KLM’s Radical Innovation Team delivering meaningful change as airline prepares for the future
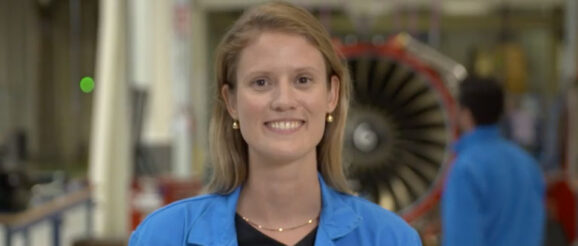
The following post was published by Future Travel Experience
KLM’s Arlette van der Veer, Task Manager Radical Innovation, talks about the benefits of the airline company’s far-flung development ecosystem.
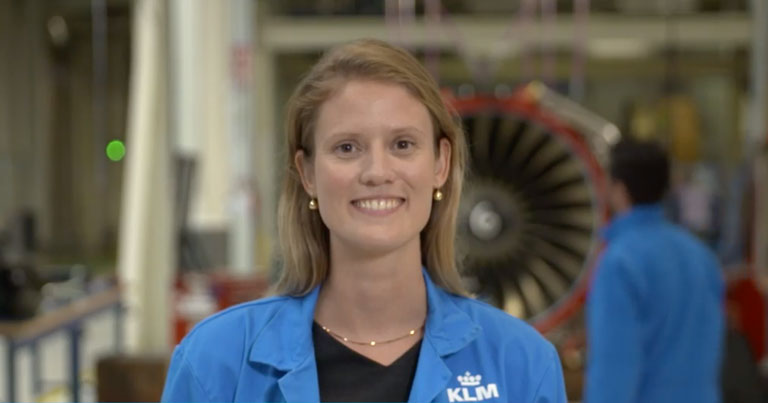
KLM Royal Dutch Airlines is not only one of the world’s earliest airlines; it is also one of the most forward-thinking. Today, regardless of the international unpredictability developed by the continuous COVID-19 pandemic and prevalent cost-cutting initiatives across the market, development stays as essential as ever to the carrier.
Within the Improvement Workplace sits the Radical Development Team, which is accountable for orchestrating the KLM development community, co-creating innovation strategy, and accelerating innovation tasks that concentrate on the most tactically essential subjects for the business.
“You do not do development at the head workplace, on the 8th floor, behind your laptop computer; you do it where the operation is and with the people who are working there,” KLM’s Arlette van der Veer, Job Manager Radical Development, explains to FTE. “We have a lot of ingenious coworkers throughout the company– they are scattered throughout all the various departments and departments.”
Development ecosystem method
Much of the innovation that is occurring within the airline is driven by 3 approaches– agile lean, design thinking and scrum– however the innovation ecosystem itself helps to guarantee that development is not performed in siloes, under the radar of other groups or departments. “Innovation community method is actually the glue to make a coherent visualisation of all the innovation present, of all the innovations and skills available, and after that you can manage it and a great deal of good things happen from it. If you’re proficient at understanding sharing the opportunities of making the best item and the right development ends up being much bigger … A development environment reveals you where the innovation is, where the innovation centers are, and it shows where you can work together.”
One example of how the development of an organisation-wide development environment is providing important outcomes can be discovered in the field of additive manufacturing. Van der Veer explains: “Within engineering and maintenance, additive production began within Engine Services. Nevertheless, it also began in Component Providers, however these people didn’t work together with each other and they weren’t knowledgeable about the fact that they were dealing with the same innovation. A development ecosystem reveals the synergies possible between associates, in between departments, on topics and innovation jobs.”
When the Radical Innovation Team understood that there was no additive manufacturing vision in place across Engineering & & Maintenance, action was rapidly taken. They hosted additive production vision workshops per department, which developed a lot of data and a long dream list. This info was then consolidated and the team organised a workshop for the essential management in Engineering & & Maintenance. As the management already knew the wishes of each of the departments, within simply 3 hours they agreed upon an additive production vision for the entire of KLM Engineering & & Upkeep. In addition, they recognized that they needed to prioritise something above all else; building 3D design ability within business.
