Coveme: Pushing for a greener solar industry with emphasis on material innovation – pv magazine International
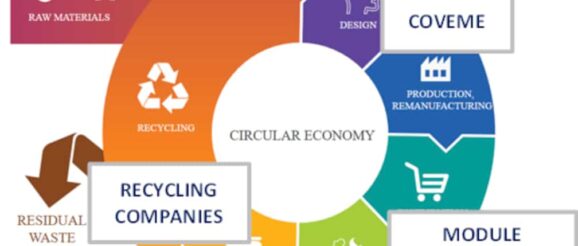
pv magazine: What does sustainability mean to Coveme?
Gian Paolo Fedrigo, CEO: We develop the concept of sustainability on two different levels: (1) Operational – On this level, sustainability means compliance with environmental and safety standards. Coveme’s production processes are subject to rigid and well-defined quality protocols and are compliant with ISO 9001:2015 quality management standards. Moreover, Coveme is certified under ISO 14001:2015 for environmental management, and ISO 45001:2018 for health and safety at work.
(2) Ethical – This entails respecting the environment that hosts us and our employees. It also means being visionaries in what the future can look like. In other words, thinking about business with a medium- to longer-term outlook. We are moving toward a future where there will be a growing need for high-quality recyclable materials, so during today’s design phase we need to take into account what the specific requirements of tomorrow’s materials will be. To achieve our final goal – implementing a “circular economy” process – we are investigating recycling models where both the backsheet and encapsulant are separated by a mechanical process through chemical recycling to become feedstock for new PET film production.
Stepping UP sustainability
In 2019, pv magazine launched the UP initiative, aimed at diving deep into what it means to be truly sustainable in the solar PV and energy storage industries. Via quarterly themes, we looked at raw material sourcing in batteries, green finance, circular manufacturing and PV module recycling in 2020. In Q1 2021, we will be turning our attention to agrivoltaics. Make sure you stay informed!
Does Coveme publish regular sustainability reports, which quantitatively measure impact, emissions, energy use, water and waste; and which compare annual progress? Please provide concrete examples of how progress has been achieved.
Coveme conducts monthly reports illustrating the company’s energy consumption and environmental impacts. These reports are published internally twice a year. We then carry out an annual environmental analysis and compare it with the reports of previous years. These are currently are not published outside of the company, but we are working on implementing a system that, starting from 2021, will release them to the public.
The Coveme website states, “Our materials are the result of a lean and green manufacturing process, embedded in a total quality system.” Please explain how manufacturing processes are green.
Our corporate mission is to minimize the environmental impact of production. We do this through mandatory restrictions that must be adhered to; in particular with the consolidated environmental text 152 from 2006 – a legislative decree that deals with environmental regulations, which for us implies authorizations, and limits on and monitoring of polluting emissions.
We also take inline measurements of our emissions’ composition. The pollutants are eliminated through state-of-the-art abatement systems. For example, being a chemical company involves working with acids. Our acids are knocked down inside counter-flow towers with a reactant, which allows the chemical neutralization of the acids and guarantees the release of purified fumes into the environment.
As for the methods and internal processes, we have adopted a whole series of behaviors which are stricter than normative standards. For example, in both our Gorizia plant and Bologna headquarters we have installed solar panels that allow us to produce renewable energy for self-consumption. In Bologna, we cover 100% of our energy needs this way. Meanwhile, we have installed a regenerative thermo oxidizer at our Chinese production site. This virtuous system captures the heat from exhaust gases, converts the solvents into carbon dioxide and water, and generates a thermal energy recovery.
As you mentioned, you manufacture in Italy and China. Do both locations adhere to the same sustainability standards?
We adopt best practices wherever we are. We always adopt a group logic, which means that if we see that best practices from an environmental point of view are Chinese, we will try to adopt these in Italy as well, in addition to the implemented Italian regulations. The same thing happens on the technology side: if we see that the best practices are coming from Italy, we ensure Coveme Zhangjiagang follows them, of course adapting to Chinese legislation.
