JEC Composites presents 2023 Innovation Award finalists
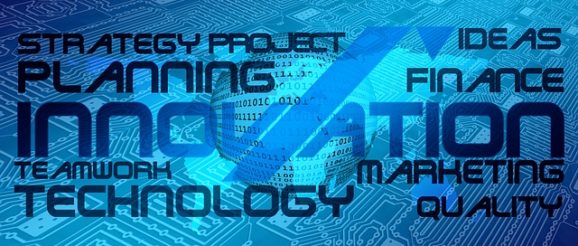
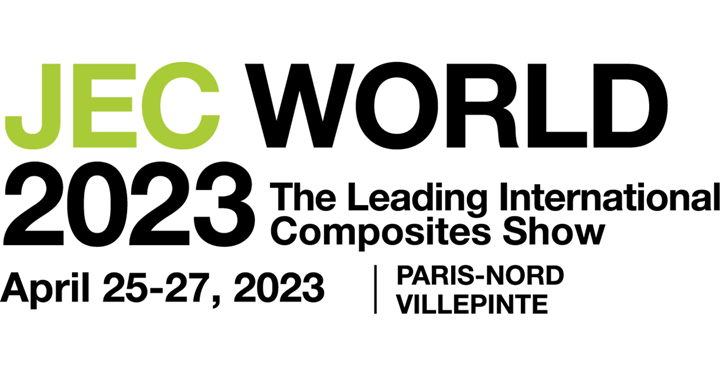
JEC World 2023 the world’s leading international composites trade show taking place April 25-27 in Paris, France, has announced the official lineup of finalists for this year’s Innovation Awards.
Each year, the JEC Composites Innovation Awards celebrate successful projects and cooperation between players of the composites industry. Over the last 25 years, the JEC Composites Innovation Awards program has involved more than 1,900 companies worldwide. Open to any company or R&D center with a strong collaborative innovation or concept to present, more than 214 companies and 527 partners have been rewarded over the years for the excellence of their composites innovations and fruitful collaboration. These composites champions are awarded based on multiple criteria such as partner involvement in the value chain, complexity or commercial potential of the project.
More than just a ceremony, these awards are an opportunity to bring possibly undisclosed projects in the limelight as well as a source of inspiration and stimulation to an expert audience always eager to reach out towards new horizons.
After pre-selection of the 30 finalists, one winner will be selected in each of the 11 categories: Aerospace – Parts; Aerospace – Process; Automotive and Road Transportation – Design Part; Automotive and Road Transportation – Process; Building and Civil Engineering; Circularity and Recycling; Digital, AI and Data; Equipment, Machinery and Heavy Industries; Maritime Transportation and Shipbuilding; Renewable Energies; and Sports, Leisure and Recreation.
The international jury representing the entire composites value chain includes:
• Dr. Deniz Korkmaz, CTO, Kordsa Teknik Tekstil AS
• Pr. Véronique Michaud, head of the Laboratory for Processing of Advanced Composites, Ecole Polytechnique Fédérale de Lausanne
• Dr. Alan Banks, UK Innovations manager, Ford Motor Co.
• Pr. Christophe Binetruy, professor of mechanical engineering, Centrale Nantes
• Mr. Dale Brosius, CCO, IACMI – The Composites Institute
• Dr. Enzo Cosentino, technical authority and composite expert, Airbus
• Mr. Guy Larnac, materials, structures and industrialization technical coordinator, Ariane Group
• Dr. Karl-Heinz Fueller, manager future outside and materials, Mercedes-Benz
• Pr. Kiyoshi Uzawa, director/professor, Innovative Composite Center, Kanazawa Institute of Technology
• Pr. Sung Kyu Ha, professor, Hanyang University
• Mr. Michel Cognet, chairman of the board, JEC
The awards ceremony will take place in Paris on March 2, 2023.
Hybrid seating structure
Hybrid aircraft seating structure designed and demonstrated under sustainability criteria, based on an easy-to-recycle lightweight composite material and produced with efficient automated processes.
