Revolutionizing nanosensor manufacture with a single drop of ethanol – Innovation Toronto
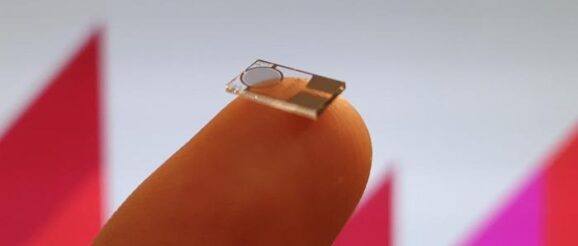
Macquarie University engineers have developed a new technique to make the manufacture of nanosensors far less carbon-intensive, much cheaper, more efficient, and more versatile, substantially improving a key process in this trillion-dollar global industry.
The team has found a way to treat each sensor using a single drop of ethanol instead of the conventional process that involves heating materials to high temperatures.
Their research, published yesterday in the Journal of Advanced Functional Materials, is titled, ‘Capillary-driven self-assembled microclusters for highly performing UV detectors’.
“Nanosensors are usually made up of billions of nanoparticles deposited onto a small sensor surface – but most of these sensors don’t work when first fabricated,” says corresponding author Associate Professor Noushin Nasiri, head of the Nanotech Laboratory at Macquarie University’s School of Engineering.
The nanoparticles assemble themselves into a network held together by weak natural bonds which can leave so many gaps between nanoparticles that they fail to transmit electrical signals, so the sensor won’t function.
Associate Professor Nasiri’s team uncovered the finding while working to improve ultraviolet light sensors, the key technology behind Sunwatch, which saw Nasiri become a 2023 Eureka Prize finalist.
Nanosensors have huge surface-to-volume ratio made up of layers of nanoparticles, making them highly sensitive to the substance they are designed to detect. But most nanosensors don’t work effectively until heated in a time-consuming and energy-intensive 12-hour process using high temperatures to fuse layers of nanoparticles, creating channels that allow electrons to pass through layers so the sensor will function.
“The furnace destroys most polymer-based sensors, and nanosensors containing tiny electrodes, like those in a nanoelectronic device, can melt. Many materials can’t currently be used to make sensors because they can’t withstand heat,” Associate Professor Nasiri says.
However, the new technique discovered by the Macquarie team bypasses this heat-intensive process, allowing nanosensors to be made from a much broader range of materials.
“Adding one droplet of ethanol onto the sensing layer, without putting it into the oven, will help the atoms on the surface of the nanoparticles move around, and the gaps between nanoparticles disappear as the particles to join to each other,” Associate Professor Nasiri says.
“We showed that ethanol greatly improved the efficiency and responsiveness of our sensors, beyond what you would get after heating them for 12 hours.”
The new method was discovered after the study’s lead author, postgraduate student Jayden (Xiaohu) Chen, accidentally splashed some ethanol onto a sensor while washing a crucible, in an incident that would usually destroy these sensitive devices.
“I thought the sensor was destroyed, but later realised that the sample was outperforming every other sample we’ve ever made,” Chen says.
Associate Professor Nasiri says that the accident might have given them the idea, but the method’s effectiveness depended on painstaking work to identify the exact volume of ethanol used.
“When Jayden found this result, we went back very carefully trying different quantities of ethanol. He was testing over and over again to find what worked,” she says.
“It was like Goldilocks – three microlitres was too little and did nothing effective, 10 microlitres was too much and wiped the sensing layer out, five microlitres was just right!”
The team has patents pending for the discovery, which has the potential to make a very big splash in the nanosensor world.
“We have developed a recipe for making nanosensors work and we have tested it with UV light sensors, and also with nanosensors that detect carbon dioxide, methane, hydrogen and more – the effect is the same,” says Associate Professor Nasiri.
“After one correctly measured droplet of ethanol, the sensor is activated in around a minute. This turns a slow, highly energy-intensive process into something far more efficient.”
Associate Professor Nasiri has already been approached by companies in Australia and internationally who are keen to work with her to put the technique into practice.
More from: Macquarie University