HyPerforma Single Use Bioreactor: Innovation – BioProcess InternationalBioProcess International
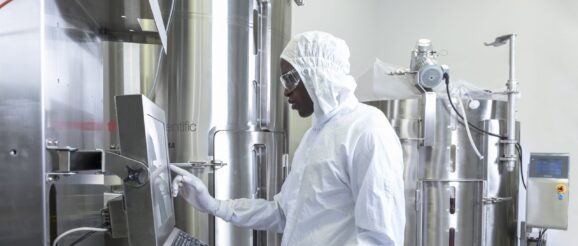
The biotherapeutic market has actually been rapidly adopting single-use technologies to reduce danger and improve functional effectiveness. For more than twenty years, Thermo Fisher Scientific has pioneered single-use innovations for this industry. Our products have been proven to be robust and scalable from lab scale-up to existing great production practice (cGMP) production applications, consisting of single-use bioprocessing equipment, versatile containment, and stiff containment product portfolios.
Our webinars will explore data, innovative products, and novel methods including single-use services for the bioprocessing market.
![]() |
< img class=" alignleft wp-image-72899" src=" https://bioprocessintl.com/wp-content/uploads/2020/09/thermo-ate-series-madsen-headshot-232x300.jpg" alt="" width=" 100 "srcset=" https://bioprocessintl.com/wp-content/uploads/2020/09/thermo-ate-series-madsen-headshot-232x300.jpg 232w,https://bioprocessintl.com/wp-content/uploads/2020/09/thermo-ate-series-madsen-headshot-791×1024.jpg 791w, https://bioprocessintl.com/wp-content/uploads/2020/09/thermo-ate-series-madsen-headshot-768×994.jpg 768w, https://bioprocessintl.com/wp-content/uploads/2020/09/thermo-ate-series-madsen-headshot-1187×1536.jpg 1187w, https://bioprocessintl.com/wp-content/uploads/2020/09/thermo-ate-series-madsen-headshot-1583×2048.jpg 1583w, https://bioprocessintl.com/wp-content/uploads/2020/09/thermo-ate-series-madsen-headshot-124×161.jpg 124w, https://bioprocessintl.com/wp-content/uploads/2020/09/thermo-ate-series-madsen-headshot-245×317.jpg 245w, https://bioprocessintl.com/wp-content/uploads/2020/09/thermo-ate-series-madsen-headshot-350×453.jpg 350w, https://bioprocessintl.com/wp-content/uploads/2020/09/thermo-ate-series-madsen-headshot-scaled.jpg 1978w” sizes=”( max-width: 232px) 100vw, 232px” >” Application-Specific Enhancements to Thermo Scientific TM HyPerforma TM Single-Use Bioreactors,” with Ben Madsen< period id=" hs-cta-wrapper-d6e65477-95a9-4797-8a96-a8ddd89d681c" class=" hs-cta-wrapper" > " class=" hs-cta-wrapper" >< period id =" hs-cta-d6e65477-95a9-4797-8a96-a8ddd89d681c" class=" hs-cta-node hs-cta-d6e65477-95a9-4797-8a96-a8ddd89d681c" > hbspt.cta.load( 1724941, 'd 6e65477-95a9-4797-8a96-a8ddd89d681c', ); Â The quick growth of biotherapeutic manufacturing has actually created substantial need for workflow services including greater product yield, lower production costs, and accelerated advancement timelines. To deal with these demands, developers have moved far from â $ one-size-fits-allâ $ methods and are increasingly concentrated on options that attend to the specific needs of diverse bioproduction processes.Given this shift towards process-specific services, Thermo Fisher Scientific has presented a series of application-specific enhancements to the HyPerforma Single Use Bioreactor (SUB) product platform, each customized to the special requirements of perfusion, heightened fed-batch, and adherent cell cultures. This presentation describes the changes required to satisfy these particular culture demands and provides case studies for each, highlighting the results of the process-specific alterations.You will find out about:
|
![]() |
< img class=" alignleft size-full wp-image-73017" src= "https://bioprocessintl.com/wp-content/uploads/2020/09/thermo-ate-series-2.png" alt="" width=" 100" >" Aggressive Microbial Production from Shot Through Harvest in Single-Use Systems," with Dmitrij Bugajev and Jason D. Brown October 22, 2020 b3e144ab-7f45-48b6-827b-994e81d87867', );< span id=" hs-cta-wrapper-d6e65477-95a9-4797-8a96-a8ddd89d681c" class =" hs-cta-wrapper" > Single-use fermentors allow production centers to use single-use technologies instead of standard stainless-steel fermentor vessels, achieving comparable expression with rapidly growing high-density cultures. We will compare some arise from various procedures with yeast and bacteria before and after technology moved to single-use at our two facilities. We will offer you our feedback as previous end users of stainless-steel fermentors and now of single-use fermentors along with things to considerations that may help you make your shift smooth. We also will discuss single-use processing advantages and time-saving benefits to streamline closed-system production from inoculation through harvest and initial downstream processing.You will find out about:
|
![]() |
< img class=" alignleft wp-image-73019 size-full" src =" https://bioprocessintl.com/wp-content/uploads/2020/09/thermo-ate-series-3.png" alt="" width=" 100" srcset =" https://bioprocessintl.com/wp-content/uploads/2020/09/thermo-ate-series-3.png 100w, https://bioprocessintl.com/wp-content/uploads/2020/09/thermo-ate-series-3-77x300.png 77w, https://bioprocessintl.com/wp-content/uploads/2020/09/thermo-ate-series-3-81x317.png 81w" sizes="( max-width: 100px) 100vw, 100px" >" Bioprocess Choice and Economics: 5,000-L DynaDrive ™ Bioreactor Moving the Paradigm," with Jeff Johnson, Mark Thomas Smith, and Kevin Mullen November 12, 2020 Single-use innovations make it possible for a flexibility and modularity successfully unattainable with more standard stainless-steel technologies, particularly in upstream bioprocesses. Single-use bioreactors as much as 2,000 L are utilized largely in preclinical- and clinical-stage bioprocesses to take advantage of this versatility. As products reach business maturity, scales bigger than 2,000 L often end up being desirable to benefit from economies of scale. With the typical ceiling of single-use bioreactors at 2,000 L, this has typically meant transfer to stainless-steel systems.The intro of the Thermo Fisher Scientific HyPerforma ™ DynaDrive ™ 5,000-L bioreactor opens a new paradigm of operation in regards to volume, while supplying extraordinary ergonomics and flexibility. In tandem with Thermo Fisher, Jeff Johnson (previous head of Merck Single-Use Network) has examined the functional and economic ramifications of this new reactor system and shares his perspective of how the biopharma market might change with the intro of the DynaDrive system. Kevin Mullen (Senior Citizen Product Manager) introduces the DynaDrive systems, and Mark Thomas Smith (Personnel R&D Engineer) explores how this technology can fulfill the demands of magnifying bioprocesses.You will find out about:
|
Transcripts of these presentations will be available in an upcoming BPI Unique Report.