Pioneering the future of aerospace with sustainable innovation
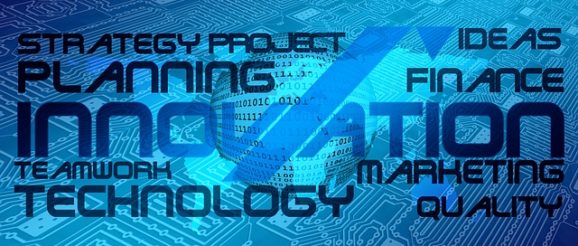
By Ivan Kudrenko, Senior Supply Chain Analyst, Boeing. In the fast-paced world of supply chain management, the recent surge in automation within warehousing stands as a testament to the industry’s adaptability and innovation. A groundbreaking study reveals that over 60% of warehousing leaders globally view automation as essential for reducing errors and meeting service-level agreements, while 68% see it as a solution to labour shortages. These statistics underscore a pivotal shift towards technology-driven efficiency in logistics and a myriad of exciting opportunities in supply chain management. Among these, the aerospace sector, known for its stringent demands for precision and reliability, has witnessed a remarkable resurgence fueled by technological advancements and strategic ingenuity. Professionals with engineering backgrounds, like Ivan Kudrenko, have emerged as pivotal figures in the evolving landscape of the aviation supply chain’s revival. With over a decade of experience in the manufacturing and aerospace industries, Ivan has led numerous impactful operations and supply chain improvement projects. Currently, he serves as a Senior Supply Chain Analyst at Boeing, a global leader in aerospace, which he joined in 2023 after completing a pivotal summer internship at the company. In a conversation with Ivan, we explored the supply chain challenges in aerospace, the high-level differences between manufacturing and aerospace supply chain management, and his experience in the aviation sector today, shedding light on the path forward for the industry. Hello, and thank you for taking the time to speak with us today! As we all can see the tectonic shifts in supply chains across multiple industries, what is your take on the current challenges in the aerospace and manufacturing sectors? Thank you for having me! The aerospace and manufacturing sectors face several significant challenges in their supply chains. Firstly, the volatility in demand patterns, exacerbated by global events such as the pandemic and geopolitical tensions, has made forecasting and inventory management increasingly complex. This unpredictability can lead to either stockouts or excess inventory, both of which are costly for companies. Secondly, the global nature of aerospace and manufacturing supply chains means that disruptions in one part of the world can have ripple effects across the entire network. Issues like port congestion, shipping delays, and customs clearance complications can lead to extended lead times and reduced supply chain reliability. In warehousing, the challenge is not only about managing space and inventory levels but also about optimizing operations for efficiency and speed. Adopting automation and advanced technologies like AI and robotics is crucial but requires significant investment and integration effort. Furthermore, the push for sustainability is driving changes in logistics and warehousing practices. Companies are exploring more eco-friendly transportation options, sustainable packaging solutions, and energy-efficient warehousing operations, which require rethinking traditional approaches. Navigating these challenges requires a strategic approach emphasizing flexibility, resilience, and innovation. The aerospace and manufacturing sectors can adapt and thrive in this dynamic environment by leveraging technology, reevaluating supply chain partnerships, and prioritizing sustainability. Given the unique challenges the aerospace sector faces, particularly in logistics, warehousing, and the heightened focus on sustainability, how are companies within this industry adapting their supply chain strategies to address these issues effectively? I would like to point out that these sectors have certain similarities and differences. The aerospace and manufacturing sectors both face challenges in logistics and warehousing, but the complexity is heightened in aerospace due to specialized components, longer lead times, and stricter regulatory requirements. The aerospace industry’s reliance on international suppliers and its products’ high value and sensitivity demand specialized warehousing solutions, which make its supply chain more vulnerable to geopolitical risks. Additionally, the environmental impact of aviation amplifies the focus on sustainable practices in logistics and warehousing, further differentiating the challenges in the aerospace sector from those in general manufacturing. Mr. Kudrenko, I am encouraged by your career advancement from a Team Lead in the manufacturing industry to a senior supply Chain Analyst at Boeing. What was the driving force behind embarking on a career as an engineering and operations expert? Growing up in a family of engineers, I naturally adopted a problem-solving mindset, learning to tackle complex problems early on by breaking them down into smaller, manageable tasks. My curiosity was piqued by the projects my parents worked on, and from a young age, I couldn’t see myself in any profession other than engineering. My fascination with coding and programming quickly led me to the world of web design, which felt like exploring new territory. At 12, I created a website for football fans, applying the HTML and PHP skills I had picked up. This was well before online courses, so I continued refining my web development and programming skills. Great beginning! Given your early successes