How Do Supply Chain Integration and Product Innovation Capability Drive Sustainable Operational Performance?
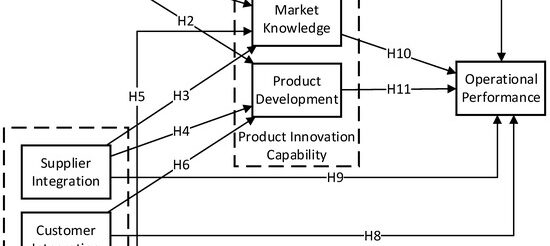
1. Introduction Organizations are under increasing pressure to improve their operational performance in today’s competitive global marketplace. Due to intense competition among companies, awareness of significant elements contributing to firms’ extraordinary performance has been demanded [ 1 , 2 ]. So far, studies have underscored innovation as an engine of competitive advantage [ 3 ]. In this regard, scrutinizing the drivers of innovation has been attempted by many studies [ 4 ]. Improvement of supply chain integration is one way to achieve this goal. As suggested by emergent evidence, supply chain integration (SCI) is a key driver of product innovation capability, and it has been broadly proposed as related to operational performance [ 5 ], as well as sustainability management practices [ 6 ]. SCI is the coordination of activities and information flow between a company and its suppliers, customers, and other partners in the supply chain. It normally involves outward incorporation with its customers and suppliers, and internal integration or association by all intra-organizational functions. A number of studies have shown that SCI can have a positive influence on operational performance (OP). For example, companies with low levels of SCI had significantly higher costs and lower customer satisfaction than companies with high levels of SCI, which had higher customer satisfaction found by [ 7 ]. A study by Liu, Lin [ 8 ] found customer satisfaction, on-time delivery, and inventory turns were positively influenced by SCI. However, there is no straightforward relationship between SCI and OP, and it is influenced by numerous factors, such as product innovation capability (PIC), which is one of them [ 9 ]. PIC is the capability of an organization to develop and introduce new products to the market that meet the needs of customers and differentiate themselves from their competitors, so it is helpful to maintain a competitive advantage. Several studies have revealed that PIC can have a positive influence on OP. For example, Song, Fan [ 10 ] found in their work that businesses with high levels of PIC had considerably higher sales growth and market share than companies with low levels of PIC. Lin, Chen [ 11 ] also described in their study that PIC has a positive relationship with product quality, customer satisfaction, and financial performance. On the other hand, PIC itself can be influenced by SCI (internal and external) [ 12 ]. A critical question arises if we consider the above-stated set of interactions. RQ: To what extent does SCI translate into better OP, and how does PIC mediate this relationship? We adopted a quantitative research design with a deductive approach to address the above-stated research question. We collected data through questionnaires and analyzed it through partial least squares structural equation modeling (PLS-SEM). Most of the existing research has concentrated on the direct connection between the two variables of SCI and OP and has not deliberated on the potential mediating role of PIC. This research gap is significant because product innovation capability can be influenced by a company’s supply chain integration, both internally and externally [ 13 ]. The major contribution of this study is that SCI and operational performance are intellectualized as multidimensional concepts rather than a unidimensional slant used by various researchers. Thus, this work intends to attain a thoughtful and insightful understanding of the role of SCI in operational performance by cherishing PIC from the perspective of manufacturing companies. In this study, we consider the mediating effects of PIC in the link between SCI and OP [ 14 ]. The rest of the paper is designed as follows to achieve the research objective. Section 2 reviews SCI and its relationship with product innovation capability and operational performance in the form of research hypotheses. Section 3 describes the data and methodology. Section 4 analyzes data and presents results. Section 5 discusses the results and provides valuable implications. Section 5 concludes the entire research. Finally, limitations and future research have been described in Section 6 . 2. Theoretical Background and Conceptual Foundation The theoretical support for this research framework comes from the resource-based view (RBV) of the firm [ 15 ], incorporating the sustainability concept into the variables. The RBV claims that firms are heterogeneous in terms of their resources and capabilities and that those means and proficiencies are the basis of sustainable competitive advantage. The RBV theory argues that a firm’s performance can be explained by its strategic resources, such as core competencies [ 16 ]. In this research, a firm’s supply chain integration (SCI) and production innovation capability (PIC) can be considered strategic resources that contribute to its operational performance (OP). RBV theory also highlights the significance of internal possessions and capabilities for operational performance. Thus, SCI is a resource that can be used to enhance sustainable OP. SCI is the coordination of activities and information flow between a company and its suppliers, customers, and other partners in the supply chain. It is essential for improving efficiency, reducing costs, and hence enhancing customer satisfaction, which can lead to operational excellence from a sustainable perspective. RBV theory also underlines the importance of innovation to achieve sustainable competitive advantage [ 17 ]. Product innovation capability (PIC) is another resource that can be used to enhance OP. PIC discusses the capacity of an enterprise to develop and introduce new products to the market. As it allows companies to offer new products that meet customers’ needs and differentiate themselves from their competitors, it is a critical factor in maintaining competitive advantage. For examining the connection between SCI, PIC, and operational performance, RBV theory provides a theoretical foundation. The RBV theory proposes that a firm’s internal and external resources and capabilities, together with SCI and PIC, augment its competitive advantage and OP. 2.1. Product Innovation Capability Synthesis of knowledge, valuable new products, services, or processes, and the successful presentation of a new idea or method is called innovation from an organizational perspective [ 18 ]. It could also be established or brand-new business products, services, or internal processes, and it is considered a significant cause of competitive gain. That comes from the capability of enterprises to get involved in value creation [ 19 , 20 ]. In an organization, the most critical determinant of performance is innovation capability, a degree of firm innovativeness [ 21 ]. Researchers and the literature distinguish different types of innovation. Some studied a particular type of innovation, like product innovation [ 22 , 23 ], process innovation [ 24 ], or marketing and organizational innovation [ 25 , 26 ]. Product, process, organizational, and marketing innovation are the most commonly applied categorizations of innovation in the Oslo Manual [ 27 ]. Reliable innovation in SMEs is carried out by adopting technology in the process and product innovation [ 28 , 29 ]. It is curious to ascertain the part of SCI in the development of PIC [ 23 ]. To supplement the work, we emphasize PIC in the current study. It is the capability to advance new or enhanced products to meet market requirements [ 30 ]. Based on this definition, market knowledge (MK) and product development (PD) capability are the two dimensions of product innovation capability. From the former dimension, it is probable for a company to generate cherished information to create or advance its product portfolio. From the second dimension, it is likely to provide a sustainable competitive benefit [ 31 ]. 2.2. Supply Chain Integration (SCI) As a research area, the SCI construct is relatively new. Managing intra-organization processes among inner functions and cross-institutional procedures with customers and suppliers refers to a firm’s operational capabilities, called SCI [ 5 , 7 ]. Some authors have examined SCI as a unidimensional construct [ 32 , 33 ], while others have broken this construct into different dimensions [ 34 , 35 , 36 ]. We argue the diverse dimensions of SCI and complicate the present literature on the SCI construct, comprising the manufacturer (internal integration) and prolonging from it in both directions (supplier and customer integration). SCI is the degree to which a manufacturer jointly succeeds in intra- and inter-organization processes and strategically collaborates with its supply chain partners. The objective is to offer supreme value to the consumer at great speed and minimum cost through well-organized and effective flows of products, services, and information [ 7 ]. Further, preceding research has emphasized the significance of distinguishing between external and internal integration for accomplishing OP [ 37 , 38 ]. The operational capability of an organization to work in partnership with its customers and suppliers is called external integration, whereas the operational capability of an organization to collaborate with all of its in-house functions is called internal integration [ 5 , 39 ]. 