Enabling a circular economy approach to advanced composites innovation, manufacturing and use, Part 1: CompositesWorld
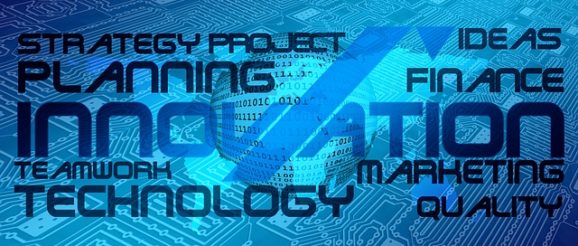
Uday Vaidya, Chief Technology Officer at IACMI
In its five years since launch, the Institute for Advanced Composites Manufacturing Innovation (IACMI – The Composites Institute; Knoxville, Tenn., U.S.) has continued to drive the large-scale adoption of advanced composites in diverse markets by investigating topics not only of interest to industry but also in the interest of national security and economic prosperity. Through these developments, IACMI has incorporated aspects of circular economy emphasis into many of the technical research projects.
Featured Content
Through a circular economy emphasis, technical research projects adopt a holistic approach: design and lifecycle perspectives are considered when developing new materials, equipment and manufacturing processes. Recycling is a key element for circular economy, but the most important mindset is to design materials and processes with the ultimate goal of reuse, and to support methodologies where multiple materials can be utilized through one process. Through these innovations and variations, industries are better equipped to adopt a more sustainable manufacturing practice.
This months’ column focuses on one of two key aspects that increase lifecycle advantages in composite applications: reducing the embodied energy of fiber-reinforced polymer composites (FRPCs). Through technical projects and guiding priorities, the Institute is helping to address key challenges in circular economy adoption through technology development.
The polymer composites industry is a major economic contributor to a range of U.S. market segments. IACMI has a unique opportunity to make significant progress toward reducing the impact of landfill contributors in various markets deploying its nationwide network of composites expertise. The projections of key markets include:
Reducing Embodied Energy
In its first five years, IACMI has focused on the adoption of advanced composites to enable energy savings and greenhouse gas emission reductions through targeted applications in vehicles, wind turbines and compressed gas storage. The focus has been with the understanding that lighter-weight vehicles reduce fuel consumption, wind turbines operate more efficiently at a lower installed cost while displacing non-renewable energy sources, and compressed gas tanks permit the economic use of lower environmental impact fuels including natural gas and ultimately hydrogen.
Yet, the energy-intensive nature of advanced glass and carbon fiber composites production offsets some of the lifecycle energy advantages. These offsets include composites fabrication — for example, in wind turbine blade production — which uses glass fibers extensively and can be highly labor-intensive; as well as the reality that composites manufacturing technologies can deliver significant weight savings or higher volume for vehicles, but not both.
For potential carbon fiber-intensive applications, the cost and embodied energy of carbon fiber-reinforced polymer composites resides primarily in the production of the carbon fibers3,4. Therefore, the best way to reduce the embodied energy is to create materials and manufacturing processes that reduce the cost of production. The energy intensity of carbon fiber can be reduced through alternative precursors and advanced conversion processing technologies, while automated layup methods, fast curing resin systems and robust inspection techniques can help improve manufacturing costs by reducing production cycle times.
IACMI and its partners are pursuing various technical activities, aligned with priorities identified in the technology roadmap (see “IACMI: Driving innovations in the composites industry”), to overcome these challenges in advanced composites markets. Some of these priorities are discussed below.
Demonstrate lightweight automotive composite components.
Volkswagen, Oak Ridge National Laboratory (ORNL), Michigan State University (MSU), Purdue University, and the University of Tennessee, Knoxville (UTK) along with industry partners have developed a glass fiber sheet molding compound (SMC) composite manufacturing process for exterior automotive body panels. With targets including a condensed cycle time of 5 minutes and a 25% reduction in cost, energy and weight, this process is suitable for high production volumes and offers a promising lightweighting solution to substitute incumbent metals such as steel.
Develop novel oxidation, carbonization, and heat-treating CF production technologies.
Oxidation is the most expensive, energy-intensive and time-consuming step of carbon fiber production. 4X Technologies, 4M Carbon Fiber, ORNL and UTK are developing the world’s first plasma oxidation oven for the oxidation phase of textile-grade carbon fibers. The project is anticipating less than half the processing time compared with conventional thermal oxidation methods, with significantly higher throughput and increased energy efficiency.
By initiating projects that develop new materials and processes that adopt a circular economy perspective, IACMI is enabling its members to develop manufacturing standards and best practices that support industry’s bottom line and also benefit the U.S. national security and economic prosperity.
Next month’s column will address another major component to increasing lifecycle advantages in composite application: improving composites’ recyclability through both material and process developments.
Join Us
IACMI has created an ecosystem of innovation that meets commercial needs, serves national security and drives national economic growth through its network of more than 150 members including academic institutions, and federal, state and local governments — supported by the U.S. Department of Energy’s Advanced Manufacturing Office. Its efforts are driven by the major industry participation of its membership and made possible by the network of world-renowned talent that participates in the community. Dr. Soydan Ozcan, Scientist at the U.S. Department of Energy’s Manufacturing Demonstration Facility (MDF) at Oak Ridge National Laboratory and Recycling Lead for IACMI, has led several of the recycling initiatives for the institute and industry collaboration. IACMI’s industry-led projects improve the flexibility of composites manufacturing processes, which in turn increases material diversity and allows optimization with improved energy efficiency, recyclability, material resource efficiency and lifecycle characteristics, including EOL disassembly and reuse.
Organizations of any size can join IACMI and, once a part of the consortium, can benefit from participating in projects such as those described above, networking with other members, and engaging in workforce development opportunities to meet organizational needs. Learn more at iacmi.org.
2Psomopoulos, Constantinos S.; Kalkanis, Konstantinos; Kaminaris, Stavros; Ioannidis, George C.; Pachos, Pavlos. 2019. “A Review of the Potential for the Recovery of Wind Turbine Blade Waste Materials.” Recycling 4, no. 1:7.
3Das, S. (2011). “Life Cycle Assessment of Carbon-Fiber Reinforced Polymer Composites,” The International Journal of Life Cycle Assessment, Vol. 16, No. 3, pp. 268-282.
4Based on an IACMI analysis of energy intensity metrics for wind, vehicle, and compressed gas storage applications, carbon fiber represents 88-95% of CFRP embodied energy compared with other constituents include intermediates, resins, and molding & curing processes. Source: Brosius, Dale; Das, Sujit, “IACMI Baseline Cost and Energy Metrics,” March 2017, Institute for Advanced Composites Manufacturing Innovation (IACMI).
About the author
Uday Vaidya serves as Director of the University of Tennessee’s Fibers and Composites Manufacturing Facility (FCMF), IACMI’s Chief Technology Officer, and is the University of Tennessee-Oak Ridge National Laboratory Governor’s Chair in Advanced Composites Manufacturing. Vaidya is an expert on the manufacturing and product development with fiber reinforced polymer composites. Vaidya serves as the Editor-in-Chief for Elsevier’s Composites B: Engineering journal. He engages a broad range of undergraduate and graduate students in experiential learning with composites technologies.