in self-education, what led you to pursue such a comprehensive educational path from Kuban State Technological University to the University of Strathclyde in Glasgow and the University of Michigan? It is a great question! Since a young age, I’ve found joy in navigating and designing complex systems. However, I persisted in believing in the value of formal education, seeing it as a means to deepen my understanding in a structured way. After school, I was accepted to the Kuban State Technological University in Russia, focusing on honing my engineering skills. This evolved into a transformative chapter with a master’s in Electrical Engineering and Business Management at the University of Strathclyde in Glasgow, UK. During my studies in Scotland, I had a chance to work on a project involving detecting partial discharges in oil-filled electrical equipment, a venture that significantly influenced my career path. I created a system to detect partial discharges in oil-immersed power equipment from the ground up. Identifying these discharges early can prevent severe failures and lead to substantial cost savings. That was an aha moment since I realized how science can be applied to real-world problems. As my career progressed, I realized the importance of a strong business foundation to grasp various business perspectives and manage large-scale projects effectively. This led me to pursue my dream MBA program at the Ross School of Business at the University of Michigan, specializing in operations and supply chain management. It was a life-changing experience! Interestingly, my journey has come full circle as I now assist the admissions office as an alum interviewer. Volunteering allows me to support the school’s mission by admitting students eager to make a difference and expand their business acumen. It’s an honor to assess prospective students and introduce them to the school and the career possibilities in operations and supply chain management. Mr. Kudrenko, after getting a master’s degree in the UK, you started working in the Krasnodar manufacturing company. Your strategic management led to 35% cost savings during the currency crisis. Could you reflect on the pioneering innovation that continues to drive improvement? Yes, that’s right. It was the time when my professional interests switched from electrical engineering to business and supply chain management. My previous company encountered significant challenges due to a major devaluation of the local currency, disruptions in established supply chains, and uncertainties with our European suppliers. The entire manufacturing industry was grappling with a heavy reliance on foreign components, increasing costs. In response, I took the initiative to establish our first international supply chain for sourcing components from China, bypassing costly intermediaries. This innovative approach was a first in the industry and gave our company a competitive edge. I developed a strategic sourcing framework to identify and evaluate international suppliers and to build mutually beneficial partnerships. This framework employed a mix of quantitative and qualitative metrics to ensure informed decision-making and effective strategic sourcing. Initially, we established a strategic and systematic framework for our sourcing process, allowing decisions to be made based on objective criteria. This methodology facilitated accurate estimation of current purchasing requirements, identification and assessment of potential suppliers, allocation of human and financial resources, risk mitigation, and informed make-or-buy decisions. This structured approach was integrated into a software application, enhancing the transparency and efficiency of our sourcing operations over several years. At that time, you led one more successful project, which reduced defects by 80%, substantially improved overall equipment efficiency, and nearly eliminated equipment breakdowns. Could you share some insights into the innovative strategies you implemented? At the heart of our success was the transformative influence of Kaizen, a philosophy that revolutionized our manufacturing processes. I was fascinated by Lean principles and determined to prove that they were applicable in the automotive industry and our make-to-order environment. With Kaizen tools, we precisely forecasted maintenance needs through enhanced preventive maintenance, optimizing operational efficiency. The 5-why tool in Root-Cause Analysis empowered us to modify processes swiftly, boosting team performance. A game-changer was the implementation of Production Line Balancing, which elevated equipment utilization and streamlined our production. We faced challenges strategically. It was crucial to gain buy-in from both leadership and workers, communicate effectively with various stakeholders to address their needs and maintain persistence and discipline to introduce change. The journey with Kaizen has elevated efficiency and underscored the power of continuous improvement and collabourative problem-solving, marking a new era of success in our production endeavors. While leading this initiative, I recognized my aspiration to pursue an MBA in the USA to learn how to see the big picture and manage all processes. During my studies, I interned at Boeing. Absolutely. Your contribution during the internship led to the company’s saving over 50 million dollars over the next three years, which speaks volumes. Given your extensive background, how does