Powering Innovation: Advancing America’s Battery Technology
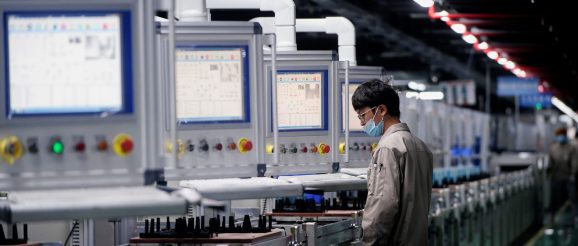
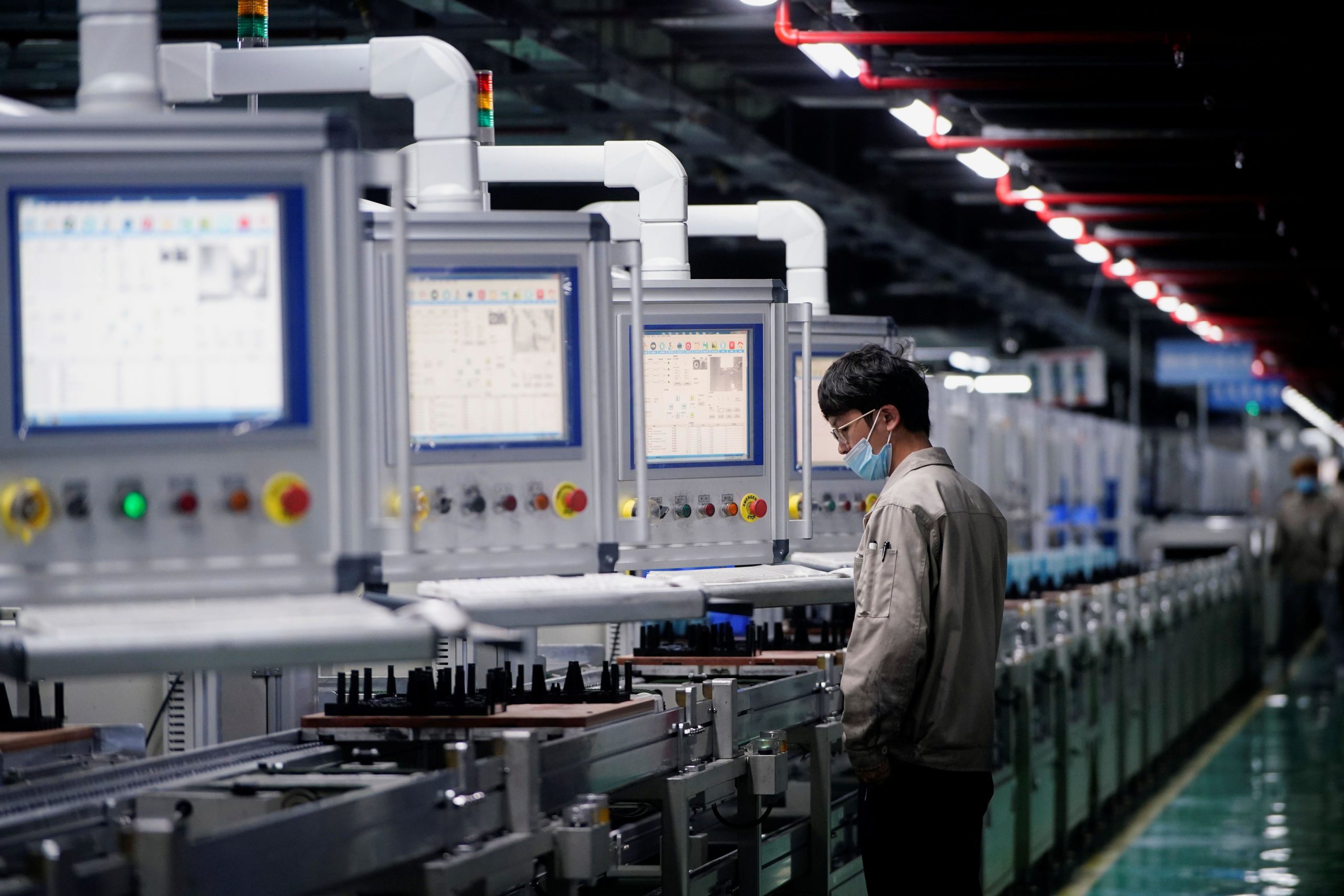
Changing consumer preferences and government policies point toward widespread future adoption of electric vehicles (EVs). Advanced lithium batteries are the primary power source for EVs. Unfortunately, China dominates today’s battery supply chain, from the extraction and processing of critical minerals like lithium to the production, packaging, and recycling of battery cells. In today’s era of great power competition, control of the supply chains for advanced technologies such as lithium batteries will have a direct impact on national power. Advanced battery technology will go a long way toward determining economic leadership in the EV market. The automobile industry is one of America’s largest manufacturing sectors and accounts for some 3 percent of U.S. GDP.
