Advanced Analytics Drive Digital Innovation in Midstream Oil and Gas | Seeq
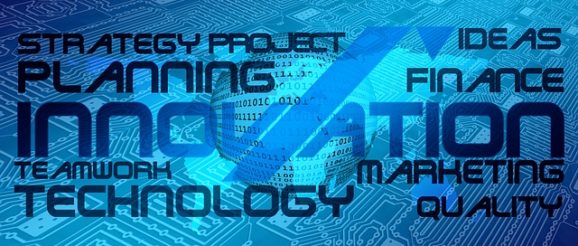
North America is expected to continue its global growth as an energy provider, and optimizing the performance of midstream assets will play a key role in this growth. As the industry emerges from the low-price crude environment, midstream operators are looking to invest in digital initiatives that provide opportunities for optimization.
With low capital expenditure requirements and a quick return on investment (ROI), digital initiatives are empowering personnel across organizations to unlock the full potential of midstream assets to ensure productive and efficient operations.
By providing access to all operational and additional diagnostic data in a central location, Seeq enables midstream oil and gas organizations to explore advanced analytics and discover real-time process improvements to improve their bottom lines.
Midstream Analytics Using Seeq
Seeq classifies midstream oil and gas assets into the following three categories with associated use cases:
1. Production, gathering, and processing
Accurate measurements of oil, gas, and water
Separation and purification of products
Rotating equipment monitoring such as compressor bearing failure prediction, monitoring for and identifying changes in operations with anomaly detectors and identification and prediction of liquid loading events
Root cause identification of flaring sources above baseline
2. Transportation
Pipeline – Drag reducing agent, process chemical, and additive optimization; lockout pressure optimization; pumps/compressor fleet optimization; valve erosion detection and failure prediction
Rail, truck, and marine – Material and mass balancing to identify and minimize areas where losses occur
Methane leak detection
3. Storage
Tank level inventory monitoring and prediction for optimizing lifting schedules
Blend giveaway minimization for finished products
Truck haul scheduling of hydrocarbons after separation from natural gas
These midstream use cases can also be categorized by the type of analytics a company is trying to deploy, such as predictive analytics to forecast failures, process optimization to ensure quality, sustainability improvement initiatives, and machine learning applications.
By focusing on rapid time to value, Seeq enables cost savings in each of these use case areas, accelerating ROI for customers. Many Seeq applications have resulted in more than 10X ROI within just a few months of use. Some examples include:
Pipeline drag reducing agent optimization – $400k OPEX savings per year per pipeline
Troubleshooting pressure drop issues – $6M savings per year
Bearing failure prediction – > $500k in lost times savings
In a recent webinar, we walked through the technical details of these use cases and the savings realized, which are summarized below.
Pipeline Drag Reducing Agent Optimization
We discussed how to optimize the use of drag reducing agents (DRAs). DRAs are frequently used in pipeline operations to maintain the fluid properties of the material being transported, while reducing energy costs associated with pumping fluid. Its usage is critical to ensure on-spec material, but it comes at a high price point, with some companies spending over a million dollars on usage each quarter.
Historically, many risk-averse midstream oil and gas companies have not optimized their DRA usage. However, as the industry collects more data related to this process, knowledge with which to make better-informed decisions is growing.
Using Seeq, these organizations can monitor hydraulic performance across various segments and different pipelines, and based on performance for each segment, a team can determine where the DRA injection should be maximized or minimized. By optimizing DRA usage, midstream oil and gas companies can reduce operating costs while continuing to maintain desired quality and with the benefit of lower energy costs.
Lockout Pressure Optimization
In every industry, safety is paramount, and at the same time, businesses must operate continuously to drive revenue. These two priorities often clash, but with data-informed decisions, both can be achieved.
During the webinar, we discussed lockout pressure optimization. To prevent safety hazards like pipeline ruptures, a pressure trip limit is set in a control system. If the discharge pressure of a pump station drops below this limit, a lockout is triggered, causing a shutdown.
Oftentimes, this limit is entered during startup, and many years can pass without any updates because of the large volumes of information and manual data cleansing efforts required to calculate the ideal setpoint.
Seeq empowers engineers to overcome these challenges by efficiently and continuously calculating an ideal pressure trip limit, reducing downtime while also ensuring lockouts occur when needed.
By optimizing lockout pressure, this user reduced startup costs, increased production uptime, and eliminated unnecessary shutdowns, adding more than 100 additional hours of production per year. This resulted in mitigating approximately $1.5M in lost revenue per unnecessary shutdown.
Bearing Failure Prediction
More than ever before, data is enabling engineers and subject matter experts (SMEs) to be proactive rather than reactive when addressing issues. For example, instead of scrambling to resolve a compressor failure after it has happened, SMEs can use advanced analytics applications to generate predictions that suggest when a failure is likely to occur, and take action to minimize impacts.
In this use case, we discussed bearing failure, which occurs with little warning, making scheduled maintenance difficult. Unplanned bearing failures result in costly downtime, due to system interdependence.
Developing an analysis to predict these failures requires collaboration between multiple roles within an organization. Using Seeq, subject matter experts can cleanse data, identify normal operation, calculate statistical thresholds, and identify deviations. Data scientists can use this cleansed data and operational context to further the analysis, building a bearing health status signal by running an anomaly detection algorithm. Operators and managers can monitor the results in real-time to stay informed of potential issues.
After developing and implementing this model, maintenance staff receive notifications when abnormal operating conditions are identified, several days prior to failure, enabling the team to preemptively address issues and reduce failures. For a critical refrigeration compressor, preventing a single bearing failure resulted in lost time savings of more than half a million dollars.
Watch the Webinar Today
Interested in learning more about using Seeq for your midstream analytics use cases? View the full webinar to see the technology in action. And if you are ready to discuss how Seeq can improve your operations, please contact us to speak with one of our industry experts and schedule a demo today.