From Sticky Notes to Digital Transformation | Human-Centered Change and Innovation
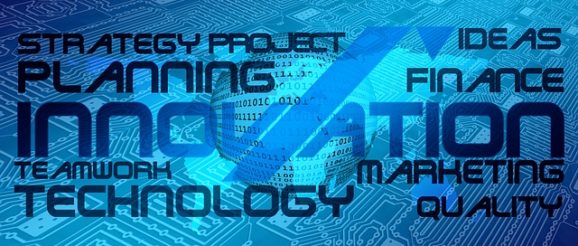
GUEST POST from Dainora Jociute
Whether it’s a bunch of sticky notes on an office wall or a clever digital tool with color-coded boxes, most of us are familiar with the ingenious concept of a Kanban board.
Perhaps that’s not the name you use. Maybe for you and your team, it’s Trello or simply a whiteboard, yet at the very core of it all, hides a little neat Japanese invention that sparks joy – Kanban.
It is not exactly a new concept, however over the years Kanban remains largely unchanged and its popularity unwavering. In this article, I will try to take a deeper look at what it is and how to make it work for you.
A Short History of Kanban
The word Kanban translated from Japanese means sign or signboard. Back in the day, and I am talking way back – 17th century – that was exactly what Kanban was. It was a signboard signaling to passersby what services or products a business offered.
In a more recent chapter of history, in the wake of the Second World War, the Japanese automotive manufacturer Toyota was in a pickle. The company struggled to make any profit, and they realized that something must be done. This is where Taiichi Ohno, the so-called founding father of Kanban comes into the picture.
A budding industrial engineer, Ohno was sent to the US to scout and gather inspiration for improving manufacturing back at the Toyota plant. The revelation hit Ohno in the most inconspicuous place – a grocery store. He noticed that some supermarkets stocked their shelves based only on customer demand. Customers would pull products they need off a shelf, and the store would restock them only once it was gone, avoiding unnecessary overloading of the shelves with excess products in advance. This system ensured that the store only sold products with real demand.
This pull approach (on that a little later) clearly reduced waste: it saved the time wasted on restocking, resources spent on overproduction, produce thrown out, and much more. Aiming to eliminate waste without sacrificing production back at the Toyota plant, Ohno introduced the pull system in the shape of paper cards that he later named Kanban.
Each Kanban card contained a clear description of each step in the production line, be it the number of materials needed or a particular task of the production chain to be done. It controlled amounts of production ensuring that only what is needed will be created. These cards moved systematically along the whole manufacturing process and guided what must be done throughout the journey. It became a simple yet ingenious tool for managing the whole manufacturing process ensuring that no waste will be created along the way.
Later down the line, other brilliant minds realized that the same approach can be applied to other industries too, not just manufacturing.
One of the key figures responsible for this adaptation was David J. Anderson. He is known for adapting Kanban principles from their origins in manufacturing to knowledge work, particularly software development and project management.
Although there were other prominent advocates of Kanban in software development, Anderson’s 2010 book on Kanban gained significant popularity, leading him to gain widespread recognition as one of the main proponents of the Kanban we all know today.
What is Kanban?
With all that said, it is time to go into more detail about what Kanban actually is.
In the simplest words, Kanban is a visual tool, a signboard for mapping and tracking planned work, work in progress, and work done.
Kanban is a visual tool for mapping and tracking planned work, work in progress, and work done.
While Toyota mainly used the original Kanban system to track inventory in their manufacturing processes, today’s Kanban can be applied to a much broader range of work areas.
Today, Kanban is widely used in knowledge work to visualize and map the value stream. It helps teams and individuals self-organize and minimizes the need for constant supervision.
However, it takes a bit of time to reach that harmonious sync with your team and squeeze the full value from the board. There are key things in the process that should be known before kicking one off, so let’s break the Kanban down.
Kanban, the Pull System
Now, you read it in this article and most likely you heard it before: Kanban is based on the pull process. But what does that entail?
In Kanban, the concept of “pull” means that tasks or projects are pulled into the process based on the team’s skills, readiness, and capabilities. Similarly, to the pull that Ohno observed in American grocery stores, in Kanban, you take action when there is a need and capability. This approach ensures that tasks are not imposed on individuals who might not have the time but are instead taken up by those who are more likely to complete them.
