Cromograf’s pioneering path to sustainable packaging production leads to Gold innovation award
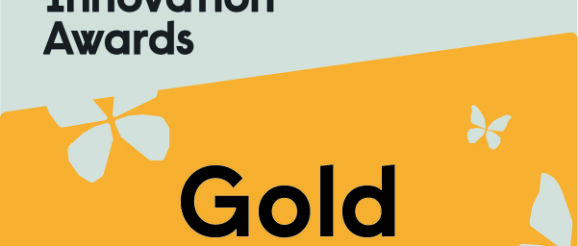
Fourteen-year ECG journey with Kodak FLEXCEL NX System positions Cromograf as technology leader in Latin America
Over the last decade and a half, Uruguayan flexo packaging pre-press trade shop Cromograf has reached beyond its Montevideo base to become a model for similar businesses in Latin America. CEO Alejandra Acosta Salati puts this down to what she describes as the company’s “restless DNA, which is always motivating us to improve. As a result, we have become something of a laboratory of innovation that has driven change in other trade shops.”
Cromograf’s embrace of sustainable production is a good example of the company’s pioneering spirit. While the thoughtful, planned use of resources may now be a mantra for all stakeholders in the packaging supply chain, Cromograf already embarked on the path in 2008. And Alejandra can almost pinpoint the precise date: “In a way, it started the day my father, Miguel Angel Acosta, saw the FLEXCEL NX System. He immediately recognized the potential of a technology that eliminated variables and brought new levels of consistency to the flexo process.
“We believe in streamlining and standardizing processes as much as possible, and the FLEXCEL NX System provided the best platform for standardized, repeatable production. That’s the way it was then, and it’s the same now.”
A technology leader in ECG
Cromograf installed the first FLEXCEL NX Mid system in Latin America in 2008, and a few months later began experimenting with Extended Color Gamut (ECG) printing; a process in which – 14 years later – Cromograf is recognized as the technology leader in Latin America and beyond.
ECG is the foundation of Cromograf’s sustainability policy, explains Alejandra, because of the savings and efficiencies that are inherent in the basic idea of printing as much as possible using a fixed CMYK ink set. “ECG uses fewer plates, fewer special inks, and cuts substrate wastage during job set-up. In addition — and this is very important for brand owners — the standard ink set means we can print multiple jobs simultaneously. This makes it easier to meet converters’ minimum order quantities despite ordering smaller volumes, which helps with test-marketing of new packaging ideas.”
None of this, Alejandra continues, would be possible without FLEXCEL NX Technology. “The whole concept of ECG is to remove variables that can impact on productivity and reduce sustainability. FLEXCEL NX Technology allows for standardized production to achieve predictable, consistent results. It’s an exceptional plate technology that offers high productivity and process stability. The dot reproduction remains stable print after print, giving us consistency, longer plate life and fewer unscheduled press stops for cleaning.”
Gold Award recognition
The company’s achievements have now been rewarded with a Gold Award in the Miraclon-sponsored Global Flexo Innovation Awards (GFIA), awarded for excellence in Print Production Workflow, Commitment to Sustainable Print, and Creative Use of Graphic Design.
For Alejandra, the Global Flexo Innovation Award is a welcome recognition of the strategy started by her father and continued under her management. “We have been printing with CMYK and ECG since 2008, and take pride in the quality of what we produce. The difference today is that people are taking notice.”
Jointly with long-standing converter customer of more than 30 years, Strong SA, Cromograf submitted a series of packaging jobs, accompanied by a level of detail that impressed the judging panel by clearly demonstrating the savings and benefits delivered by ECG. For example, the winning entry — flexible packaging for a range of flavored rice — achieved remarkable savings by using ECG instead of the previous production process:
- no special inks (compared to 15 using CMYK + Special Inks)
- 28 plates (compared to 49)
- 28 mounting tapes (compared to 49)
- 28 washouts (compared to 49)
Similar levels of savings were achieved on every one of Cromograf’s entries, including one job for which Cromograf saved 10.8 kg of red ink. Add in the reduced usage of mounting tapes and cleaning solvents, less time spent setting up jobs, and a reduced storage space for inks and plates and the savings quickly add up.
Approach to new projects impresses judges
The GFIA judges were also impressed by how Cromograf approach each new packaging project in order to decide how best to apply ECG. Dr Chip Tonkin, from the Sonoco Institute of Packaging Design and Graphics, observed: “They do a lot of analysis on an incoming job to determine if it needs anything beyond CMYK, and they take extreme measures to do it within CMYK for the vast majority of jobs. For most colors, you can achieve it with CMYK, particularly when you optimize your CMYK.”
Says Alejandra: “The packaging value chain begins with an idea and ends when the packaging is in the hands of the consumer. Along the way, we consider the use of every resource input, controlling the process at every stage with the goal of producing a stable product with a minimal carbon footprint.”
Analysis begins with an initial discussion with the design team, and Cromograf’s extensive experience immediately comes into play. Explains Alejandra: “The way we manage color, media and inks means we know immediately which colors work best with ECG and can advise how slight design modifications can reap major efficiency and sustainability benefits.” (As an example of this attention to detail, for one of the jobs entered for the GFIA Cromograf positioned cut marks and process control targets inside the job, leading to a one per cent saving in media, which, as the judges noted, added up to significant figures over the total production run.)
As we wrap up our discussion, she also acknowledges the contribution made by the teams at Miraclon. “It helps to be dealing with an excellent team of individuals over many years. We regard both Miraclon and our local dealer, Lumila, as a vital part of our business.”
About Miraclon
Miraclon is the home of KODAK FLEXCEL Solutions, which have helped transform flexographic printing for more than a decade. The technology, including the industry-leading FLEXCEL NX and FLEXCEL NX Ultra Systems, and FLEXCEL NX Print Suite that enables PureFlexo Printing, maximizes on-press efficiency, delivers higher quality and overall best-in-class results. With a focus on pioneering image science, innovation, and collaboration with industry partners and customers, Miraclon is committed to the future of flexo and continues to be positioned to lead the charge. Find out more at, and follow us on LinkedIn and YouTube.