COVID-19 sparked a burst of industrial innovation in Capital Region
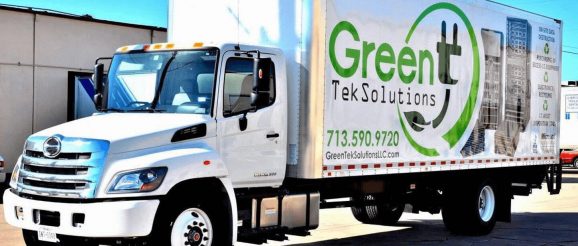
COVID-19 remains with us, even though many critical shortages have eased. But those desperate months in 2020 have had a lasting impact on society, including the business sector, where unexpected players found themselves thrust into the forefront of an effort to combat the pandemic.
In the Capital Region, distillers switched to making alcohol-based hand sanitizers and at least one manufacturing firm, Precision Valve & Automation, retooled and started building ventilators. Researchers at Rensselaer Polytechnic Institute set to work building a special ultraviolet box that could disinfect items like masks, while others at the school developed smartphone apps designed to help people avoid dense crowds.
The efforts evoked the wartime industrialization that occurred during World War II as government and industry worked in concert toward a shared goal. And like the war, which led to innovations in optics, radar, aeronautics, medicine and other fields, the fight against COVID will likely spawn new industries.
Today, as pandemic medical supply shortages have eased, many of the initial players in the Capital Region are getting back to normal, but their rapid innovations will nonetheless have a lasting effect.
Jumping hurdles
“I still have people buying it,” Matthew Jager, of Albany’s Yankee Distillers said of the gallons of hand sanitizer he started making last year. While he’s back to focusing on top-shelf whisky, Jager still has several hundred gallons of sanitizer at the distillery.
The initial conversion was simple. Jager knew he could mix denatured ethanol and glycerin in batches to produce an effective disinfectant. What was confusing was the welter of Food and Drug Administration regulations and rules about how to do it.
In addition to navigating the bureaucracy, Jager also faced supply shortages, including a lack of containers for the new product. He ended up using what was available, which were plastic milk jugs, equipped with warning signs that this was disinfectant, not a dairy product.
He gave away and sold it, and after a while, people were coming by the distillery for refills. Like his whiskey, Jager decided to go high end, running his ingredients through a carbon filter to ensure it was extra pure.
“I turned all these people into hand sanitizer snobs,” Jager said with a chuckle. “It was kind of a neat thing.”
Ventilator production
Twenty minutes north in Clifton Park, staffers at Precision Valve & Automation knew early on they could help with what was at the time a dire shortage of ventilators.
The company makes valves, automated devices such as those that spray coat materials. Some of their products already were used in ventilators. Once then-Gov. Andrew M. Cuomo put out a call for more ventilators, they were able to put together machines that use a bag mask that pushes air in and out of a patient’s lungs.
They were simple devices as ventilators went but they did the job and could be built for less than $8,000, which was a bargain by modern ventilator standards.
“The FDA authorization was the biggest hurdle,” said Frank Hart, PVA’s managing director of sales and marketing. The actual building of the devices wasn’t that difficult and it was about six weeks from the initial plan to production.
As it turned out, doctors were easing off on their use of ventilators and they built about 100 units, many of which were exported to Africa and Asia.
They halted production and went back to their mainstream business but the exercise also opened up some business opportunities. The federal approval process brought PVA an ISO 9001, or International Organization for Standardization, certification.
That’s roughly akin to a Good Housekeeping seal of approval for industrial devices like valves. As a result, they are finding it easier to export their valves to Mexico and China, which is where about 60 percent of those sales go.
The company is on track to surpass their 2019 sales and the 200-person organization is looking for new employees, although Hart notes that every business he knows is hiring these days.
Ultraviolet, polymers, apps
The pandemic has created an explosion in researching new approaches to personal protective equipment and nowhere is that truer than at Rensselaer Polytechnic Institute.
As the mask shortage was at its peak, researchers at RPI’s Center for Lighting Enabled Systems & Applications constructed a light box that bombards masks with ultraviolet “C” waves that kill the COVID virus. The closet-sized machine took about two weeks to build and was sent to New York City’s Mount Sinai Hospital, which has been working with the school on a number of Covid-protection developments.
The hospital tested the machine in its biohazard lab and found it to be effective with 120 seconds of UV exposure on all sides of the mask.
“The success was that we could kill the virus and figure out the dose,” said Deepak Vashishth, director of the Center for Biotechnology and Interdisciplinary Studies and a professor of biomedical engineering.
As with PVA, the immediate need for such machines was reduced after the mask shortage eased. But building the machine was a proof of concept, showing that this was a viable approach to sterilization although it didn’t go into actual use.
Vashishth believes such devices could be useful in places where there may be a shortage of sterile masks and other equipment. Much of that, he said, depends on future calculations about whether they can be made at an affordable price. They have heard from one firm in India that expressed an interest in building the devices on a commercial scale but it remains unclear precisely what those plans are.
Also in the development stages at RPI is a special antiviral coating that could be sprayed on masks or other medical devices that COVID virus might land on. Aided by a grant from the National Science Foundation in April 2020 at the height of the mask shortage, RPI researchers Helen Zha and Ed Palermo experimented on thin polymer coatings as an antiviral agent.
Zha, an assistant professor of chemical engineering, said that’s in contrast to other researchers who are looking at substances like copper or silver as antiviral agents.
“There are a lot of companies in this space now,” said Zha.
There are no immediate plans for a startup company or other commercialization efforts. And Zha said their main goal is to get the technology proven and out in the public arena so people can use it in manufacturing if they so choose.
“This definitely is a pandemic-motivated innovation,” she said.
Also motivated by the pandemic was the “Study Safe” smartphone app that Kristin Bennett’s students developed at RPI.
Working with the United Health Foundation, Bennett, a math and computer science professor, worked with her students to develop the app, which locates the least crowded spots on the RPI campus, which are presumably the safest for studying during a pandemic.
The app tallies anonymized Wi-Fi signals by location to map the changing crowd numbers and compares it with past data about crowds in those areas. The numbers also are updated about every half hour.
“We made it happen using all undergraduate researchers,” said Bennett.