Manufacturers Undertake a Course Correction on Innovation
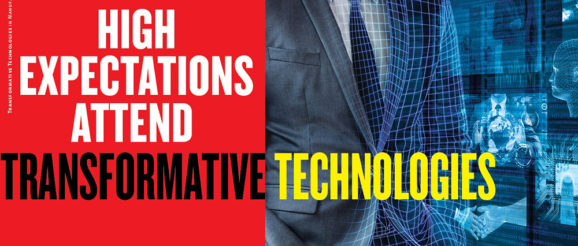
The Manufacturing Leadership Council’s latest survey on Manufacturing 4.0-related technologies reveals that companies are expecting big things from the IIoT, analytics, 3D printing, and other new technologies. But few are approaching their adoption strategically. By David R. Brousell
Over the next five years, manufacturers see a range of new technologies fundamentally changing they way they produce products. Whether it is the Internet of Things, 3D printing, or artificial intelligence, manufacturers expect these and other technologies to be potential game-changers in their operations.
At the same time, though, the path to realizing these changes for many manufacturers is anything but well paved. Few manufacturers have formal technology roadmaps in place today. Responsibility for devising and implementing technology strategies and their roadmaps is often diffused and unclear. And, particularly for small and medium-size companies, the capacity to evaluate and understand the potential of a growing set of new technologies emerging on the industrial scene is often lacking.
These are some of the key findings of the Manufacturing Leadership Council’s latest survey on Transformative Technologies in Manufacturing, one of the Council’s Critical Issues facing the industry. Survey respondents weighed in on the potential of new Manufacturing 4.0-related technologies, their investment plans, their challenges around adopting and using technologies, and where they think they stand in relation to competitors at this stage in the M4.0 journey.
The View in 5 Years
Today, many manufacturing organizations are at the beginning of the learning curve of understanding and realizing the potential of new production and information technologies. This is not to be unexpected. It takes time, experimentation, and experience to leverage capabilities in a new analytics software program or production platform.
But imagination has been unleashed. Manufacturers are seeing game-changing potential over the next few years in a range of technologies that will be used on factory and plant floors.
Take the Industrial Internet of Things. Today, only 16% of survey respondents think that the IIoT, which involves IP-enabling plant floor equipment, is a game-changer in their production operations (Chart 10). But over the next five years, that number catapults to 40% expecting a fundamental impact from the technology.
Over the next two years, manufacturers are looking to invest in a mixed bag of IT-related technologies.
A similar acceleration in expectations occurs with other M4.0 technologies. Only 10% of survey respondents today believe that artificial intelligence and machine learning, for example, are having a transformative impact in their operations. Over the next five years, however, a near-tidal wave builds as the number soars to 49% of respondents expecting that AI and machine learning will be a game-changer for their companies.
This quantum leap effect is evident with 3D printing technology, Big Data and advanced analytics software, and collaborative robots, all of which will enable manufacturing operations to become more information-driven, automated and autonomous, and flexible in how they produce products.
Near-Term Purchase Plans
Over the next two years, manufacturers are looking to invest in what has turned out to be a mixed bag of IT-related technologies, including already well-entrenched products such as enterprise resource planning (ERP) and manufacturing execution system (MES) software.
ERP and MES software have been in use in manufacturing companies for a long time, but many systems in place have aged. There is an increasing realization among these companies that, in order to move ahead with M4.0, these back-end systems need to be modernized first. As a result, the survey results indicate fairly robust investment intentions in these technologies in the years ahead.
But equal if not stronger intentions lie with some of the newer technologies (Chart 1). Artificial intelligence technology, for example, is in use in only 16% of survey respondent companies today, but over the next two years, 26% expect to invest in it, the strongest buying intention among 10 technologies examined in the survey. Not too far behind is augmented reality and virtual reality systems. Today, only 16% say they have already invested in these systems. Within the next two years, 19% say they will do so. Blockchain is another interesting example. Only 1% of survey respondents say they are using blockchain today, but 16% expect to invest in it over the next two years.
Part 1: Technology Investments and Plans
AI, MES Slated for Investments in Next 2 Years
Q: Please indicate your company’s investment posture for the following IT-related technologies.
Q: Please indicate your company’s investment posture for the following communications and networking technologies.
Predictive Maintenance, Machine Learning Top Production Plans
Q: Please indicate your company’s investment posture for the following production technologies.
Part 2: The Technology Assessment Process
Most Have Not Yet
Developed M4.0 Roadmaps
Q: Has your company developed a formal M4.0 roadmap to support transformative technology adoption?
Tooltip Text
Informality Attends Most M4.0 Roadmap Approaches
Q: Which statement best describes your company’s
current approach to adopting a M4.0 Roadmap?
