Innovation and Potentiality of Concrete Usage
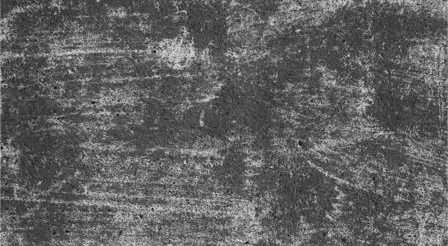
Developing and maintaining world’s infrastructure to meet the future demands of industrialized and developing countries has become necessary to economically grow and improve the quality of life. The quality and performance of concrete plays a key role for most of the infrastructure including commercial, industrial, residential and military structures, dams, power plants and transportation systems. Concrete is the single largest manufactured material in the world and accounts for more than 6 billion metric tons of materials annually. In United States, federal, state, and local governments have nearly $1.5 trillion dollars in investment in the U.S. civil infrastructure. The worldwide use of concrete materials accounts for nearly $780 billion in annual spending. The industrialized and developing world is facing the issues related to new construction as well as repair and rehabilitation of existing facilities. Rapid construction and long term durability are requirements on most projects. Initial and life-cycle costs play a major role in today’s infrastructure development. There have been number of notable advancements made in concrete technology in the last fifty years. Some of these advances have been incorporated in routine practices. But, in general, the state-of-practice has lagged far behind the state-of-art. This is particularly true for public sector projects. There is an increasing concern in most parts of the world that it takes unduly long time for successful concrete research products to be utilized in practice. Even though some advances have been made in quick implementation of new concrete technology, significant barriers to innovation and implementation remain. Continued coordination of ongoing inter- national research and educational pro-grams is needed. Numerous advances have been made in all areas of concrete technology including materials, mixture proportioning, recycling, structural design, durability requirements, testing and specifications.
Market Potential
Rapid Strength Concrete Market is estimated to surpass USD 450 billion by 2024; according to a new research report by Global Market Insights, Inc. Strong demand for rapidly setting concrete in the construction industry which helps in reducing the overall construction time and cost is likely to augment rapid strength concrete market size by 2024. The product possesses excellent properties which helps in developing high resistance in few hours of being applied. It helps in removing the formwork early to move forward in the building process and become operational in a shorter duration over conventional concrete, which will help drive the overall rapid strength concrete market size by 2024.Urbanization and industrialization in Asia Pacific, followed by the Middle East & Africa has led to large scale construction activities, which is mainly attributed to rising investment in the construction industry. This in turn will augment demand for rapidly setting concrete to speed up the construction process which will make noteworthy contribution to the rapid strength concrete market size in these regions by 2024. For instance, as per Asian Development Bank (ADB), Asia Pacific would invest approximately USD 26 trillion in the next 15 years. The aforementioned trends will make substantial contribution to the rapid strength concrete market size by 2024.
According to gminsights.com, Rising construction activities in Asia Pacific and the Middle East & Africa will contribute in rapid strength concrete market size during the forecast timeframe. Rapid strength concrete is able to develop high resistance within a short time after construction. This feature enables the early removal of the formwork which not only speeds up the construction process but also reduced overall cost. With the increasing need for high speed construction processes all over the world, rapid strength concrete is poised to witness fast increase in demand in coming years.
The European construction industry has slowly revived from the economic downturn, with residential construction output increasing by 1.5% on the previous year in 2015. Germany, France, and UK have been at the forefront of this growth with the German residential construction increasing by 2.7% in 2015. The German residential construction output was valued at USD 198.7 billion in 2015, while the output in France and UK was USD 117.5 billion and USD 98 billion respectively. This high amount of residential construction activities in these countries will augment the rapid strength concrete industry as the product is being used to build columns, walls, beams, slabs, panels, etc. at a faster rate than traditional concrete.
Several new construction projects in the U.S. has been commissioned in 2016 with the government earmarking USD 1 trillion for the development and maintenance of infrastructure. Some of the projects such as the USD 1.6 billion worth DFW Connector project in Dallas, project Neon in Las Vegas, and the new bridge construction project in New York will increase rapid strength concrete demand in the coming years. These new mega construction projects will see higher usage of the rapid strength concrete as it can reduce the project timing by a considerable amount owing its quick setting nature. Infrastructure projects has also been fast-tracked in many other countries across the globe. Construction of new airports, bridges, tunnels, and roads in the emerging countries, for instance India and China will open up plentiful opportunities for the rapid strength concrete market size during the forecast timeframe.