2.3. Operational Performance The performance of the in-house operation of an enterprise with respect to product/process quality, efficiency, and productivity is termed OP [ 40 ] and is an indicator used to measure how proficiently a firm accomplishes its aims [ 18 ]. In order to provide a deep understanding, OP needs to be measured as a multidimensional concept, and in literature, different dimensions have been considered, including cost, quality, delivery, and flexibility [ 2 , 41 , 42 ], inventory turnover [ 43 ], lead time [ 44 ], and defect percentage [ 33 ]. In the current study, cost, quality, delivery, and flexibility are the four capacities used to measure OP. Santos Bento, Tontini [ 45 ] also found that the abovementioned four areas are the most common operational performance indicators. 2.4. Hypotheses Development 2.4.1. Internal Integration (II) and Product Innovation Capability Internal integration is significant and superior to improving cost, quality, and information sharing among different departments in an organization. Collaboratively working on internal functions refers to II and is attained by eradicating functional obstacles [ 7 ]. II enables cross-functional teams to innovate and advance product and process designs [ 33 ]. New product innovation capability and processes are accelerated by avoiding delays and eliminating steps [ 46 ]. Information sharing across functions such as marketing, production, and R&D helps facilitate product innovation capability [ 47 ]. Gomes, de Weerd-Nederhof [ 48 ] found a substantial association between II and product innovation by surveying 40 British and Dutch enterprises from several areas. Internal integration bolsters collaboration and knowledge sharing among different departments within the institute, and when different departments work together, they can collectively gather insights and expertise from various perspectives. Such a collaborative environment facilitates the exchange of market-related information and customer feedback and plays a spirited role in humanizing organizational knowledge [ 49 ], leading to enhancing market knowledge. Internal integration brings together individuals with diverse expertise and skills from various functional regions, allowing for a comprehensive market understanding. By fostering knowledge sharing, cross-functional expertise, data accessibility, rapid communication, and alignment of strategies, internal integration positively impacts market knowledge [ 50 ], and the hypothesis is proposed as follows: Hypothesis 1: Internal integration has a positive impact on the market knowledge of manufacturing organizations. When teams work together and leverage each other’s expertise, it enriches the quality of product development by incorporating diverse perspectives and insights from various stakeholders within the organization [ 51 ]. Throughout the product development process, the integration of different departments, such as marketing, manufacturing, design, engineering, and quality assurance, ensures that all aspects of product development are aligned and optimized. In summary, by nurturing collaboration, cross-functional cooperation, resource optimization, streamlined processes, innovation, and continuous improvement, organizations can enhance their product development capabilities [ 23 , 52 ], and we propose the following hypothesis: Hypothesis 2: Internal integration has a positive impact on the product development of manufacturing organizations. 2.4.2. External Integration (EI) and Product Innovation Capability EI implicates knowledge sharing and strategic alignment of business processes with customers and suppliers [ 7 ]. External integration sanctions organizations to gain knowledge about customers’ needs and shares this product design requirement with suppliers [ 53 ]. This type of integration is known to be more effective in constructing collaboration with customers and suppliers [ 52 ]. Because of EI, new product innovation processes are closely linked between customers and suppliers [ 53 ]. The product innovation capability of manufacturing organizations will be enhanced by including or integrating external partners (suppliers and customers). External integration or collaboration between companies and external parties increases innovation capability in new product development [ 54 , 55 , 56 ], and external integration helps advance the capabilities usually possessed by suppliers and customers [ 57 ], where the purchasing and manufacturing department’s staff need to make sure suppliers understand the design and new products’ manufacturing process. Khair, Zaid [ 58 ], He, Lai [ 55 ], and Purnama, Wardana [ 52 ] also recommended that by implementing external integration, product innovation capability is enhanced. Active involvement of customers in the innovation process of an enterprise is called customer integration, which sanctions companies to gather insights, feedback, preferences, pain points, and ideas directly from customers, whereas understanding the market dynamics, customer needs, and competitors’ offerings refers to market knowledge. The collection of real-time feedback on product prototypes is facilitated by customer integration, and this feedback loop helps companies identify potential issues, make necessary adjustments to their product offerings, and validate their assumptions. Companies can ensure that their products align with market demands and preferences by involving customers in this iterative process. Customer integration allows companies to gain a deeper understanding of their diverse market segments and adapt their products accordingly, as well as tap into their collective wisdom and gain insights into emerging market trends and demands [ 59 ]. Overall, in terms of product innovation capability, customer integration positively impacts market knowledge, and the hypothesis proposed from the above argument is as follows: Hypothesis 3: Customer integration has a positive impact on the market knowledge of manufacturing organizations. Manufacturing organizations can gain a deep understanding of the customers’ preferences and obtain information from customers by involving them in the process, and this customer integration allows companies to adopt a customer-centric approach to product development, resulting in higher customer satisfaction [ 52 ]. Companies can gather customer opinions on features, functionalities, usability, and aesthetics during the product development phase, and the incorporation of such customer feedback early on can prevent costly design flaws and enhance product relevance, which increases the chances of product success and acceptance. Customer integration allows companies to identify and address potential issues or shortcomings before the product reaches the market, and this iterative feedback loop enables continuous improvement [ 23 ]. Customers often come up with unique ideas and suggestions, and involving customers in brainstorming sessions can fuel innovation. Customers develop a sense of ownership and loyalty towards the product and drive word-of-mouth referrals when they feel involved in the product development process. A hypothesis proposed from the above argument is as follows: Hypothesis 4: Customer integration has a positive impact on the product development of manufacturing organizations. Suppliers bring their specialized knowledge and expertise and provide insights into market trends and emerging technologies when integrated into product development. Enterprises incorporate supplier knowledge and capabilities into product design, leading to more tailored solutions, and such customization augments the understanding of customer preferences, eventually strengthening market knowledge [ 60 ]. Supplier integration can streamline the supply chain, and by harnessing the combined expertise of internal and external stakeholders, such integration can provide companies with a competitive advantage [ 23 ]. A hypothesis proposed from the above argument is as follows: Hypothesis 5: Supplier integration has a positive impact on the market knowledge of manufacturing organizations. Companies can tap into their expertise, knowledge, and resources by involving suppliers early in the product development process. Suppliers often possess specialized resources and technologies, and companies can leverage these resources and technologies to gain access to advanced components, materials, or production techniques by integrating suppliers into the development process. Supplier integration improves supply chain efficiency, promotes continuous innovation and iteration in product development risk mitigation, and enables the development of more innovative and technologically advanced products [ 23 ]. That is why enterprises are advised to increase their internal capacity to absorb external information from suppliers [ 52 ]. A hypothesis proposed from the above argument is as follows: Hypothesis 6: Supplier integration has a positive impact on the product development of manufacturing organizations. 