This enhances efficiency and effectiveness, prevents bottlenecks, increases the completion rate, and prevents waste. In the end, by pulling tasks based on readiness, the team can maintain a sustainable workflow and deliver outcomes within the expected timeframe.
Elements of the Kanban Board
When it comes to Kanban, the true beauty hides in its simplicity, and here, less is truly more. All you need is just a few elements to have a working Kanban board:
Kanban Board
In addition, it is worth knowing the following definitions:
Cycle time measures the actual time spent working on a task.
Lead time measures the whole time spent on a task, both active work time and inactive waiting time.
These elements, paired with a clear process policy are all you need for the Kanban process to work.
How to Make Your Kanban Work
So, while the elements of Kanban are simple and straightforward, the success of the Kanban process and results heavily depend on the implementation of policies and effective communication practices.
There are a few of those that should be set in place before you start your Kanban initiative:
Benefits of Using the Kanban Method
Kanban is flexible, easy to use, and quick to master and there are plenty of benefits of using the method. To name a few:
From Sticky Notes to a Digital System
Some years back, I worked in a company where we used a real, physical Kanban board. And I don’t mean a whiteboard, I mean a full wall, covered from top to bottom in sticky notes (big organization, big team, and a huge process). And part of me loved it.
We all worked like busy bees, with our individual tasks, tied to a common goal. Kanban was the place where everything fell into place.
Every morning we would hover over that wall, with a cup of coffee in our hands, checking where those stickies are traveling. It was a whole story unfolding in front of our eyes.
However, everyone agreed that tracking each sticky note took a big bite of our mornings.
Was the task I worked on approved by legal and moved to the next stage, or was it sent back to be reworked?
That’s why I see the digitalization of Kanban as a blessing. It makes things easier to track and increases readability, which reduces waste.
Also, think about the analytics and reporting. Our manager used to take pictures of the wall and show them during the Monday team meetings. Zooming and deciphering individual handwriting… yeah, not the best. Luckily, digital tools save us from this burden.
Pros and Cons of Digital Kanban Board
There are some obvious benefits of a digital Kanban board:
However, as with most tools, there is no one right way. Digital Kanban tools has some disadvantages too:
With that said, if you will look deeper into the pros and cons of digital vs physical, you might find a lot of contradicting information. Some articles might argue that digital tools can be time-consuming, requiring people to navigate additional applications, while others claim that physically going to a board might take extra time.
Similarly, some articles highlight concerns about communication issues and working in silos, whereas others praise digital tools for facilitating communication, especially among remote teams. The contrasting viewpoints can lead to different interpretations and opinions on the impact of digital tools in the workplace.
So, physical, or digital? As predictable as my answer will sound – it all depends on your unique way of working.
Going Digital
There are a lot of tools that could be used as a digital Kanban board. From the good old Excel to a dedicated digital Kanban tool such as Kanbanize, you have plenty to choose from. However, such tools are not necessarily equal to one another. If you were to take the digital route, here are some points worth considering before committing:
Conclusion
Kanban has come a long way from its inception as a simple manufacturing process management tool to the project management tool that it is today. And while Kanban is often associated with development, software, Lean, Agile, and Scrum… do not get tricked. Kanban can be used to manage wide-ranging projects with multiple stakeholders and at the same time, it can be used to help with organizing and managing personal projects.
As discussed earlier, it is obvious that the simplicity, flexibility, ease of deployment, and effectiveness in visualizing workflows, promoting collaboration, and continuously improving processes make Kanban an attractive tool for a variety of industries. It brings a myriad of benefits such as the reduction of bottlenecks, enhanced productivity and efficiency, improved communication and so much more. So, it is a no-brainer when it comes to giving Kanban a shot.
As to why it remains mostly unchanged, the good old rule of if it ain’t broke, don’t fix it applies here perfectly. From the 1940s to 2023, from automotive manufacturing to software development, Kanban has been and still is a simple tool that simply works.
Image credits: Viima, Unsplash
Sign up here to join 17,000+ leaders getting Human-Centered Change & Innovation Weekly delivered to their inbox every week.