SPE Automotive Division names 36 finalists for annual Automotive Innovation Awards Gala
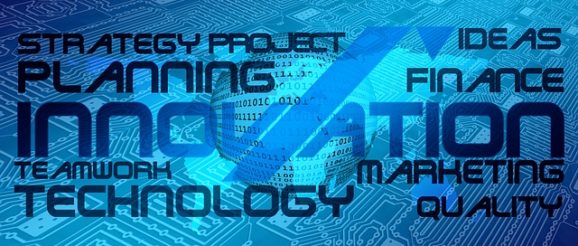
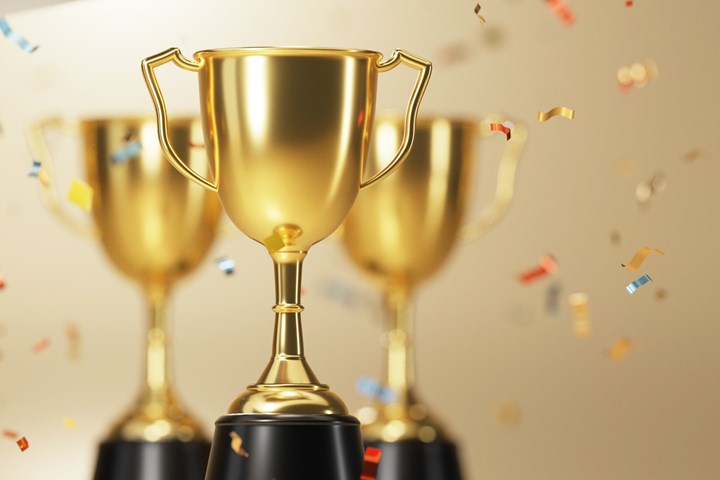
Photo Credit: Getty Images
The Automotive Division of the Societyof Plastics Engineers (SPE, Danbury, Conn., U.S.) has announced the finalists for its 50th annual Automotive Innovation Awards Gala. Nominations were first subjected to a pre-qualification review and then were presented before a panel of industry experts on Sept. 23-24, 2021. The panel then sent forward category finalists to the Blue Ribbon judging round, which was held Oct., 1, 2021. Category and grand award winners selected during the Blue Ribbon judging round will be announced on the evening of Nov. 10, 2021, during the 50th SPE Automotive Innovation Awards Gala. Finalists from this year’s competition are listed below in category and submission order:
Category: Additive Manufacturing
Chassis Spring Sleeve
- OEM make and model: 2005 Ford Motor Co. Ford Mustang GT
- Tier supplier/processor: Ford Performance Parts/Ford Advanced Manufacturing Center
- Material supplier/toolmaker: BASF Corp. /not applicable
- Material/process: Ultrasint TPU01 TPU/additive manufacturing
Replacing extruded rubber moldings with 3D-printed TPU and post-process vapor smoothing, these aftermarket polymeric spring sleeves were designed with design for additive manufacturing (DFAM) principles, eliminating the adhesive normally used to bond rubber sleeves to springs. The design balances assembly feasibility, performance, weight and material usage and provides an aesthetic not typically seen in such applications. When the traditional supplier no longer could provide parts, Ford designed and produced the kits in-house, reducing mass, cost and material usage, improving water-shedding capabilities and saving $150,000 through tooling avoidance.
Integrated Tether System
- OEM make and model: 2021 Ford Motor Co. Ford Maverick
- Tier supplier/processor: IAC Group/IAC Group
- Material supplier/toolmaker: Not available/not applicable
- Material/process: Not available/additive manufacturing
In an industry first, customers can select, download NFTL files and 3D print their own swappable accessories (e.g., cupholders, trash bins, etc.) that fit in storage slots of their vehicle across the entire Maverick series. Initial designs were developed by Ford and its supply teams, but future ones could be suggested by customers. A variety of printer types and suggested materials can be used. This provides customers with flexible, customizable storage and use features or the option to maximize cabin space while avoiding significant tooling investment.
