Decarbonization is at the forefront of environmental innovation
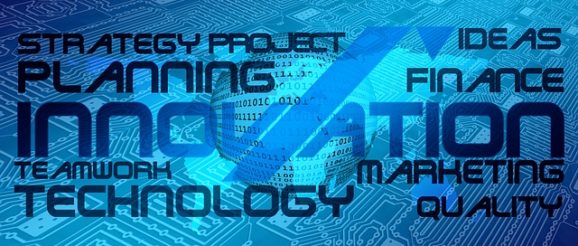
Decarbonization is at the forefront of environmental innovation
Earth’s carbon dioxide levels have increased appreciably within the last several decades, which directly correlates to rising environmental concerns of GHG emissions, pollution and disruptions of marine and terrestrial environments, among others.
Earth’s carbon dioxide (CO₂) levels have increased appreciably within the last several decades, which directly correlates to rising environmental concerns of greenhouse gas (GHG) emissions, pollution and disruptions of marine and terrestrial environments, among others.1 A 2022 study showed that CO₂ levels are 50% higher vs. the pre-industrial era—a significant environmental impact that will continue to affect humankind.2 The increase in CO₂ levels in the Earth’s atmosphere (i.e., GHG) is associated with trapping the sun’s radiation and warming the planet’s surface. The traditional carbon capture methods with petroleum-based feedstocks, which capture CO2 from the combustion of hydrocarbon fuels (i.e., flue gases), are unable to keep up with the continued rise in CO2 emmissions.
With the increased environmental pressure to reduce CO₂ output and minimize GHG emissions, new players within the industry are looking to introduce innovative decarbonization technologies that will disrupt the traditional paradigm.
Decarbonization typically involves replacing traditional fossil fuel-based power with low-carbon power from renewable energy sources (such as wind, solar and biomass), thus reducing CO2 output. In addition to the immediate benefits of replacing fossil fuel-based power generation, including the reduction of air pollution and the adverse effects on climate change, the introduction of renewable energy sources provides the opportunity to perform overall process optimization of complete systems to leverage process electrification and reduce net energy input.
To stand at the forefront of their industry, companies like Origin Materials, PureCycle Technologies and ION Clean Energy have taken different paths toward utilizing novel decarbonization processes. Whether replacing processes requiring petroleum-based feedstocks with carbon-negative processes, recycling of petroleum-based manufactured products, or capturing emitted CO₂ and reusing feedstock for other industries, each company is poised to capture significant market share while contributing to a reduction in GHG emissions.
This article reviews these three process pathways and how each is used for successful decarbonization.
Decarbonization by substituting non-petroleum-based feedstocks
Origin Materials has developed an innovative technology that replaces hydrocarbon feedstocks with 100% renewable plant-based feedstock to manufacture polyethylene terephthalate (PET), the material of choice for most consumer-based plastic bottles. Using its proprietary technology based on the same principle of photosynthesis, the company has eliminated the need for fossil-fuel resources while capturing carbon in the process.
Photosynthesis is nature’s original carbon capture technology, capturing atmospheric CO₂ and storing it as cellulose. Rather than extracting carbon from petroleum, Origin Materials’ technology extracts the carbon needed for its manufacturing process from plant cellulose. While the preferred feedstock is sustainably harvested wood, the advantage of this technology is that any cellulose can be used, including other types of wood, and even cardboard box waste.
The company’s carbon-negative process converts C6 cellulose into four essential building-block chemicals for manufacturing: furan (CMF) chloromethyl furfural, (HTC) hydrothermal carbon, levulinic acid and furfural. Given the need to locate its decarbonization plant close to its biomass feedstock distribution network and the desire to bring this technology to market promptly, Origin Materials opted for a modularly constructed process system and delivery model. First, an initial demonstration-scale unit was created and tested. This was followed by scaling up to a commercial-size unit consisting of 15 process modules, two stair modules and a large standalone vessel (FIG. 1).
Decarbonization by recycling petroleum-based products
PureCycle Technologies has developed a novel process that has eliminated the need to utilize new petroleum-based feedstocks to manufacture food-grade polypropylene (PP), while also addressing the growing need to recycle plastic waste.
Rather than introducing new petroleum-based PP into the market, PureCycle’s technology recycles post-consumer PP back into ultra-pure recycled PP, thus closing the loop in the reuse of plastic.
