Forage 2021: Innovation in the hayfield
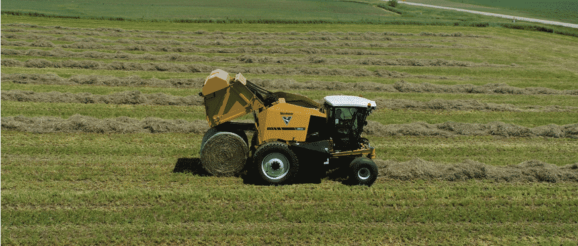
Two former ag teachers, a mechanical engineer and a machinist were fishing one day, talking about haying. While this may sound like the beginning of a good joke, their discussion on how difficult it was sometimes to rake and bale hay efficiently without unpredicted afternoon showers setting the process back resulted in the development of a new product, proving the old proverb correct, necessity is indeed the mother of invention.

FlexRake
For years, hay producers have had enough to worry about while cutting, drying, baling and storing hay efficiently without weather events, second guessing timing, or sacrificing quantity for quality, and as a result, machinery manufacturers have responded with new innovations and inventions and more improvements to old equipment, year after year.
“We were looking for something that one, would eliminate a second tractor and the extra labor, and two, some way to get raked and baled at the same time so it wouldn’t get rained on and we just kept working with it and trying one thing or another,” says Joe Waldorff, vice president of Flex Rake LLC, the business that was formed between friends while fishing.
It took roughly one haying season of adapting and improving before the designers were happy with the end product. They made it more heavy-duty and more trouble free so that it would last longer, changing the shaft to two-inches with three carrier bearings and adding a larger rear frame so it would handle larger windrows.
The Flex Rake looks similar to a traditional rake, but is modified for use between a tractor and baler, eliminating the need for a second operator and tractor, or pass with a tractor and baler at a later time, saving money, labor and wear on equipment.
“The drive shaft between the tractor and the baler is installed inside of the frame of the rake,” says Flex Rake’s website. “There are no PTO driven parts on the rake. This allows for safer operation of the baler behind the rake. The rake has wings which come in and out, hydraulically, for ease of use, precise hay gathering, and transport of the implement.”
Because Flex Rakes are built to order in Alabama, they can be used for a variety of haying needs from traditional grass hay to perennial peanut hay.
“We build the frames and have all the components ready to customize,” Waldorff says. “The main things that are specific to the individuals is the wiring harness for the baler, the choice of PTO shafts, the hydraulics and the rake wheels.”
Wheels come with high capacity tines or standard tines, depending on the forage being raked and baled. For those who use both square and round balers, the Flex Rake can be modified with an additional wiring harness to accommodate both balers.
While Flex Rake LLC is a small company with one, highly modifiable product, larger, more well-known equipment manufacturers are coming out with newer and more efficient products. Square balers are always reaching for more capacity, swathers are cutting faster and laying nicer windrows that can dry faster, and now Vermeer has come out with a self-propelled baler, the first of its kind.

VermeerBaler
“There’s always advancements in precision planting technology and that’s getting better all the time, but probably one of the greatest things that’s come out in agriculture as a whole as far as machinery goes is Vermeer’s self-propelled baler,” says Dave Vanek of Billings Farmhand, Inc. “They’re performing really good with very little for problems with a new piece, so it’s been working pretty good.”
Because it is driven by all hydraulic motors, the net wrapping process is sped up considerably. It is easier and faster to navigate fields with the zero-turn capabilities, that can also be turned off, locking the front wheels together so that it steers like a pickup while transporting from field to field at speeds over 30 miles per hour. The on-board camera system lets operators view the bale formation, from intake to bale ejection, without having to physically look back. Not only does the self-propelled baler make the baling process faster, estimating it can bale a field one and a half times faster than the traditional method, it also makes picking up hay out of the field faster with the ability to leave the bale straight in line with the baler or rotate them 90 degrees.
“It’s not self-driving yet, but there will be a day when it is,” Vanek says, adding that Hesston by Massey Ferguson has a self-propelled windrower that can cut hay down at 17 miles per hour, hands free. “It’s all GPS guided because you can’t physically drive one that fast in the field,” he says. “They really can out-do what a human can do, you just plug in your map and go. Precision agriculture is here.”