Innovations in concrete
Aligning with popular demand of concrete several innovation is happening across, the globe, some of the popular ones are discussed below:
GRAPHIC CONCRETE
Finnish company has developed a patented method for creating patterned concrete surfaces that involves the precise application of a surface retarder to the exterior of a concrete formliner. The surface pattern is the result of the contrast between the smooth face and the exposed fine aggregate in the concrete. This approach allows precast concrete manufacturers to produce highly detailed concrete elements, panels, and slabs with a variety of select patterns, as well as virtually any custom design.
LIGHTWEIGHT CONCRETE
Architectural cladding panels made with CarbonCast carbon-fiber grid reinforcing can weigh up to 66% less than convention precast panels. That’s because carbon-fiber reinforcing resists corrosion and therefore requires less concrete cover. These thinner, lighter concrete panels can also be integrated with insulation, increasing the R-value of wall systems. When used in the flanges of pre-topped double tees, CarbonCast can reduce weight by 15% and eliminate the need for sealers and sacrificial barrier coatings.
CHROMOS CONCRETE
A trio of UK-based product designers has developed a method for incorporating dynamic patterns, numbers, and text into concrete surfaces. Chris Glaister, Afshin Mehin, and Tomas Rosén have figured out that by incorporating thermochromatic pigment and wire heating technology into a standard concrete mix, the color of concrete can be changed. With the use of microprocessor control devices, the color-changing pattern can be precisely manipulated to form complex patterns and even information displays, such as dot-matrix clocks. While Chronos Chromos Concrete is not yet commercially available, the material is being used in several projects, including a 40×78-inch information display in the entrance hall of a new building in London.
WALLED PAPER PRECAST CONCRETE
At first glance, walls constructed with Walled Paper precast concrete may appear to be covered with decorative paper, but the complex, ornate patterns are actually cast into the surface of the concrete panel. UK-based Concrete Blond can cast more than 50 standard patterns and virtually any custom design into architectural precast panels for interior and exterior cladding, flooring, and surface applications. The patterns can be cast with a textural depth of 1/64 to 3/16 inch on to three types of concrete: Brutalist gray, Victoriana black, and Portland white.
SOLID POETRY IS A CONCRETE
Developed by Dutch designers Frederik Molenschot and Susanne Happle, Solid Poetry is a concrete tile that reveals a pattern when wet. The detailed patterns are created by carefully applying surface treatment to the finished concrete surface that darkens when exposed to water or humid air. Solid Poetry is ideal for floors, walls, and surfaces in environments that encounter frequent humidity changes, such as poolsides, gardens, bathrooms, and saunas.
Contents: Concrete, surface treatment.
CONCRETE BASE SLAB
Swedish Hospital and Medical Office Building, Issaquah, Wash., is a 600,000-sf campus developed by Hammes Company, with architect Collins Woerman and contractor Sellen Construction leading the Building Team. The project was completed ahead of schedule and nearly $35 million under budget through a combination of methods, including heavy use of Lean principles, BIM, and integrated delivery. One result of the teamwork was the choice of the SUPERCAP system to cap the concrete base slab, instead of using a traditional trowel-applied finish. The system combines a Greenguard-certified, low-alkali, self-leveling cement-base technology with a computer-controlled pump truck. At Swedish Hospital, the system eliminated concerns about flatness inherent to concrete slab work with structural steel buildings. Sellen placed about 20,000 sf/day of concrete, compared with 15,000 sf/day using conventional troweling. LATICRETE
RAPID-DRYING CONCRETE
The original schedule for Billy Earl Dade Middle School, a replacement school for the Dallas Independent School District, called for a 14-month construction period. When officials asked that the schedule be cut to 10 months so students could move in for the fall 2013 term, the Building Team knew concrete drying posed a potential problem. Aridus Rapid Drying Concrete, a ready-mix formulated to help prevent moisture-related flooring failures, was selected for its combination of fast drying time, high early strength, compressive strength, and low permeability. The project required 20,000 cubic yards of concrete, including 5,000 cubic yards of Aridus used to cover 120,000 sf of floors. Crews were able to install final flooring 21 days after the concrete was poured, compared with a typical drying time of at least four months. On the Building Team: Satterfield & Pontikes Construction (GC), Redi-Mix Concrete (concrete supplier), and KAI Texas (architect). U.S. Concrete.
