A catalyst to make renewable paints, coatings, and diapers from trees and corn – Innovation Toronto
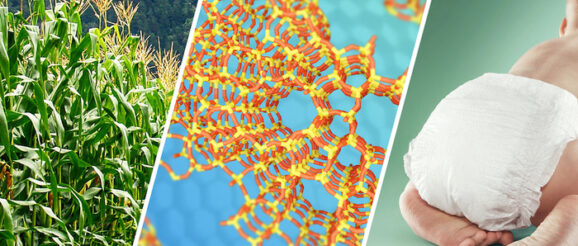
Research discovery will enable the manufacturing of biorenewable materials from trees and corn
A team led by University of Minnesota Twin Cities researchers has invented a groundbreaking new catalyst technology that converts renewable materials like trees and corn to the key chemicals, acrylic acid, and acrylates used in paints, coatings, and superabsorbent polymers. The new catalyst technology is also highly efficient, which means lower costs for manufacturing renewable chemicals.
The new catalyst formulation converts lactic acid-based chemicals derived from corn to acrylic acid and acrylates with the highest yield achieved to date. The technology exhibits substantially higher performance when benchmarked against other classes of leading catalysts.
The research is published online in the Journal of the American Chemical Society Gold (JACS Au), a leading open access journal of the American Chemical Society.
The research team was supported by the U.S. National Science Foundation through the NSF Center for Sustainable Polymers, a multi-university collaborative team with a mission to transform how plastics are made, unmade, and remade through innovative research.
The public is most familiar with acrylic acid and associated acrylates through its uses in everyday items from paints and coatings to sticky adhesives to superabsorbent materials used in diapers. These chemicals and materials have been made for the last century from fossil fuels. But in the last few decades, the corn industry has been growing to expand beyond food and livestock feed to manufacturing useful chemicals. One such corn-derived chemical is sustainable lactic acid, a key ingredient in the manufacturing of the renewable and compostable plastic used in many everyday applications.
Lactic acid can also be converted to acrylic acid and acrylates using catalysts. However, until this new catalyst discovery, traditional catalysts were very inefficient achieving low yields and making the overall process too expensive.
“Our new catalyst formulation discovery achieves the highest yield to date of acrylic acid from lactic acid,” said Paul Dauenhauer, professor in the University of Minnesota Department of Chemical Engineering and Materials Science. “We benchmarked the performance of our new catalyst to all prior catalysts, and the performance far exceeds previous examples.”
The new catalyst formulation substantially reduces the cost of manufacturing renewable acrylic acid and acrylates from corn by improving yield and reducing waste. For the first time, this could reduce the price of renewable acrylic acid below fossil-derived chemicals.
The economic opportunity generated by the new catalyst is being pursued by Låkril Technologies, a startup company that aims to manufacture low-cost renewable acrylic acid and acrylates. By licensing the catalyst technology from the University of Minnesota, Låkril Technologies will develop the technology beyond the laboratory.
“Chemical manufacturing has relied on a class of catalysts called ‘zeolites’ for half a century,” says Dr. Chris Nicholas, CEO of Låkril Technologies. “Because the new catalyst discovery is based on a zeolite formulation already available at scale, our new process to make acrylic acid and acrylates will achieve low cost with low risk.”
Låkril Technologies, located in Chicago, already has received $1.4 million in pre-seed financing to scale the process. The Iowa Corn Growers Association led the financing with participation from the Kentucky Corn Growers Association along with grants from the Minnesota Corn Research and Promotion Council, Indiana Corn Marketing Council, Corn Marketing Council of Michigan, along with Small Business Innovation Research (SBIR) awards from both the U.S. Department of Agriculture and the U.S. Department of Energy.
At the University of Minnesota, the research team plans to continue their basic research on catalyst design to understand the fundamental aspects of the chemistry with financial support from the Center for Sustainable Polymers headquartered at the University of Minnesota.
“This is a wonderful example of how addressing important basic research questions that are at the heart of fundamental catalysis can lead to innovative new processes that have true technological promise,” said Marc Hillmyer, director of the Center for Sustainable Polymers and a professor in the University of Minnesota Department of Chemistry. “A grand challenge in the Center for Sustainable Polymers is the efficient and sustainable conversion of biomass to polymer ingredients, and this work represents a groundbreaking solution to that challenge that will have lasting impact.”