Realizing the STEP fusion dream will require cryogenic innovation at scale and at pace
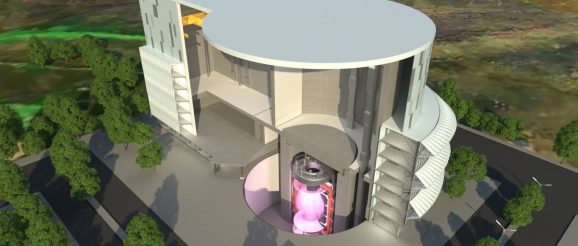
Deliver a UK prototype fusion energy plant, targeting 2040, and thereafter a sustainable, long-term pathway to the commercial viability of nuclear fusion. That’s the ambitious objective – and even more ambitious timeline – confronting the scientists, engineers and project managers currently sweating the details for the conceptual design of the so-called Spherical Tokamak for Energy Production (STEP).
The four-year, £220 million design phase for STEP is already well under way and due for completion by mid-2024. Heading up the initiative is the UK Atomic Energy Authority (UKAEA) at Culham Science Centre, Oxfordshire, which is already home to two leading-edge experimental fusion reactors: the Mega Amp Spherical Tokamak Upgrade (MAST-U) and the Joint European Torus (JET).
While STEP will leverage the deep domain knowledge and expertise of both these established projects, it is the spherical tokamak capability pioneered at MAST-U (and its parent facility MAST) over the past two decades that is being touted as the precursor for a compact, cost-effective and commercially scalable next-generation fusion power plant (see below: “Back to basics on STEP”).
Equally significant, of course, is the associated industry supply chain to source the core enabling technologies and innovations that will make commercial fusion a reality. A case in point: the myriad complex cryogenic systems that will be required throughout the STEP fuel cycle, guaranteeing bulletproof integrity across a range of low-temperature regimes (15–80 K) to deliver successful, sustained fusion operation.
Cryogenic conversations
Those low-temperature technologies and applications were very much front-and-centre last month when more than 50 industry delegates turned up to the Culham Science Centre – in person and online – for the STEP Cryogenics Engagement Workshop. The gathering marked an acceleration of STEP’s early-stage dialogue with the UK cryogenics community, with the UKAEA team seeking to tap the collective wisdom of specialist manufacturers and academia to bottom out the development roadmap for the project’s cryogenic infrastructure.
Together with industry partners we need to identify where technological developments [in cryogenics] should be targeted and explore who might lead on such developments
Chris Waldon
“Right now, our priority is to introduce the cryogenics community to STEP, explain the importance of the programme for future energy production, and outline the challenges in terms of cryogenic refrigeration,” explained Chris Waldon, deputy director and chief engineer for STEP. “Together with industry partners we need to identify where technological developments [in cryogenics] should be targeted and explore who might lead on such developments.”
Fair to say, given there is still much work to be done regarding the granular detail of the STEP fuel cycle, that not all of those low-temperature technologies have yet been selected (nor calculations undertaken for the expected cryogen usage and estimated power loads). Nevertheless, some high-level cryogenics requirements are already nailed down. “Our priorities are to minimize the real-estate and associated power budget for cryogenic refrigeration,” explained Nanna Heiberg, specialist contractor for cryogenics on the STEP project team. “Currently, though, the cryogenic technology is not available at the scale and power efficiency that we need to support a range of core subsystems in STEP.”
Among those crunch-points are compound cryogenic pumps for the exhaust systems of the fusion reactor vessel; matter injection into the plasma core using cryogenic pellets; and cryogenic distillation systems to adjust the ratio of hydrogen isotopes (deuterium/tritium) for fuelling the fusion plasma.
In short, STEP scientists and engineers need to engage with the cryogenics industry – at scale and at pace – in order to realize a viable conceptual design for a prototype fusion power plant versus that looming 2024 deadline. Those industry partners, in turn, will gain access to targeted R&D contracts to support near-term cryogenic technology development, testing and prototyping, while positioning themselves as preferred suppliers for the anticipated scale-up to commercial fusion power generation from the middle of the century.
It is not a straightforward sell, however. One of the biggest challenges facing the STEP project team is getting the right creative and commercial people in cryogenics to focus on that slow-burn fusion opportunity. That is especially so given that “business as usual” markets – supporting the hydrogen economy, liquefied natural gas applications and emerging quantum technologies – are where these companies currently see their surest commercial returns.
“We need to help the cryogenics industry see beyond BAU to the significant growth potential of fusion energy,” added Heiberg. “STEP is the proving ground through which we will realize the necessary cryogenic innovations and, as such, it is not just about one prototype fusion power plant, but the catalyst for a sustained commercial and technology opportunity.”
Connecting with engineers
One industry insider with a clear-eyed view on the fusion opportunity – as well as the potential pitfalls for smaller cryogenics companies – is Paul Kelly, chief technical officer at ICEoxford, a UK-based designer and manufacturer of specialist cryogenic systems for scientific research and industry. “My high-level take-away from the workshop is that there is a very long way to go before we realize commercial fusion,” he explained. “Nonetheless, it’s vital that STEP fosters connections with cryogenics engineers sooner rather than later to minimize divergence on the desired ‘cold requirements’ versus what’s actually going to be feasible.”
So how can the STEP team guarantee the cryogenic solutions it needs at the right price point and versus the project’s tight timeframes? “The fusion part of the STEP puzzle is still in its early stages, with probably numerous design changes yet to be made,” noted Kelly. For sure, he adds, the cryogenics industry will need hard-and-fast numbers and targets to hit, so it’s going to be essential to have strong decision-makers to scope out the granular cryogenic requirements for STEP during the current concept design phase.
The cooling requirements for STEP are huge, also the range of temperatures to be controlled is broad
Paul Kelly
“When you start talking about kilowatts of heat load, a cryogenics engineer wants to turn and run away,” Kelly added. “The cooling requirements for STEP are huge, also the range of temperatures to be controlled is broad. I’m sure things will accelerate, though, once the fusion and cryogenics specialists get together and define a complete, joined-up initial design.”
Getting that collaboration right between STEP and the cryogenics suppliers will be fundamental to success, with the feedback coming through loud and clear from small- and medium-sized equipment vendors and academic groups – all of them wary of committing significant time and resource to tender for sprawling, broad-scope design studies.
“What we’re instead investigating is the potential for tighter collaborative R&D engagements, with smaller packages of funding against discrete and more manageable deliverables,” concluded John Teah, cryoplant lead within the STEP project team. “PhD studentships could be another important part of the mix when it comes to engaging with cryogenic experts in academia.”
Back to basics on STEP
In the prototype STEP power plant, nuclear fusion will be realized in a spherical tokamak device that uses superconducting magnets to confine and control a hot plasma of fusion fuels in a container called a torus.
At the heart of it all is the fusion reaction between deuterium and tritium nuclei, yielding one helium nucleus, one neutron and, in the process, liberating huge amounts of thermal energy for electricity production (although STEP is not expected to be a commercially operating plant at this stage).
While most of today’s experimental fusion reactors – including JET and the work-in-progress ITER project in southern France – are built in the shape of a ring doughnut, STEP’s spherical plant will be shaped more like a cored apple (as per MAST-U). This spherical tokamak design is expected to minimize STEP’s physical footprint, improve operating efficiency, as well as potentially reduce capital and running costs.
The post Realizing the STEP fusion dream will require cryogenic innovation at scale and at pace appeared first on Physics World.