2.5. Relationship between Internal Integration and Operational Performance Inside a firm, various departments and functional areas jointly operate, which is called internal integration. II is anticipated to be related to performance because it breaks down functional obstructions rather than traditional departmentalization in order to meet the customers’ requirements. Customer orders flow across functions even though manufacturers may retain a functional organization arrangement. Customer orders delayed calls for an integrated customer order fulfillment process, and cross-functional teams, joint planning, and information sharing are significant elements of this process [ 7 ]. Due to the interdependence of supply chains and their inherent complexity, it is challenging to select the appropriate performance measures. SC’s performance dimension must take into account operational indicators, like the ability to respond to a shifting environment and customer service, as Beamon and management [ 61 ] and Van Hoek [ 62 ] suggested. Flynn, Huo [ 7 ], Gimenez and Ventura [ 63 ], Simbarashe, Charumbira [ 64 ], and Srinivasan and Swink [ 38 ] found a positive affiliation between II and OP. These scholars propose that to optimize process and product design, II assists the alliance of various departments, thus improving quality and reducing cost [ 39 , 65 ]. Furthermore, to improve production capacity and delivery performance, II enables knowledge sharing across functions by breaking down functional obstacles [ 7 , 37 , 66 ]. We argue that for SCI, the base is internal integration and will be significantly connected to OP. Hence, we endorse: Hypothesis 7: II has a positive impact on the OP of manufacturing organizations. 2.6. Relationship of External Integration to Operational Performance External integration (EI) reveals the degree of alliance between a firm and its customers and suppliers [ 67 ] and helps manage inter-organizational business processes [ 68 ]. By selecting, developing, and implementing strategies, a manufacturer should respond to its external environment changes to maintain a fit with its exterior setting. Thus, a manufacturer’s internal integration helps build supplier and customer integration [ 7 ]. Improvement in the accuracy of demand information is possible because of the handy connection between the manufacturer and customers, and it reduces production planning time and inventory obsolescence. Thus, it enables manufacturing organizations to create greater value, reduce costs, and anticipate changes in demand speedily. In order to better meet the manufacturing organization’s needs and anticipate its varying requirements, strong strategic partnerships with suppliers will be helpful in any integrated supply chain. This information exchange about schedules and processes helps manufacturing organizations produce goods, thus improving their delivery performance. Suppliers’ strong understanding of the manufacturing organization’s operations helps the companies enhance their customer service. It has been established that supplier integration is connected to product development performance [ 69 , 70 ]. As external integration allows firms to organize supply and demand excellently, it is supportive in the optimization of their production plans, enlightening the production flexibility and delivery routine [ 39 ]. Likewise, external integration encourages joint efforts to improve quality and reduce costs [ 68 ]. Finally, numerous studies supported a positive link between EI and OP [ 5 , 38 , 39 , 64 ]. 2.7. Customer Integration and Operational Performance Actively involving customers in product development, service design, decision-making processes, forecasting, and planning activities allows organizations to tailor their operations accordingly [ 71 ]. It results in more efficient operations, reduced inventory costs, and minimized stockouts [ 65 ]. Organizations can identify potential issues and make necessary adjustments by engaging customers in pilot programs and feedback sessions. This customer-centric approach reduces the costs associated with customer complaints and returns and leads to improved operational efficiency and higher customer satisfaction [ 66 ]. Thus, we hypothesize the following: Hypothesis 8: Customer integration has a positive impact on the operational performance of manufacturing organizations. 2.8. Supplier Integration and Operational Performance Organizations can streamline procurement, production scheduling, and inventory management by integrating suppliers into their supply chain processes. Such value-added coordination leads to reduced lead times and increased overall supply chain efficiency [ 65 ]. Also, to ensure consistent product quality and adherence to specifications, organizations implement supplier quality management programs and integrate suppliers into quality control processes. In this way, firms can evaluate supplier performance by establishing key performance indicators (KPIs) and performance metrics (a proactive approach). In short, firms improve product quality, reduce costs, mitigate risks, and drive innovation, eventually leading to enhanced operational performance by integrating suppliers into their operational processes [ 66 , 71 ]. Thus, we hypothesize the following: Hypothesis 9: Supplier integration has a positive impact on the OP of manufacturing organizations. 2.9. Product Innovation Capability and Operational Performance In a struggle to attain the best organizational performance, the innovation capability of an organization integrates the key capabilities and resources [ 72 ]. To deal with a continuously fluctuating situation, innovation capability integrates, shapes, and reconfigures both internal and external competence [ 73 ]. The development of excellent new innovative products is enabled by high innovation capability, and this capability is critical to prospering in the long run. In this way, product innovation capability is considered a cherished asset for organizations and a driver of operational performance. Kafetzopoulos and Psomas [ 21 ] stated that there is a substantial and profound effect of PIC on the OP of manufacturers. Iranmanesh, Kumar [ 18 ] also confirmed that the operational performance of manufacturing organizations is highly dependent on their product innovation capability. 2.10. Market Knowledge and Operational Performance For the purpose of gaining a deeper understanding of market trends and customer preferences, market knowledge is helpful, which can improve the organization’s demand forecasting accuracy. With this accurate demand forecasting, organizations align their production capacities and optimize resource allocation, leading to improved operational performance. An imperative feature of market knowledge for improving OP in a supply chain environment is the social compliance [ 74 ]. Market knowledge plays a major role in the exceptional performance of any organization [ 75 , 76 ]. Organizations can achieve a long-term competitive edge through the knowledge management process [ 77 , 78 ]. Thus, we hypothesize the following: Hypothesis 10: Market knowledge has a positive impact on the OP of manufacturing organizations. 2.11. Product Development and Operational Performance To draw new product development strategies is very important because it is not simply to promote new products but to fulfill customer needs and survive competitors’ threats [ 8 , 79 ]. Companies can enhance their overall operational performance by streamlining manufacturing processes, optimizing product designs, and reducing material waste. Higher product quality is possible due to a well-structured product development process that includes thorough testing and validation. Organizations maintain optimal operational performance and stay ahead of competitors by adapting to changing market demands quickly and adjusting their product offerings efficiently. Those organizations are more likely to achieve a competitive edge when they invest in effective product development practices. Valuing the employees’ contributions and involvement in product development ultimately leads to improved operational performance. In consequence, a business’s product development capability is becoming an important weapon and positively influences a firm’s operational performance [ 80 , 81 ]. On the basis of the above research, the following hypothesis is suggested: Hypothesis 11: Product development has a positive impact on the OP of manufacturing organizations. 