Product Development and Innovation at WeatherTech | WeatherTech
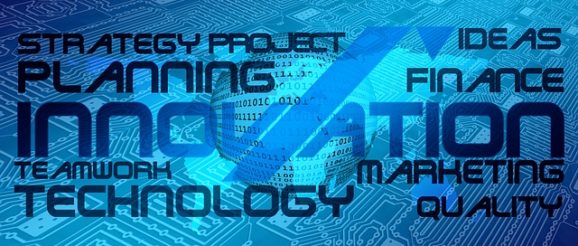
Product Development and Innovation at WeatherTech
How a FloorLiner is Created
Since 1989, WeatherTech continues to manufacture the highest quality automotive, home and pet products on the market today. It’s a process that’s been perfected over countless hours, utilizing cutting edge technology and manufacturing methods to bring customers the best product and an absolute perfect fit when it comes to vehicle protection.
What many customers might not know is the time and effort it takes behind the curtain by the WeatherTech Product Development team to produce even just one FloorLiner application. Every WeatherTech FloorLiner is custom measured for each vehicle application. So as you can imagine, one vehicle could have up to 10 different FloorLiner molds that would need to be created for that vehicle. To help understand how a FloorLiner is created, we figured we would shed some light inside the Product Development team and how they start with a new vehicle and create a FloorLiner for it.
FloorLiner Development Timeline:
Step 1. Research: New vehicles come out every single year for many manufacturers, so paying close attention to manufacturer’s vehicle launch dates are key in getting a good jumpstart. Once you obtain the new vehicle information, next is confirming how many different configurations are going to be available for this particular vehicle — does the vehicle come with five or more seats, what type of console configuration, manual vs. automatic and what countries will this vehicle be sold in?
Step 2. Measuring: Once all the research is done, the next step in the process is going out and finding that new vehicle. Once found, using a laser scanner, the Product Development team will scan the floors and cargo area of the entire vehicle. This requires putting multiple reflective positioning targets in the vehicle and masking off any chrome or other shiny surfaces. They will then scan the vehicle, changing the seat positions, to ensure the designers know the exact location of seats if adjustments need to be made. They scan the gas, brake and clutch pedals while engaged, so they can determine the firewall height. The last step in this process is they will take multiple photos of each vehicle, including photos of seats, console drawer, pedals in different positions and any other features such as retention locations that are important in the design.
Step 3. Part Creation and Data Processing: The Product Development team will head back to the lab and start to compile all this newly obtained data. Using the ISO standards (certified quality standards), they create the part in their system with feasibility reports, design requirements, photos, and convert the raw scanned data. The raw data is cleaned up further and the file is converted to a format the designer can utilize.
Step 4. Design: Through the use of advanced, fully integrated Computer Aided Design (CAD) and Computer Aided Manufacture (CAM) software platforms, the designers create a virtual 3D model of the FloorLiner. These designs take into account all the data that was collected previously to ensure the correct fitment per application.
Step 5. Stereolithography Creation: Using Stereolithography (SLA) or in a term you might have heard before “3D Printing,” the Product Development team will send the CAD information to the printers to create multiple sections of a prototype. The SLA sections are then assembled into the first prototype sample. The process of creating an SLA can take up to two days.
Step 6. Prototype Fitment: With the 3D printed prototype in hand, the Product Development team will go into the field to test fit the prototype in the vehicle. Some of the items they are checking for are gaps on the walls and floor, the position of the retention devices, the movement and folding of the seats and vehicle controls. They will then check the functionality of the doors, consoles, drawers/storage, vents and option items such as subwoofers. The Product Development team will photograph everything and bring all the information back to the shop and change the designs if necessary. This process is repeated from step 4 through 6 until the prototype is a perfect fit. They may also do multiple test fits of each SLA, depending on the build quality of the vehicle.
Step 7. Tooling: After the final revisions are completed by the designer, the part then goes to WeatherTech’s tooling shop. These highly trained and skilled machinists use American-made CNC machines to create a metal mold out of the 3D modelling data provided by our product engineers. The process of creating one tool can take anywhere between one to three weeks to complete, depending on size and complexity of the design.
Step 8. Sample Creation and Approval: Once the tooling has been completed, the next step is creating an actual FloorLiner as a sample. WeatherTech uses a patented High-Density Tri-Extruded (HDTE) material to create FloorLiners. The HDTE material comes in large sheets that are then heated in a large industrial oven. Once these sheets are heated to the correct temperature, they are pressed over the mold and then vacuum sealed down onto the cooler metal’s surface. This process is called Thermoforming. Once the FloorLiner has been cooled, it is removed from the mold, and, if necessary, some minor additional trimming may occur before it is ready for its final test fit. The Product Development team will head back to their vehicle and place the FloorLiner in the vehicle. Once again, multiple photos are taken for vehicle control, seat movement, and the other checkpoints listed in step 6. If the FloorLiner fits perfectly, it is finally approved for that vehicle’s application. That information will be sent to the ecommerce team and placed on the website for sale.
As you can see, WeatherTech goes to the extreme to make sure the FloorLiner you purchase will accurately and completely line the interior carpet of your vehicle giving “absolute interior protection.” Shop for Floor Protection for your vehicle today!