But EVs and advanced batteries also have important military applications. EVs will function as mobile energy nodes on the battlefield, providing power for unmanned systems, communication links, electromagnetic warfare systems and more. These capabilities will help the U.S. military conduct more decentralized operations in contested regions. Beijing long ago predicted the strategic shift from fossil fuels to renewable energy sources and, in response, has spent years tightening its grip on the supply chains for this critical technology. If the United States desires to grow its EV industry, and fully capitalize on the military capabilities that batteries offer, policymakers must develop a national battery strategy that:
Makes and encourages investments in mining, processing, battery production, and recycling. Given the strategic importance of batteries and their inputs, government support is necessary to build a robust American battery industry. Policymakers should leverage diplomatic and economic tools to work with friendly countries to ensure a sustained source of critical minerals, plus offer incentives for domestic mining and processing firms, cathode and anode manufacturers, and battery producers.
Drives innovation in mineral substitutes, next-generation battery technologies, and manufacturing methods to minimize supply chain vulnerabilities and leapfrog Chinese suppliers. The U.S. must develop alternate battery chemistries to substitute for costly or scarce minerals, boost R&D for next-generation battery technologies and increase funding for improved manufacturing techniques for lithium-ion batteries.
Uses DOD tools to strengthen the supply chain for military batteries, with a goal of putting new capabilities in the field. DOD must employ its policy tools to secure the supply chain for military-grade batteries, which are built to more extreme specifications than commercial versions.
Invests in workforce development and talent programs across the supply chain. The U.S. should cultivate domestic battery talent by investing in educational opportunities, supplemented by foreign expertise where necessary.
Understanding the Supply Chain
The United States controls only a tiny fraction of the advanced battery supply chain. China dominates much of the mining and processing of critical minerals as well as cell manufacturing and battery assembly. These bottlenecks grant Beijing significant strategic leverage: given the CCP’s penchant for economic coercion, it is not difficult to imagine how China could weaponize the battery supply chain against the United States. The battery supply chain begins with the production of critical minerals, such as lithium and cobalt. Key metals must be extracted from mines, then chemically processed and refined in special facilities. These refined minerals are then used to create battery cells. Once cells are produced, they are combined to form modules, which are then wrapped into battery packs—a process that takes place in dedicated “megafactories.”
The last stage of the battery supply chain, recycling, comes about during the end-of-life cycle. Critical minerals make up between 50 and 70 percent of the cost of an EV battery.
Currently, the United States lacks the capability to produce and refine many of these minerals, while China remains the leading global producer. In 2018, the U.S. Geological Survey released a list of thirty-five mineral commodities considered critical to the economic and natural security of the United States. That list includes most of the minerals considered critical to the production of lithium-ion batteries: cobalt, lithium, manganese, and graphite.
Cobalt: Under the CCP’s “Go Out” investment strategy, China has sought to secure critical minerals from around the world for its rapidly growing EV industry. This is evident in the global competition for cobalt production. Cobalt is one of the most potentially problematic inputs for lithium-ion batteries, as production is concentrated in politically unstable regions: almost 72 percent of the mined production of cobalt comes from the Democratic Republic of the Congo (DRC). This is problematic due to humanitarian concerns, as reports suggest that child labor is still used in some Congolese cobalt mines.
While very little cobalt mining occurs domestically in China, Chinese companies have acquired stakes in foreign mines, particularly in the DRC, as well as Papua New Guinea and Zambia. Eight of the fourteen largest cobalt mines in the Congo are now Chinese-owned, accounting for more than half of the country’s output. Thanks to the equity positions Chinese companies have acquired in foreign mines, “Go Out” policy activities have reduced China’s reliance on cobalt imports from 97 percent to 68 percent.
In addition to investing in the foreign mining of cobalt, China dominates the upstream processes of cobalt supply. Cobalt must be chemically processed and refined before it can be used to make batteries. In 2019, China accounted for 82 percent of the chemical processing and refining of cobalt supply. Just three Chinese firms are responsible for 46 percent of the world’s total output.
Lithium: Lithium consumption for batteries has increased significantly in recent years, and as the world transitions toward EVs, demand for the mineral is expected to spike. A recent report from McKinsey & Company anticipates a 340 percent increase through 2050, with 79 percent of growth projected to come from battery demand. Today, most lithium mining is concentrated in Latin America and Australia; however, Chinese companies acquired mining operations in these countries to the point where they control much of the supply.
Chinese mining giant Tianqi Lithium, for instance, owns a 51 percent stake in the world’s largest lithium reserve, Australia’s Greenbushes mine. Ganfeng Lithium, another Chinese mining giant, completed a deal in 2019 to secure 50 percent of one of the world’s largest high-grade reserves at Mt. Marion mine in Australia. As a result of these efforts, China now holds direct or indirect control over 70 percent of the global lithium supply. Once mined, lithium, like cobalt, must be processed and refined in specialized facilities. China is also the dominant player in this step, refining 59 percent of the world’s lithium in 2019.