Within the realm of communications and networking technologies, IIoT-related technologies, now in use in 36% of respondent companies, will see significant growth as another 34% of respondents make investments in the technologies (Chart 2). And on the factory floor, predictive maintenance, IoT, machine learning, and collaborative robots garner the strongest buying intentions in the years ahead (Chart 3).
Along the way, manufacturers will be seeking competitive advantage from the technology, an edge, if found, that is always hard to sustain over time as new technologies emerge and the adoption/value cycle begins again. Right now, only about one-third of survey respondents say they are ahead of their competitors in the adoption of M4.0 transformative technologies. A nearly equal percentage says they are about equal with their competitors and 17% say they are behind (Chart 8).
The Challenges Ahead
Best intentions aside, the technology assessment process currently in place in many companies could end up being a constraint on adopting and deriving value from many IT and operational technologies.
At this point in time, only 6% of survey respondents say they have a formal roadmap for M4.0 transformative technologies in place in their companies. Another 11% say they are working on such roadmaps, while 39% say roadmaps are under consideration but not yet started (Chart 4).
What’s apparently going on in some companies is that different groups within companies are investing in specific technologies often to deal with immediate issues. This reactive, tactical approach was cited by 70% of survey takers (Chart 5).
Tooltip Text
Responsibility for M4.0 Roadmaps is Diffused
Q: Who is responsible for implementing your M4.0 roadmap/strategy?
Tooltip Text
Majority Indicates Difficulty
in Vetting New Technologies
Q: Please indicate the extent to which you agree with the following statement: The accelerating pace at which new technologies are emerging is causing us to fall behind in our efforts to evaluate and understand their potential.
Tooltip Text
Less Than One-Third Think They are Competitive With M4.0
Q: Where do you think your company stands in relation to its primary competitors’ adoption of transformative M4.0 technologies? (Check one)
Tooltip Text
Measuring ROI, Assessing Cost/Benefit Are Top Challenges
Q: What are the most significant challenges related to adopting and using M4.0 technologies?
Part of the challenge here may be found in survey findings regarding who within manufacturing companies has responsibility for M4.0 technology strategy and road-mapping. The picture appears to show a diffusion of responsibility. For example, 26% of the survey respondents identified their CEO as the responsible executive, which certainly makes sense in smaller manufacturing companies where the CEO is wearing many hats (Chart 6).
But even more, 36%, said it is their chief operating officer or manufacturing head. Thirteen percent said their plant manager had the responsibility and 9% identified their CIO as the responsible authority.
Layered on top of this issue is the challenge of measuring the impact and effectiveness of M4.0 technologies, an issue that has cropped up in prior surveys. The most significant challenge with the technologies, say survey respondents, is in measuring the return on investment, followed by assessing cost/benefit, and migrating from or integrating with legacy systems still in place (Chart 9).
Taken as a whole, though, these challenges are pretty typical of the cycle that always surrounds the adoption of new technologies. Over time, as they get more experience with the technologies, manufacturers will get better at deriving benefits and measuring both hard and soft returns.
As they do, one challenge that has all the markings of an issue that seemingly will become more pronounced over time is the growing wave of data that is inundating companies. With now near-ubiquitous connectivity and more instruments in place for generating data from both objects and people, today’s manufacturing enterprise is hard at work to not only hold back the flood but also to manage its flow in ways that will benefit the business.
This is no easy task as the data volumes grow. The survey has revealed the dimensions of the problem. When asked how well prepared their companies are to organize, evaluate, and make decisions on the volumes of data that are or will be generated from greater connectivity of devices and equipment, only 9% of survey respondents indicated that their organizations were well prepared today. Another 44% said moderately prepared and 39% said poorly prepared (Chart 15).
This may very well be the chief challenge of our digital age. We asked for more information. Now, we are going to have to figure out what to do with it. M
Tooltip Text
Strong Potential Seen for the IIoT
Q: What is your assessment of the potential of the Industrial Internet of Things IIOT), specifically IP-enabling your plant floor equipment and products, both today and in five years time?
Tooltip Text
Nearly a Majority Sees 3D as a Game-Changer Ahead
Q: What is your assessment of the potential of 3D printing, both today and in five years time?
Tooltip Text
Potential for Analytics Seen
as Strong in Next 5 Years
Q: What is your current assessment of the potential of Big Data/advanced analytics, both today and in five years time?
Tooltip Text
Q: What is your current assessment of the potential of collaborative robots, both today and in five years time?
Tooltip Text
Q: What is your current assessment of the potential of
collaborative robots, both today and in five years time?
Tooltip Text
Only a Fraction Say They Are Well Prepared for the Data Tsunami
Q: How prepared is your company to organize,
evaluate, and make decisions on the volumes of data that are or will be generated from greater connectivity of devices and equipment?
Tooltip Text