THERMAL INSULATION CONCRETE
ThermaEZE thermal insulation works with poured concrete wallsincluding foundation wallsfor better insulation than conventional poured concrete, according to the manufacturer. The system consists of panels of expanded polystyrene foam, placed within the wall forms before the pour and held in place by a patented web structure that becomes embedded in the concrete. The resulting walls thus consist of a concrete layer and an attached insulation panel, with fastening strips on the exposed face to facilitate application of drywall or other finish materials. Depending on the thickness of the concrete, R-values range from 9.6 to 11.7. Panels are termite-resistant, odor-free, and contain no CFCs, HCFCs, HFCs, or formaldehyde. The UL-approved system is IECC code-compliant for foundation walls, and meets ASTM C578 Type 1 and ICC-ES EG239 requirements for below-grade use. North American Specialty Products.
BIO-BASED COMPOSITE
Tradical Hemcrete, developed in the U.K. by Lime Technology, incorporates hemp shiv (the woody core of industrial hemp) and a lime-based binder, Tradical HB. The resulting composite exhibits good thermal insulation and excellent thermal inertia, according to the manufacturer, creating environments that need minimal heating or cooling. The material has negative embodied carbon because CO2 that is captured by hemp as it grows is ultimately sequestered within the Hemcrete. Several design and construction methods are appropriate, including direct application to timber-framed structures and use with a rainscreen system. Because proper on-site drying can be tricky, the company recently developed systems that incorporate the material in factory-made panels, including Hembuild (for low-rise buildings) and Hemclad (for large-scale buildings with a primary structural frame). American Lime Technology.
POLYASPARTIC COATINGS
Rapid-curing polyaspartic coatings using raw materials from Bayer MaterialScience are designed for faster productivity without sacrificing high performance or durability. Usable for both metal and concrete surfaces, the coatings resist damage from ultraviolet light, chemical spills, and abrasion. They have ultra-low VOC emissions and high color stability and cleanability, according to the manufacturer. Formulations offer a fast curing time, with a typical start-to-finish cycle that fits within an eight-hour work day. Coatings made with polyaspartic esters can be applied at temperatures below 50°F and in high-humidity environments, extending the application season. The coatings can be applied over stains for attractive effects. Appropriate commercial projects include hotels, restaurants, retail space, healthcare, and other facilities with concrete floors. Bayer MaterialScience.
CONCRETE ROOF TILES
BoralPure Smog-Eating Tile, recipient of Popular Mechanics’ Breakthrough Award, removes nitrogen oxides from the atmosphere to improve environmental quality. The tiles include the photocatalyst titanium dioxide, which oxidizes with vehicle-emitted NOx and removes it from the atmosphere. The benign precipitate resulting from the chemical reaction washes away in the rain. The technology also uses naturally occurring UV light to help break down organic substances that can occur on roofs, such as mold and algae. Additional benefits cited by the manufacturer include high thermal mass, emissivity, and reflectivity, and an insulating air space between the tile and the roof deck. At the end of their service life, the tiles can be recycled for new structures or roadways.
DRAIN WATER WITH TOPMIX PERMEABLE
Preventing floods on the jobsite and in the finished project are a crucial element of any construction job. Topmix Permeable is the first truly porous concrete material, which allows it to absorb water down into the ground below. Traditional concrete is somewhat permeable, but it’s hard to compare its absorption rate of a few dozen gallons of water per hour to Topmix Permeable’s rate of a few hundred gallons per minute.
PREVENT CRACKING WITH SUPERHYDROPHOBIC
This super-technical name is for a majorly innovative cement composite. Road surfaces only have about 40 years before the slow accumulation of moisture in freezing conditions cracks the concrete surface. You can triple that time with incredibly durable Superhydrophobic concrete. Unfortunately, with its current cost, we’re a long way from widely using concrete that lasts 120 years.
CONCRETE MADE FROM ORGANIC-BASED MATERIALS
Even concrete is in the process of going green, as researchers at MIT are using natural materials like shells, bones, and sea sponges to make a durable and sustainable concrete mixture. Since these organic materials can go millions of years without breaking down, it’s safe to say that they’ll prolong the life of any structures they’re used in.
