ITMA 2023 – Where the Worlds of Textiles, Garment and Innovation Converge – Knitting Views
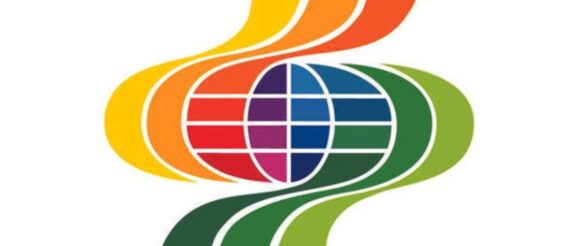
SHIMA SEIKI to demonstrate smart, speedy and sustainable production
Leading flat knitting technology firm SHIMA SEIKI MFG., LTD. of Wakayama, Japan, will presenting the latest technology to the textile industry at booth No.Hall 4, Stand D209. Due to exhibition rules, there was a time when visiting ITMA meant you could expect to see brand-new machines exhibited for the first time. Since the 1990’s however, that regulation has become relaxed, and more recently, the kind of excitement expected from manufacturers showing first-time technology seemed like a thing of the past.
Meanwhile, SHIMA SEIKI has consistently maintained an impressive showing at ITMA, showing something new and exciting at every edition under our guiding philosophy: “Ever Onward.” For 2023, this tradition not only remains intact, but recalls ITMAs of the past through a brand-new lineup mostly consisting of new machines and next generation prototypes.
The Next-Generation group of machines is represented by the letter ‘R,’ first used in the SWG-XR WHOLEGARMENT® knitting machine launched last year in time for SHIMA SEIKI’s 60th Anniversary event. The SWG-XR name is based on the original SWG-X four-needlebed WHOLEGARMENT® knitting machine which debuted at the Milan ITMA in 1995. As ITMA returns to Milan, SWG-XR refers to its origin as a pioneering invention that launched a new genre of seam-free knits produced in one entire piece. At the same time it represents a renewal of SHIMA SEIKI’s commitment to its customers, the industry and the environment, as all aspects of the machine were reevaluated in terms of its purpose, the way it is manufactured, how it is used and how it impacts the environment. The same renewal has been applied to the rest of the company’s product lineup, and it is this renewal that becomes the core of SHIMA SEIKI’s exhibition concept for ITMA 2023: “Reborn.”
Of the 9 knitting machines SHIMA SEIKI is exhibiting at its 600 sq. meter booth located at Hall 4, Stand D209, 8 machines will be part of the NextGeneration lineup, ranging from WHOLEGARMENT® knitting machines and computerized flat knitting machines to glove knitting machines. More than 300 items will be on display as proposals for knitted applications in various fields ranging from fashion, sports, shoes, bags and accessories to medical, safety, automotive, aeronautical and other wearable and industrial textile applications.
In addition to machine technology, SHIMA SEIKI’s SDS-ONE APEX series computer graphic design system and software will be shown with their latest software upgrades that feature significant improvements in knit programming, 3D functions and speed. Demonstrations will be available for a comprehensive fashion tech solutions package based on realistic virtual sampling and supported by various digital solutions and web services.
With a comprehensive display of its latest products and services, SHIMA SEIKI technology at ITMA 2023 will demonstrate smart, speedy and sustainable production that further secures its leading role as flat knitting solutions provider.
Latest developments and solutions from Karl Mayer
Our times are stormy, but with the right changes, the headwind becomes a tailwind. “MASTER THE CHANGE – profitable, flexible, and sustainable” is our motto for a successful future. Under this motto we like to present our latest developments and solutions to our customers and all visitors of our booth at ITMA 2023 in Milan.
In light of the upheavals in the wake of current events, we spoke with our customers from all sectors and branches about their concerns, priorities and goals. During the discussions, five questions emerged as strategically essential and urgent. At ITMA 2023 in Milan, we will be presenting solutions and innovations in response to the following customer questions.
Business Unit Warp Knitting
Tricot machine with electronic pattern drive for fast and easy pattern changes to react to the changing market demands and smaller order quantities. This tricot machine has a focus on energy management. Environmental protection and resource saving are further important success factors. Double bar raschel machine that uses perfected jacquard technology to implement spacer designs with an unprecedented play of colors. The colorful 3D warp knitted fabrics offer particular potential for further applications in the apparel, furniture and automotive sectors.
Business Unit Warp Preparation
Next generation of full automatic sample warping for more flexibility and higher productivity, equipped with the latest digital solutions. Further benefits are short setup time that increases the flexibility for pattern warps.The denim industry is benefiting from an innovation that makes indigo dyeing twice cleaner and at the same time three times more efficient than conventional processes. This is based on the use of nitrogen (NOX) technology to control the chemical dyeing process.
Business Unit Technical Textiles
Latest warp knitting machine with magazine weft insertion for the production of a wide range of applications in the field of infrastructure, building and construction. Look forward to a machine that offers more efficiency by reducing weft yarn waste at high working width and speed. A new electronic function ensures pattern changes without mechanical handling.A warp knitted net made of biobased materials for vertical greening shows how technical textiles can be used to master our environmental challenges in new fields of application.
Business Unit Stoll
In the flat knitting sector, we will be presenting our wide range ADF machines. With the various STOLL technologies such as knit and wear®, weave-in® or intarsia, the ADF machines are true all-rounders. According to the motto “all articles on one machine”, various garments will be created on one and the same ADF model in front of the eyes of ITMA visitors in Milan.
Next to this you can look forward to machine models with more added values without additional process steps. This is made possible by a special robot function for STOLL knitting machines of the knitelligence® generation. At ITMA we will demonstrate how functional elements can be incorporated directly into the textile during knitting. STOLL’s fully fashion production also promises multiple benefits: Fewer additional fabrication steps mean less waste and more speed in the implementation of new products.
Digital Solutions by KM.ON
Less textile waste and material consumption is made possible by designsoftware from KM.ON for flat knitted textiles. This is made possible by exporting the design to any 3D software to create realistic 3D renderings, reducing the need to create physical patterns and swatches. Brands and designers are therefore less dependent on manufacturers in the design development process. They get immediate visual feedback on how the design will look. This also enables faster response to changing trends and shortens time to market.
One example, how to be profitable with increasing cost pressure, is KM.ON’s Digital Production Management System for the digitization of processes, which, among other things, creates more transparency on the shop floor for the analysis and optimization of production with production-specific key figures available on a dashboard.
New Coarse Gauge Intarsia Machine from Steiger
Swiss flat knitting machine manufacturer Steiger has launched a brand-new Antares 2.185 flat knitting machine, that will be shown for the first time at ITMA in Milan in June. The unique machine with 24 yarn guides to knit coarse gauge intarsia sweaters, will be on show in Hall 4 stand D101/D101a.
The Antares 2.185 is a coarse gauge (3 needles per inch) machine to knit panels, fully fashioned, shaped garments, Jacquard and stitch structure combinations. It has the characteristic Steiger open carriage with two knitting systems and full three-way-technique, with variable intelligent stroke knitting on a 185 cm needlebed.
The Antares 2.185 has individual electronic needle selection, special Steiger upper take-down and takedown comb, direct yarn feeding on an open carriage with 24 independent motorised yarn-carriers with, 24 cutters and clamps on the needlebed. The machine is available in gauge 3.
Antares 2.185 is a single head compact machine, without cam carriage bridge, with direct yarn feeding from the top and two system cam boxes, each with integrated bidirectional transfer. It has a working width of 185 cm (73?).
Electronic needle selection permits unlimited patterning possibilities due to three-way-technique and integrated function for split-stitches and shaping by stitch transfer and press-off method.
Stitch quality is controlled electronically without limits, with the possibility to modify at any time. The machine can be fitted with up to 24 motorised yarn-carriers with direct feeding, independent to carriage movement. Yarn carriers are dropped off automatically at the edge of the design or the selvedge.
