Little Rock AFB Airman sparks 3D printed innovation for C-130 fleet | Mirage News
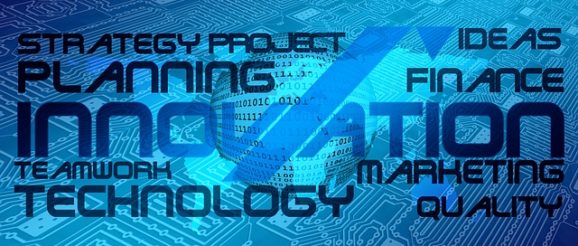
One of those Airmen is Tech. Sgt. Ryan McBride, 19th Maintenance Squadron noncommissioned officer in charge of metals technology. He pursued his innovation by collaborating with the to 3D print a hydraulic pump bracket for the .
His idea came to fruition on June 4, when the bracket became one of the first 3D printed metal parts to be installed on the C-130J.
The bracket is designed to hold the C-130J’s manual hydraulic pump, a device that allows for lowering or raising the ramp with a hand pump when the aircraft is powered off or the hydraulic system fails.
McBride explained that during his time working on C-130Js, he found himself and his team having to manufacture the bracket at an alarming rate due to the immense force required to operate the pump.
“With its current design, the bracket can withstand very minimal side loading from the pump handle,” said 1st Lt. Jesse Montgomery, Air Force Life Cycle Management Center C-130 structures engineer. “Because of this, an estimated 30 to 40 brackets break per year and must be locally manufactured which is a very difficult and time-consuming process.”
The re-creation of the bracket provided an opportunity to completely revamp its structure and strength to decrease the number of repairs needed over time.
“Lab testing has shown the new 3D printed part can withstand three times the downward force and 10 times the side force compared to the original bracket, making it much less likely to break in the field,” Montgomery said. “The 3D printed version also costs an estimated $3,800 less per part to make and requires significantly fewer man-hours to produce.
“It also showcases the power of 3D printing in using complex geometry to improve strength and reduce costs, which would not be possible using traditional manufacturing,” Montgomery continued.
McBride said 3D printing the bracket will make it easier for C-130J maintenance units across the Air Force to obtain the part and eliminate the need to manufacture it themselves.
“Pending successful field testing, the bracket can be mass-produced for the supply chain,” he said. “Once approved, we will be able to order already printed parts that are ready for installation.”
McBride added that as 3D printing becomes more prevalent, it has the potential to become more commonplace for engineering and manufacturing aircraft parts at a cheaper and more efficient rate.
“This introduces people to the benefits of 3D printing aircraft parts,” he said. “This is just the beginning. It’s still a fairly new technology, but it’s becoming much more readily available.”
Montgomery said as older models of aircraft continue to age and production of parts become less prevalent, 3D printing is seen as a potential solution to future limitations within the supply chain.
“Hopefully this part serves to spark the creativity of C-130 units across the Air Force once they see the capabilities of 3D printing and its broad applications for Air Force aviation,” he said.
Airmen like McBride contribute to the innovative culture of the Air Force, embracing a standing challenge posed to the force by .
“Our heritage of success is based on innovation made possible by our diverse group of professional, dedicated and warrior Airmen,” Goldfein said in a service-wide message. “Airmen are the strength of the Air Force. I challenge each of you to take deliberate steps toward expanding your understanding of this new national security environment, the threats we will face and the tools we will need to prevail. Your dedication and commitment to expand your understanding ensures we remain the best Air Force the world has ever seen.”