CONFLEXPAVE GIVES FLEXIBILITY
The addition of polymer microfibers to the ConFlexPave solution gives it the unique ability to bend without breaking. This innovation could be revolutionary to the concrete industry because structures and roads built using ConFlexPave wouldn’t crack under the weight of heavy loads.
BIOCONCRETE REPAIRS ITSELF
This concrete can self-heal by using bacteria to bind together fractured cement grains. When moisture enters the cracks, it gives the bacteria a source to germinate and multiply before producing calcium carbonate. This results in limestone formation, which plugs the cracks.
ARIDUS RAPID DRYING CONCRETE OUT-PACES THE COMPETITION
While there are already many forms of quick-drying concrete on the market, Aridus Rapid Drying Concrete is speeding past the competition. Currently, wide-scale infrastructure projects need around 6 to 12 months for the concrete to dry fully. By using Adrius Rapid Drying Concrete, you can cut costs and project timelines significantly, because this concrete dries in only 45 days.
3D-PRINTED CONCRETE
Additive-manufacturing concrete printers aren’t exactly new (Redshift first mentioned the technology in 2014), but 2017 saw a major milestone as not one but two bridges were constructed on-site using commercial 3D printers. The first, a Gaudí-inspired pedestrian footbridge in Madrid, was designed by the Institute of Advanced Architecture of Catalonia. The second, a cyclist bridge in the Netherlands, was designed and built by engineers from the Eindhoven University of Technology and construction company BAM Infra.3D printing offers many advantages here: Structures require only the amount of cement that will be used (lowering carbon-dioxide emissions), require no formwork (lessening waste), and can be built into shapes previously possible only with extensive CGI movie magic.
SELF-HEALING CONCRETE
It’s the bane of every engineer and construction professional’s existence: concrete cracks. Once a concrete project cracks which all will at some point leakage can occur, disrupting the integrity of the material. Scientists at the Netherlands’ Delft University of Technology have invented bioconcrete. This is concrete that is mixed using the same techniques as traditional concrete except that it also contains specific bacteria. These bacteria generate crystals that enclose their cells. When mixed with other secretions, such as proteins and sugar, a glue-like substance is generated. When the concrete cracks, these bacteria are activated and form either limestone or calcite, a process that seals the gaps.
GREEN CONCRETE
With its continued focus on the environment, it shouldn’t be a surprise that the construction industry is developing materials that are more ecologically friendly. Concrete typically generates a great deal of carbon. In fact, it produces so much carbon that the typical carbon footprint of concrete is nearly as large as the weight of the material itself. When mixed with fly ash a waste material that is generated by power stations that burn coal and other materials such as concrete and Portland cement, many benefits become evident. Not only does using fly ash reduce the carbon footprint of the concrete by as much as 25 percent, it also requires less water. This eco-friendly concrete is creamier and easier to place within projects. Finally, using the fly ash helps keeps this waste product from being dumped in landfills.
PERVIOUS CONCRETE
Another environmentally-friendly concrete solution that is poised to gain a great deal more traction within the construction industry is pervious concrete. Traditionally, concrete has been impervious meaning water runs off of it, allowing architects to direct its flow in more focused ways. At least, that was the original intent. This strategy, though, led to numerous incidents of urban flooding, erosion, pollution and other problems. As a result of these serious ecological issues, a solution pervious concrete was developed. Sometimes called a porous pavement, pervious concrete is made of larger particles than traditional concrete. This creates voids within the concrete that allow for the gradual infiltration of rainwater into the ground below.
WONDER-MATERIAL GRAPHENE CONCRETE
Experts from the University of Exeter have developed a pioneering new technique that uses nanoengineering technology to incorporate graphene into traditional concrete production.
The new composite material, which is more than twice as strong and four times more water resistant than existing concretes, can be used directly by the construction industry on building sites. All of the concrete samples tested are according to British and European standards for construction.
Crucially, the new graphene-reinforced concentre material also drastically reduced the carbon footprint of conventional concrete production methods, making it more sustainable and environmentally friendly.
The research team insist the new technique could pave the way for other nanomaterials to be incorporated into concrete, and so further modernise the construction industry worldwide.