Photo Credit: Fraunhofer ICT
Integrally stiffened TP primary structure
Development of a high-rate molding process using aerospace-qualified thermoplastic materials for parts with complex geometries enabling the replacement of heavier metallic components with composites.
Lunar lander with carbon monocoque structure
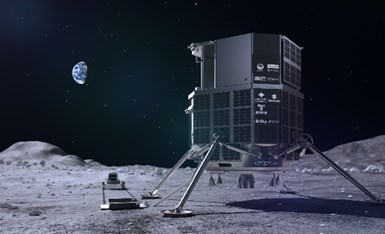
Photo Credit: Toray Carbon Magic
Development of a lightweight structure by committing completely to the pursuit of specific strength and stiffness. Encouragement of the airframe structure as close to a one-piece composite structure as possible.
Manufacture a Krueger wing flap in thermoplastic
Innovative Krueger flap produced in-situ with an automated thermoplastic consolidation process.
- Partner(s): Loiretech (Bouguenais, France), AFPT GmbH (Doerth, Germany) and Sonaca SA (Gosselies, Belgium)
Self-cure of CFRP for aerospace applications
Self-cure — joule heating of CFRP to cure temperature — significantly increasing the energy efficiency of the curing process, reducing cure time and increasing the quality of cured components.
Hydrostatic membrane press technology for composites
The metal membrane press concept allows for the production of high-temperature thermoplastic composites using a flexible metal tooling side to achieve high laminate quality and production rates.
Photo Credit: CTC GmbH
Category: Automotive and Road Transportation (Design Part)
2022 Toyota Tundra composite seatback design
Taking an all-steel assembly that contained 60 stamped and welded parts and integrating it into four composite parts reducing weight by 20% while passing all relevant crash test requirements.
World’s first carbon roll cage for production cars
Extreme lightweight carbon roll cage, to be road legally fitted into a production car, enabled by engineering a unique geometry.
Photo Credit: Dr. Ing. h.c. F. Porsche AG
DRIFT technology
Wire-shaped inserts for load-oriented fiber reinforcement of injection-molded thermoplastic components.
Category: Automotive and Road Transportation (Process)
Koridan – active core molding
Active core molding process for the self-forming of CFRP to its final shape.
Photo Credit: Alia Mentis srl
BEV battery protection plate in composite design
Largest, innovative, sustainable BEV underride guard in thermoplastic sandwich lightweight design with highly efficient one-shot manufacturability for the new Audi Q8 e-tron.
- Audi AG (Germany)
- Partner(s): Polytec Group (Netherlands)
Graphene from waste tire for lightweight vehicles
Nanografen produces graphene from waste tires in pilot scale used as a co-reinforcement in compounding process for cost-effective and lightweight automotive composites without changing the mold.
Category: Building and Civil Engineering
CFRP cable-net glass façade
An innovative and novel CFRP cable-net structure for glass façades providing maximum transparency with no visible supporting structure, enabling a clear design language for building envelopes.
- Carbo-Link AG (Switzerland)
- Partner(s): seele (Germany)
Sheephouse wood bat mitigation structure
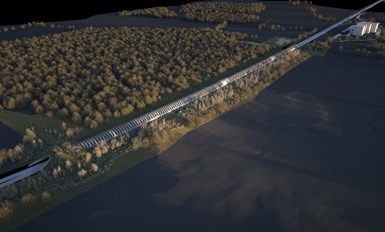
Photo Credit: Asset International Structures
Provide a safe structure, ensuring the protection of a rare species of the bat using off-site modular construction, minimizing embodied carbon, and maximizing safety using our FRP and concrete units.
Composite roof for the stadium of Real Madrid
Three elements are mechanically joined to reach beams with a span of 75 meters. The manufacturing process was infusion with double VAP membrane, avoiding the use of holes in the core and excess polymer.
Category: Building and Civil Engineering
Circular welding process for thermoset composites
A super-fast, reusable welding process that creates high-performance joints between fast-curing epoxy composites involving a co-bonded thermoplastic interlayer that enables the design for circularity.
100% recycled CF-spun yarn and applied products
Photo Credit: Toyota Industries Corp.
One-hundred percent recycled CF-spun yarn compatible to pultrusion process. Establishment of comprehensive CF circulation system from recycling to product application.
