Innovation in hard rock mining from Komatsu | Komatsu Mining Corp.
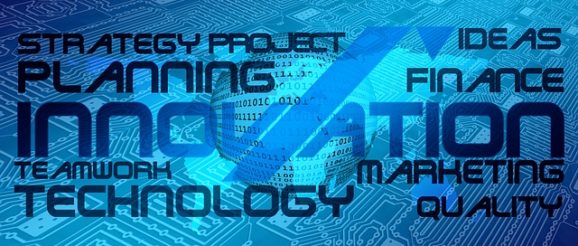
Your hard rock mining operations require flexibility, with machines that can evolve with your operation. Listening to what our customers need has led to new machines with innovative enhancements, designed to help optimize hard rock mining operations.
Collaboration with customers is critical to product innovation. Since 1921, forging partnerships with customers has granted us insight into the challenges you face, and earned us your trust to develop solutions to overcome those challenges.
Our new hard rock mining products are the direct result of your invaluable feedback, multiple prototype tests, and our engineers rolling up their sleeves to create and build innovative products that meet the needs of today’s hard rock mining operations.
It’s a jumbo; it’s a bolter; it’s both
To help meet your bolting and drilling needs, we’ve developed a new concept for hard rock: a common platform between bolter and jumbo. Offering a smaller profile compared to competitors in the same class, two brand-new Komatsu products with large capabilities represent this mining innovation: the Komatsu ZB21 underground bolter, and the Komatsu ZJ21 jumbo drilling machine.
What’s truly unique about this product line is its common platform design. The platform offers 100% design commonality between bolter and jumbo, from the rear skirt to the outer boom structure — an industry first — for a seamless conversion from bolter to jumbo, or vice versa.
With the ZB21 small-class bolter, the inner boom can be swapped out for a drilling feed system, effectively converting it to a jumbo. The same is true for the ZJ21; its inner boom can be changed out for bolting.
The common platform approach goes beyond the attachment: the controls are similar too. The hydraulic pilot control system with universal bolting and drilling controls, simplifies user training and adoption across both models. Platform universality also provides advantages with job site efficiency, leveraging common parts, service, and maintenance — which can help reduce costs.
Beyond the innovation of a common platform, these machines offer other additional value to hard rock mining operations.
Despite being one meter longer (on average) than competitors in the class, the ZJ21 can effectively navigate a 90-degree intersection in a 3-meter by 3-meter heading. In this same heading size, the ZJ21 can feature up to a 16-foot drill steel, promoting excellent productivity for machines in its class. This longer boom provides significant usable face coverage, so the ZJ21 can back up a two-boom jumbo in larger drives. With an overall operating height of 2.8 meters and maximum width with leveling jack extended to 2.7 meters, the ZJ21 can be used efficiently in small headings.
The boom design also helps promote zero contact with the operator’s station or the carrier or leveling jacks when drilling on the face, including the lifters — even in the longest feed configuration and fully retracted.
The design of the ZJ21 provides a profile that matches the typical mining tunnel while delivering up to 66 square meters of coverage. This greatly assists operators performing vital tasks such as drilling lifters, perimeter holes, and up or down ramps. You can also create truck loading bays, service bay, cross cuts and even back up two-boom jumbos in larger drifts.
Utilizing the same carrier and common platform as the ZJ21 jumbo, the ZB21 bolter can handle up to an 8-foot bolting head. Its bolting fan pattern offers 7 meters on the walls, 7.5 meters on the backs and a 50-square meter face coverage.
Literally able to bolt in any direction, the bolting head technology of the ZB21 lets the operator perform 100% of the bolting cycle from the enclosure thanks to a patented screen handler design and innovative chemical injection system. The bolting head also leverages polyurethane-casted components to decrease weight and reduce parts count, compared to conventional components.
The diesel version of both the ZB21 bolter and the ZJ21 jumbo are available to order now. A battery option will be available next year.
A bolting head designed for durability
Cast polyurethane bolting head components on the ZB21 promote durability while reducing weight. This specially-selected material provides forgiveness in areas such as the bolt centralizers, bolt carousel, bolt driver, stinger pad and rear feed plate. The polymer components also help to reduce the need for adjustment while reducing the overall number of moving parts, promoting precision alignment for bolt installation.
A notable feature of the bolting head is that it handles and installs all four major types of bolts and features a 9-bolt magazine in its base configuration. It can manage two various types of bolts with minimal carousel adjustment needed to modify the bolt diameter.