2.12. Indirect Relationship between Constructs Eleven hypotheses (H1 up to H11) have been formulated based on previous discussions of various researchers about two consecutive constructs’ relationships. Between any two constructs, a direct relationship is revealed from those hypotheses, and based on such kind of direct relationship, the indirect relationship can be hypothesized to reflect the mediating role of PIC (MK and PD), and the following six hypotheses are developed as follows: Hypothesis 12: MK mediates the relationship between II and operational performance. Hypothesis 13: MK mediates the relationship between customer integration and operational performance. Hypothesis 14: MK mediates the connection between supplier integration and operational performance. Hypothesis 15: PD mediates the association between II and operational performance. Hypothesis 16: PD mediates the association between customer integration and operational performance. Hypothesis 17: PD mediates the relationship between supplier integration and operational performance. A model can be portrayed from the developed hypotheses, as exposed in Figure 1 . 3. Methodology A questionnaire was used to test our hypotheses. A widely used management research approach, partial least squares structural equation modeling (PLS-SEM), was applied for the subsequent analysis of the collected data [ 82 ]. It was considered appropriate for this analysis based on the sample size and the model’s characteristics [ 83 ]. The statistical data analysis, including the estimated significance levels of relationships using the bootstrapping technique, was done with the help of Smart PLS 3 software. 3.1. Ethical Statement This study was conducted as per the ethical guidelines given in the Helsinki Declaration. The authors got approval from the ethical committee of the National College of Business Administration and Economics, Pakistan, Ref: NCBA&E-2023-3. 3.2. Sample and Data For this research, the target population was manufacturing organizations operating in Pakistan, and the data were collected between August 2021 and October 2022. Organizations with less than 75 personnel were left out of the population to avoid the inclusion of very small firms. The target population was 207 medium and large manufacturers. Because of an in-depth understanding of the organization’s structure and innovation capabilities, data were collected from executive managers of the target organizations. They were contacted through personal and university relations. A link to the online survey was sent to potential respondents, along with follow-up phone calls at two-week intervals. After eliminating missing data associated with the variables in our research, the final sample contains 129 firms, representing a response rate of 62%. To compare the dissimilarities between organizations that finished the matched surveys and those that did not, a t -test was applied in view of nonresponse bias. On the subject of mean scores of the constructs and the underlying items, these groups exhibited no significant difference, signifying nonresponse bias was not severe [ 5 , 84 ]. Table 1 presents the sample demographics. Here, the potential for common method bias must be inspected because independent and dependent variables are inquired about at the same time and in a cross-sectional slant [ 85 ]. To assess the extent of the bias, we conducted an analysis using Harman’s one-factor test. The result shows that the study does not have significant concerns related to common method bias because a single factor accounts for 29.4% of the variation. 3.3. Measures A quantitative survey was performed using a structured questionnaire that was separated into five sections, including basic personal and company information, supply chain integration, product innovation capability, and operational performance. Constructs were operationalized with multiple items, and items were adapted from existing studies to ensure content validity. For a detailed description, see Appendix A . 3.4. Product Innovation Capability MK and PD are the two reflective first-order constructs of product innovation capability. Items of both dimensions were assessed using a seven-point Likert-type scale ranging from 1 = absolutely unsatisfactory to 7 = absolutely satisfactory. MK measured the company’s capability to use new technologies to comprehend the market, update operations, and develop requisite quality. On the other hand, the company’s capability to improve existing or develop new products is evaluated through product development items [ 23 ]. The scale of product innovation capability was adapted from Freije, de la Calle [ 23 ]. 3.5. Supply Chain Integration (SCI) This construct comprises two dimensions: External integration (supplier and customer integration) and internal integration. Each item of the stated first-order constructs in the questionnaire was measured with a five-point Likert scale, ranging from 1 (“strongly disagree”) to 5 (“strongly agree”). Supplier integration items look to joint planning, partnership, and knowledge sharing with suppliers. The extent of collaboration between the organizations and their clientele is reflected through customer integration items. Four internal integration items find the extent of collaboration between the departments within the firm and consider the aspects of responsiveness and system integration [ 5 ]. The scale of SCI was adopted from Liu, Liu [ 5 ]. 3.6. Operational Performance Four measures of OP are production cost, product quality, delivery, and production flexibility, and their measures were adapted from Shou, Li [ 86 ]. Two items of cost, quality, and delivery, and three items of flexibility were measured by five-point Likert scales, in which the upper value specified enhanced performance. 4. Analysis and Results 4.1. Reliability and Validity The final analysis was conducted after removing some items with low factor loadings, which are CI4 and OP8. Several techniques are used to examine the construct’s reliability and validity. Cronbach α and composite reliability (CR) values above the threshold of 0.70 specify good reliability for each scale [ 87 ], as shown in Table 2 . Second, there is good convergent validity in that the measurement model fits the data excellently (CMIN/df = 549.77/281 = 1.957, CFI = 0.973, RMSEA = 0.051, SRMR = 0.037), as indicated by confirmatory factor analysis (CFA) results. Figure 2 shows the CFA for measurement model. Third, the threshold of 0.50 is below all the values of average variances extracted (AVE), and their square roots are higher than the correlations with other constructs (see Table 2 ) and exhibit good discriminant validity [ 88 ]. 4.2. Hypothesis Testing To explore mediation in a number of studies [ 89 ], a methodology described by Zhao, Lynch Jr [ 90 ] has been applied, and we applied the same in order to test our hypotheses. This methodology can establish mediation without demanding a significant direct effect if we compare it with Baron and Kenny’s criteria. Zhao, Lynch Jr [ 90 ] methodology replaces the Baron-Kenny steps with only one test: a bootstrap test of the indirect effect, which has proven to be rigorous. To analyze our proposed model, we execute the bootstrap test in SPSS. Figure 3 shows the bootstrap testing result. As displayed in Table 3 , bootstrap results show a significant relationship between internal integration and market knowledge ( β = 0.306, p < 0.001), which offers backing for H1. The results of Table 3 show that II exerts a notable profound effect on product development ( β = 0.154, p = 0.006), customer integration exerts a substantial positive Influence on market knowledge ( β = 0.209, p = 0.008), customer integration exerts a substantial positive impact on product development ( β = 0.413, p < 0.001), supplier integration exerts a significant positive effect on market knowledge ( β = 0.194, p = 0.001), and supplier integration exerts a significant positive effect on product development ( β = 0.324, p < 0.001), so H2, H3, H4, H5 and H6 are supported. Conversely, internal integration and customer integration have no significant impact on OP ( β = 0.091, p = 0.133), ( β = −0.106, p = 0.139). Therefore, H7 and H8 have not stayed. Further, the results in Table 3 also show that SI relates positively to OP ( β = 0.398, p < 0.001), market knowledge links confidently to OP ( β = 0.235, p < 0.001), and product development relays positively to OP ( β = 0.281, p < 0.001), so H9, H10, and H11 are supported. 