Innovation Meets Operations with Digital Trace™ Manufacturing – Nexteer
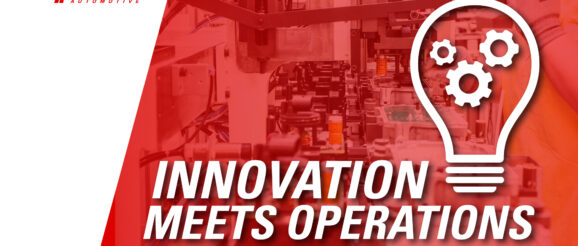
Innovation Meets Operations with Digital Trace™ Manufacturing
A few years ago, Nexteer’s Manufacturing team began a journey of developing a manufacturing system that mirrored the innovation and technology leadership we focused into our products. To put it simply, we wanted to be relentless innovators not only in “what we do”, but also in “how we do it”. We knew that taking this approach would increase the value, responsiveness and quality that we could offer to our customers.
Consequently, Digital Trace™ Manufacturing (DTM) was born and has made a significant impact on our global manufacturing operations. DTM launched in 2018 as the automotive industry’s most advanced, holistic, integrative approach to design and manufacturing systems. This award-winning system uses the latest technologies and data analytics within one common, global architecture.
DTM is unique from what is commonly called “digital thread” or “manufacturing automation” because of the vastness of what DTM covers. Because of the scope and the level of integration, DTM represents an ongoing journey where we will constantly update, improve and expand our abilities.
Connecting the Dots: How It Works
DTM helps deliver high-quality product performance while boosting cost-competitiveness and global capacity optimization – enabling us to be more agile and responsive both internally and to our customers. It does this by using a connect-the-dots approach, in which the thousands of data-producing dots around the world are standardized and talk to one another.
Each dot represents a machine, process, database, document, workplace robot and so on. When the dots are connected, the result is one common, global architecture. DTM allows us to deliver a dynamic, comprehensive view of our manufacturing operations in real time. DTM also allows us to quickly replicate any improvement in design or production made at one location at other locations globally.
Making a Real-World Impact: Technology & Process Examples
As part of DTM, we’ve introduced several cutting-edge technologies and processes into our manufacturing operations. This helps quality engineers proactively confirm product quality early in the process – potentially eliminating the need for costly end-of-line testing. Some examples include:
For our global teams, communicating is easier with DTM. The system streamlines and enhances manufacturing giving real-time visibility into all global manufacturing activities. Additionally, teams are able to predict future manufacturing issues and proactively solve them before challenges arise. The system fully optimizes all capacities from factory-floor logistics to inventory and planning. The data-driven insights help employees do their jobs more efficiently.
As an example, our virtual factory portal called 1Link connects people and data on the factory floor quickly and easily. 1Link allows simple, mobile access to the plant documents that employees need to perform their jobs on the plant floor (such as instructions, control plans, prints, etc.). It also allows employees to view the latest released documents, training status of operators and previous revisions.
The Value of a Holistic Approach to Integrating Manufacturing & Design
When we began this journey, there was no blueprint, no roadmap for us to follow – we had to create our own. We embarked on this innovative process to create a digital manufacturing solution to support global manufacturing engineering processes, Manufacturing 4.0 initiatives and manufacturing operations document control and accessibility.
Ultimately, these new technologies are optimizing manufacturing processes, enhancing quality and improving product performance. Our development and success with DTM are testaments to the innovative, solution-oriented spirit that runs through our entire OneNexteer team globally.
DTM allows innovation to come to life throughout the design and manufacturing process – enabling ideas, advancements and improvements to be shared seamlessly.
Nexteer is steering the future of intuitive motion control – not only in what we do, but how we do it – through collaboration, innovation and industry leadership.