Take down is programmable and is active at 25mm from loop formation. A programmable take-down comb is also fitted. Drive is by brushless motor, giving infinitely variable stroke and programmable knitting speed up to 1.30 m/s. Stop motions cover yarn breakage, knots, shock, over-heating of motors, fabric press-off etc. Racking is selective over +-60 mm, with the possibility of correction. The Antares 2.185 is programmed via Steiger’s Model software on PC.
Yonthin to display new Electronic Jacquard Terry Machine
At ITMA Milan 2023, Yonthin is taking a new approach and inviting visitors to witness firsthand the remarkable advantages Yonthin users experience with its latest technologies. Yonthin will present the latest Yonthin Electronic Jacquard Terry Machine to the textile industry at booth C202, Hall 2.
Yonthin Textiles Group was established in 1989 and starts to develop the multiple head embroidery machine and knitting machine in China. The Group is a national high technology company with ISO 9001, ISO14001, CE approval. Yonthin Group already provides their machines to over 70 countries all over the world to their customer and built a closer relationship with their customer by good and high efficient service. What Yonthin Group insist is innovation and services. Yonthin always value the customer need and offer world first class products and services to their customer. Yonthin means “Honest Forever” in Chinese, which is Yonthin believe and Yonthin promise to their customers.
Yonthin Electronic Jacquard Terry Machine
Yonthin Electronic Jacquard Terry Machine utilizes computer control to select sinking according to pattern requirements for the production of jacquard terry cloth fabric. The pattern is unlimited, and the operation is simple and easy to learn. The computer system and needle selector have a long service life and high durability, combined with the stable rotation of the high-precision machine frame from Yonthin Company.
Making this model highly accurate and with a low failure rate. The produced jacquard terry cloth fabric has a soft touch and strong three- dimensional effect. This machine is widely used in the production of decoration, sweatshirts, children’s clothing, fashion, and other fields. The company is represented in India by The Empire Textiles, Tirupur.
Mayer & Cie. to focus on longer life and greater efficiency at ITMA
The textile machinery manufacturer Mayer & Cie. will be there for the first time with both of its business units: circular knitting machines and braiding machines. Along with the circular knitting machines Mayer & Cie. is exhibiting a braiding machine at its stand E101 in Hall 2. The company focuses on similar features in both areas: sound machines fitted out with solutions that make braiders and circular knitting machines more efficient, longer-lasting and thereby more valuable. The solutions range from upgrade kits for individual machines and innovations to reduce waste zo digital solutions that improve the customer experience.
A tried and trusted choice: circular knitting machines
Mayer & Cie. will be exhibiting three circular knitting machines at ITMA: the revised OVJA 2.4 EM and Relanit 3.2 HS and the new three-thread fleece SF4 3.2 III. All three serve classical uses and, except for the new SF4-3.2 III, are established in the market.
The OVJA 2.4 EM knits double jacquard with electronic individual needle selection in the cylinder and double fabric with weft thread. It is currently the most productive machine in its class. Spacer fabric has now been added to its portfolio.
Machine number 2 is a byword for every knitter. For ITMA 2023 Mayer & Cie. has fitted out the existing Relanit 3.2 HS with improved yarn guides. It has a needle with an optimised hook and tongue shape and a pre-determined breaking point to improve safety at higher output. The new sinker is another feature of the Relanit 3.2 HS. It makes the machine run smoother and reduces wear and tear. “Many knitting mills all over the world already swear by Relanit machines,” says Axel Brünner, Head of product management at Mayer & Cie. “For them and new customers we are working on further improvements to our bestsellers.”
With the third machine on show Mayer & Cie. is addressing a major trend in the clothing industry. The SF4-3.2 III for three-thread fleece, especially for leisurewear, both in pure cotton and in blends, is in great demand. As Axel Brünner explains, “In this new machine we combine our tried and trusted MBF 3.2 and components of our MFC 3.2 that have proved advantageous in the Chinese market.”
Brisk braiding: Extra-speed machine for textile braid
The MR-15/18 C/Single Deck braider on show at ITMA is designed for textile braiding. It comes with the new capstan wheel pull-off that is especially suitable for smaller-diameter hoses with textile braiding. The SpeedBooster upgrade kit delivers more speed and up to ten percent more output.
Smart upgrades for long, efficient machine life
Longer, faster and with even greater precision, upgrade kits enable customers to benefit from technical progress at Mayer & Cie. The upgrade portfolio ranges from speed boosters to special plaiting and laying equipment. Another newcomer is spare parts with upgrade kits customised for individual machines. They deliver additional production and planning safety.
Upgrade kits – like all known spare parts – are available from the web shop. Along with an easy-to-use search function the web shop provides smart additional functions and includes the new loyalty programmemy.loyaltyclub with attractive discounts.
Smart functions: knitlink, knithawk and Control 5.0
Fewer faults and less waste is the simple truth. The new knithawk recognises and identifies knitting faults fast during the knitting process, switching the machine off automatically. That makes production significantly more sustainable and efficient.
knitlink is the platform that links the manufacturer, representatives and customers. It is IIoT-based and the central location for all machine data that every customer can use to record and evaluate the performance of his machines. It is also a repository for documents such as operating instructions, manuals and spare part recommendations. In addition, knitlink provides every customer with remote access to the circular knitting machine.
knitlink incorporates the web shop, which is digitally linked to the new-generation Control 5.0. Circular knitting machines with Control 5.0 are IoT-enabled and can inter alia be operated from mobile devices, so the knitter no longer needs to be physically at the controls.
VENTURA ITM to launch new technology in circular knitting
VENTURA ITM was born from an idea by Diego Ventura, with the aim of bringing to the market a cutting-edge and technologically innovative Made in Italy product. Involving Rena to Pilotelli, who in over 60 years of career has revolutionized the world of knitwear, and who with enormous product quality and innovative ideas has become the world leader in the sector over the years, gave birth to VENTURA Italian Textile Machinery.
Through this joint venture, with the integration of the historic company’s team and centralizing the study, design and production in Italy, and from the development of the famous JVCE-3 they have created the brand new SJM 3.5 OW.
The company’s latest development will be showcased at ITMA 2023 Expo in Milan, Italy from 8th – 14th June in Hall H2, Booth C204, once again pushing the boundaries of what’s possible in the world of textile machinery. The company has recently appointed RI Texsolutions Pvt Ltd as agent for Indian market.
SJM 3.5 OW – Single- Jersey Machine Open Width Frame
From the development of the famous JVCE-3, this innovative machine has unique set-ups and innovations, which allow the development of fabrics quickly and efficiently.
Equipment:
• 3 feeder cylinder cam boxes
• 4 needle tracks, 3 equipped with needles and cams for piquet and 2 yarn fleece
• Sector cap for a quick sinkers change
• Navigator plus touch screen
• Tube creel preparation (without creel elements)
• Groz Beckert needles
• Kern Liebers sinkers
• 3 holes zirconium yarn carrier
• Central stitch length adjustment
• Click-clack system for yarn carriers positioning
• Drive tower of yarn positioned outside for easy handling
• Venticleaner on top and inside cylinder with 2 fan units
• Electronic needle detectors
• Speedfactor (max) 1,080
Frame:
• New take down open width easy
convertible in tubular knitting
• Fabric width up to 2300 mm
• Fabric roll diameter up to 380 mm
• Cadratex fabric spreader
• Ceramic cutting blade
Advantages at a glance:
• Basic model for high production of single knit fabrics with 3 feeds for inch and speedfactor of 1,080
• Large pattern range with up to 4 needle tracks in cylinder cam and a wide gauge spectrum (up to 40)
• New open width takedown system for an even and constant fabric tension
• Modern and innovative control unit with touch screen for easy and user friendly operation
• Reliable and high quality elastane plating
Fine Gauge Electronic Jacquards Knitting technology by Monarch
Monarch Knitting Machinery (UK) Ltd. will be unveiling four of its latest circular knitting machines at the forthcoming ITMA 2023 textile machinery exhibition in Milan. In Hall 4, Stand E105-E106, the Leicester, UK based company will be focusing on its latest fine gauge electronic technology in both single and double-knit Jacquards – high production mattress ticking and single jersey raceway machinery.