4.3. Mediation Analysis Based on the criteria for mediating effects introduced by Zhao, Lynch Jr [ 90 ], Table 4 tabulates the results of the mediation effects. Full, partial, and no mediation are the three types of mediation effects [ 89 ]. From Table 4 , out of six hypotheses, four are fully mediated, and others are partially mediated. The variables MK and PD fully mediate the relationship between internal integration (II) and OP as well as between customer integration (CI) and OP. Whereas, MK and PD partially mediate the relationship between supplier integration (SI) and OP. 5. Discussion Our knowledge of the question “how SCI influences OP” [ 64 , 86 ] remains limited in spite of the calls for research on the underlying mechanisms. We fill this gap by investigating how a firm’s product innovation capability mediates SCI’s effect on operational performance. On the basis of data from 129 manufacturing firms in Pakistan, the findings show that supplier integration directly advances operational performance, while II and CI did not. Addressing the OP regarding a firm’s efficiency in transforming various inputs into outputs is a possible explanation for these findings. EI stresses boosting existing transactions between firms, customers, and suppliers, and internal integration can directly increase revenue by reducing costs, thus improving OP. We also find an unpredicted result: II did not improve OP. This outcome is similar to several answers in earlier studies that question the worth of II in product innovation capability [ 23 , 53 ] and operational performance [ 5 , 51 ]. Lastly, the outcomes directed that the OP of manufacturers is greatly reliant on their product innovation capability (H10 and H11). This reveals the position of innovation in enhancing the OP of firms, which involves four main proficiencies that a manufacturing firm needs to survive in the existing competitive market. This result agrees with the previous study that product innovation capability could improve operational performance [ 18 , 21 ]. Additionally, this study has developed indirect-effect hypotheses through the intervening variable. The hypotheses H12, H13, H14, H15, H16, and H17 state that II and EI (SI and CI) affect operational performance through PIC (MK and PD), which is not reinforced in current research. Nevertheless, II and CI do not directly affect operational performance (H7 and H8). Our findings confirm that PIC fully mediates the link between II, CI, and operational performance. The results show that the effect of product innovation capability cannot be countered in improving operational performance, and enterprises should take solid steps to foster product innovation capability. So, the findings of the current work also support hypotheses H12, H13, H14, H15, H16, and H17. 5.1. Theoretical Implications This study introduces a growing but inadequately covered field of supply chain integration and product innovation capability influencing operational performance. This study helps in three ways. The first contribution is the consideration of the SCI-performance association by connecting SCI and OP and segregating the impacts of EI and II on OP. Explicitly, in preceding research on SCI, the performance relationship ignored more comprehensive measurements of a firm’s overall operating efficiency but has generally concentrated on conventional performance measures such as technological innovation and financial performance. The second contribution is an analysis of how SCI translates into product innovation capability. SCI has been claimed to be an enabler in product innovation capability [ 23 ], and we make practical proof available to exhibit the association between SCI dimensions and product innovation capability. This approach is fascinating because of the eminence usually given to customers and the clear differences in handling the various dimensions of the supply chain. Third, to unpack the link between SCI and OP, it is crucial to consider the intermediary factor that explains how SCI matters. By indicating an intermediate mechanism with product innovation capability, we encompass this torrent of research that links SCI and operational performance, as our review of business literature revealed that there is seldom a study that unequivocally addresses the intermediary elements. Empirical findings of this study suggest that product innovation capabilities mediate the association between SI (a dimension of SCI) and firms’ OP. 5.2. Managerial Implications Superior OP is critical for manufacturing organizations to survive and thrive in a competitive market. To enhance cost performance, quality, delivery, and flexibility, both researchers and practitioners regard SCI as a strategic means. Our research provides initial evidence to strategic managers that SCI improves operational performance and nurtures operational performance through product innovation capability. Without compromising operational performance, SCI can enhance environmental performance. It means that managers should go beyond economic results. Further, supply chain managers are often responsible for implementing strategic decisions in a firm. In this study, they are also responsible for enhancing operational performance and integrating the supply chain of the enterprise. Our results suggest that supply chain managers need to invest in EI with customers and suppliers to support supply chain integration and increase OP simultaneously. For example, they can nurture external integration in terms of information sharing and joint planning with customers and suppliers. From this research, policymakers can also gain interesting insights, mainly in regions with a sound industrial base where product innovation capabilities and operational performance can open new business opportunities as well as strengthen existing manufacturing ones. In the present condition, with primarily low levels of integration, there is a wide edge of improvement. Apart from boosting external collaboration, emphasizing the importance of internal integration capabilities, which are perhaps less widely considered in policy agendas, could also be very beneficial. Managers of manufacturing organizations should put supplementary emphasis on PIC, as it is a significant factor for achieving sustainable competitive advantage and improving overall firm performance. It may guide companies in achieving better OP by using innovation. So, for managers, there are clear, practical implications to allocating resources and choosing strategies in order to advance their enterprise’s operational performance. 6. Conclusions This research aimed to understand the influence of SCI dimensions, specifically internal integration (II) and external integration (EI), on product innovation capability (PIC) and operational performance (OP) of manufacturing firms, with PIC acting as a mediator. The data were collected through a survey of 129 medium and large manufacturers in Pakistan, and structural equation modeling was employed for analysis. The findings, based on the structural equation modeling technique, indicate that supplier integration (SI) directly impacts both PIC and OP. However, II and customer integration (CI) do not have a direct relationship with OP. This unexpected result aligns with previous studies that question the effectiveness of II in enhancing product innovation capability and operational performance. Furthermore, the study reveals that the link between PIC and OP is positive, highlighting the importance of innovation in improving firm performance. The study also identifies that PIC fully mediates the effects of II and CI on OP, indicating that product innovation capability plays a crucial role in enhancing operational performance. Theoretical implications of this research include filling the gap in understanding the relationship between SCI, PIC, and OP. The study contributes by considering the comprehensive measurement of a firm’s overall operating efficiency and examining the translation of SCI into product innovation capability. It also highlights the importance of considering the mediating role of PIC in the SCI-OP relationship, which was often overlooked in previous research. From a managerial perspective, the findings suggest that supply chain managers should enhance EI with customers and suppliers to simultaneously improve supply chain integration and operational performance. The study emphasizes investing in PIC to achieve sustainable competitive advantage and overall firm performance. The limitations of this study include the use of cross-sectional data and the absence of qualitative data in the questionnaires. Future research can address these limitations by employing longitudinal data, analyzing the evolution of capabilities, and considering other operational capabilities related to SCI. 7. Limitations and Future Research The limitations of this study can be addressed in future research projects. First, we got limited responses (129); however, if the number of respondents is increased, it would be possible to have more solid and