HP working with Dyndrite, AMT, Evonik, and U.S. Marine Corps. on digital workflow automation, advanced post-processing, and material innovation – 3D Printing Industry
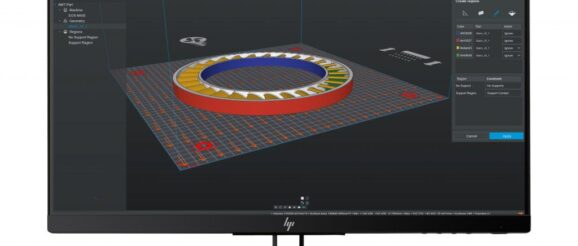
Multinational printing firm HP has released a spate of announcements in the lead up to this year’s Formnext Connect, aiming to drive digital, software, services, and automation advancements within the additive manufacturing industry.
The three pillar launch saw HP unveil a new software solution, the HP Universal Build Manager, which is powered by Seattle-based software company Dyndrite, alongside its new HP 3D Factory Services to aid customers in implementing their production processes, and its HP Automatic Unpacking Station, developed in partnership with Rösler Group’s AM Solutions.
The company also announced the successful development of a new printable thermoplastic elastomer for its Multi Jet Fusion (MJF) technology in collaboration with German specialty chemicals company Evonik. Further still, HP revealed a partnership with UK-based post-processing specialist Additive Manufacturing Technologies (AMT) to provide end-to-end MJF printing and post-processing services to part manufacturers and industrial partners.
“Automation, software, and data are key to delivering mass customization of parts and unlocking the full potential of large-scale additive manufacturing,” said Ramon Pastor, GM and global head of 3D Printing and Digital Manufacturing at HP. “We are committed to relentlessly improving our capabilities and helping customers optimize and automate workflows, enabling compelling new applications, and produce sustainable, high quality parts at scale.”
HP’s Universal Build Manager powered by Dyndrite
The Universal Build Manager (UBM) brings together HP’s proprietary software and data innovation with Dyndrite’s Accelerated Geometry Engine, leveraging its GPU-accelerated processing and Python scriptability. This combination helps customers to simplify, automate, and speed up build preparation across their additive workflows while facilitating the mass-personalization of parts, complex workflow automation, and scalability across both manual and automated workflows.
Dyndrite’s GPU-accelerated geometry engine will help to speed up computational tasks such as support generation, slicing, and tool pathing. Based on Python scriptability, the engine is also able to capture knowledge, process definitions, and streamline workflows through automating repetitive tasks.
The UBM supports industry CAD and vendor-neutral formats to allow CAD-to-print workflows for all major MCAD applications. Meanwhile, an extensive plug-in framework enables UBM platform access to all users, machine manufacturers, and software vendors, to eliminate the need to share sensitive IP information.
“We are addressing software challenges in the additive industry that have prevented it from becoming mainstream and are providing capabilities to help customers accelerate the journey to digital manufacturing,” said Ryan Palmer, Global head of software, data and automation, HP Personalization and Industrial Business. “The new HP Universal Build Manager simplifies, automates, and delivers a digital-first approach to manufacturing.
“This solution will enable customers to explore new areas of complexity and value, push the boundaries of sustainable production, and automate critical steps in their digital workflow.”
The UBM is already being deployed by Cobra Aero and Cobra Moto, propulsion system manufacturers for racing, fire fighting, aerospace, and surface and underwater vehicles. The companies are integrating the UBM to simplify and automate their workflows across HP Jet Fusion and Renishaw additive 3D printing systems.
Meanwhile, Aconity3D, Aon3D, Aurora Labs, EOS, Essentium, ExOne, Open Additive, Photocentric, Plural AM, Renishaw, and SLM Solutions, have all agreed to explore how HP’s UBM could be integrated into their own 3D printing systems. Deemed an open-architecture platform, the UBM will also facilitate interoperability with independent software vendors.
HP is a founding member of Dyndrite’s Developer Council and has worked closely with the software firm for over a year. In August, the companies announced a new strategic 3D printing partnership which saw Dyndrite license its 3D geometry kernel to HP.
HP Factory Services
Designed to assist in the implementation of digital factories which feature HP’s MJF technology, 3D Factory Services will provide support to customers looking to manage the production of high-quality parts at scale. Spanning facilities and equipment assessment, human capital planning and training, and the design and implementation of production processes, HP’s 3D Factory Services will aid customers through three digital offerings; 3D Application Programming Interface (API), 3D Process Control, and 3D Center.
The 3D API will be available to software companies with customers who use HP’s 3D printing solutions, providing them with an automated API for integrating data and streamlining workflows. One such example is MES and workflow software specialist, Autonomous Manufacturing (AMFG), enabling Henkel to integrate the 3D API into its management processes to create centralized end-to-end workflows.
“With the help of AMFG to connect our global infrastructure of application centers using HP Jet Fusion printers, we are aiding in centralizing the end-to-end workflows, from initial request to final part production,” said Chris Liddiard, Market segment head for Automotive and Industrial Parts, Adhesive Technologies Group, Henkel Corporation. “Armed with this important data, Henkel can better understand and interpret data patterns related to machine utilization, failure rate, geometrical specifications and processing parameters, allowing us to provide better manufacturing services for our clients.”
Customers such as Henkel will be able to tune their HP 3D printing systems for high-repeatability for certain actions, implement scalable industrial-level processes and quality controls, and trace raw and recycled material to improve sustainability.