True bio-based thermoset resin
Development of a new, low-viscosity thermosetting resin based on lignin. Designed to work with established processes, i.e., VARI. It reduces the carbon footprint of composites significantly.
Category: Digital, AI and data
Auto-teaching algorithm for thermography
Thermography is a fast way to robotically inspect a composite part. The innovation lies in an auto-teaching algorithm that automatically defines the optimal path(s) for inspection.
AI-powered, cloud-based, real-time process control
sensXPERT is an end-to-end, integrated equipment as a service solution for the plastics manufacturing industry solving challenges around consistent process stability while ensuring cost efficiency.
In-process AFP manufacturing inspection system
In-process AFP manufacturing inspection system (IAMIS) for automated fiber placement (AFP) head to detect manufacturing defects and a user-friendly augmented reality visualization module.
Category: Equipment, Machinery and Heavy Industries
Composite high-speed railway car body
Development of a hybrid composite car body structure for a high-speed train made of CFRP composite and aluminum with a 25% weight reduction. The demonstrator is a whole car body of an intermediate coach of Talgo 350 at TRL 6/7 1:1 scale.
Isotruss carbon fiber tower
Isotruss carbon fiber towers are up to twelve times stronger than steel for a given weight, or as little as one-twelfth the weight for a given load, depending on the design, site and specifications.
Lightweight booms for agricultural sprayers
A modular concept of sprayer boom with intelligent use of composites and manufacturing processes, to provide a scalable, cost-efficient and environmentally friendly solution for agriculture.
Category: Maritime Transportation and Shipbuilding
Automated, mold-less composite wing sail for yacht
Rondal, Curve Works and Artemis Technologies present a fully customizable, automated, composite solid wing sail assembled from load bearing carbon fiber skin panels manufactured on adaptive tooling.
Solid sail mast
Industrialization of the fabrication of a very large mast to fit to price and delay of the marine industry market.
Serial use of hemp for small parts in boating
Development and integration of a glass-hemp complex in the industrial production of composite parts in closed mold process for boatbuilding applications.
- Group Beneteau (France)
New acrylic adhesives for a better world
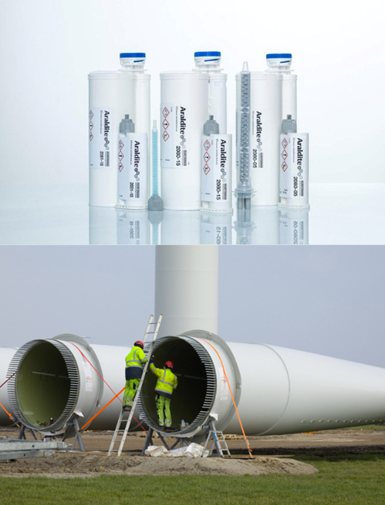
Photo Credit: Huntsman Advanced Materials
New non-flammable, low-odor and primer-free structural acrylate adhesives with a favorable health and safety profile, providing exceptional bonding performance on multiple substrates.
Opticore design platform for blade lightweighting
OptiCore is a software enabling more efficient core kits for wind blades, considering mechanical properties, geometrical fit, blade weight, resin uptake, manufacturing cost, health and permeability.
Corpower WEC – clean electricity from ocean waves
Industrial-scale wave energy converter enabled by an innovative mobile filament winding factory for composite hull manufacturing at scale.
Category: Sports, leisure and recreation
Recyclable thermoset CFRP composite bike
Thermoset CFRP bicycle was made from recyclable EzCiclo prepreg. Composite parts can be recycled by CleaVER liquid to reclaim resin and fiber enabling closed-loop recycling of thermoset composite.
Integrated loop technology bicycle frame
A bicycle frame produced by an automated fiber winding process, incorporating continuous fiber tube joining development integrated loop technology (ILT).
Photo Credit: CompoTech Plus Spol
Modular suitcase made from rCFRP
Application of rCFRP and natural flax fibers with Roctool TP technology. Recycle and reusing from Expliseat. Modular design makes it possible to recycle the composite parts from the products.