generalizable statistical results. Second, this analysis employed cross-sectional data, but if longitudinal data are collected, it can help understand changes over time. It would also be remarkable to analyze the evolution of these capabilities and their impact on operational performance in the service industry and compare them with other regions. Third, we highlight the mediating effects of product innovation capability between SCI and OP. It may be productive to consider operational capabilities related to other mechanisms. Fourth, due to various contingency factors, the effects of supply chain integration on product innovation capability may be influenced. So, there is a further need for empirical investigations. Finally, the research is based on quantitative analysis, but future research can collect qualitative data to capture the soft aspects related to performance. The paper can also be enriched by providing a better understanding of the causal mechanisms between SCI, PIC, and OP through interviews with members of the firms included in the sample. According to specific supply chain conditions, industry, and other specific characteristics, case studies should be developed to comprehend the particularities of these relationships. For companies, researchers, and policymakers, precise stimulating insights might be extended from such research. Future researchers are also encouraged to explore the effect of confounding variables to enhance the robustness of the research and contribute to a more nuanced understanding of the relationships. Moreover, future studies from the perspective of developed countries may enrich the current findings. Author Contributions Conceptualization, A.A.A. and A.M.; methodology, A.M.; software, A.M.; validation, A.A.A.; formal analysis, A.M.; investigation, A.A.A.; resources, A.A.A.; data curation, A.A.A.; writing—original draft preparation, A.A.A.; writing—review and editing, A.M.; visualization, A.A.A.; supervision, A.M.; project administration, A.M.; funding acquisition, A.A.A. All authors have read and agreed to the published version of the manuscript. Funding This research received no external funding. Institutional Review Board Statement This study was conducted in accordance with the ethical guidelines given in the Helsinki Declaration. The authors got approval from the ethical committee of the National College of Busi-ness Administration and Economics, Pakistan, Ref: NCBA&E-2023-3. Informed Consent Statement Informed consent was obtained from all subjects involved in the study. Data Availability Statement The data that support the findings of this study are available from the corresponding author upon reasonable request. For inquiries and requests regarding access to the data, please contact Asif Mahmood at [email protected] . Conflicts of Interest The authors declare no conflict of interest. Appendix A Table A1. Survey items and confirmatory factor analysis results. Table A1. Survey items and confirmatory factor analysis results. Construct and Items Standardized Loading Internal integration (Cronbach’s α = 0.87) Have a high level of responsiveness within our plant to meet other department’s needs. 0.871 Have an integrated system across functional areas under plant control. 0.811 Within our plant, we emphasize information flows among purchasing, inventory management, sales, and distribution departments. 0.898 Within our plant, we emphasize physical flows among production, packing, warehousing, and transportation departments. 0.918 External Integration: Customer integration (Cronbach’s α = 0.88) Have a high level of information sharing with major customers about market information. 0.893 Share information with major customers through information technologies. 0.878 Have a high degree of joint planning and forecasting with major customers to anticipate demand visibility. 0.878 Our customers provide information to us in the procurement and production processes. Deleted Our customers are involved in our product development processes. 0.883 Supplier integration (Cronbach’s α = 0.92) Share information with our major suppliers through information technologies. 0.951 Have a high degree of strategic partnership with suppliers. 0.921 Have a high degree of joint planning to obtain rapid response ordering process (inbound) with suppliers. 0.871 Our suppliers provide information to us in the production and procurement processes. 0.947 Our suppliers are involved in our product development processes. 0.885 Product Innovation Capability: Market knowledge (Cronbach’s α = 0.85) Capability for being updated with market knowledge. 0.858 Capability for developing quality in products (as the market requires). 0.885 Capability for using new technologies and knowledge. 0.909 Product development (Cronbach’s α = 0.86) Capability for developing new products. 0.980 Capability for developing improvements in existing products. 0.857 Operational performance (Cronbach’s α = 0.86) Unit manufacturing cost 0.835 Ordering costs 0.834 Conformance quality 0.774 Product quality and reliability 0.823 Delivery speed 0.845 Delivery reliability 0.819 Volume flexibility 0.855 Mix flexibility Deleted Product customization ability 0.802 References Morgan, T.; Anokhin, S.A.; Wincent, J. New service development by manufacturing firms: Effects of customer participation under environmental contingencies. J. Bus. Res. 2019 , 104, 497–505. [Google Scholar] [CrossRef] Arshad Ali, A.; Mahmood, A.; Ahmad, A.; Ikram, A. Boosting Up Operational Performance of Manufacturing Organizations through Interpretive Structural Modelling of Enabling Practices. Mathem. Problems Eng. 2020 , 2020, 8645343. [Google Scholar] [CrossRef] Hwang, W.-S.; Choi, H.; Shin, J. A mediating role of innovation capability between entrepreneurial competencies and competitive advantage. Technol. Anal. Strateg. Manag. 2020 , 32, 1–14. [Google Scholar] [CrossRef] Moaniba, I.M.; Su, H.-N.; Lee, P.-C. On the drivers of innovation: Does the co-evolution of technological diversification and international collaboration matter? Technol. Forecasting Soc. Chang. 2019 , 148, 119710. [Google Scholar] [CrossRef] Liu, A.; Liu, H.; Gu, J. Linking business model design and operational performance: The mediating role of supply chain integration. Ind. Mark. Manag. 2021 , 96, 60–70. [Google Scholar] [CrossRef] Kang, M.; Yang, M.K.; Park, Y.; Huo, B. Supply chain integration and its impact on sustainability. Ind. Manag. Data Syst. 2018 , 118, 1749–1765. [Google Scholar] [CrossRef] Flynn, B.B.; Huo, B.; Zhao, X. The impact of supply chain integration on performance: A contingency and configuration approach. J. Oper. Manag. 2010 , 28, 58–71. [Google Scholar] [CrossRef] Liu, C.-M.; Lin, K.-W.; Huang, C.-J. Effects of product development on operating performance in textile industry. Anthropol. 2014 , 17, 157–163. [Google Scholar] [CrossRef] Lemon, M.; Sahota, P.S. Organizational culture as a knowledge repository for increased innovative capacity. Technovation 2004 , 24, 483–498. [Google Scholar] [CrossRef] Song, Z.-h.; Fan, L.-b.; Chen, S. Knowledge sharing and innovation capability: Does absorptive capacity function as a mediator? In Proceedings of the 2008 International Conference on Management Science and Engineering 15th Annual Conference Proceedings, Long Beach, CA, USA, 10–12 September 2008. [Google Scholar] Lin, R.J.; Chen, R.H.; Kuan-Shun Chiu, K. Customer relationship management and innovation capability: An empirical study. Ind. Manag. Data Syst. 2010 , 110, 111–133. [Google Scholar] [CrossRef] John, T.; DeWitt, W.; Keebler, J.S.; Min, S.; Nix, N.; Smith, C.; Zacharia, Z. Defining Supply Chain Management. J. Bus. Log. 2001 , 22, 1–25. [Google Scholar] Yuen, K.F.; Thai, V.V. The relationship between supply chain integration and operational performances: A study of priorities and synergies. Transp. J. 2016 , 55, 31–50. [Google Scholar] [CrossRef] Huo, B.; Ye, Y.; Zhao, X.; Shou, Y. The impact of human capital on supply chain integration and competitive performance. Int. J. Prod. Econ. 2016 , 178, 132–143. [Google Scholar] [CrossRef] Barney, J. Firm resources and sustained competitive advantage. J. Manag. 1991 , 17, 99–120. [Google Scholar] [CrossRef] Mooney, A. Core competence, distinctive competence, and competitive advantage: What is the difference? J. Educ. Bus. 2007 , 83, 110–115. [Google Scholar] [CrossRef] Teece, D.J.; Pisano, G.; Shuen, A. Dynamic capabilities and strategic management. Strateg. Manag. J. 1997 , 18, 509–533. [Google Scholar] [CrossRef] Iranmanesh, M.; Kumar, K.M.; Foroughi, B.; Mavi, R.K.; Min, N.H. The impacts of organizational structure on operational performance through innovation capability: Innovative culture as moderator. Rev. Manag. Sci. 2021 , 15, 1885–1911. [Google Scholar] [CrossRef] Dess, G.G.; Picken, J.C. Changing roles: Leadership in the 21st century. Org. Dyn. 2000 , 28, 18–34. [Google Scholar] [CrossRef] Lambert, D.M.; Cooper, M.C. Issues in supply chain management. Ind. Mark. Manag. 