The bolting head for the ZB21 is available in 5- to 8-foot lengths. The 8-foot configuration offers simple adjustability to a 7- and/or 6-foot overall length to promote versatility and accommodate most ground support programs.
Reengineered feed system
The feed system has been reengineered to enhance maintainability and productivity, and it too features lightweight polyurethane components for flexibility. The all-purpose design provides enhanced forgiveness for a reduction in misalignment. Timing ropes are identical lengths with common part numbers and come with a standard “quick attach” feature to make changing the ropes easier in an underground setting.
The hose drum has no bearings and is also made of polyurethane, a material that is far less brittle than traditional plastics. The graphite-impregnated hose drum is virtually self-lubricating. Guide strips have been designed with the maintenance team in mind: they are common from left to right and twice as thick as the competitors’ yet made of a slightly softer material to reduce cracking. Only one technician with hand tools is needed to change them out.
Bring intelligence to your hard rock operation
If you’re looking for a medium-class development drill that also offers a common platform, the ZJ32Bi delivers. With an “organically developed” computer control system, the “i” stands for intelligent.
This new computer-controlled system with a smart control platform offers many benefits. If you’re trying to make inroads into automation at your mining operation, the ZJ32Bi, offers a step in that direction.
With semiautonomous functionality and built-in operator augmentation features when in manual drilling mode, the computerized, smart platform features two-joystick functions, onboard manuals, parts books and semiautonomous operation. Modular controls, a self-diagnostic system and ground monitoring are designed for precision. Features such as fixed bit and actuator roll around can augment the skills of even the most experienced operators.
Operator comfort is key to your operation’s productivity, and the newly designed fully enclosed cabin of the ZJ32Bi includes features to promote comfort and efficiency. Its ROPS/FOPS-certified operator enclosure has been completely updated with double-curved glass for improved visibility, and sightlines for drilling lifter holes and crosscuts. The glass helps reduce noise to keep sound at approximately a 73-decibel noise level. The cab has been designed to comfortably accommodate operators (from 5-foot 7-inches to 6-foot 3-inches tall), whether your operator is seated or standing.
Is that boom really hoseless?
Chafed and damaged hoses on the boom can cause significant downtime for hard rock mining operations. What if you could have a hoseless boom? Soon you can. Our hoseless boom will complete all fluid and communication transfer inside of the boom cylinder, offering a potential game-changer in terms of automation and productivity.
Here’s how it works. The ZJ32Bi jumbo with hoseless booms eliminates the need to account for hoses in our automation algorithms. A hoseless boom also eliminates wear between the inner and outer boom tubes for to improve drilling accuracy over time.
Smart hydraulics reduce hoses to six
However, since not every application may need a hoseless boom, we’ve also designed an unconventional “conventional” boom offering. Our solution leverages smart hydraulics to reduce hoses to only six per boom, to improve visibility and help control costs. The reduced hose boom accommodates automation and can promote a reduction in the downtime associated with traditional hosed booms. All sensors and electronics are integrated into the design, protecting the six hoses, yet still making them accessible for maintenance.
To support sustainable initiatives — or if you’re driving toward zero emissions — the ZJ32Bi is battery-powered. Also available in a diesel-powered model, as the Komatsu ZJ32i, the medium class ZJ3i series will be commercially available with the reduced hose in the spring of 2021. The hoseless boom option will be available at a later date.
What’s next?
Driving to zero emissions and supporting mines in their goal toward electrification is a high priority. Our new bolting and drilling platform, with both conventional diesel and battery-electric drive options, suit your ever-evolving needs. Moving forward, we’ll continue to introduce more new hard rock mining products powered by the latest advanced electric-battery technology.
Autonomous operations is another goal, and with mining innovations, like the hoseless boom and “intelligent” controls, these machines support your journey toward automation, and can augment the performance of both your new and most experienced operators.
Our new drilling-bolting platform will include nine new models by the end of 2021. In addition to the newly released WX04 and WX07, we’ll also introduce several other new haulage products.
Stay on top of the latest trends and mining innovations, and follow us on The Road to MinEXPO, a series of virtual programs that offer an in-depth look at Komatsu’s newest innovations in mining. To learn more about our new sustainable and innovative solutions for hard rock, or to connect with a product expert, please visit our online virtual platform.