How Specialized’s New Innovation Lab Builds Bikes 10 Times Faster Than Before | Inc.com
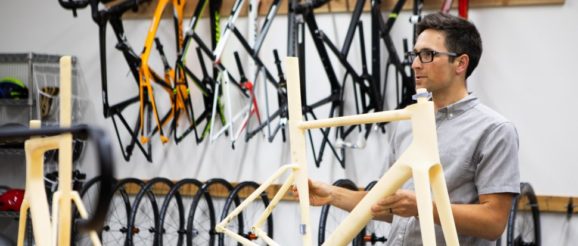
Before opening the lab, the company would have to design a component, send it to one of its manufacturing facilities overseas, and wait to receive the new version. Now designers can use the lab’s 3-D printers to quickly create everything from small parts to full-scale models. A process that used to require three months takes just one week.
“Now we can take risks,” Yu says, “and try crazy, crazy geometries because we have the time to be able to go backwards if necessary.” Those design changes might not look all that radical to the untrained eye–maybe increasing the angle of the head tube by a half-degree, or shortening the chainstay by fractions of an inch–but they can have a big impact on the bike’s performance.
Once a prototype is ready, the fun part happens: testing it. To simulate high-stress conditions, Specialized previously had to choose from only three adequately equipped wind tunnel facilities in the U.S. The company’s preferred one was in North Carolina, which required reserving blocks of time months in advance and then flying a team of engineers cross country. Sometimes, Yu says, Specialized would travel back and forth two or three times to test a single model. Now, in the wind tunnel in Specialized’s lab, air blasts the bike and its rider at up to 70 miles per hour while engineers collect performance data.
Yu says the new system has given Specialized the ability to create bikes it never could have before. One of the company’s newest models, the Roubaix, combines an ultra-compliant suspension system, innovative materials engineering, and an aerodynamic frame design in such a way that would have been too complex several years ago. “We might have been able to make a bike that’s as compliant or as light or as fast,” Yu says. “But without this facility, I just don’t think the combination would have been possible with any amount of time.”