2000 , 29, 65–83. [Google Scholar] [CrossRef] Kafetzopoulos, D.; Psomas, E. The impact of innovation capability on the performance of manufacturing companies: The Greek case. J. Manuf. Technol. Manag. 2015 , 26, 104–130. [Google Scholar] [CrossRef] Prajogo, D.I.; Sohal, A.S. The multidimensionality of TQM practices in determining quality and innovation performance—An empirical examination. Technovation 2004 , 24, 443–453. [Google Scholar] [CrossRef] Freije, I.; de la Calle, A.; Ugarte, J.V. Role of supply chain integration in the product innovation capability of servitized manufacturing companies. Technovation 2021 , 118, 102216. [Google Scholar] [CrossRef] Abrunhosa, A.; Sá, P.M.E. Are TQM principles supporting innovation in the Portuguese footwear industry? Technovation 2008 , 28, 208–221. [Google Scholar] [CrossRef] Evangelista, R.; Vezzani, A. The economic impact of technological and organizational innovations. A Firm Level Anal. Res. Policy 2010 , 39, 1253–1263. [Google Scholar] Gunday, G.; Ulusoy, G.; Kilic, K.; Alpkan, L. Effects of innovation types on firm performance. Int. J. Prod. Econ. 2011 , 133, 662–676. [Google Scholar] [CrossRef] Data, I.I. Oslo Manual; OECD/Euro-Stat: Paris, France, 2005; OECD/European Community; Available online: https://www.conicyt.cl/wp-content/uploads/2014/07/Manual-de-Oslo.pdf (accessed on 14 August 2023). Siagian, H.; Tarigan, Z.J.H.; Jie, F. Supply chain integration enables resilience, flexibility, and innovation to improve business performance in COVID-19 era. Sustainability 2021 , 13, 4669. [Google Scholar] [CrossRef] Tarigan, Z.J.H. The Impact of Organization Commitment to Process and Product Innovation in Improving Operational Performance; Petra Christian University: Surabaya, Indonesia, 2018. [Google Scholar] Najafi-Tavani, S.; Najafi-Tavani, Z.; Naudé, P.; Oghazi, P.; Zeynaloo, E. How collaborative innovation networks affect new product performance: Product innovation capability, process innovation capability, and absorptive capacity. Ind. Mark. Manag. 2018 , 73, 193–205. [Google Scholar] [CrossRef] Noke, H.; Hughes, M. Climbing the value chain: Strategies to create a new product development capability in mature SMEs. Int. J. Oper. Prod. Manag. 2010 , 30, 132–154. [Google Scholar] [CrossRef] Marquez, A.C.; Bianchi, C.; Gupta, J.N. Operational and financial effectiveness of e-collaboration tools in supply chain integration. Eur. J. Oper. Res. 2004 , 159, 348–363. [Google Scholar] [CrossRef] Rosenzweig, E.D.; Roth, A.V.; Dean, J.W., Jr. The influence of an integration strategy on competitive capabilities and business performance: An exploratory study of consumer products manufacturers. J. Oper. Manag. 2003 , 21, 437–456. [Google Scholar] [CrossRef] Campbell, J.; Sankaran, J. An inductive framework for enhancing supply chain integration. Int. J. Prod. Res. 2005 , 43, 3321–3351. [Google Scholar] [CrossRef] Tiwari, S. Supply chain integration and Industry 4.0: A systematic literature review. Benchmarking Int. J. 2021 , 28, 990–1030. [Google Scholar] [CrossRef] Yu, W.; Chavez, R.; Jacobs, M.; Wong, C.Y.; Yuan, C. Environmental scanning, supply chain integration, responsiveness, and operational performance: An integrative framework from an organizational information processing theory perspective. Int. J. Operat. Prod. Manag. 2019 , 39, 787–814. [Google Scholar] [CrossRef] Huo, B.; Qi, Y.; Wang, Z.; Zhao, X. The impact of supply chain integration on firm performance: The moderating role of competitive strategy. Supply Chain Manag. Int. J. 2014 , 19, 369–384. [Google Scholar] [CrossRef] Srinivasan, R.; Swink, M. Leveraging supply chain integration through planning comprehensiveness: An organizational information processing theory perspective. Decis. Sci. 2015 , 46, 823–861. [Google Scholar] [CrossRef] Wong, C.Y.; Boon-Itt, S.; Wong, C.W. The contingency effects of environmental uncertainty on the relationship between supply chain integration and operational performance. J. Oper. Manag. 2011 , 29, 604–615. [Google Scholar] [CrossRef] Nabass, E.H.; Abdallah, A.B. Agile manufacturing and business performance: The indirect effects of operational performance dimensions. Bus. Pro. Manag. J. 2019 , 25, 647–666. [Google Scholar] Sancha, C.; Wiengarten, F.; Longoni, A.; Pagell, M. The moderating role of temporary work on the performance of lean manufacturing systems. Int. J. Prod. Res. 2020 , 58, 4285–4305. [Google Scholar] [CrossRef] Arshad, A.; Mahmood, A.; Salam, A. Prioritizing the practices that influence the operational performance of manufacturing organizations using hybrid AHP-TOPSIS analysis. S. Afr. J. Ind. Eng. 2020 , 31, 65–77. [Google Scholar] Liu, H.; Wu, S.; Zhong, C.; Liu, Y. The sustainable effect of operational performance on financial benefits: Evidence from chinese quality awards winners. Sustainability 2020 , 12, 1966. [Google Scholar] [CrossRef] Bayraktar, E.; Sari, K.; Tatoglu, E.; Zaim, S.; Delen, D. Assessing the supply chain performance: A causal analysis. Ann. Oper. Res. 2020 , 287, 37–60. [Google Scholar] [CrossRef] Bento, G.d.S.; Tontini, G. Developing an instrument to measure lean manufacturing maturity and its relationship with operational performance. Total Qual Manag. Bus. Excel. 2018 , 29, 977–995. [Google Scholar] [CrossRef] Turkulainen, V.; Ketokivi, M. Cross-functional integration and performance: What are the real benefits? Int. J. Oper. Prod. Manag. 2012 , 32, 447–467. [Google Scholar] [CrossRef] Caridi, M.; Pero, M.; Sianesi, A. Linking product modularity and innovativeness to supply chain management in the Italian furniture industry. Int. J. Prod. Econ. 2012 , 136, 207–217. [Google Scholar] [CrossRef] Gomes, J.F.; de Weerd-Nederhof, P.C.; Pearson, A.W.; Cunha, M. Is more always better? An exploration of the differential effects of functional integration on performance in new product development. Technovation 2003 , 23, 185–191. [Google Scholar] [CrossRef] Kong, T.; Feng, T.; Huang, Y.; Cai, J. How to convert green supply chain integration efforts into green innovation: A perspective of knowledge-based view. Sustain. Dev. 2020 , 28, 1106–1121. [Google Scholar] [CrossRef] Liu, Z. Identifying the antecedents of internal integration in improving green product innovation. Int. J. Serv. Econ. Manag. 2020 , 11, 256–273. [Google Scholar] [CrossRef] Koufteros, X.; Vonderembse, M.; Jayaram, J. Internal and external integration for product development: The contingency effects of uncertainty, equivocality, and platform strategy. Decis. Sci. 2005 , 36, 97–133. [Google Scholar] [CrossRef] Purnama, C.; Wardana, L.W.; Rahmah, Y.; Fatmah, D.; Rahmah, M. The Impact of External Integration and Internal Integration to Product Innovation and Competitive Advantage on Small and Medium Enterprises (SMEs). Int. J. Innov. Econ. Dev. 2020 , 6, 82–95. [Google Scholar] Wong, C.W.; Wong, C.Y.; Boon-Itt, S. The combined effects of internal and external supply chain integration on product innovation. Int. J. Prod. Econ. 2013 , 146, 566–574. [Google Scholar] [CrossRef] Lii, P.; Kuo, F.-I. Innovation-oriented supply chain integration for combined competitiveness and firm performance. Int. J. Prod. Econ. 2016 , 174, 142–155. [Google Scholar] [CrossRef] He, Y.; Lai, K.K.; Sun, H.; Chen, Y. The impact of supplier integration on customer integration and new product performance: The mediating role of manufacturing flexibility under trust theory. Int. J. Prod. Econ. 2014 , 147, 260–270. [Google Scholar] [CrossRef] Xu, Q.; Hu, Q.; Chin, T.; Chen, C.; Shi, Y.; Xu, J. How supply chain integration affects innovation in a digital age: Moderating effects of sustainable policy. Sustainability 2019 , 11, 5460. [Google Scholar] [CrossRef] Aloini, D.; Martini, A. Exploring the exploratory search for innovation: A structural equation modelling test for practices and performance. Int. J. Technol. Manag. 2013 , 61, 23–46. [Google Scholar] [CrossRef] Khair, M.; Zaid, A.; Al-Hyari, K. The Effect of Supply Chain Integration on New Product Performance: The Mediating Role of Product Innovation Capability. Jordan J. Bus. Admin. 2020 , 16, 1. [Google Scholar] Ruzo-Sanmartín, E.; Abousamra, A.A.; Otero-Neira, C.; Svensson, G. The impact of the relationship commitment and customer integration on supply chain performance. J. Bus. Ind. Mark. 2023 , 38, 943–957. [Google Scholar] [CrossRef] Perols, J.; Zimmermann, C.; Kortmann, S. On the relationship between supplier integration and time-to-market. J. Oper. Manag. 2013 , 31, 153–167. [Google Scholar] [CrossRef] Beamon, B.M. Measuring supply chain performance. Int. J. Oper. Prod. Manag. 1999 , 19, 275–292. [Google Scholar] [CrossRef] Van Hoek, R.I. “Measuring the unmeasurable”—Measuring and improving performance in the supply chain. Supply Chain Manag. Int. J. 1998 , 3, 187–192. [Google Scholar] [CrossRef] Gimenez, C.; Ventura, E. Logistics-production, logistics-marketing and external integration: Their impact on performance. Int. J. Oper. Prod. Manag. 