the intersection of technical knowledge and practical insights help you to drive innovation? My background intersects with my engagements. I am reviewing conference papers for Logistiqua 2024, an international supply chain conference. Additionally, I have recently become a member of the team of peer reviewers at the International Journal of Information Systems and Supply Chain Management. It helps me to gain insights into the latest trends and innovations in supply chain management, ensuring that my knowledge remains up-to-date and relevant. Joining the team of peer reviewers at the International Journal of Information Systems and Supply Chain Management further enhances my understanding of cutting-edge research and allows me to contribute to the scholarly advancement of the field. I’m deeply engaged in merging theoretical knowledge with practical applications, with a keen focus on electrification, automation, blockchain, and sustainability within the dynamic field of supply chain management. Exploring the nuances of electrification and automation, inspired by the aerospace industry’s advancements in electric vehicles, has become a pivotal aspect of my work. Simultaneously, my interest in blockchain technology empowers me to assess and implement innovative solutions in supply chain management, enhancing security, transparency, and efficiency. Beyond technological realms, my commitment extends to sustainability initiatives, where I translate theoretical advancements into tangible, eco-friendly practices in warehousing and broader supply chain operations. Mr. Kudrenko, this multifaceted approach contributes to the sector’s resilience and elevates the United States’ global competitiveness and innovation. You’ve recently participated in the TITDS-XIV-2023 conference. How do you envision this intersection shaping a more resilient and sustainable future for American industries? Embarking on this research journey has been truly enlightening. The convergence of manufacturing, technology, and sustainability in my work has allowed me to dissect complex challenges and provided strategic frameworks for overcoming them. Reflecting on the interdisciplinary nature of my efforts, I envision this holistic approach as a catalyst for reshaping the future of American industries—infusing resilience and sustainability into their core. How do I see this intersection influencing the paradigm shift towards a more sustainable and resilient future for our industries? There isn’t a universal solution, as the appropriate response varies by sector, stage of business, supplier network, and other factors. Yet, the pandemic and geopolitical tensions have highlighted how much US and European companies depended on international suppliers and standard practices. This reliance led to issues like the bullwhip effect, excessive inventory during transit, soaring freight costs, disorganized sourcing practices (where sustainability and quality often took a backseat), and widespread inflation. Ideally, relocating the production of essential items like EV batteries, semiconductors, and aerospace components back home could safeguard critical sectors and national interests. But, such moves might only sometimes be practical or affordable. In these instances, nearshoring presents a viable option, as does adopting a sourcing strategy from multiple suppliers. I’m keen to explore and conduct a comparative analysis of these risk management approaches within a specific industry. I notice it as planting the seeds for a future where we make things brighter and kinder to the Earth. As a final question, Mr. Kudrenko, what projects are you looking forward to in the coming years as you reflect on your career? As I look ahead, my vision involves leading the integration of blockchain, AI, and sustainable practices in the aerospace industry. I am excited about initiating a pilot project at Boeing that will demonstrate the feasibility and benefits of these technologies, setting a new standard for innovation in our industry. Specifically, I am eager to explore how AI can revolutionize warehousing operations, enhancing visibility and sustainability. AI-powered analytics and automation can significantly improve the speed and accuracy of order fulfillment while reducing waste and costs. I am also passionate about boosting supply chain resilience through AI by enabling real-time monitoring and analyzing various factors that could disrupt operations. By leveraging AI for predictive analytics and risk management, we can ensure operations continuity and minimize disruptions’ impact. Finally, sustainability is a key focus in my operations and supply chain management approach. Integrating AI can help reduce waste, energy consumption, and carbon emissions. By optimizing transportation routes, reducing packaging waste, and identifying opportunities for recycling and reuse, we can make significant strides toward a more sustainable future for the aerospace industry. Recently, I completed a research paper on reusable packaging in the aerospace industry, which is currently under peer review in an international journal. Author: Ivan Kudrenko. With over a decade of experience in the manufacturing and aerospace industries, Ivan has led numerous impactful operations and supply chain improvement projects. Currently, he serves as a Senior Supply Chain Analyst at Boeing, a global leader in aerospace, which he joined in 2023 after completing a pivotal summer internship at the company.