Monarch will also be introducing a new design simulation software that will take fabric digitalisation to the next level. The company will also be showing its latest development in E-Needle technology and MMS (Monarch Monitoring System) for Industry 4.0.
OD7-M2XC-A3.2RE: On show will be a 30-inch diameter OD7-M2XC-A3.2RE in 28 gauge. The 96-feed single jersey raceway machine on open-width frame is aimed at high production. The machine features the latest E-Needle technology from Fukuhara reducing energy consumption and improved needle life.
OD7-M-SEC7BS: Also, on show will be a 30-inch OD7-M-SEC7BS in 40 gauge. The 72-feed single jersey electronic jacquard model is now available with true 3-way selection at all feeds on the cylinder. A combination of the compact SS actuator and newly developed machine encoder has given the possibility to produce a range of new super fine fabrics suitable for sportwear, mesh and lingerie.
M-LEC7BS: Monarch will also exhibit a 30-inch M-LEC7BS in 36 gauge. The 72- feed double jersey electronic jacquard model has true 3-way selection on the cylinder. RDS (Rotary Drop Cam System) on the dial is standard on the machine allowing ultra-fast pattern changes to be made without removing cam box sections or elements. The machine is capable of knitting fabrics in both rib or interlock gating for sportswear, outerwear, and lingerie fabrics.
M-LEC7KSH: A 20-gauge MLEC7KSH in 38 ich diameter, completes the new machine line-up. The 84-feed double jersey electronic jacquard is a high production mattress ticking machine. The machine features a brand-new needle selection system that has significantly reduced weight and height of the knitting head. The main benefits will be further energy saving, improved machine handling and increased productivity.
Digitalisation: Monarch will also be showing its latest MMS developments in machine monitoring with its partner BMS (Belgium Monitoring Systems). MMS not only monitors knitting machines but also all manufacturing and logistical activities within the knitting factory.
Monarch will be showing a new MKS development concept for fabric simulation which will allow designers to develop fabrics digitally. The software will simulate the design in 2.5D and create the pattern data for the machine using the most appropriate stitch formation. The software will allow for the creation of fabric collections and or pre-selections prior to production of the textile. Visit Monarch Knitting Machinery (UK) Ltd.
BMSvision to show live demo of KnitMaster system
The BMSvision KnitMaster system will also be on display with a live demo monitoring four circular knitting machines on the Monarch stand in Hall 4 (booth E 105/106).
Through intelligent wireless networking of all production equipment in the mill, the BMSvision KnitMaster, WeaveMaster and SpinMaster MES (Manufacturing Execution Systems) solutions transfer huge amounts of data originating from the various production machines and processes into meaningful information for managers.
QualiMaster is the BMSvision solution for on-loom, grey and finished fabric inspection including a very powerful module for optimized mapping and cutting. BMSvision will showcase the latest Version 9.10 of its Master systems now available with both Oracle and SQL server data base engine, focusing on:
• New web-based module for real time “Events & Alerts” with integration of MyMES mobile app and the Smart Bracelets
• MyMES mobile app with the alert and cockpit module. The cockpit shows the KPI’s and most important production data of the plant on the user’s smartphone
• Smart Bracelet: low-cost wearable device informing operators when there is a need for intervention at a machine
• New version of WEB-DU with various new features to assist operators and technicians in optimizing their workload
• BI Connect for big data analytics
EnergyMaster, one of the modules of the BMSvision MES solution, makes all energy streams in the plant transparent and allows allocating the exact energy cost to each production batch. Excessive consumptions or consumptions while the machine is idle, are immediately detected and highlighted.
ITMA 2023 will also witness the introduction of TEXconnect, a cloudbased platform offering a wide range for MES features for the entire textile manufacturing chain.
Using the same reliable and proven BMSvision data collection hardware and network, the TEXconnect subscription-based system is easy to set up and provides the most common functionalities of the on-premises Master systems at a limited initial investment. TEXconnect can be accessed from the browser of any internet connected device and is easily scaled according to the customer’s requirements.
The Cyclops and Argus camera based automatic on-loom fabric inspection systems detect warp, weft and point defects during the weaving process and stop the loom in case of presence of any critical defect. The Cyclops is mainly used to inspect plain fabrics while the Argus is the perfect quality monitoring tool for weavers of high end unicolor jacquard fabrics, such as OPW airbags.
At ITMA, BMSvision will present a new generation of these systems allowing mounting above the loom, resulting in inspection immediately after the reed. The BMSvision KnitMaster system is also on display with a live demo monitoring 4 circular knitting machines on the Monarch stand in Hall 4 stand E 105/106.
With experience since the 1970s, BMSvision is a leading global supplier of Manufacturing Execution Systems (MES) for the discrete manufacturing industry, with focus on the textiles and plastics industries. BMSvision offers a wide range of systems aimed at productivity, quality improvement and energy management. BMSvision is present at key locations around the world, either with own branch offices or through a worldwide network of agents and service centres.
Busi Twin Layer Machine, from its Platinum line
Italian socks knitting machine manufacturer Busi Giovanni has announced the inclusion of its Busi Twin Layer Machine, from its Platinum line, in its Milan line-up. The Busi Twin Layer is a high production single cylinder sock machine with latch needles in the dial that enable it to produce technical sports socks with twin fabric. The machine is based on the Busi Idea Terry, and it has all the same features and knitting possibilities.
The machine is provided with a patented device that uses the dial needle for the production of an internal layer and the cylinder needles for the production of the external layer. The two fabrics that form the sock are knitted contemporarily and can be joined as required, merging into one fabric at the welt, heel and at the toe of the sock. This way the two fabrics cannot slide one onto the other.
“The machine is also provided with a device for selected terry, which is designed to enable the machine knitting the sandwich terry and the normal terry even in the same sock without any mechanical change. It also enables the fully automatic switching from plain stitch to half terry and to full terry,” the company reports.
Rimaglio 3.0
The Twin Layer performs 3-colour patterns plus ground and can be equipped with the company’s Rimaglio 3.0 device for automatic stitch-by-stitch toe closing. The Rimaglio device is designed to enable classic linking to be achieved on the machine in a completely automatic way. The automated device is situated at the side of the knitting machine, it downloads the sock from the machine, after completion of the knitting operation, and it transfers the sock to the linking device, where it is sewn loop by loop.
The sock is turned inside out, so that the linking remains on the inside of the sock, resulting in perfect traditional-looking linking. After being sewn, the sock, already reversed to the right side, is removed from the machine and is ready for the next boarding operation.
Since 1958 Busi Giovanni Srl has specialized in the design and construction of single-cylinder machines with rib needles in the dial for the production of high-quality stockings, socks and tights. Today, Busi is recognized worldwide as one of the most inventive producers of machines for high-performance and high-tech socks.
The company is a supplier to the most important producers of stockings, socks and tights, for the men’s, women’s and children’s markets – classic, patterned, sports, technical-sports, as well as medical, with special solutions for graduated compression.
Busi sells in more than 50 countries around the world (90% export) through a network of partners that provide distribution and service.
Steam setting and conditioning equipment by Xorella
At ITMA 2023 (stand B106 in Hall 18), Xorella, the specialist in steam setting and conditioning equipment for yarns and fabrics, will launch XO Automation for the double door XO Select conditioning machine series, and XO Solid, a new machine series to complement XO Smart, XO Trend and XO Select machines.
XO Automation
The new XO Automation system consists of roller conveyor systems for loading and unloading two-door XO Select conditioning machines. An additional pallet wrapping machine with a turntable, weighting station, label printer, safety fence and security system can complete the system. The XO Select controller and automation system can handle and store individual customer-specific material and packing programmes.
