Academia and business to develop 3D printed pancreas for testing diabetes medication – Med-Tech Innovation | Latest news for the medical device industry
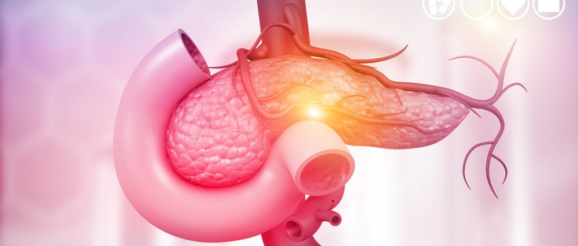
In the European project ENLIGHT, Readily3D joins forces with academic centres and companies across Europe to develop a living model of the pancreas to enable better testing of diabetes medication.
This model will be shaped using 3D printers made by Readily3D, leveraging tomographic printing to produce centimetre-scale structures in less than 30 seconds. The prints themselves will be done at UMC Utrecht and EPFL, which jointly pioneered the use of volumetric printing for biofabrication in 2019, with specialised stem cells developed by ETH Zurich and the University of Naples.
Damien Loterie, CEO of Readily3D: “We are excited to be part of the ENLIGHT project and to push the frontiers of biofabrication together with our partners.”
The ENLIGHT project has received a four-year grant from the European innovation Council fund Horizon 2020. The aim is to realise the first working tissue model within three years.
Partners in the project have been granted a contribution of €3.6 million by the European Innovation Fund Horizon 2020. Led by the UMC Utrecht, the multidisciplinary consortium consists of Readily3D (Switzerland), Ecole Polytechnique Fédérale de Lausanne and ETH Zürich (Switzerland), the University of Naples Federico II (Italy), AstraZeneca (Sweden), Rousselot (Belgium), and Fondazione Giannino Bassetti (Italy).
Readily3D will be joining the research programme as manufacturer of the bioprinters and will work on adapting its volumetric printing technology to the particular needs of pancreatic structures.
To reach their goal, the ENLIGHT researchers want to force two breakthroughs. The first is Readily3D’s newly developed bioprinter, which can reproduce part of the human body, including living cells, at speed. Where conventional 3D printers can take several hours to print centimetre-scale structures, volumetric bioprinters can do it within a minute. This is important because the survival rate of the cells decreases as printing takes longer.
Paul Delrot, CTO of Readily3D: “With its rapid build speed, low light dose and sterile build environment, tomographic bioprinters open up previously inaccessible applications in biofabrication.”
Once the bioprinter has created a living 3D model of human tissue, the second step will be to add signalling molecules, which tell the cells how to behave based on external stimulation. This is needed to recreate functionality at the human organ level.
The use of tissue from a 3D bioprinter has a number of advantages. Artificial models could eliminate the need for animal testing and accelerate drug discovery for pharmaceutical industries. This type of personalised medicine could also reduce the burden on individual patients, as they would no longer have to experiment with different drugs until one works. If the model works it can also be used for other diseases, such as cancer.
Professor Riccardo Levato, biofabrication researcher at the UMC Utrecht and coordinator of ENLIGHT: “With cells from a patient, practitioners can recreate the diseased tissue. Subsequently, a laboratory test can be performed to determine which candidate medication has the greatest effect. This spares patients a long search with unpleasant side effects, saves on treatment costs, and leads to the best available care for individual patients.’’
The next four years are aimed at creating a living model of the pancreas, including hormonal functions. In the longer term, the ENLIGHT projects aims to provide new tools to resolve the shortage of donor organs for transplantation and regenerative medicine.