CPG’s New Normal: Three Focus Areas for Smart Connected Operations – Viewpoints on Innovation
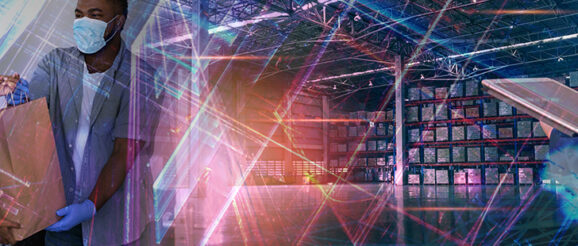
Kalypso is a people business. We don’t have our own manufacturing plants or production lines, but we do have industry expertise and deep experience with clients that do. To meet this moment, we’re working hard to capture what we know and share it. We hope you find this article useful as you think about what you can do to reduce your risks today and prepare for the future.
As the world has responded to the global pandemic in the first half of 2020, many factories across the world shut down abruptly and supply chains were suddenly disrupted. Consumer packaged goods manufacturers and brands now face a new normal as the world slowly starts to re-open. All companies must develop strategies and new ways of working designed to help them be more resilient in the future.
One key strategy and approach to address both near-term response and long-term resiliency is smart connected operations (SCO), which can minimize the risk of disruptions.
Consumer Expectations in an Uncertain World
The global crisis has fueled significant changes in consumers’ relationship to food safety and has triggered them to re-evaluate some loyalties that were previously unchallenged. This directly impacts the way consumer good supply chains are organized in several ways:
Three Focus Areas for Smart Connected Operations in CPG
Smart connected operations is the ability to connect process and data across the enterprise using digital technologies to uncover new insights, improve decision making, and reduce time and cost. These technologies connect the enterprise across all functions including product development, manufacturing, operations, supply chain, and sales and marketing.
Here are some of the top methods CPG companies can leverage SCO to address shifts in consumer behavior while also minimizing the risk of disruptions to operations.
Focus Area 1:
Improve Manufacturing Throughput and Reduce People on the Shop Floor
All consumer companies have a responsibility to minimize the risk of transmission within their facilities, and potentially to customers. Transmission risk is reduced through traditional methods such as increased screening, increased separation of employees and enhanced cleaning procedures. When companies apply digital technologies to their manufacturing facilities, they can simultaneously improve employee health and safety while also improving manufacturing throughput and reducing costs.
Use IoT and Electronic Tagging for Real-Time Remote Insights
While it is relatively easy for office workers to work remotely, factory floor workers need to be physically present on-site to operate machines, read machine status or track inventory. IoT and tracking technology plays a crucial role in reducing the need for on-site presence. By connecting machines, technicians and management can remotely monitor manufacturing operations.
This can be further enhanced by electronically tagging parts, products, and packaging so there is always a live view of both quantities on hand and location. This reduces the need for manual inventory counts and is a key enabler of automated transportation.
Automate Material Movement and Handling
Automating the movement and handling of in-factory materials and equipment has several advantages:
There are multiple ways to enable automated in-factory transportation that serve different needs. Autonomous indoor vehicles (AIVs) can move materials and goods between warehouses and production lines. Within the production process, these can be combined with flexible conveying, filling, and packing technologies to reduce the need for people to touch or move items from one station to the other. Automation technologies combined with advanced analytics can reduce risk, reduce overhead allocation costs, and improve Overall Equipment Effectiveness (OEE) and operating margins.
Provide Training Remotely through Virtual Reality
Instead of training new associates on the job, companies use virtual reality (VR) to train new workers (or existing workers on new skills) remotely. Remote training uses a digital twin of the factory line to create a life-like VR experience, allowing factory floor workers and operators to train on an exact virtual replica of the production line. This minimizes or even eliminates the need to interrupt production for pilots, trials, or training.
Facilitate Remote Monitoring and Maintenance
While the solutions above will help reduce the need for a company’s own people to be physically present on the factory floor, there is still a risk when bringing in third-party partners for maintenance and machine repair.
Leveraging digital technologies like SCO, IoT and analytics, companies can actively monitor all assets and identify machine failures before they happen. This allows preventive maintenance to be scheduled during hours where there are a minimal number of other people in the facility. Secondly, by using augmented reality (AR) technologies, companies can collaborate with remote technicians to troubleshoot using visual interactions instead of inviting them to troubleshoot problems on-site.