HIGH PERFORMANCE CONCRETE (HPC)
Normal Strength Concrete (NSC) is heavy and lacks the required work-ability in some large concrete structures, such as high-rise buildings, bridges, and structures under severe exposure conditions. By increasing concrete strength and performance, the required thickness of concrete members and the cost of concrete structures can both be reduced. In the U.S., a major move to-ward HPC is underway, especially in the manufacturing environment of precast concrete. A major demonstration precast concrete bridge is under construction in Texas. High Performance Concrete (HPC) is the latest development in concrete. It is not just High-Strength Concrete (HSC) and has replaced HSC developed in the early 1980’s. HPC can be defined as a concrete made with appropriate materials (superplasticizer, retarder, fly ash, blast furnace slag and silica fume) combined according to a selected mix design and properly mixed, transported, placed, consolidated, and cured to give excellent performance in some properties of concrete, such as high compressive strength, high density, low permeability and good resistance to certain forms of attack.
SMART CONCRETE
Concrete has been widely used for many years as a composite material for various types of structures. One of the weaknesses of concrete is that it cannot withstand tension which can cause cracks easily. There has been a huge demand to monitor concrete structures cracking and preventing them from propagating further. These efforts are important for timely repair, safety and long-term durability of critical structures. Non-destructive evaluations, such as attaching or embedding sensors into structures, have been used in many ways to accommodate the demand, yet the tests are considered expensive. Smart concrete was developed by Dr. Deborah D.L. Chung from State University of New York at Buffalo. Smart concrete is reinforced by carbon fiber as much as 0.2% to 0.5% of volume to increase its sense ability to strain or stress while still has good mechanical properties. By adding small amount of short carbon fiber into concrete with a conventional concrete mixer, the electrical resistance of concrete increases in response to strain or stress. As the concrete is deformed or stressed, the contact between the fiber and cement matrix is affected, thereby affecting the volume electrical resistivity of the concrete. Strain is detected through measurement of the electrical resistance. So, the smart concrete has the ability to sense tiny structural flaws before they become significant, which could be used in monitoring the internal condition of structures and following an earthquake.
SELF-CONSOLIDATING CONCRETE (SCC)
It has brought about “Revolution” in the precast industry. No compaction required in SCC still it results in no segregation and shows excellent flow-ability. It eliminates vibration and yields smooth surface finish with no voids.
CONDUCTIVE CONCRETE:
Concrete has been used for many years as a composite material that has excellent mechanical properties and durability for construction. However, concrete is a poor electrical conductor, especially under dry conditions. Concrete that is excellent in both mechanical and electrical conductivity properties may have important applications in the electrical, electronic, military and construction industry (e.g. for deicing road from snow). Traditional methods can warm roads, but installation cost is high and the procedure is complicated. The principle behind it is the use of cement to bind together electrically conductive materials such as carbon fiber, graphite and ‘coke breeze’ a cheap by-product of steel production to make a continuous network of conducting path- way. The design formulation is based on the ‘electrical percolation’ principle by which the composite conductivity increases dramatically by several orders of magnitude when the content of the conductive phase reaches a critical ‘threshold’ value. Further increases in the conductive phase content boost composite conductivity only slightly. The design specifies an amount just over the threshold content, assuring high conductivity and mechanical strength as well as good mixing conditions.
MELLOSE NON-DISPERSIBLE UNDERWATER CONCRETE ADMIXTURE
Many under-water civil engineering structures are affected not only by the presence of water or salt but also by water pressure; flow of water, and by the different material’s density. These factors could cause cracks, corrosion, and dispersion of concrete particles. Mellose is a viscose agent based on under water Cellulose (Hydroxy Propyl Methyl Cellulose). It is commonly referred to as a self-leveling agent that increases viscosity when is dissolved in water. It can be also described as an anti-wash-out concrete or non-dispersible concrete mixture. When Mellose is added, it prevents the loss of cement in the mortar and the separation of the concrete particles due to its increased viscosity. It combines first with the water than with the cement and the other concrete particles.
Robust growth in construction industry has propelled demand for rapid strength concrete. The construction of high rise and multi-storied buildings along with the need for eco-friendly materials led to the product market expansion. Rapid strength concrete’s usage in the maintenance and restoration of old infrastructure also led to its growing popularity in the business. The increasing construction spending mainly in the emerging economies will create a favorable environment for the industry’s growth in the future.
Info Source