Langley Air Force Base opens a lab to encourage innovation
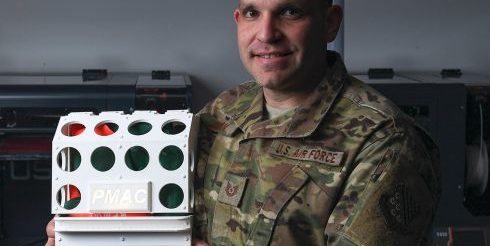
NEWPORT NEWS, Va. (Tribune News Service) — Air Force Tech Sgt. Daniel Caban doesn’t fly the F-22 Raptor, but his soaring imagination could benefit the stealth fighter all the same.
A maintenance crew chief at Langley Air Force Base, Caban has developed a new way to shield intakes on Raptor jets parked on the ground. It utilizes a flexible cover ringed by a series of magnets that attach firmly to the aircraft.
Langley leaders like what they see. In fact, they want to stoke that innovative fire among more airmen.
That’s why base personnel gathered Tuesday to open a new innovation lab so airmen can brainstorm and develop other problem-solving ideas. The immediate goal is to find ideas that help Langley’s 1st Fighter Wing.
But Caban’s idea has potential to help the entire Raptor fleet.
Base leaders found space for the lab by converting a storage room and filling it with computers, 3-D printers, soldering and coding stations, and electronic robotics gear.
“We’re just excited to bring this to our airmen,” said Maj. Brian Pascuzzi, 1st Fighter Wing innovation chief. “Even if they have a problem, we want them to come talk to us.”
The idea of empowering younger airmen to come forward is somewhat of a culture change, and Pascuzzi admits he was skeptical at first. That changed last year when he attended a symposium in Las Vegas sponsored by AFWERX, the innovation hub of the service.
He watched as an airman took out his phone, unlocked his lab in New Jersey and started a 3-D printer.
That experience made him a believer.
The lab is looking for quality, not quantity. A brainstorming success rate of 5% to 10% would be welcomed if the results equal what Caban has devised, which potentially could save the Air Force millions of dollars.
Caban’s idea predates the innovation lab itself. He presented it in March during a pitch session before the base’s innovation board, which consists of senior leaders. It generated an immediate buzz, Pascuzzi said.
Caban said he’s gratified the idea has taken off, but he might not be finished. The concept might work on commercial jets, too.
“I’ve started designing some civilian ones,” he said.
Covering intakes on jet engines is important because debris, birds or other foreign objects could pass through the opening and damage the engine. The current cover system consists of bulky foam pads that measure 13.1 cubic feet and cost $11,000 each. Each jet that deploys requires three sets to make sure the sensitive openings are shielded at different landing sites.
Caban’s design goes by the acronym PMAC, Portable Magnetic Aircraft Covers. The production cost is less than half of the foam pads. Equally important, his system is collapsible and fits inside a small compartment on the jet itself. The bulky foam intakes must be shipped separately.
When Raptors need to deploy in a hurry — to escape a hurricane, for example — it’s much more efficient to have the intake covers stored in the aircraft rather than wait for a separate shipment. Caban said he’s seen Raptor intakes protected with plastic and masking tape in a pinch because the foam pads weren’t immediately available.
Pascuzzi said he hopes more ideas will bubble up from the grassroots now that the innovation lab is up and running. All personnel are invited.
“The whole point of this is to engage our airmen,” he said.
Langley is calling its lab a “spark cell.” Leaders hope that Caban’s PMAC will be selected as a finalist for the 2020 Spark Tank competition during the Air Force Association conference in Orlando, Florida. He should know sometime next month.
hlessig@dailypress.com
©2019 the Daily Press (Newport News, Va.)
Visit the Daily Press (Newport News, Va.) at www.dailypress.com
Distributed by Tribune Content Agency, LLC.