Flexible battery cell drives wearable innovation
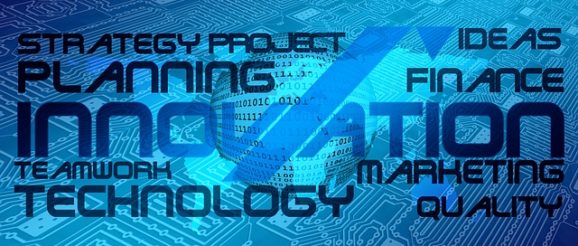

Physicists and chemists have conducted countless experiments and invested heavily in R&D to develop batteries that enable and improve the products we increasingly depend on. While they’ve been successful in increasing energy density through the development of various chemical materials and manufacturing technology, form factor remains a key barrier for design engineers and product developers.
The battery imperative
Batteries have become one of the most important components for product performance and design as more and more products have become portable, include more functionality and require more power to work. And now battery form factor is an essential consideration for creating attractive and comfortable devices.
While product components including sensors and chips tend to be small enough to enable flexibility in product design, the traditional rigid battery limits innovation in the majority of cases. As wearables and IoT device manufacturers compete with products that provide higher and higher levels of usability and comfortability, demand for thin and flexible batteries is rising.
Battery use cases
Lithium ion, which boasts high energy density, is the dominant battery chemistry used in everyday products. Rigid batteries and other form factors are useful for a variety of applications, but as you’ll see in table 1, thin, flexible batteries are enabling next-generation products.
Thin, flexible battery
As you might expect, the biggest difference between flexible batteries and traditional rigid ones are the flexible battery’s ability to withstand pressure at various degrees and still perform as expected. It can be bendable, rollable and even foldable in any direction. This is critical for new products that need to be curved or bent along the surface of an object or, in the case of wearables, a part of the body.
Moreover, flexible batteries are needed to turn existing products into Internet of Things or so-called connected devices. These devices need to maintain, or even improve, their original look and feel, while adding features that make them smart. A thin and flexible battery as shown in figure 1 can be used to make the change seamless.
Let’s take a jacket as an example. If a product designer wants to build a jacket with LED lights on the back for safety in defense or security use cases, and have a rechargeable battery embedded inside the jacket for emergencies, it is essential to design the jacket in a way that ensures the productivity and safety of the people wearing it.
Wearers should be able to focus on their task, whether they’re working, biking or running at night, or performing other activities, without being bothered by a bulky battery in the pocket or unbalanced weight in one side of the jacket. Therefore, the ideal location would be on their back. With a thin, flexible battery, users won’t even notice it is there. This is the only way to ensure user satisfaction and that they wear the jacket as often as needed.
In order to customize this seamless battery for devices, wearables and, in this case, the jacket, here are sample questions designers can ask to determine battery capacity, since capacity is calculated by the design of the system:
- How long the lights are on per day
- How often the battery inside the jacket should be charged
- How it should be charged
- Whether it is necessary to communicate with the system when the lights go off
- What is the maximum thickness the jacket can handle
- What capacity and dimensions are required. Battery size will be determined based on the available area and energy capacity needed to run the system. If the priority of the product design is to make it thin, it is possible to increase width and length. If it is necessary to fit the battery into a small area, the thickness can be increased while width and length decrease. The degree of flexibility will be decided based on the thickness.
Testing flexible battery viability
In the case of lit jacket, the following tests proved the viability of a lithium ion flexible battery.
Performance
The battery was bent continuously (dynamic bending), 10,000 times, with a bending radius of 20mm while it was charging and discharging for 10 hours (0.1C). The results seen in figure 2 show almost no difference in performance between flexible, bent and traditional, non-bent cell. Even with constant dynamic bending, the flexible battery performed at the same efficiency and capacity as the non-bending baseline level. Thus, the jacket can be bent and scrunched without concern that the battery will degrade.
Safety
Safety is one of the key concerns for consumers. It is important to ensure the stability of battery performance so that it does not catch on fire or explode. It’s crucial to ensure that the integrity of flexible batteries is not affected, despite numerous bending cycles.
When used in wearable applications, you must also make sure that, even if it is cut or pierced, nothing can leak out and harm the wearer’s skin. For this purpose, batteries made of gel-polymer have a big advantage over those made with liquid electrolyte, which can be prone to leakage. A test
was done to check the safety of this wearable product life in relation to flexibility and performance under different conditions. 10,000 bends were done first to analyze the life cycle of cell. (Cycle refers to how many times charging and discharging can safely be done). As shown in figure 3, the bent battery performed almost the same as traditional rigid, non-bent batteries to 1,000 cycles with capacity retention rate above 80%.
Next- generation thin, flexible batteries are enabling a new era of wearables and IoT-connected devices. By making battery considerations a core component of your design parameters, you can innovate high-performance, useful and compelling products.
About the author:
EJ Shin is Managing Director at Jenax –