The U.S. has the potential to develop a lithium supply chain.
One American company, Albemarle, is among the world’s largest lithium companies and owns the only operational lithium mine in the United States. While sources of lithium are relatively abundant in North America—the U.S. has the fourth-largest reserves in the world —there are significant barriers for American companies associated with its extraction.
Many of these challenges are environmental and political: in January 2021, for instance, a second domestic lithium mine site was approved by the Trump administration, but it has faced stiff resistance from organized camps of environmental protesters and activists. Another hurdle is the lithium refining process: processing facilities are not only expensive, but they are also extremely energy-intensive, making it difficult for U.S. companies to set up domestic operations.
Other Materials: Other minerals necessary for lithium-ion EV batteries include graphite, manganese, and nickel. Graphite makes up the anode material in most lithium-ion batteries, but China dominates all aspects of this supply chain as well. Beijing controls about 65 percent of the world’s natural graphite mining capacity. Before graphite can be used in batteries, however, natural graphite must either be refined into spherical graphite, or the material must be produced synthetically. China produces 80 percent of the world’s synthetic graphite and 100 percent of the world’s spherical graphite. The United States imports the majority of its graphite from China.
The story is similar for manganese, also an important input for battery cells. While China has very little mined production of manganese—only around 7 percent—it controls 93 percent of the chemical refining process. The United States has not produced manganese ore domestically since 1970 and relies fully on imports. Unlike manganese, nickel is mined and produced in the United States; however, imports still account for some 50 percent of total consumption. Despite minimal mined production of nickel, China is still able to dominate the upstream global supply of the mineral, as 65 percent of nickel chemical processing and refining occurs in the country.
Cell Component Production: After these minerals have been mined, refined, and processed, they are used as inputs for the components of the battery cell: the cathode, anode, electrolyte, and separator. All of these major components have supply chains of their own, but as with raw materials, the production of these component parts is dominated almost entirely by China.
Most of the lithium, cobalt, and nickel found in lithium-ion batteries is used to produce the cathode, making this component the most expensive part of the battery. Indeed, cathode materials account for over half of the total cost of producing battery cells. China holds sway over the majority of global cathode production, some 61 percent in 2019. China also dominates the production of anode material, which is primarily graphite-based. As noted above, China remains the sole commercial-scale producer of spherical graphite used in lithium-ion battery anodes, and it also controls manufacturing for battery-grade synthetic graphite. China produced 86 percent of all anodes (natural and synthetic graphite). China also dominates electrolyte production—Chinese companies accounted for close to 60 percent of production in —while Japan controls the separator supply.
Conclusion
Today’s world is changing at a dizzying pace. In the energy sector, the shift toward EVs and renewable energy promises to remake some of the world’s largest industries. The CCP intends to capitalize on this change. Chinese grand strategy hinges on the assumption that, in our technology-driven world, a country’s ability to control market share, domestic production, and international standards in high technology sectors has become perhaps the most important factor in calculating national power. This belief is driving CCP efforts to “seize the commanding heights” in advanced technologies, including batteries and EVs. As Chinese Premier Xi Jinping’s push for self-sufficiency and “indigenous innovation” demonstrates, Beijing has embraced the logic of decoupling: the CCP seeks to bolster China’s national power by means of zero-sum technological and economic leadership, throwing the process of globalization into reverse.
The United States has no choice but to reciprocate. Given the importance of batteries as a source of geopolitical leverage, as a crucial enabler of next-generation defense concepts, and as the key to competition for economic leadership in the EV industry, breaking Chinese bottlenecks in critical mineral production and battery manufacturing must be a strategic imperative for the United States. To break free of Chinese leverage, American policymakers must communicate and implement a national battery strategy that builds a domestic supply chain for advanced batteries, but this strategy must be approached through the lens of geopolitics. Such a strategy should include the four steps:
1. Provide U.S. government support for critical mineral mining and processing, battery and cell production, and battery recycling.
2. Offer additional U.S. government funding to boost innovation in cobalt- and graphite-less chemistries, next-generation batteries, and manufacturing techniques for lithium-ion batteries through targeted investments.
3. Create DOD initiatives to secure the supply chain for military-grade batteries, and
4. Invest in workforce and talent development programs.
Whether the United States can successfully implement and resource this strategy is another matter. Ultimately, this may be a question of will—establishing a more resilient battery supply chain will require years of sustained effort from dedicated policymakers. If the U.S. intends to win the battery race, reframing energy policy as another front in the U.S.–China strategic competition is a crucial first step.
Nadia Schadlow, Ph.D., is a senior fellow, Arthur Herman, Ph.D., is a senior fellow and director of the Quantum Alliance, and Brady Helwig is a research associate at The Hudson Institute. This article is excerpted from the Hamilton Commission on America’s National Security Industrial Base.
The post Powering Innovation: Advancing America’s Battery Technology appeared first on Jewish Policy Center.