Southern Star Central Gas Pipeline earns Engineering Innovation award at SGA Natural Gas Connect conference
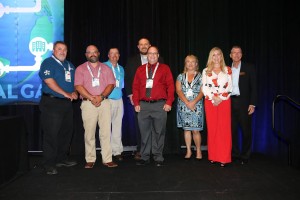
Driving innovation in an organization begins with a culture that inspires and recognizes ideas, not just the results. Innovative companies like Southern Star rely heavily on employees to encourage innovation. At Southern Gas Association (SGA), we want to recognize our members and the ideas that are driving their company and our industry forward. Moreover, we believe peer-to-peer awareness and recognition will drive innovation in all areas of the industry. SGA is proud to recognize Southern Star’s hard work, operations excellence, thought-leadership and dedication to industry advancement.
Congratulations to our Engineering Innovation – Transmission and Midstream – award winners, Southern Star Central Gas Pipeline, whose award was presented during Natural Gas Connect.
The Southern Star Central Gas Pipeline team earns the Engineering Innovation Award-Transmission and Midstream, at SGA’s Natural Gas Connect conference, July 2019
AWARD ENTRY DETAIL: “Modernization through Data Analytics” — Southern Star has been at the forefront of implementing the Windrock Platinum system in compression and as a result have 5 Cooper GMV units running at one station and have real-time data analysis and continual monitoring. They are currently monitoring 9,137 unique shutdown points on 88 compressor units.
Our gas compression engines that move gas across our system have what are essentially on-board computers that control the engines as well as annunciate an alarm or shutdown if a run parameter issue occurs. This is similar to the check engine light on a car. At that point, we are on the reactive side of the maintenance, because the issue has already occurred. We thought it would be pretty neat if we could bring all the data that these computers (Programmable Logic Controllers or PLCs) are processing to one location so we could display the data in a more user-friendly fashion and run analytics on it to catch items before the check engine light comes on. This would put us on the proactive side of the maintenance. To accomplish this, we purchased Pi software from OSISoft. This software allows us to gather and historize the run parameter data we are receiving from our PLCs across our system. We are then able to analyze the parameters we are capturing and make notifications when we catch items trending outside of the norm and can also compare the data for the various units in a more efficient manner. One of the first items we caught was an internal leak on a compressor cylinder. It was registering a leak index of 20%. Temperatures were not different than what was expected. We were able to schedule the repair, take the unit down, and make the repair before it got to the alarm or shut down stage. The issue was a faulty gasket under a compressor valve and completing the repair lowered our leak index to 2%. This maintenance was completed on the proactive side of the maintenance. We are also utilizing the program to catch in-efficiencies across our units for items such as lubrication amounts, fuel usage comparisons, etc. The capabilities that we are now building in the system are helping us to operate more efficiently and reduce unplanned outages.