Innovation leads the country’s garment success
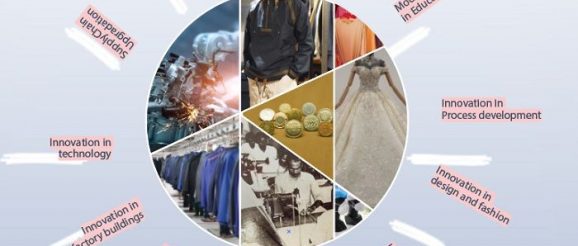
Bangladesh is now the most reliable and committed garments sourcing country to buyers. The accomplishment came with a journey of nearly four and half decades. Beginning with the shipment of a few million US dollars in the late 1970s the amount reached $35.81 billion in the year 2021. During the long journey of the apparel industry, innovation has led the sector to come today’s position.
How textile and garments industry recovered so fast and booming
There are many analyses available in the market. However, one main point hide-out behind other discussions which is most of the factories are now more process-driven, innovative and agile. They don’t just sew the apparel but have very good business and market insights that help them to sustain and recover fast.
Even the sector is likely to witness a booming inflow of work orders from the international clothing retailers and brands as the country is already a major hub for garment items.
With the recovery of the global supply chain, the garment export grew in such a way that for the first time the monthly export earning of garment items crossed $4 billion mark in December last year.
Now garment manufacturers are confident about supplying garment products worth $8 billion a month to international buyers after Bangladesh consolidated its place in the global supply chain by remaining open for businesses even during the peak of the coronavirus pandemic.
Even in the time of COVID-19, the innovations took place in the sector. Bangladesh has already become a good sourcing destination for COVID-19 related products like Personal Protective Equipment (PPE), bed sheets, medical and hospital technical textile and isolation bed sheets.
“Bangladesh is gradually getting ready to cater garment work orders worth $7 billion to $8 billion every month. At present, we are not capable of supplying products worth $7 billion to $8 billion, but we are expanding our capacity,” recently Faruque Hassan said at the ERF Dialogue in Dhaka.
All these are success stories of Bangladesh in the garment sector over the last four and half years. However, the success stories were made through the innovation of the hard-working entrepreneurs and exporters. The innovations took place in products diversification, marketing, management, technologies, logistics and workers’ productivity.
Despite a lot of constraints and negativities, the shipments of the garment have been rising from the very beginning of the trade except only a few incidents, because of innovation by the entrepreneurs.
The glowing example of innovation in the sector is noticed in the image building after the twin industrial disasters including Tazreen Fashions fire and Rana Plaza building collapse. After the Rana Plaza building collapse the entrepreneurs in the garment sector started constructing the green factory buildings to remove any bad image in the sector globally.
Innovation in factory buildings
Currently, Bangladesh is globally champion in green garment factories as the country has 153 green factories including the highest number of platinum-rated and gold standard factories in the garment sector.
More than 500 garment factories are waiting to be certified to be Leadership in Energy and Environmental Design (LEED) by the US Green Building Council (USGBC). The image of the country’s garment sector has been brightened due to the innovative ideas of green buildings and also been saving nearly 30 percent energy and water consumption.
Innovation in technology
The local entrepreneurs are so prompt that they are using the latest technologies in the garment sector to have the maximum outputs. For instance, few textile and spinning mills have started using robot in their factories for more and efficient production of yarn as the demand for finer varieties of yarn has been rising in the country.
The garment factories also started automation in different sections to improve the productivity as they have to do business with facing a lot of competition from other garment-producing countries.
The application of automation has already reduced their cost of production to a bit and they are becoming more competitive in the global clothing supply chain. They stared using innovative automation in production and sewing.
Innovation in design and fashion
The innovations have come in the design and fashions over the last few years as the local garment manufacturers are also trying to develop design locally reducing over dependence on the designs supplied by the buyers only. Many modern factories have their own design studios for producing new fashion and design in garment items.
There are many factories those who have office and target market countries to understand fashion trends. Eventually which helping them to take decision easily.
Innovation in primary textile sector
A lot of innovation happened in the country’s primary textile sector over the years as the millers have brought new machineries and managements for higher growth, said Monsoor Ahmed, Chief Executive Officer of Bangladesh Textile Mills Association (BTMA).
Innovation has taken place in spinning, weaving, finishing, printing and sizing over the years, he said.
Monsoor also said the current investment in the primary textile sector is $16.0 billion and by 2025 the total investment in the textile sector will cross $20billion.
The market demand for innovative goods inspired the local entrepreneurs for high investment in the sector, Monsoor also said.
Innovation in accessories industry
Abdul Kader Khan, the immediate past President of Bangladesh Garments Accessories & Packaging Manufacturers and Exporters Association said once upon a time hardly any factory used to produce the garment accessories like hangers, zippers and cartons.
However, now Bangladesh is self-reliant on garment accessories as the local garment exporters need not to import from other countries, he said.
Many of the local entrepreneurs have been producing many innovative accessories garment items for meeting the demand, Khan said.
BGMEA initiative for innovation centre
Hassan said BGMEA has been making an innovation house and it may start working in next three or four months. The first of its kind Center is expected to elevate Bangladesh apparel industry to the next level by bridging the knowledge gap in the industry and connecting stakeholders as critical partners of the knowledge hub.
The main objective of the Center is to make a paradigm shift in the product basket from the basics to high-end. The innovation centre will mainly work to bring new items in design and fashion, marketing, management and in training.
Moreover, BGMEA has been conducting studies on three important issues including technical garment products, fibre diversification and the post-COVID-19 roadmap to lift the industry to the next level.
How ‘Textile Today Innovation Hub (TTIH)’ enhancing industry capacity
Textile Today is a communication and networking platform that has been functioning as an effective ‘Innovation Hub’ from 2021. It is resilient to reveal companies’ best practices; showcase employer branding; conduct training; organizing seminars, symposiums and exhibitions; impart industry intelligence and consultancy etc. It helps businesses to grow, innovate and sustain the textile and apparel industry globally. TTIH activities are run under mainly three streams:
Methodology and achievement of Textile Today Innovation Hub
‘Setting Transformation Blueprint’ (STB) is the method to do innovation/change at the partner companies. ‘Work on small, Make on spot’ is the method of doing STB. STB projects are done by engaging Industry Experts, Academic Experts, Learner (student/career seeker). Each STB projects are completed in 9 steps.
Following the well-defined methodology, the Innovation Hub already initiated 80+ projects, from which 45+ projects result received and finally 23 results shared with the industry (continuing).
To do this gigantic work, the Innovation Hub engaged 30+ factories ( including Robintex Group, HAMS Group, Mondol Group, Noman Group, APS Group, Epyllion Group, Mosharaf Group, South West Composite Ltd, Fatullah Dyeing & Calendering Mills Ltd. etc.), 170+ Experts from the industry and academy.
Innovation often takes place through the development of more-effective products, processes, services, technologies and business models. Despite massive investments of management time and money, innovation remains a frustrating pursuit in many companies.
Why is it so hard to build and maintain the capacity to innovate? The reasons go much deeper than the commonly cited cause: a failure to execute. The problem with innovation improvement efforts is rooted in the lack of an innovation strategy. That’s why company’s top management should take leadership in making innovation which ultimately will help in business growth and sustainability.