As an additional benefit, this will significantly enhance the mean time to repair (MTTR) and the first-time right ratio (FTR).
Optimize Virtual Line Change Commissioning and New Production Equipment Deployment
Reduce the amount of manual effort involved in commissioning line changes with simulation/emulation tools for virtual commissioning. These tools also reduce the required time to get to optimal operating efficiency by:
Implement Personal Physical Distancing Technology
Even with all the above use cases implemented, there will likely be a need for some people to be physically present in the plant. Digital technologies can be used to help people maintain their social distance on the factory floor.
Wearables are a lightweight option to provide a warning signal if proximity to another person is within six feet. This can also enable automatic contact tracing to quickly understand which people have been in the same physical spaces over a specific period of time.
Focus Area 2:
Reduce Paperwork and Administrative Tasks for More Focus on Quality and Operating Performance
Typically, there are a lot of administrative and manual tasks associated with the manufacturing process, from registering hours to monitoring machine throughput. These processes are often manual, requiring employees to write numbers down on forms or enter data into a computer.
Companies should minimize these non-value-added activities by automating them. This can be either through a modern MES system or through Robotic Process Automation (RPA). The goal is to remove manual activities and transform data into electronic batch records so plant workers can focus more on value-added activities, like quality and operating performance.
Using AR devices, companies can provide workers with readily available data, insights, and instructions without requiring them to use physical manuals or handheld devices. By combining this with voice-commanded software, the need to enter data by hand is further eliminated. This creates a paperless and touchless process.
Finally, companies can use algorithms to create an optimal allocation of people within their facilities. By tracking workers’ skills and completed training certificates, an optimal mix can be found that assigns the right people to the right station in the factory while minimizing the need for rotations or individualized coaching. This reduces the risk of disruptions when employees are suddenly sick or need to self-isolate at home. Planning algorithms can help adjust worker allocations quickly to respond to such unforeseen changes.
Focus Area 3:
Enhance Operations with Data Science and Artificial Intelligence
The operational measures CPG companies can take to improve their resilience are not limited to the factory floor. There are opportunities to improve operations both upstream as downstream in the supply chain by capturing data and using advanced analytics to create real-time insights. Data-driven insights enable instant decision making in case of supply disruptions, demand changes and/or product issues.
Increase visibility into Raw Material Availability of Upstream Suppliers
In an ongoing crisis, there is a chance that additional plant closures or other disruptions will suddenly limit access to specific raw materials or parts. CPG manufacturers should seek to build data sharing mechanisms with suppliers. This creates real-time insight into production and inventory levels, enabling them to react more quickly to disruptions and efficiently shift material sourcing.
Incorporate Automated Analytics of Real-Time Sales Data
Typically, there is a significant delay between when a consumer buys a product at a retail store or online and when sales data is shared with product manufacturers or suppliers. With electronic tagging, manufacturers can gain live insight into real-time sales data. Using advanced analytics, they can rapidly adjust production levels based on accurate demand data.
Provide Consumers with End-to-End Product Traceability
As the industry adjusts to a new normal, we can expect an increased push from consumers who want visibility into where products originated, as well as where and how they were transported. Deploying RFID on products or packs can create product traceability. This can be supplemented by blockchain solutions to create a repository to store and access this information, making it visible to all supply chain partners and end-consumers.
Create a Smart Connected Production and Distribution Network
Instead of specializing each production location or line to a specific product, manufacturers should create flexibility across manufacturing locations, allowing them to readily change production output in one location when another has limited capacity or is temporarily shut down.
Connecting multiple production facilities or production lines through IoT and creating a digital twin of the entire production network gives management a live view of all factories and production lines so they can quickly make production allocation decisions. In addition, VR can be used to rapidly train people to work on other lines or locations and further increase flexibility.
Finally, with manufacturing becoming more and more automated, the case to manufacture offshore is slowly starting to diminish. Combined with the risk of disruptions to supply networks in case of a crisis, companies will look for options to shorten supply lines and bringing manufacturing closer to the end-consumer.
Now is the Time to Get Started
All the technologies described in this article are already available and driving value for companies at the forefront of digital innovation. As CPG companies continue to navigate a global crisis while keeping the safety of both consumers and factory workers top of mind, now is the time to start investing in these technologies and enhance the ability to thrive in the new normal.