VW’s US Innovation Hub just revealed 4 EV breakthroughs
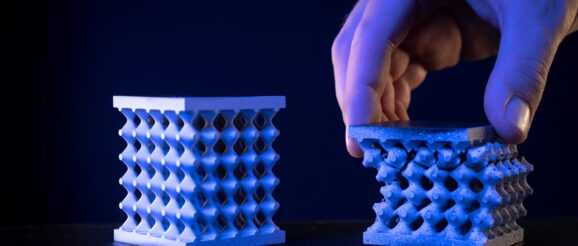
VW’s US Innovation Hub just announced four breakthroughs in electric mobility and sustainable transport – here’s what the research center has achieved.
Volkswagen’s Innovation Hub opened in 2020 at the University of Tennessee (UT) Research Park at Cherokee Farm in Knoxville. The federally funded Oakridge National Laboratory (ORNL) is there too. VW collaborates with UT and ORNL scientists on its EV research. Here’s what the VW Innovation Hub has been up to:
AI-optimized EV battery pack frame
Volkswagen researchers are working on new material structures to reduce vehicle weight, which in turn helps to increase the range of EVs. The aim of the first pilot is to replace the steel frame that houses the EV battery pack with something lighter.
The team used artificial intelligence (AI) with millions of parameters on UT’s high-performance computer cluster to develop a modular repeating structure in the shape of tiny pyramids (main photo). The structure can be 3D-printed from liquid resins and can hold 30K times its own 0.15 lb weight (68g). So this frame would be up to 60% lighter than the steel frame. The researchers found that the resin frame absorbs more energy than the steel frame (they’re testing its durability in the photo above), which means it’s robust.
Electrek’s Take: Intriguing. As VW is claiming that its resin frame is lighter and stronger – and we’re going to assume it’s made sustainably – I hope to see this progress beyond the pilot stage and will keep an eye on it.
EV interiors made of paper
Scientists at UT’s Center for Renewable Carbon are using paper as a recyclable alternative to plastic parts and foils for EV interiors. The team has patented a method of preforming and hot-pressing cellulose fiber-reinforced thermoplastics into durable interior parts.
The recyclable paper-based composites can be transformed into various interior shapes and sizes, and different textures and colors can be added.
VW says it’s “checking opportunities” to include paper-based interior parts in future models and “work to support industry-scale production.”
Electrek’s Take: Any move toward recyclable materials and away from plastics can’t come fast enough. No timeline is given here from VW on industry-scale production plans; it’d be great to see this material used by VW in mass-produced EVs.
Lightweight fiber composite body parts
Researchers re-created the liftgate of a 2020 Volkswagen Atlas using sheet molding compound, a type of fiberglass-reinforced plastic. The new liftgate was 13 pounds lighter than the metal one, resulting in a weight savings of more than 35%. That would help increase the range of EVs.
VW says that the fiber composite liftgate doesn’t need changes in assembly sequence compared to metal liftgates, so the former can be produced in high volumes.
Researchers have recently further refined molding processes and ways to optimize durability, quality, and design options.
Electrek’s Take: Fiber composite body parts are already in production at Bentley and Lamborghini, which are part of the Volkswagen Group. They’re using the new materials and the molding process for the Bentley Continental and the Lamborghini Aventador. Those are luxury cars, so it’s not exactly mass production, but researchers are also exploring fiber composite pickup truck beds and other components.
Wireless EV fast charging
VW’s team has patented a coil and charging pad design with silicon-carbide materials. In early trials, the automaker says that the prototype silicon-carbide inverter system has proven to be highly efficient. The research team has been able to increase the charging power level up to 120 kW with this prototype from an earlier 6.6 kW prototype, and their goal is to reach 300 kW.
Electrek’s Take: There’s no further elaboration from VW on what’s next for its wireless EV fast charging project, so I’m guessing this is still in early stages. It’d really need a lot of finessing to be viable on a widespread scale. Still, to progress from 6.6 kW to 120 kW is an achievement. It’d be nice to just pull up over a charging pad in a parking spot and start charging, especially when it’s extremely hot – that’s you down south – or when it simply won’t stop raining, like us up here in the Northeast.
I hope at least half of these projects go into mass production and become cost-effective. But seeing how VW has implemented a short-term spending freeze, it’s probably not going to happen soon.
Photos: Volkswagen
If you’re an electric vehicle owner, charge up your car at home with rooftop solar panels. To make sure you find a trusted, reliable solar installer near you that offers competitive pricing on solar, check out EnergySage, a free service that makes it easy for you to go solar. They have hundreds of pre-vetted solar installers competing for your business, ensuring you get high quality solutions and save 20-30% compared to going it alone. Plus, it’s free to use and you won’t get sales calls until you select an installer and share your phone number with them.
Your personalized solar quotes are easy to compare online and you’ll get access to unbiased Energy Advisers to help you every step of the way. Get started here. –ad*
You’re reading Electrek— experts who break news about Tesla, electric vehicles, and green energy, day after day. Be sure to check out our homepage for all the latest news, and follow Electrek on Twitter, Facebook, and LinkedIn to stay in the loop. Don’t know where to start? Check out our YouTube channel for the latest reviews.