2005 , 25, 20–38. [Google Scholar] [CrossRef] Simbarashe, M.; Charumbira, J.; Vhanda, R.; Shava, G.; Ndlovu, M.; Shumba, F. The Effect of Supply Chain Integration on the Operational Performance. Indiana J. Humanit. Soc. Sci. 2022 , 3, 86–94. [Google Scholar] Masa’deh R e Muheisen, I.; Obeidat, B.; Bany Mohammad, A. The Impact of Supply Chain Integration on Operational Performance: An Empirical Study. Sustainability 2022 , 14, 16634. [Google Scholar] [CrossRef] Chen, C.-H.V.; Chen, Y.-C. Influence of intellectual capital and integration on operational performance: Big data analytical capability perspectives. Chin. Manag. Stud. 2022 , 16, 551–570. [Google Scholar] [CrossRef] Lai, K.H.; Wong, C.W.; Cheng, T. Bundling digitized logistics activities and its performance implications. Ind. Mark. Manag. 2010 , 39, 273–286. [Google Scholar] [CrossRef] Chen, M.; Liu, H.; Wei, S.; Gu, J. Top managers’ managerial ties, supply chain integration, and firm performance in China: A social capital perspective. Ind. Mark. Manag. 2018 , 74, 205–214. [Google Scholar] [CrossRef] Petersen, K.J.; Handfield, R.B.; Ragatz, G.L. Supplier integration into new product development: Coordinating product, process and supply chain design. J. Oper. Manag. 2005 , 23, 371–388. [Google Scholar] [CrossRef] Koufteros, X.A.; Cheng, T.E.; Lai, K.-H. “Black-box” and “gray-box” supplier integration in product development: Antecedents, consequences and the moderating role of firm size. J. Oper. Manag. 2007 , 25, 847–870. [Google Scholar] [CrossRef] Amoako, T.; Huai Sheng, Z.; Dogbe, C.S.K.; Pomegbe, W.W.K. Effect of internal integration on SMEs’ performance: The role of external integration and ICT. Int. J. Product. Perform. Manag. 2022 , 71, 643–665. [Google Scholar] [CrossRef] Ferreira, J.; Coelho, A.; Moutinho, L. Dynamic capabilities, creativity and innovation capability and their impact on competitive advantage and firm performance: The moderating role of entrepreneurial orientation. Technovation 2020 , 92, 102061. [Google Scholar] [CrossRef] Rumanti, A.A.; Rizana, A.F.; Septiningrum, L.; Reynaldo, R.; Isnaini, M.M.r. Innovation Capability and Open Innovation for Small and Medium Enterprises (SMEs) Performance: Response in Dealing with the COVID-19 Pandemic. Sustainability 2022 , 14, 5874. [Google Scholar] [CrossRef] Yeung, A.H.; Lo, V.H.; Yeung, A.C.; Cheng, T.E. Specific customer knowledge and operational performance in apparel manufacturing. Int. J. Prod. Econ. 2008 , 114, 520–533. [Google Scholar] [CrossRef] Dhir, S.; Ongsakul, V.; Ahmed, Z.U.; Rajan, R. Integration of knowledge and enhancing competitiveness: A case of acquisition of Zain by Bharti Airtel. J. Bus. Res. 2020 , 119, 674–684. [Google Scholar] [CrossRef] Christa, U.; Kristinae, V. The effect of product innovation on business performance during COVID 19 pandemic. Uncertain Supply Chain Manag. 2021 , 9, 151–158. [Google Scholar] [CrossRef] Alam, S.; Zhang, J.; Shehzad, M.U. The mechanism of knowledge management processes toward knowledge workers operational performance under green technology implementation: An empirical analysis. Kybernetes, 2022; ahead of print. [Google Scholar] Iftikhar, A.; Ali, I.; Shah, A. The Impact of Big Data Analytics on Firm’s Operational Performance: Mediating Role of Knowledge Management Process. In Proceedings of the 2nd Asia Pacific International Conference on Industrial Engineering and Operations Management, Surakarta, Indonesia, 14–16 September 2021. [Google Scholar] Alamro, A. The Impact of New Product Flexibility (NPF) on Operational Performance: Evidence from Jordanian Manufacturing Companies; Qatar University: Doha, Qatar, 2014; pp. 1–8. [Google Scholar] Helm, R.; Krinner, S.; Endres, H. Exploring the role of product development capability for transforming marketing intelligence into firm performance. J. Bus. Bus. Mark. 2020 , 27, 19–40. [Google Scholar] [CrossRef] Syed, T.A.; Blome, C.; Papadopoulos, T. Impact of IT ambidexterity on new product development speed: Theory and empirical evidence. Decis. Sci. 2020 , 51, 655–690. [Google Scholar] [CrossRef] Kaufmann, L.; Gaeckler, J. A structured review of partial least squares in supply chain management research. J. Purch. Supply Manag. 2015 , 21, 259–272. [Google Scholar] [CrossRef] Henseler, J.; Ringle, C.M.; Sarstedt, M. A new criterion for assessing discriminant validity in variance-based structural equation modeling. J. Acad. Mark. Sci. 2015 , 43, 115–135. [Google Scholar] [CrossRef] Kortmann, S.; Gelhard, C.; Zimmermann, C.; Piller, F.T. Linking strategic flexibility and operational efficiency: The mediating role of ambidextrous operational capabilities. J. Oper. Manag. 2014 , 32, 475–490. [Google Scholar] [CrossRef] Podsakoff, P.M.; MacKenzie, S.B.; Lee, J.-Y.; Podsakoff, N.P. Common method biases in behavioral research: A critical review of the literature and recommended remedies. J. Appl. Psychol. 2003 , 88, 879. [Google Scholar] [CrossRef] Shou, Y.; Li, Y.; Park, Y.; Kang, M. Supply chain integration and operational performance: The contingency effects of production systems. J. Purch. Supply Manag. 2018 , 24, 352–360. [Google Scholar] [CrossRef] Lance, C.E.; Butts, M.M.; Michels, L.C. The sources of four commonly reported cutoff criteria: What did they really say? Org. Res. Methods 2006 , 9, 202–220. [Google Scholar] [CrossRef] Fornell, C.; Larcker, D.F. Evaluating structural equation models with unobservable variables and measurement error. J. Mark. Res. 1981 , 18, 39–50. [Google Scholar] [CrossRef] Arshad Ali, A.; Mahmood, A.; Ikram, A.; Ahmad, A. Configuring the drivers and carriers of process innovation in manufacturing organizations. J. Open Innov. Technol. Market Complex. 2020 , 6, 154. [Google Scholar] [CrossRef] Zhao, X.; Lynch, J.G., Jr.; Chen, Q. Reconsidering Baron and Kenny: Myths and truths about mediation analysis. J. Consum. Res. 2010 , 37, 197–206. [Google Scholar] [CrossRef] Figure 1. Research Model. Figure 1. Research Model. Figure 2. Confirmatory factor analysis for measurement model. Figure 2. Confirmatory factor analysis for measurement model. Figure 3. The structural model. Figure 3. The structural model. Table 1. Sample demographics (N = 129). Table 1. Sample demographics (N = 129). N Percentage % Firm age ≤10 69 53.49 11–15 46 35.66 ≥16 14 10.85 Firm size ≤100 48 37.21 101–200 37 28.68 201–300 18 13.95 ≥301 26 20.16 Industry Food and beverages 15 11.63 Pharmaceutical and medical 43 33.33 Petroleum and chemical 27 20.93 Machinery and equipment 44 34.11 Total 129 100 Table 2. Validity Analysis. Table 2. Validity Analysis. CR AVE OP SI II CI MK PD OP 0.944 0.678 (0.824) SI 0.963 0.838 0.680 (0.916) II 0.929 0.767 0.522 0.505 (0.876) CI 0.934 0.780 0.547 0.626 0.721 (0.883) MK 0.915 0.782 0.528 0.481 0.557 0.557 (0.885) PD 0.917 0.848 0.616 0.660 0.617 0.727 0.376 (0.921) Table 3. Hypotheses testing results. Table 3. Hypotheses testing results. Relationships Estimate p-Value Results H1: Internal integration → Market knowledge 0.306 p < 0.001 Accepted H2: Internal integration → Product development 0.154 p = 0.006 Accepted H3: Customer integration → Market knowledge 0.209 p = 0.008 Accepted H4: Customer integration → Product development 0.413 p < 0.001 Accepted H5: Supplier integration → Market knowledge 0.194 p = 0.001 Accepted H6: Supplier integration → Product development 0.324 p < 0.001 Accepted H7: Internal integration → Operational performance 0.091 p = 0.133 Rejected H8: Customer integration → Operational performance −0.106 p = 0.139 Rejected H9: Supplier integration → Operational performance 0.398 p < 0.001 Accepted H10: Market knowledge → Operational performance 0.235 p < 0.001 Accepted H11: Product development → Operational performance 0.281 p < 0.001 Accepted Table 4. The results for mediating effects. Table 4. The results for mediating effects. Path Direct Effect Indirect Effect Mediation Type H12: II → MK → OP 0.091 (0.133) 0.072 (0.000) Full Mediation H13: CI → MK → OP −0.106 (0.139) 0.049 (0.004) Full Mediation H14: SI → MK → OP 0.398 (<0.001) 0.045 (0.001) Partial Mediation H15: II → PD → OP 0.091 (0.133) 0.043 (0.013) Full Mediation H16: CI → PD → OP −0.106 (0.139) 0.116 (0.001) Full Mediation H17: SI → PD → OP 0.398 (<0.001) 0.091 (0.001) Partial Mediation Disclaimer/Publisher’s Note: The statements, opinions and data contained in all publications are solely those of the individual author(s) and contributor(s) and not of MDPI and/or the editor(s). MDPI and/or the editor(s) disclaim responsibility for any injury to people or property resulting from any ideas, methods, instructions or products referred to in the content. © 2023 by the authors. Licensee MDPI, Basel, Switzerland. This article is an open access article distributed under the terms and conditions of the Creative Commons Attribution (CC BY) license (https://creativecommons.org/licenses/by/4.0/).