XO Select and XO Automation are designed for yarn steaming on multiple pallet dimensions at heights up to 2,650mm. The linear material flow passing conveyor and steaming machine avoids any mix between steamed and unsteamed materials. XO Automation fills the gap between the XO automated moving platform and the fully automated transport system – from spinning hall to warehouse.
XO Solid
The new cubical XO Solid combines a high loading space of 1,800mm x 1,700mm x 4,000mm (H x W x L) through double row pin trolleys or pallets for easy manual loading of six units on floor level without a pit or platform. XO Solid is therefore designed for installations on upper floor levels. The new frame design combines all necessary components which are factory preinstalled on a single frame, for easy ‘plug and play’ installation at the customer site. Additional smaller steamer dimensions for two and four loading units are also at the planning stage.
The new XO Solid incorporates all the renowned features of Xorella machines based on the long term experience in high temperature dyeing vessel production of Fong’s, including:
• A Siemens controller with OPC UA interface and XO data tool for batch storage
• Am XO EcoPac waterless claw pump or two-stage water ring vacuum pump
• A high energy efficient accumulator for steam, electric and combined heating
• Vessel and piping in world-class stainless steel
• European key components such as pumps, heating elements, valves and sensors
Full range of machinery for treatment of knitted fabrics by Goller
Goller, a member of the CHTC Fong’s Group, will promote its KnitExcellence package at ITMA 2023 in Milan, at stand B106 in Hall 18. The KnitExcellence package includes a full range of machinery for the complete treatment of knitted fabrics – Knit Complexa for bleaching, Knit Mercer for mercerisation, Knit Economica for dyeing and the versatile Sintensa washing concepts for washing after dyeing and printing.
The multi-purpose rollerbed steamers of the Knit Complexa can be used for steaming after bleaching but also washing, when required. The rollerbed in the steamer transports the material while slightly shifting the material from roll to roll to avoid yellowing on the fabric surface. A sump heating equalises the steam condition in the entire compartment and guarantees a homogeneous humidity. The Knit Mercer unit provides very low tension during caustic treatment and a homogeneous mercerizing effect. Short distances, load cells and drive control provide continuously smooth transport of the material through the machine.
The Knit Economica S Roll padder secures the same pressure over the width of the squeezing rollers and assures an equal dyeing of the fabric The combination of dwelling and drum wash concepts with cyclone rotors realises the best use of washing times and mechanical treatment to minimise water and chemical consumption.
The Goller Sintensa is a continuous washing machine used for washing off knitted textiles after reactive dyeing and printing as well as polyamide after acid printing, wash off disperse print and every kind of spin oil washing. The machine uses a combination of mechanical action, water and detergent to remove any residual dye or chemicals from the fabric. It can handle large volumes of fabric, making it ideal for use in industrial settings instead of discontinuous treatments. The machine is designed to minimise water and energy consumption, which can help to reduce operating costs.
Overall, the Goller Knit Excellence concept is a reliable and efficient package that is well-suited to all wet finishing treatments of knitted textiles. Its robust and high quality design and advanced features make it a popular choice for textile manufacturers around the world.
Fong’s Europe will show efficient and eco-friendly Dyeing Machines
Fong’s Europe has constantly evolved its dyeing systems based on the Airflow principle for achieving excellent dye penetration and uniformity while minimising colour differences between different areas of a fabric. At ITMA 2023 in Milan (Stand B106 in Hall 18), the company will introduce its latest Then Synergy Airflow and Then Airjetwin machines which exploit the principle to provide high-quality, efficient and eco-friendly dyeing processes for a variety of fabrics.
“Then introduced its first machines with Airflow technology in 1980 and since then we have had wide experience of pretreating and dyeing with Airflow transport systems on all kind of fabrics,” says Fong’s Europe Director of Sales and Marketing Richard Fander. “Our team of engineers has collected data on dyeing processes, results and consumption figures for years and constantly makes use of this accumulated know-how to optimise the processes of our customers.
“The team understands Airflow dyeing processes and technology based on it guarantees the lowest liquor ratio on round shape machines. The transport of fabric by air reduces the liquor ratio compared to every kind of hydraulically driven transport system.”He adds that while not every fabric can be dyed and treated on Airflow machines with the same handle and appearance as on hydraulic round shape or long shape machines, where it is applicable, it can lead to significant savings of up to 35% in water, 50% in salt, 20% in dyestuffs and 30% in process time.
“The need to reduce energy and water consumption worldwide is much higher than in the past and a significant number of the overall processes in a dyehouse can be successfully shifted to Airflow machines,” Fander says. “We will see more of a mix of different machines and technologies in the dyehouse than in the past and while this may lead to complexity in a company’s machine portfolio, it will ultimately result in considerable cost savings. A higher volume of data can be managed, but the higher environmental impact of the old routines will soon become a competitive disadvantage.”
Features: The Then Airflow dyeing machines have several innovative features, including several parallel functions for reducing process time. The VPR system shortens the rinsing time and water usage and the well-proven robust and homogeneous spraying device in the nozzle ensures a uniform dyeing in the shortest process time. The very short liquor ratio also reduces the use of salt and chemicals.
Then Airflow systems also have a unique dyeing process control system that allows for precise control over dyeing parameters such as temperature, pressure, and chemical dosing, ensuring consistent and high-quality results.
Homogeneous distribution of the air in the machine is a must to get equal dyeing and turn times. The design of the Airflow blower, its drive and the whole piping guarantees an equal air pressure and air volume in the complete system, even for big multiport machines. It blows up the fabric and avoids crease marks. Additional options like spray ring in front of the nozzle and additional liquor application in the nozzle now allow Airflow dyeing on nearly every kind of fabric.
Knits and woven fabrics from light up to heavy weight and virtually any fibre or fibre blend can be bleached and dyed without machine modifications or changes. Additionally, the
Synergy Airflow dyeing machine has a user-friendly interface that allows for easy operation and monitoring of the dyeing process.
“Overall, the Then Synergy Airflow dyeing machine is a reliable and efficient solution for high-quality and eco-friendly fabric dyeing,” Fander concludes.
LAIP, dyeing technology consistency with environmental and market needs
LAIP was founded in 1958 with the intention ever since to supply the market of the textile dyeing industry with innovation and quality. The context in which the company lives is the Prato district, Italy, strongly: by unrivaled textile knowhow. Therefore, the obvious need to work is quality without forgetting innovation, two fundamental production concepts.
Thanks to this attitude the market globally recognizes the continuous evolution of LAIP. At ITMA 2023 (Stand: Hall 11 • Booth C105) LAIP will be showcasing its latest machines both for fabric yarn and fiber dyeing.
Among them
198 HT, the highly demanded machine for tow – packages and fibre dyeing, it allows the same liquor ratio to be maintained even with partial loads!
BID, (Bobbins Injection Dyeing) ensures absolute repeatability, productivity and reliability for multicolour printing and dyeing of yarn in bobbins.
Nautilus, the cutting-edge machine. Conceived with a double belt, it is suitable for dyeing delicate fabrics keeping the low liquor ratio constant by the maximum fabric load up to 40%. The low water consumption means low electrical consumption and energy saving.
Jet 250 HT, the easy machine that never stops to get perfectly dyed fabrics with no abrasions nor creases.
Beam, the ideal machine to dye high end silk and technical fabrics, tubular and warp knit for sportwear enabling the optimisation of production times and superlative technical
performance.
The company is driven to always face new challenges and the interaction with customers stimulate the design and technology department to find suitable solutions to face the new and important needs of dyehouses. From this ability to dialogue, the innovations – that will then be globally disseminated – are born.
It is not easy in the world of dyeing to find eco-friendly solutions, as requested by many customers. Yet they must be faced and resolved. This is where innovation comes from:
super-efficient pumps, low liquor ratio, ease of use, automated systems, efficiency improvement and industry 4.0 features. All aimed at creating ever more performing dyeing machines in terms of sustainability that goes towards an ecological transition that sees LAIP and its customers seriously committed.
