operational excellence, the plant floor offers immense opportunity for companies looking to gain a competitive edge. The winners in this category bring significant improvements in efficiency and flexibility, with an even stronger focus on quality and safety.
Interestingly enough, despite the current buzz surrounding biopharmaceuticals, all of the plant operations winners are related to tablets and capsules. The fact that new advancements are still being made in solid dose is no doubt a contributing factor to the sector’s longevity.
Kicking off this category is one of the more unique technologies in this year’s group of winners. The use of high potency active pharmaceutical ingredients (HPAPIs) is increasing, as pharma strives to focus on developing more targeted, effective treatments. This means manufacturing often involves handling toxic or highly sensitive solids that can pose a direct threat to worker safety. Rommelag, who you might recognize as the first company to introduce blow-fill-seal technology to the U.S., has stepped up to the plate with its Flecotec single-use containment system, enabling consistent containment from API to production.
The system’s core components consist of the company’s Flecozip and Flecotric. Flecozip acts as the contamination-free interface between process units and containers, while Flecotric makes it possible to adapt the system to virtually all common equipment and processing units.
Allowing for both primary containment to the mid-nanogram levels, as well as secondary
containment with similar or increased performance, the system has been installed in new applications as well as used as a direct replacement for lesser performing, existing equipment. In addition, because Flecotec is all about single-use containment, once a process step has been completed, the entire system is simply disposed of — keeping cleaning and validation to a minimum. The system reliably protects workers and the product from contamination, while also allowing protective clothing to be eliminated in many work areas.
Qualicaps’ QUALIS-UVS laser printer
Making its colorful world premiere at Achema 2018, Fette Compacting’s FEC20 capsule filling machine allows each individual capsule filling process step to be controlled and monitored separately. With this machine, the company has adapted and further developed the technical concept of its FEC40 unit (released in 2016) in order to make it available for medium-sized batches of up to 200,000 capsules per hour.
Prior to the FEC series, the assemblies in capsule filling machines were controlled by mechanical coupling. By using servo and torque motors, the new machine decouples individual process steps. What this means is that optimal parameters for each process step can be defined, thereby improving both quality and output per time unit. The machine’s database contains all formulations and user process parameters, while the system automatically and immediately examines each entry for consistency.
Next we have Key International’s Enclony PLANET 6G, a state-of-the-art, high-speed automatic tablet and capsule visual inspection machine. The inspection machine’s 10 interdependent 2D cameras and two additional 3D cameras take 14 pictures of every tablet or capsule that passes through the machine, checking them back to a “golden” image. Each tablet is captured from eight precise angles, eliminating blind spots. Defects are compiled so that users can improve their process.The patented removal system of the tamping pin station together with the hygienic design reduces the time for a changeover. This enables the user to swiftly change between products as well as between dosing methods.
The Enclony’s jam free sorting, smart HMI, humidity and temperature sensor, and four-sided wing door capability enable it to produce as many as 350,000 tablets per hour and 150,000 capsules per hour. Key says that the machine can be programmed for new products in just 30-35 minutes, as the intuitive Smart HMI guides the operator thorough the process. Additionally, the company boasts that the machine can cover 95 percent of product sizes and shapes on market with the tools included.
Closing out this category is Qualicaps’ QUALIS-UVS laser printer. A viable alternative to traditional ink printing, UV laser imprinting has many benefits, including the elimination of defects caused by ink, flexible design options, operational efficiency and larger print surface.
Qualicaps, perhaps most well-known for its range of capsule offerings, has proven that it can also offer innovation in laser printers. The QUALIS-UVS imprints on tablets or capsules at a speed up to 400,000 per hour — the company boasts this is one of the fastest UV laser printers in the world. The new machine is more compact than the company’s existing UV laser printer (LIS-250D), includes a built-in blower, and requires fewer change parts. Marking letters, marks or logos can be made by CAD software, allowing for flexibility in design.
Today’s complex and high potency drug formulations require that packaging and packaging equipment evolves. Many newer drugs are temperature sensitive, unstable and/or vulnerable to contamination, making packaging design more difficult — but packaging suppliers have stepped up to the task. Our largest and most diverse category brings several cross-company collaborations, resulting in targeted solutions to new industry packaging challenges.
Groninger and SKAN’s INTEGRA Isolator
As the industry produces more potent APIs, larger molecules and modified release profiles, there is increased risk for stability issues associated with moisture, oxygen
and volatile reactives. Innovative dosage forms, such as chewable and disintegrating tablets, also face significant shelf life challenges with respect to humidity sensitivity. Recognizing the complexity of matching moisture- and oxygen-sensitive medicines to ideal packaging solutions, Aptar CSP Technologies launched the Xcelerate services suite.