HP’s Automatic Unpacking Station
The third pillar in HP’s end-to-end automation offering is its new industrial-grade Automatic Unpacking Station, developed in partnership with AM Solutions, the Italian 3D printing subsidiary of the Rösler Group, which specializes in surface finishing solutions. Designed for customers using HP’s Jet Fusion 5200 systems, the Unpacking Station will help to reduce costs and achieve greater build consistency across workflows. The agreement between the two companies was announced at last year’s Formnext,
“The comprehensive knowledge of HP in 3D printing, software and digitized manufacturing allows us to quickly develop innovative solutions for 3D post-processing and adapt these solutions to the demands of industrial users,” said Stephan Rösler, president and CEO of Rösler Group.
The station, which automatically unpacks builds in as little as 30 minutes, minimizes the manual handling of material powder and post-processing labor while reducing the variation between prints through operator-independent outcomes.
Italian 3D printing and CNC service provider Weerg is one of the initial customers of HP’s Automatic Unpacking Station.
“We are excited for the continued automation advancements from HP and its partners like AM Solutions,” said Weerg founder Matteo Rigamonti. “As we expand our business and manage a growing fleet of HP Jet Fusion systems these enhanced capabilities are designed to help us meet customer demand, and improve our turnaround times for high volume production parts.”
HP and Evonik develop new flexible TPA powder
Elsewhere, HP and industrial chemical corporation Evonik have enjoyed a long-standing industry partnership since 2016. Now, the two companies have produced a co-branded flexible specialty powder based on a thermoplastic amide grade (TPA) for 3D printing, to be presented at next month’s Formnext Connect.
Optimized for HP’s MJF technology, the new TPA powder is flexible and lightweight with a density of 1.01 g/cm³ and a Shore A hardness of 91. The powder is suitable for producing functional high-tech 3D plastic parts which require high extensibility and energy return, such as components for cars or sports equipment.
“We are excited to continue building on our long-standing partnership with Evonik to deliver another compelling material for our customers and expect to see innovative new applications that take advantage of TPA’s flexible, lightweight properties,” said Tim Weber, global head of materials, HP 3D Printing and Digital Manufacturing.
“Open collaboration with materials leaders like Evonik continues to be so important as we push the boundaries of additive manufacturing and accelerate the industry.”
The TPA powder enables the speedy 3D printing of usable prototypes without the need for tooling, an aspect which Californian rapid prototyping service provider GoProto is taking advantage of to produce a variety of applications.
“We have had customers make ducts and bellows and footwear, athletic equipment, wearables, and harnesses and connector parts,” said Jesse Lea, GoProto president and CEO. “The combination of production quality material properties like high wear resistance, energy return, longevity, and lightweight continues to impress at every application.”
HP and AMT partner to deliver high-quality post-processing
The final development in this latest string of announcements from HP sees the firm team up with leading post-processing specialist Additive Manufacturing Technologies (AMT) to provide end-to-end MJF and post-processing services to industrial partners across the automotive, industrial, medical, and sporting goods sectors.
The collaboration will expand HP’s ecosystem of strategic industrial partners while providing current and prospective HP MJF customers with chemical vapor smoothing benchmarking services.
AMT’s chemical vapor smoothing technology can be utilized to create sealed surfaces suitable for medical applications, enhance the mechanical properties of automotive parts, and improve the look and feel of commercial products. The company’s PostPro chemical vapor smoothing systems are compatible with HP’s full portfolio of jet fusion printers, with all commercially available materials having been validated.
“Like HP, we are focused on unlocking the full potential of industrial additive manufacturing and its sustainable impact,” said Joseph Crabtree, CEO, and founder of AMT. “The combination of HP’s industry-leading Multi Jet Fusion technology and AMT’s advanced chemical vapor smoothing systems leverages the benefits that 3D printing provides while having injection-molded quality finish and performance characteristics, enabling customers to produce manufacturing-grade parts at scale.”
HP and AMT have already started working with customers to develop new applications requiring an injection molding-like finish, such as 3D High Reusability PA 11 nasopharyngeal swabs developed to aid in combating Covid-19, and custom seating made from BASF Ultrasint TPU01 lattice structures.
Looking ahead to Formnext
To date, more than 50 million parts have been produced via HP’s MJF, with some five million of those produced throughout the Covid-19 pandemic.
In August, HP launched a new versatile, durable, and chemically resistant polypropylene (PP) material for use in its Jet Fusion 5200 3D Series printers. Towards the end of last year, the firm announced it had hit an important milestone when together with Volkswagen and GKN, 10,000 metal parts were produced on the HP Metal Jet System. New customers of the Metal Jet include golf equipment manufacturer Cobra Golf and U.S. Marine Corps.
With its most recent announcements, HP is looking ahead to Formnext Connect, where, with its partners and customers, it will be participating in a variety of sessions covering advanced post-processing, digital workflow automation, materials innovation, and highlighting its new High Reusability TPA.
Subscribe to the for the latest news in additive manufacturing. You can also stay connected by following us on and liking us on
Be sure to subscribe to the Another Dimension podcast on your chosen podcast player to make sure you never miss an episode.
Looking for a career in additive manufacturing? Visit for a selection of roles in the industry.
Featured image shows HP’s Universal Build Manager leverages proprietary HP software and data innovation, combined with the Dyndrite Accelerated Geometry Engine. Image via HP.