Italy’s Santex Rimar to present innovative solutions
SANTEX RIMAR AG is the leader in technology for textile finishing of high-quality knitted fabrics, offering comprehensive systems of stand-alone machines for the treatment of tubular and open knitted fabrics. Santex’ goal is to maximise performance with low energy consumption to achieve low residual shrinkage, smoother handle and silklike appearance. The lines are equipped with various energy saving options, benefiting customers through sustainable production and low CO2 levels.
Many of the world’s renowned fashion houses rely on the expertise of SANTEX RIMAR AG, which was founded in Switzerland in 1982. With Santaframe and Santacompact RDA, Santex Rimar AG presents its well-known stenter frame in combination with the felt belt compacting machine for the finishing of high-quality open-width knitted fabrics and for woven fabrics.
The outstanding performance and production of the SANTAFRAME is based on continual development using the latest advances in thermodynamics, allied to the changing need of customers. The heating system is located above the fabric web in the upper part of the 2 m treatment zone.
An air circulation fan draws the air from the nozzles and the treatment zone through the filter panels and guides it along a short path to the heat exchanger, from where it is fed into the nozzles. The arrangement of the heat source on the pressure side of the air circulation fan enables a high air circulation speed and uniform heat distribution over the entire fabric width, thus achieving an unrich drying performance. This technology results in energy savings and cost reductions in the drying and heat-setting process of textile fabrics.
Visit Santex Rimar Group in Hall no. H18 Booth no. A110 and discover the products which stands for Swiss and Italian innovative solutions based on the real need of the customer and for high productivity and sustainable production.
Thies will exhibit the Signature Series, opening a new chapter in fabric coloration
For Thies, this year‘s ITMA is characterized by today‘s mega trends – transition now, transparency, digitalization, automation and the circular economy. Thies Team is happy to welcome you in Milan in Hall H11, booth B208. We invite you to engage in thought-provoking conversations, to share with us your biggest challenges, and to assess our technological breakthroughs.
Transition Now
For the first time, Thies will exhibit the Signature Series, opening a new chapter in fabric coloration. We are confident the Signature Series will prove to be both disruptive and seamless. Following years of research and development, Signature technology transforms dyeing as we know it, but it is plug-in ready for existing dye houses. With its novel ability to precisely dose concentrated chemistries and flexibly use less water to transport fabric, the Signature Series is capable of delivering highly consistent results with liquor ratios starting at 1:2.3 liter of water per 1 kg of fabric. Proven in bulk production, water consumption is tremendously reduced, dyeing uniformity is improved and batch times are shorter. Signature‘s ultra-low liquor ratio has further multiple cost and environmental benefits. Dye consumption is reduced up to 20 % while achieving the same shade, less energy is required for heating water, and the treatment of water is less costly because the total dissolved solids (TDS) is reduced up to 50 %. Unlike pad or spray dyeing, with Signature there is no need to have separate machines for washing, bleaching and dyeing because nearly all wet treatments can be carried out on this single machine. There is no intermediate handling and drying, and there is no end-to-end variation associated with wet-on-wet pad-bath dilution. Color uniformity is improved over pad dyeing because fabric passes through the nozzle 60+ times versus a single nip, and there is no side-center-side variation caused by pad roll wear or crowning. A wide array of fiber types and fabric structures can be successfully processed, including woven fabrics, warp knits, spacers, and circular knits. In short, the Signature Series has the proven advantages of batch dyeing while competing with the low liquor ratio of single-pass applications. The ease with which Signature technology fits into existing production lines means payback on investment starts on day one.
Transparency and Digitalization
The first steps toward making dyeing a more comprehendible science are measurement and analysis. Thies offers several tools for digitalization, reporting, and process control. Energy Control, pH-control, conductivity measurement, and Dye Control are tools for optimizing recipes and process settings. Visual representations of the process curves enable both a control of the turbidity and a determination of the dye extract from the liquor. By measuring the process and providing intuitive reports that aid decision making, Thies makes dyeing less art and more science.
Automation
The need for automation is ever-growing, and its advantages are diverse. Automation offers (1) increased productivity through reduction of wait times, (2) stable quality, (3) improved occupational safety, (4) a more inviting workplace, and (5) freedom from constraints caused by labor shortages.
An automated storage, weighing and dispensing system for dyestuffs and / or auxiliary chemicals comes with many advantages:
• Workers no longer have routine contact with chemicals and dyes during weighing, transportation, dispensing, and dosing.
• Tasks that do not add value are eliminated, and the workplace is safer. The dangers of falling or spilling chemicals and dyes are minimized, protecting workers and the environment from harm.
• The digital storage system manages the exact stock levels and generates order proposals if the stock falls below the defined safety level.
• A supervisory production planning system, centrally hosted, controls the process organization of the complete dye house by bidirectional communication. The MPS systems (Multi Product Supply systems) monitor the delivery destinations (tanks). The synchronization ensures an optimal process and production sequence. MPS systems integrate themselves seamlessly into the concept of a future-oriented, efficient dye house, delivering large increases in productivity and quality.
• At the same time, the automatic weighing, dissolving and provision of dyes and chemicals leads to increased dyeing quality results, maximum reproducibility, savings of human resources, significantly increased occupational and environmental safety, as well as optimized consumption of products.
• Today, there are solutions for smaller dye houses that work self-sufficiently, and modularity offers a manageable, affordable, step-wise improvement for larger dye houses.
• As a system provider, Thies also offers holistic solution concepts. An example is the automated loading and unloading of package carriers. The package carriers are prepared automatically using intelligent robot technology, so that there are no waiting times and the time-consuming and physically strenuous manual work is no longer necessary. In addition, the yarn packages and locking devices are loaded and unloaded or locked much more gently.
• Thies automation solutions are no longer limited to the dyehouse. We offer custom solutions for fabric finisher and the coating industry.
Circular economy
Wastewater and its thermal energy are valuable resources. This has an ozone system in its portfolio that can be used to decolorize colored waste water. The use of active oxygen splits the organic and inorganic impurities. The oxidized dye molecules become colorless. The result is a colorless solution which can be recycled for reuse in the process. Heated wastewater is a regenerative energy source. Transferring its energy to cold water reduces primary energy consumption as well as CO2 emissions. The use of Thies‘intelligent heat recovery systems enables a significant reduction in production costs and makes a major contribution to efficient, clean and energy-saving production. In addition to global market forces, the European Green Deal demands that, by 2030, textile products placed on the EU market are long-lived and recyclable, to a great extent are made of recycled fibers, are free of hazardous substances, and are produced in respect of social rights and the environment. With expertise in industrial-scale production of pressure vessels and automated material handling equipment, Thies supports solutions for both removal and re-dyeing of recycled fibers and yarns.
Wet Processing and Jet Dyeing Technology by BENNINGER
Benninger aims to become the complete system supplier with leading technology for continuous wet processing, discontinuous dyeing and remain the leader for solutions for the tire cord industry. We take seriously our responsibility towards sustainable textile production and have always stood for textile finishing plants that are particularly resource efficient.
Benninger supply overall solutions for all important textile wet finishing processes, and we specialize in the continuous open-width treatment of woven and knitted fabrics, technical textiles as well as jet dyeing machines, jiggers, along with the complete and integrated dye house supply systems such as liquid dispensing, salt and soda ash distributing systems as well as dye staff distribution systems. Our portfolio also includes caustic soda recovery plants and waste-water heat recovery systems. Thanks to our comprehensive process know-how and deep engineering understanding we offer high quality installations with excellent customer service. With our solutions, producers will make a huge contribution to Decarbonizing Textile.
At this year’s ITMA Milano, BENNINGER will be presenting its latest developments:
• The new Benninger jet dyeing machine Fabricmaster, with unmatched water consumption figures. It is the most sustainable way of discontinuous dyeing today. Fast, cost effective and on the road to zero footprints.