Since then, a series of projects have actually been effectively completed, possibly most especially the application of a circular additive production procedure which uses recycled plastic bottles from KLM flights to ultimately produce and print tools for airplane upkeep. This is just one example however comparable success stories exist across numerous departments.
The Radical Development Group has actually also established the Innovation Environment SharePoint, which will be launched in mid-September. This online one-stop-shop provides the KLM workforce with information on which themes and technologies are presently being checked out, checked and executed. Ranging from robotic procedure automation to drones, the “knowledge base”, as van der Veer describes it, is broad varying. As browsing for info and motivation, colleagues can publish questions and find colleagues who may be able to provide competence on a particular topic.
Integrating strategy and innovation
The Radical Development Group has the ability to help deliver really meaningful innovation thanks in part to the structure that it sits within. The Method Office is also within the Improvement Workplace. “The great thing is they are my direct coworkers,” states van der Veer. “On paper we are two separate teams, however we work a lot together, since you see that some strategy questions or choices you make are sustained by technological developments or developments that you wish to implement … We make sure that our developments are aligned with the method team.”
Not all airline companies– nor airports, for that matter– see the holistic value of development in the manner in which KLM does. Some have minimized their development spending plans as part of current cost-cutting measures. In van der Veer’s opinion, there is much more to innovation than investing money on relatively futuristic jobs.
“I believe there is just one option and that’s truly concentrating on understanding sharing,” she informs FTE. “People believe that to be able to purchase innovation you require cash. Of course, you need cash if you need innovation developments, but when times get difficult that’s not the only choice you have … knowledge is also extremely, really important.”
Together with the style believing innovation programme with the University of Technology of Delft, KLM is partnering with the Technical University of Twente to attend to a shortage of data scientists within the organisation. “We are going to kick-off a program in October with crucial cargo associates wanting to co-create a minimum viable item on a data algorithm we’re taking a look at for freight clients,” van der Veer describes. “We have all the market understanding, the only thing we lack is the actual information researchers who will develop the algorithm and that’s why we’re working together with universities. They have students who are lacking in global experience who can not presently do any internships, who can not graduate at companies, and so this is what we’re doing right now.”
Overcoming legacy systems and state of minds
Naturally, the global background does look bleaker than anyone anticipated at the start of the year, but van der Veer hopes the market can take some important lessons from the COVID-19 crisis. Increased diversity– covering everything from the gender balance and new mindsets, to ethnic background and the variety of universities closely aligned with the sector– is on her own desire list, as is a desire to see the market embrace much-needed modification.
“I think that with all crises, it really lays bare the weak points of a business or a market,” she says. “The weak points in our market are the tradition systems and legacy mindsets that are obstructing development. The industry has a very clear purpose– we are here to take individuals and freight securely from A to B. Whatever else is secondary. If it’s not safe then we can just stop.
“However, many of these guidelines and frame of minds were created 50 years ago. Then we didn’t have the technological advancements that we have now, we didn’t have the computer programmes or quantum computing that we have now, we didn’t have forecasting models or 3D programs that enable us to test ideas essentially initially, but we’re still handling the mindset that was developed 50 years ago. I hope that since of the crisis, we are going to change our state of mind. Nevertheless, what is never ever going to change is that it constantly needs to be totally safe– that is always the top thing. In 2020, we can test and we can try out brand-new technologies while being safe which is the huge difference. I hope that we, as an industry, become more nimble in screening and exploring in the improvement that this industry truly desires.”
While the overall state of the air transport sector in one, 2 or 5 years’ time can not be properly forecasted today, one thing that is specific is that KLM will continue to place its faith in innovation as it continues to look for new methods to optimise effectiveness and provide enhancements across business.
Article originally published here:
KLM’s Radical Innovation Team delivering meaningful change as airline gets ready for the future