When a backsheet has been integrated into a module, the recycling of said backsheet is then in the hands of the module manufacturer/end user. What measures does Coveme have in place to ensure its backsheets are properly recycled?
Yes, backsheet recycling is up to those who recycle PV modules. They must follow certain obligations. Coveme is working to support final clients both at the product and service level, in order to fulfill these obligations. At the same time, we are working with our suppliers to make polyester easily recyclable and to use already recycled polyester in our production process. In addition, we work with our partners to find new solutions and this bring us back to the “circular economy” concept. To be precise, we help our customers and suppliers develop a disposal system consistent with European, rather than U.S. or Asian regulations. We are part of various international working groups focused on understanding module disposal. In this way, we can offer our customers and suppliers all the references they need about this topic.
Popular content
How do you quantitatively ensure that external partners in your supply chain are operating sustainably?
Coveme has chosen multinational worldwide companies as suppliers, which must all be ISO14001 certified. Moreover, we often carry out on-site audits to verify that all rules are followed correctly by our suppliers, with a particular focus on their sustainable behavior.
In 2017, Coveme called on the Fraunhofer Institute to conduct a study evaluating different backsheets. The conclusion was that the “use of fluoropolymers or halogenated polymers in PV modules should be avoided, and alternative PET-based or biobased backsheets used instead. If halogenated backsheets are used they must be properly labeled to inform users and EOL managers. Labeling should comply with the Ecolabeling Standard.” With this in mind, why does Coveme continue to offer fluorinated backsheets? Are they labeled as described above? Has Coveme researched bio-based backsheets?
At a time when this topic was not well known, we were one of the first companies to start several studies on backsheet recycling in collaboration with the Fraunhofer Institute. The 2017 study consists of an analysis of the behavior of different types of backsheets in the various disposal processes (landfill, pyrolysis, incineration). The conclusion was that the use of fluoropolymers or halogenated polymers in photovoltaic modules should be avoided and alternative PET based or biobased backsheets should be used.
We have a wide range of products, which include fluorinated backsheets, that are Tedlar based, but also fluorine-free backsheets that are polyester based. Our company is a technical solutions’ provider so we must put customer care at the center and we always try to offer to our customers the greenest solutions. Furthermore, considering the difficulty of some customers in switching from backsheets based on Fluorurate TPE production to those based on PET PPE, we are also offering recycling solutions to module manufacturers with fluorine based backsheets.
One of the advantages of polyester is that it already has a lower carbon footprint than alternative materials, with clean and efficient manufacturing. An additional advantage is the potential to further reduce the carbon footprint by incorporating recycled content. This helps, because for every kilogram of virgin material you replace, you reduce the related carbon emissions by approximately 1.5 kilos. Increasing those levels comes with better messaging to the wider industry about a further carbon reduction, but this needs to be done step-by-step.
Is Coveme part of any schemes, like the Carbon Disclosure Project or Declare Label? If not, is this something the company will undertake? And/or has the company taken part in any processes, workshops or programs like Ecolabeling, the circular economy or green manufacturing? Please elaborate.
Coveme is pushing for a greener industry, with a particular emphasis on material innovation in recycled and recyclable products. We are working on several fronts, including on an institutional level, a supplier level and an industry partner level. This includes:
Finally, why did Coveme decide it was important to support pv magazine’s new UP sustainability initiative?
First of all, we thank pv magazine for this first year of partnership, which we intend to continue in the future. The activities we have done in this first year have confirmed the importance of exchange of best practices with other players, and to ensure that ecological and sustainable products are at the same time the most highly performing products.
From our first product on there always been a technical and qualitative improvement of the material. This development is still ongoing, so much so that the latest films developed with DTF have performances that can be equated to Tedlar – perhaps better – and that can even occasionally replace the glass layer of the solar panel. We hope to have made a first contribution as a polyester film converter with a know-how of more than 50 years and as a supplier of the PV industry for over 20 years.
This content is protected by copyright and may not be reused. If you want to cooperate with us and would like to reuse some of our content, please contact: [email protected].