• The chemical dispensing system, CDS, serves all kind of discontinuous and continuous machines in an accurate, unbeatable, and fast way.
• The new Benninger-Küsters CPB dyeing station for knitwear, the only salt-free cold dyeing process.
• The new Benninger singeing machine, SingeRay, ensures perfect singeing effects, cost efficiency and uniform quality.
The sustainable way of discontinuous dyeing with the new Fabricmaster
Benninger has produced the fastest, most versatile, and economic Jet dyeing machine of the industry and which ensures dramatically shorter process times. The Fabricmaster is not only a robust and reliable system, but the benchmark of the industry in future. Its harmonic versatility is the beacon to conquer new markets. Our passion for perfect fabric quality makes sure that you produce the widest range of fabrics at lowest cost and unmatched water consumption levels.
Salt-free dyeing of woven fabrics and knitwear
Salt-free dyeing without the use of energy is only possible using the cold pad batch (CPB) dyeing process. This process is also becoming increasingly popular in tropical and subtropical regions, which is reason enough for Benninger-Küsters to adapt the CPB systems even more effectively to the climatic conditions. The heart of our CPB system is the BENNINGER KÜSTERS DYPAD, which we will also be presenting again this year at the ITMA Milano. BENNINGER is the only textile machine manufacturer with the knowhow of the original S-roller technology, which is synonymous with an even dyeing result across the entire fabric width.
Brand new Singeing machine “SingeRay”
The “100% made in Germany” singeing machine is equipped with 2 burners and a double nozzle strip. The silicium carbide burning chambers ensure complete combustion, and a constant burner temperature thanks to 4 cooling channels. Low gas consumption and a perfect flame will increase the scope of your fibres and blends.
BRÜCKNER presents innovative and trend-setting highlights for textile finishing and coating
BRÜCKNER will show the next stenter generation POWER-FRAME SFP-4 with many new features: new electric / hydrogen-powered heating systems, intelligent software solutions for optimizing formulas, systems for heat-recovery and exhaust air purification, innovative application systems for chemicals, and newly developed machine concepts.
CO2-free heating systems
The most important innovation of the BRÜCKNER dryer are without doubt the innovative heating systems. Driven by the energy crisis and the constant focus on energy-efficient solutions, new possibilities to combine different heating media like gas, steam, oil or electricity have been developed. In addition, BRÜCKNER also offers burners which can be operated with hydrogen in the future. These combination possibilities allow the textile finisher maximum flexibility in the choice of the energy carrier. Another exciting development are solutions for the purely electric heating of industrial ovens by means of heat pumps, which BRÜCKNER offers together with a partner. In the present situation and with a view to the future, these new types of heating offer decisive advantages: Green hydrogen and/or electricity reduce the dependence on fossil raw materials and contribute considerably to minimize the CO2 footprint.
Smart Production Systems
Digital products and services are another highlight. On request, new lines are equipped with various intelligent assistance systems that support the machine operator in finding the optimum machine setting for each process. A special innovation is the new simulation tool ExperTex: with the help of artificial intelligence, the desired production process of drying or heat-setting is simulated on the computer. Different scenarios can then be compared with each other: Throughput times, energy consumption, CO2 footprint and production costs. This innovative system offers customers considerable added value, as it allows accurate pre-calculation of orders, opens up productivity gains and/or energy savings, and permits “right-first-time production” by means of preoptimized formulas. Expert knowledge and years of experience in textile finishing are thus available at the push of a button. This tool and much more will be available to customers in the new myBrückner customer portal in the future. All important machine information, access to digital services, and a service system will be bundled there and can be accessed at any time.
Heat-recovery and exhaust air purification systems
The new generation of ECO-HEAT heat-recovery and ECOAIR exhaust air purification systems features a new type of intelligent control. Both types of lines can also be retrofitted at any time to older lines from various manufacturers in order to realize the best possible energy savings and solve existing exhaust air problems. All exhaust air treatment systems can be tested in advance at customers’ sites by means of laboratory systems in order to better assess utilization rate and efficiency.
Innovative systems for the application of chemicals
Of course, customers can inform themselves on the BRÜCKNER booth also about numerous further possibilities to save primary resources such as energy, water, chemicals and waste water. Here, for example, the minimum application unit ECO-COAT should be mentioned, a new type of padder with minimum preparation quantity or residual liquor, and a further developed coating unit OPTI-COAT 2in1, which combines the use of floating knife and knife-over-cylinder application in one system. With a high-precision coating cylinder and a perfectly ground coating knife, excellent results can be achieved for paste and foam coatings. In addition, the special design of the unit ensures optimum accessibility for cleaning and maintenance purposes.
New finishing machines
Another highlight is a completely new designed highperformance relaxation dryer POWER-DRY which can be heated CO2-free by means of a high-temperature heat pump. In order to show the variety of BRÜCKNER’s product portfolio and to illustrate technologies in a realistic and “tangible” way, many machine models will also be exhibited.
The total cost of ownership (TCO) is lower for BRÜCKNER’s lines than for other suppliers. This applies to all presented machines in the field of finishing of carpets, nonwovens and denim, migration- and crease-free continuous dyeing as well as in the versatile field of technical textiles and is supported by the technological advice of experienced experts.
Modernization / upgrading of existing lines
With regard to sustainability and resource conservation, BRÜCKNER’s After Sales team and the technology team offer numerous possibilities for modernization and technological e on site. It is not always necessary to invest in a new line, often the potential of older machines can be exploited quickly and efficiently by modifications and also by technological consulting. Noticeable improvements in productivity and energy efficiency can be achieved without longer downtimes.
Let yourself be inspired by these highlights! The BRÜCKNER team is looking forward to meet you personally and to talk about further innovations in hall 18, booth no. A101 – the way is worthwhile!
Imogo newly developed Dye-Max Spray Dyeing line
Imogo is excited to show about our Digital dyeing technology at ITMA 2023 and how it reduces the environmental impact of dyeing and increases productivity.
Textile dyeing is one of the most wasteful, and from a sustainability stand point, questioned industries. The newly developed imogo Dye-Max spray dyeing line is the answer for everyone looking for a sustainable alternative process. The beauty of the story is that not only does the environment benefit from implementing the Dye-Max, profitability and productivity will also be greatly improved through the dramatically reduced waste water volumes, the greatly reduced energy and chemistry consumption and the incresed production speed and consistant and predictable quality.
The imogo Dye-Max is a flexible system designed to be implemented in just about any process where precise and repeatable application of low viscosity dye is required. In most cases this will mean replacing a padder. The system can be configured with customized reel stands for “Spray batch” production or integrated in an existing line. The DyeMax is ideal to integrate in a stenter line or in most continuous dyeing lines.
The dye application stations are powered by the patented imogo Pro Speed valve. The Pro Speed valve in combination with the high precision nozzle produces an even and consistent coverage along and across the fabric.
Ideally the Dye-Max is combined with a Mini-Max lab unit. This will even further increase productivity and enable Right First Time dyeing through the recipe testing concept. The DyeMax application unit is a closed chamber where the dye dispersion is applied by high preformance spray valves.
The spray casettes consists of precision nozzles for accurate and consistent coverage in combination with the patented imogo pro speed valve that controls the volume applied. The chamber is equipped with an exhaust system and droplet separator to ensure that the environment around the unit is free from sprayed particles.
The application unit of the Dye-Max consists of a closed chamber containing a series of high speed digitally controlled valves with precision nozzles for accurate and consistent coverage. Fast changeovers with virtually no waste together with a high production speed enable a high productivity and unmatched production flexibility.
At ITMA 2023 the proven Mini-Max laboratory unit, used alongside Dye-Max installations for pre-determining application volumes and colour matching for Right First Time dyeing, will demonstrate the principles of imogo’s technology.
The huge potential of Dye-Max has been quickly recognised by brands seeking solutions to their sustainability targets and an industrial-scale installation is currently being commissioned. Further details will be announced prior to ITMA 2023.
