30 Years of Innovation: Bringing 3D Printing’s Benefits to Metal
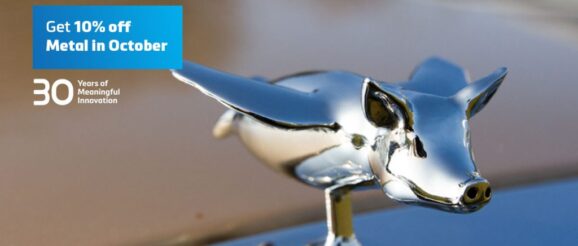
We have actually passed the middle of our 30th-anniversary blog site series, and for October, we’re looking into Metal 3D Printing. Keep reading to discover how our parent company Materialise makes use of Metal 3D Printing to combine AM’s advantages with tried-and-tested materials and how our team in Bremen, Germany is working to more establish the innovation.
3D printing for plastics was the plan for AM innovators to produce Metal 3D Printing processes. When the laser sintering innovation was patented, users began to experiment with applying the procedure to numerous metals as well. After a considerable industry-wide research study stage to enhance the innovation throughout the years, it became a reliable, premium option by the mid-2010s. At this point, Materialise brought Metal AM into our production portfolio to not only offer the printing service to our customers however to also utilize our AM proficiency to additional enhance the innovation.
The appeal of Metal AM was clear. Simply like for plastics, business now needed to opportunity to receive parts much faster than ever before, and now with robust products. 3D printing does not require the lengthy production of molds or assembly line like conventional innovations– with a digital file in hand, almost any style can be printed within approximately 10 working days. Nevertheless, we acknowledged that usually, the orders Materialise got didn’t gain from all of the technology’s benefits. With our know-how and design know-how, there was untapped potential that we could assist our clients accomplish– design liberty, expense reductions, and danger mitigation, for instance.
With Metal 3D Printing in our portfolio, we placed a focus on helping our clients leverage all of its advantages. And today, we continue to innovate to drive the innovation and our metal services forward. Our team is working to see that Metal 3D Printing is not just a quicker option to making metals, but the favored approach.
The one-stop-shop for Metal 3D Printing
To become true professionals in Metal AM, we chose to broaden our services into a place where we could both fulfill the needs of our orders and be near our consumers and other leaders in the manufacturing world. That is why we opened a center devoted to Metal 3D Printing in Bremen, Germany in 2016. In this way, we could constantly find out about markets such as aerospace, vehicle, commercial automation, and eyewear to advance our services.
Materialise opened its Bremen Metal AM center in April 2016.
When the facility was in place, we might provide a service that helped clients in using Metal AM to its complete capacity throughout the whole production process, from design to complete. “We provide a service that assists customers during each step of Metal 3D Printing,” shares Ingo Uckelmann, Technical Manager of Metal 3D Printing. “Our design and engineering, accredited manufacturing, and post-machining groups are all extremely educated about how finest to use the innovation and ensure that our clients get the most out of it.”
Let’s demonstrate this idea with our style and engineering team’s work on enhancing the design of a metal suction gripper. The team worked closely with the consumer to totally revamp their production part utilizing Style for AM principles. Because of these changes, the brand-new part was 94% lighter, 50% cheaper, and more performant.
The initial part (above) was not developed for AM, implying it was much heavier and more pricey than essential.
The team also started efforts to enhance the quality and consistency of the technology– a mission that continues to stay a focus. To do so, the group began by making sure consistent alloys via internal screening and aligning our alloy standards to that of our proven plastics offerings. For any metal prints i.materialise clients can select in between Aluminum, High-Detail Stainless-steel, Steel, and Titanium.
But these aren’t the only metals you can get on i.materialise — we also use 5 rare-earth element alternatives: Brass, Bronze, Copper, Gold, and Silver. Unlike our metal alternatives, we use lost-wax printing and casting to produce these materials. With this printing procedure, which is a kind of Stereolithography, customers can utilize 3D printing’s freedom of style with these sensational material choices.
Gold is readily available as 14k or 18k solid gold in three different colors: yellow gold, red gold, and white gold.
Taking Metal AM to the next level
At Materialise, we’re continuously aiming greater to enhance our technologies and make the benefits of 3D printing more available. This objective is no various with Metal AM. We want every customer to experience lighter parts, cost-effectiveness, and freedom of design integrated with the durability of metal materials. Then, Metal 3D Printing will undoubtedly be everyone’s first choice for manufacturing, not simply the option they turn to when they need a quicker option. This is why we’re installing the new Metal Skills Center at our Bremen facilities in early 2021.
“We’re establishing the innovations of tomorrow.”– Ingo Uckelmann, Technical Supervisor of Metal 3D Printing
This center was developed to bring together our experts in both AM software application and production to advance Metal 3D Printing while supporting a sustainable future. Here, the group can face any cost-effective or ecological challenge head-on and construct solutions with Metal 3D Printing’s abilities to overcome it. They distinctively integrate knowledge from the production flooring with know-how from decades of AM software advancement to further increase the technology’s dependability and consistency.
Thanks to this cooperation, the Metal Proficiency Center production can be the very first to deal with the current, most ingenious software from our team, and the software application developers can enhance software application with direct feedback from production. This quick feedback and advancement cycle enables the team to rapidly and continuously enhance their services to bring the best to consumers.
Our specialized software application, such as e-Stage for Metal, improves the reliability and quality of 3D printing.
“At our Metal Competence Center in Bremen, we’re developing the innovations of tomorrow,” discusses Ingo. “By enhancing Metal AM to make it much easier, more accessible, and more budget friendly, we will ensure that it’s a feasible innovation that companies will rely on first for their metal parts.”
As we’ve looked deeper into our own processes and fine-tuned Metal AM software and workflows, we’ve efficiently automated numerous jobs, hence shortening preparations and decreasing costs. Enhancing the technology through automation and style for Metal AM helps our clients reach the next level with their metal parts while keeping costs low. For series productions, we work together with clients to enable modification and improved parts with the power of Metal 3D Printing– all while satisfying their time, monetary, and quality expectations.
Let’s begin
All set to print your own tasks in Aluminum, High-Detail Stainless Steel, Steel, Titanium, Brass, Bronze, Copper, Silver Or Gold? Get your parts quicker than ever by purchasing online through i.materialise. Until October 31, we’re using an additional 10% off all Metal and Valuable Metal orders when you use the code 30Y_Metal at discount.