The company began process development by constructing its Phase 1 feedstock evaluation unit. Having successfully proven its technology, PureCycle is building its first-of-a-kind modular commercial-scale plant consisting of 20 process units (FIG. 2). This facility is expected to produce more than 105 MMlb/yr of ultra-pure recycled resin. Ultimately, this recycled feedstock will be used in consumer goods packaging, home furnishings and other applications which today have limited options for recycled PP. Plans are also underway to construct additional facilities based on this initial design.
Decarbonization by CO2 capture
With funding from the U.S. Department of Energy’s National Energy Technology Laboratory, ION Clean Energy is commercializing a new low-cost CO₂ capture technology, with ambitious plans to capture 1 Bt of CO₂ by 2050. ION has completed pre-front-end engineering design for its 300-MW modular CO₂ capture system project, which has been retrofitted onto an existing coal-fired power station (FIG. 3).3
Projected to capture 1.9 MMtpy of CO₂ at an estimated cost of $32.50/t, this project will be one of the lowest-cost CO₂ capture solvent technologies in the marketplace. The company’s long-term goals include applying its innovative technology to other industries and utilizing the captured CO₂ as feedstock for other higher-value-add chemical and biological processes.
Delivering decarbonization projects to the market
The three pathways to decarbonization mentioned in this article reduce future reliance on petroleum-based feedstocks, either by eliminating them as source feedstocks or by reducing global consumption by substituting recycled petroleum-based materials as feedstocks. Although each pathway is unique, they all share the need for the design and execution of the new plants to be both scalable and repeatable.
Scalability is essential to address in the beginning, as the demand for non-petroleum-based feedstocks will only increase due to the growing focus on environmental impacts. If a first commercial plant can be constructed, at a minimum investment, to replace a CO₂-generating process and then successfully generate revenue, this demonstrates the technology to de-risk future expansion. As feedstock availability and product demand increase, additions can be made to the base case design to increase output.
Repeatability is also essential because many novel decarbonization technologies require rapid deployments across various geographies near feedstock point sources.
Delivering a modular decarbonization project vs. field-erecting a plant enables companies to build both scalability and repeatability into their plant designs. Fabricating a project offsite in modules and then assembling completed modules onsite provides project cost certainty and a faster time to market vs. conventional field construction. Cost savings can be in the range of 30% and even higher for more remote plant sites. Project schedules can be shortened by 6 mos or more when modules are used. Therefore, a modular construction solution is the most cost-effective and timely way to address scalability and repeatability for decarbonization projects.
The future of decarbonization
As demand for products traditionally derived from petroleum-based feedstocks continues to increase, the industry will seek new decarbonization technologies to reduce CO₂ output and minimize GHG emissions.
The world is witnessing only the early stages of new emerging technologies that will eventually decarbonize the oil, gas and energy industries. Companies like the ones mentioned in this article are pioneering this transition to a greener, carbon-neutral industry. HP
LITERATURE CITED
The Authors
Tom Schafer is Vice President of Koch Modular Process Systems. He has more than 45 yr of experience in process design, operations management, cost estimating, plant layout, and sales and marketing, as well as equipment design, including distillation, heat transfer, fluid flow and process control. Schafer earned a BS degree in chemical engineering and an MS degree in chemical engineering from Manhattan College in New York City, New York.
Tom Schafer is Vice President of Koch Modular Process Systems. He has more than 45 yr of experience in process design, operations management, cost estimating, plant layout, and sales and marketing, as well as equipment design, including distillation, heat transfer, fluid flow and process control. Schafer earned a BS degree in chemical engineering and an MS degree in chemical engineering from Manhattan College in New York City, New York.
Mauricio Villegas is the Manager of Business Development at Koch Modular Process Systems. He has more than 25 yr of experience in the engineering and construction industry, delivering projects across industries ranging from small brownfield projects to greenfield mega-projects. Prior to joining Koch Modular Process Systems, he held various management roles at WorleyParsons, Technip, IHI E&C and Arcadis. Mr. Villegas earned a BS degree in business administration and management from Northeastern University in Boston, Massachusetts.
Mauricio Villegas is the Manager of Business Development at Koch Modular Process Systems. He has more than 25 yr of experience in the engineering and construction industry, delivering projects across industries ranging from small brownfield projects to greenfield mega-projects. Prior to joining Koch Modular Process Systems, he held various management roles at WorleyParsons, Technip, IHI E&C and Arcadis. Mr. Villegas earned a BS degree in business administration and management from Northeastern University in Boston, Massachusetts.