An innovation favorite among our evaluators, the suite optimizes the active packaging development process through end-to-end expert insight, resulting in expedited speed to market for moisture- and oxygen-sensitive medicines. Xcelerate combines Aptar CSP’s groundbreaking active packaging with technology from FreeThink Technologies, a contract research organization with expertise in stability.
Xcelerate services are designed to significantly condense the entire active package design, testing, and implementation process — often by months, according to the company. The comprehensive, hands-on approach also includes capabilities to produce clinical trial and stability samples, regulatory support and consulting and testing during commercial implementation.
Our next winner is a joint cross-company development project from groninger, known for its high-precision filling and closing machines and SKAN, experts in cleanroom equipment and isolator design. Recognizing that processing aseptic and high potency products requires increased safety for operating personnel, optimized machine design for shortest set-up times, and optimum accessibility for machine operation and cleaning, the duo produ
ced a unique line concept for vial processing.
Making its debut at ACHEMA 2018 (and also taking home an ACHEMA Innovation Award), the INTEGRA line integrates both an isolator and filling machine.
INTEGRA was developed with a focus on processing toxic products. Thanks to the integration of the filling machine into the isolator and the integration of the SKANFOG decontamination system, the entire line can be cleaned and decontaminated in approximately 30 minutes with optimum accessibility for the operating personnel.
Increased security and support for format changes is made possible by the use of QR codes, which give operators a better overview of position, installation order and recipe assignment.
The integrated lines are available with different line speeds up to 400 objects/minute and with oRABS or standardized isolator technology.
Our next three winners fall into the drug delivery and device portion of this category. Starting with another collaboration, the SteriDrop tube combines the trusted barrier properties of Neopac’s proprietary Polyfoil tubes with an Ophthalmic Squeeze Dispenser from Aptar Pharma (part of the same AptarGroup as the first winner in this category). Designed for eyedrops, the packaging eliminates the need for preservatives, such as Benzalkonium Chloride, which can lead to side effects with chronic use.
The tube’s mechanical system releases a precisely measured drop when pressure is exerted on the tube, and prevents the liquid from flowing back into the tube, thereby guaranteeing a level of microbiological safety previously unattainable. Introduced at CPhI Worldwide 2018, the SteriDrop tube has proven highly conducive to protecting preservative-free eyedrops from contamination before, during and after initial consumer use.
Recognizing the need for exacting packaging requirements to protect against interactions between drug and container, our next winner has produced a new generation of ultra-pure pharmaceutical vials. Designed as a modular concept, SCHOTT’s EVERIC vials provide pharma companies with a unique combination of attributes to package biologic drugs while supporting today’s fill-finish quality requirements.
EVERIC pure, the first feature available, is designed for sensitive drugs and drugs with low filling volumes. The vials ensure drug stability by using an improved Borosilicate glass tubing.
Thanks to their better chemical resistance, the vials show a very low concentration of leached glass elements even for low fill applications — a major advantage over aluminosilicate vials. As a result, the new vials provide a tool for pharma companies to keep delamination under full control.
In the future, pharma companies will be able to add more features to their vials to improve the drug filling and transportation process. EVERIC strong vials will better withstand side compression and axial load during filling and transportation and EVERIC smooth vials will offer coating on the outer surface.
BD Pharmaceutical Systems’ Hylok prefillable syringe
The final spot in this category goes to BD Pharmaceutical Systems for its BD Hylok syringe.
High pressure exerted on syringes during injection of viscous solutions can cause needle disconnection and connector rotation, which can lead to leakage. The BD Hylok glass pre-fillable syringe is a new luer syringe for the administration of viscous and intravenous drugs — and according to the company, it’s the first glass pre-fillable syringe validated for delivery of IV drugs.
The syringe offers customers the advantages of glass containers (inertness and resistance to steam sterilization), with a strong and robust luer connection. The main applications for the BD Hylok syringe are hyaluronic acid (dermal fillers, intra-articular) and IV injection. However, it is compatible with main needles or IV connectors, allowing it to address a wide array of medical needs across the health care and medical aesthetics markets.
And there you have it — the 2019 Pharma Innovation Award winners — the greatest things since last year’s winning technologies. Congratulations and thank you for listening to the needs of the industry and your customers, and tirelessly pushing to make pharma better.