Weko&Rota Spray to exhibit at ITMA Milan
Weko and Rota Spray, the leading manufacturers of rotor spray minimal application systems for textile dyeing, finishing, coating and moisture management will be exhibiting at ITMA in Milan, Italy, at Hall 14, Stand B103.
“The worldwide textile industry is suffering from COVID-19 impact and the highly unsustainable use of water, energy and chemicals as well as an immense cost pressure,” said Jayanta Sanyal, Head of technical sales and processes at Weko. Weko and RotaSpray have therefore analysed today’s processing in dyeing and finishing mills to find out opportunities to increase sustainability, productivity and profitability.
Today one of the main dyeing processes is discontinuous and consumes a high amount of water, production time and drainage. The existing solutions for continuous dyeing ranges are consuming high energy, chemicals and generating a high load on the effluent treatment plants. Also in a conventional continuous dyeing range a cost and scrap efficient production of small lots is nearly impossible while the market demands for it, the company said in a press release.
This gap could be closed by using a minimal rotor spray application method from German companies Weko and RotaSpray. These technologies combine a lot of benefits such as low pick-up, no tailing (contact-free application), stable and precise production, low drainage, strong reduction of energy costs, no centre-side-variation, no hydrolysis, substantivity or incompatibility issues and single and both side dyeing.
The rotor spray technology could be used for reactive, Sulphur, pigment, VAT and disperse dyeing on fabric or denim yarn stage.
The key solution beside the special spray technology is the set up of new processes invented by Weko and RotaSpray. For example, the PS² process instead of the classic PDPS process, or PSB35 instead of CPB and many more.
PS2 process could save up to 1.350 tons of CO2-emission every year and could reduce start-up scrap rate by 90 per cent compared to the classic PDPS process. For denim slasher dyeing a new process of a compact slasher dyeing range was recently developed and will be promoted during the coming ITMA 2023. The latest development along with partners is a continuous Polyester Disperse and Pigment dyeing process using another newly invented technology: Weko-Spray +Weko Dry-E + Weko Fix-E.
The Weko Dry-E and Weko Fix-E technology is a combination of advanced near-infrared (aNIR) light energy, high performance management of the NIR energy and a precisely controlled moisture extraction.
The aNIR principle reacts fast with comparatively low energy. The technology is still proven in a lot of other industries and works with electromagnetic waves which have the highest energy densities and effect molecules of various substances much faster than a cotton, viscose or polyester fibre.
Weko Dry-E and Weko Fix-E are based on a pure electrical power supply. Therefore these units can be easily used with renewable energy sources to realise a carbon neutral production.
The system could be used on diverse dyeing and finishing lines and unfolds its biggest potential by combining it with a minimal rotor spray application system. Think about the energy saving which could be only reached by immediate start/stop function and format setting. Additionally in a lot of processes like typical stenter frame drying the water molecules are extracted up to six times faster. “This could be a real big step forward in textile processing to reduce the carbon footprint,” added Sanyal.
New ways in textile production from market leader in measurement, control and automation technology by Mahlo
Transforming the World of Textiles is the motto of this year’s ITMA, which is being held from 8-14 June in Milan. The theme could not be better chosen, says control and automation specialist Mahlo. Not only are the tasks of textiles becoming increasingly diverse, but the focus of their production is also shifting. Producers are performing a balancing act between sustainability and economically viable production in the face of steadily rising energy costs and a shortage of raw materials.
German machine manufacturer Mahlo GmbH + Co KG says it is ‘hitting the zeitgeist’ with its latest developments for process optimisation. Increasing productivity and saving costs at the same time – visitors can see how this is possible at booth H18 – C108.
“Textile machinery manufacturers and textile producers are working ever more closely together to create a more sustainable future for the industry,” says Mahlo Head of Sales Thomas Höpfl, and his company is just the right partner for this, he explains. The broad product portfolio in the field of measurement, control and automation technology
covers almost every textile application. “Thanks to our modular system architecture, we find individual solutions for our customers to optimize their production sustainably,” he adds. At ITMA, visitors can therefore expect an overview of all sectors that the machine manufacturer caters to. Public product presentations with changing themes will
provide concise information on the most important systems.
Straightening machines
For almost 80 years, the name Mahlo has been synonymous in the textile industry with high-quality automatic straightening machines and process control systems. The recipe for success from decades of experience coupled with the latest technological developments has made Mahlo the world market leader in the field of straightening and control. Mahlo also intends to set the highest standards in distortion detection and correction with the new Orthopac RXVMC straightening concept, which will be presented for the first time in Milan. The system can remove distortions in textile fabric webs even faster and more precisely.
Process control and QMS
Process control systems are a must in modern textile production. They not only ensure quality, but above all contribute to the efficient use of the machines. Thanks to control of exhaust air, fabric temperature, dwell time and moisture, only as much energy and raw material is consumed as is really needed. Also, on show in live operation are the Patcontrol PCS for pattern recognition and the Famacont PMC for controlling weft and stitch course
density. Both systems help producers to maintain the residual shrinkage values they guarantee. Interested parties can get an explanation of howthey work at the Mahlo booth, and fabric samples they bring along can be tested on site.
Digital environments
Another major topic remains Industry 4.0, because the best measured data is of no use if it cannot be utilised. Mahlo has continuously developed its digital environment mSmart. “Our systems generate data that the customer can use immediately to regulate goods on-line. At the same time, all measured values are backed up in our data management system mLog enhanced and can be retrieved at any time. With this historical data, processes can be optimized and weak points in the process can be minimized,” explains Thomas Höpfl.
And of course, there is one thing that a Mahlo booth at ITMA cannot do without – the Mahlo Bistro. Here, visitors can enjoy Bavarian specialties and recap in peace how their production processes can be effectively improved, Mahlo concludes.
Baldwin Technology to demonstrate how to “Finish with Perfection”
Baldwin Technology Company Inc. is excited to show the textile supply chain how to “Finish with Perfection” at ITMA 2023 with its TexCoat™ G4 precision spray finishing system, eliminating chemistry waste on changeover, saving water, and achieving faster speeds through the stenter frame and relaxed dryer.
Baldwin will demonstrate TexCoat G4 from Stand H-14-C205, as well as its Plasma Pure treater. ITMA participants can stop by and “touch” Baldwin’s wide array of TexCoat G4-applied fabric samples from textile mills around the world and experience what precision finishing “feels” like. Experts will be on hand to discuss how Baldwin Technology can assist in transitioning the textile supply chain to reach their sustainability and carbon footprint goals while improving performance and saving money.
“Since its introduction at ITMA 2015 in Milan, global textile finishers have embraced TexCoat and reaped the benefits,” said Rick Stanford, Baldwin’s VP Global Business Development, Textiles. “They have been able to increase profitability, cut energy use, and reduce their carbon footprint in addition to exercising precision control with patented precision spray technology.”
In the context of a cost-sensitive global economy and an increased focus by brands, consumers and regulatory agencies on sustainability, customers are placing a premium on sustainability-advantage textile production. TexCoat G4’s noncontact spray technology offers numerous advantages compared to old and commodified methods of applying finishing chemistry.
TexCoat G4 processes a wide range of low-viscosity waterbased chemicals, such as durable water-repellants including PFAS-free, softeners, anti-microbials, easy-care and flame retardants, just to name a few. The company’s technology uses the same chemicals as found in traditional pad baths with no special auxiliaries required.
In addition to TexCoat G4, Baldwin is offering its Plasma Pure treatment for textiles. The system enhanced and more efficient dyeing, coating and lamination of textiles and nonwovens. Its ceramic electrodes generate an air plasma used to efficiently treat the fabric surface. Key benefits include dramatically improved absorption and adhesion properties of the fabric, boosting productivity while enhancing the absorption properties with an optimized and uniform dyeing result and a significant acceleration of the absorption process. Laminated fabrics benefit from Plasma Pure technology with greater bonding strength.
Groz-Beckert presents its highlights from research and development
Groz-Beckert will be represented at ITMA (hall 2, booth D101) with its six product sectors and will have various innovations in its luggage. The presentations at the booth will be supported by augmented reality applications. This allows visitors to discover the products both live and virtually.
The Knitting product sector will be represented at the GrozBeckert stand with its four product groups circular knitting, flat knitting, legwear and warp knitting. In the circular knitting segment, for example, two newly developed knitting systems will be on show which has been realized in collaboration with machine manufacturers. The developments focus on energy savings, extended cleaning intervals and increased process reliability.
The flat knitting group will be presenting a newly developed high-performance needle, which is particularly suitable for the production of technical or medical textiles. For customers in the legwear industry, Groz-Beckert has both further developed sock and fine hosiery needles and system parts in the bag. Thanks to their high resistance, these products help to reduce knitting process costs. The warp knitting product group will be presenting new needle modules at its booth, as well as the newly developed hole punching needle for piezo jacquard machines.
In addition to the machines for weaving preparation, the Weaving product sector will present its recently expanded portfolio of technical weaving reeds. The new weaving reeds make it possible to supply customers who produce fabrics with high densities. The weaving reeds are used in the production of special fabrics, for example, in technical filtration, membrane technology, solar cells or touch screens.
Products and services for classic needling and hydroentanglement will be presented by the Felting (Nonwovens) product area. In the field of felting needles, visitors can look forward to two world firsts: a new notch shape and the Groz-Beckert felting needle module. In the felting needle module, the needles are embedded as a module in a plastic mold for the first time. The needle modules are characterized by very high deformation resistance and offer new dimensions in needle density.
For the production of tufted floor coverings such as carpets, bath mats or artificial turf, the Tufting product sector will be presenting its proven Gauge Part system. The coordinated combination of the various materials of the individual parts and the functional interaction ensure a convincing result in the production process.
Various new and further developments will also be shown by the Carding product area. For those interested in the nonwovens industry, for example, the world’s finest Interlocking wire for reduced risk of crashis included. For customers of the spinning industry, the division will be presenting further developed stationary flats and revolving tops. The new revolving tops have been adapted to the processing of fine yarns, while the stationary flats have been provided with a new, resistant aluminum profile.
The Sewing product sector is focusing on the presentation of its special application needles, SANTM. The sewing machine needles of the SANTM series have been specially developed for demanding sewing operations – e.g. for sewing technical or finest textiles. The division will also be presenting its new Needle Finder. The Needle Finder is an interactive tool in the online customer portal that helps customers select the right needle.
Kern-Liebers has a full range of its needles and accessories for the knitting machine sector
Kern-Liebers Textile, one of the leading suppliers of components for textile machinery, will have a full range of its needles and accessories for the knitting machine sector on display at ITMA exhibition. The company will present its latest developments and products, including innovative solutions for the textile industry. Visitors to the booth can look forward to a wide range of products for knitting, hosiery and spinning machines. Likewise, this show will provide an excellent opportunity to network and exchange ideas with customers and interested parties.
Amongst the company’s latest developments are the latest generation of Relanit Sinkers, which have been designed to meet the increasing market demand for high speed, high quality knitted fabric production.As the demand for higher quality fabrics continues to grow, so in turn is there a requirement for improved machine settings and the tolerances of the ancillary equipment, a factor that requires a higher standard of specification for the Relanit Sinkers.
According to Kern Liebers, the new sinker technology ensures a uniform pattern, even for highly advanced knitted fabrics. Based on its long experience as an OEM supplier for Mayer &Cie, the company has managed the perfect adjustments to reach the latest demands of the markets. This new ‘High End’ product at the highest quality level is a further completion of the worldwide biggest sinker program made by Kern-Liebers Textile.
These new developments also continue Kern Liebers’ growth policy aimed at expanding its range of available needles and other accessories as it looks to become a complete supplier to the global knitting and hosiery industries.
“ITMA 2023 will also feature a series of seminars, workshops and conferences focusing on the latest developments and trends in the textile industry,” the company added. “These events provide an excellent opportunity for Kern-Liebers Textile to learn about the latest developments in the industry and exchange ideas with other experts.Kern-Liebers Textile is proud to be a part of this important event.” At the show Kern-Liebers will be in Hall 4, Stand D203.
Pleva will present advanced technology for energy-efficiency and sophisticated processes
Make sophisticated processes transparent and efficient with PLEVATEC pro: The new, advanced process control system PLEVATEC pro allows an integration of a huge variety of process critical data with all information at one glance and optimal controls. It is designed to enhance and simplify operation even at complex production lines with different modules.
Hereby, tolerances can be set as well as parameters saved and loaded within the integrated recipe management system. The customizable system provides solutions to a huge range of processes, e.g. a production line with foulard, coating and stenter frame.
In general, an integration of the following PLEVA devices is possible:
• Exhaust humidity FSX for great energy savings
• Fabric/air temperature TDS for transparent drying/heattreatment processes
• Residual moisture RR, RF/AF for improved fabric quality and efficiency
• Application moisture/coating AF/MP for savings of valuable chemicals
• Pick/course density CAM for high quality fabric
Through the continuous process monitoring and control of the parameters, a significant optimization of even very complex production processes is possible. And by having more stable processes, a constant, high quality of the goods is ensured. This means that there are no expensive adjustments or second-choice goods, which saves valuable resources.
The smart way of weft-straightening SL smart: The SL smart is designed for knitted and woven fabrics with a plurality of solutions customizable to fit the individual customer needs. It includes options like fully-integrated accessories for tensionsensitive fabrics, Industry 4.0 applications and more. The heart of the SL smart is the well-established traversing camera technology which is unique in weft-straightening.
The high-resolution camera captures more than 20 measuring points per meter of fabric width. This gives a complete overview of the fabric instead of few fixed positions. Finally, advanced evaluation algorithms ensure an ultra-precise distortion analysis which enable perfect straightening results in a blink of time. With the weft-straightener SL smart only one round through the production line with the respective fabric is needed and the aimed result is directly produced. This, of course, also saves energy and enhances the production efficiency directly from the beginning.
The all seeing eye – CAM series 400: For the assessment of quality parameters but also weft-straightening, precise detection and advanced image processing is the most important
aspect. The brand new CAM offers cutting-edge technology with many novelties for best results: Completely new lighting with increased brightness and special lighting possibilities allow a detection of all kinds of fabric independent from density or color.
This in combination with a four times higher calculation power, higher resolution with five-times more pixels and revised algorithms for calculation of distortion and pick/course density makes it the leading technology in the area. On top, it is also designed as a retrofit for existing PLEVA systems with easy connectors and is fitted for even the harshest conditions thanks to an improved housing design.
Sizing made sustainable and efficient with updated AS 120: Sizing is the crucial preparation for weaving and high yarn quality. Therefore, sizing agents are applied with a squeezing
unit to the warps. To be on the safe side often 10-25% more sizing is applied than required. This implies disadvantages like higher use of expensive sizing agents, more wastewater, unstable yarn quality, lower weaving efficiency, etc. To eliminate those disadvantages, a measurement and control is needed.
The AS 120 measures the size add-on after size box constantly. It includes a newly designed special construction with integrated protection against steam vapours and high temperatures as well as a faster, even more precise electronic. This enables a reliable, continuous monitoring and control. As a result, 1.5% up to 4% higher weaving efficiency is easily possible and at the same time production gets greener.
Besides those new developments, PLEVA also offers special versions of sensors for special demands such as the TDS sensor for fabric and air temperature fitted for EX-zones, state of the art interfaces like Profinet and the PLEVA Remote Service for even faster support of your production. Whether for standard applications or demanding processes, PLEVA is your partner for the sustainable and efficient production of tomorrow. PLEVA is looking forward to show all highlights live in hall 11 booth A101!