Category: Body Exterior
Cowl Vent Grille
- OEM make and model: 2020 Ford Motor Co. Ford F150
- Tier supplier/processor: US Farathane/US Farathane
- Material supplier/toolmaker: The Materials Group/not available
- Material/process: Optipro CP47GB post-industrial recycle PP/injection molding
This is said to be the first exterior, weatherable, MIC application to use low-density microspheres plus PP from PCR carpet. The application lowered mass (0.2 kilograms) and cost $0.50-1.00/vehicle while offering enhanced weatherability, excellent dimensional stability and surface aesthetics in a more environmentally friendly form. The drop-in application required minimal tooling modifications, yet was 16% less dense than talc-filled prime PP while offering better processing, mechanicals, surface finish, scratch and mar, weatherability and a shorter cycle time. It contributes to 680,000 kilograms of potential landfill avoidance and reduces carbon emissions 83%.
Grille with Integrated Lit Emblem
- OEM make and model: 2021 Ford Motor Co. Ford Mustang Mach E GT
- Tier supplier/processor: Magna Exteriors/LexaMar Div. of Magna Exteriors
- Material supplier/toolmaker: Covestro/Inevo Group
- Material/process: PC/injection compression molding
This hardcoated and painted front grille with lit emblem provides a 3D, futuristic effect in a single part. Injection/compression molding forms the large-format clear PC grille with variable wall thicknesses (ranging from 3-5 millimeters) in a lower-tonnage press that helped minimize or eliminate flow lines and stress marks. After molding, the optical-quality part undergoes hardcoat silicone dip to provide excellent weathering and abrasion resistance, the pony emblem is milled out, and primer and paint are selectively applied to the B side of the part — said to be the first use of paint-over-hardcoat for an auto exterior trim application.
Bumper with Park-Aid Sensor Integration
- OEM make and model: 2021 Ford Motor Co. Ford Bronco
- Tier supplier/processor: ABC Technologies/ABC Technologies
- Material supplier/toolmaker: ABC Technologies/Rocand Inc.
- Material/process: Salflex 615 PP/blow molding
This is reported to be the first time integrated park-assist sensors have been successfully incorporated into blow-molded bumper assemblies. Versus stamped steel, blow-molded PP beams are lighter, lower cost and offer optimized design freedom and versus injection molded beams, they offer excellent structural rigidity, reduced assembly complexity and lower-cost tooling. The resulting fully capable, lightweight bumper system makes use of snap-fit features that eliminate additional hardware to retain the sensors in place.
Category: Body Interior
Third Row Seatback
- OEM make and model: 2021 Toyota Motor Corp. Toyota Sienna
- Tier supplier/processor: Toyota Boshoku Corp./Flex-N-Gate Corp.
- Material supplier/toolmaker: BASF Corp./Concours Technologies Inc.
- Material/process: Ultramid B3ZG7 CR PA 6/injection molding
A 16-piece steel assembly was replaced with a single, shoot and ship plastic assembly for this third-row seatback that reduced mass 30%, cost 15%, represented a two-time improvement in crash performance and takes 63% less effort for occupants to raise the seat to its upright position, eliminating the need for a seat motor. This is industry’s first fully-plastic freestanding seatback offering excellent energy absorption without need for metal support brackets. A new 35% short-glass, impact-modified PA6 resin was developed for this sequentially injected application.
Max Recline Seat
- OEM make and model: 2021 Ford Motor Co. Ford F150
- Tier supplier/processor: Adient PLC/Leggett & Platt, Windsor Machine Group
- Material/process: Delrin, Zytel, Ultramid, ADX, Delrin POM, Zytel PA, Ultramid PA, TPO Acetal, GF Nylon, TPO/injection molding/overmolding
A helpful feature in this entry-level model are front driver and passenger seats that recline fully yet support both neck and chest (via a special thoracic bolster with five lockable positions) as well as hip and lower back (via a cushion-lift mechanism). Plastics were key to achieving the proper balance of support and flexibility for comfort and to provide a durable solution without BSR concerns in the cushion-lift assembly. To date, six patents/innovations have been granted on this design.
First Row Center Seat Mobile Work Station
- OEM make and model: 2021 Ford Motor Co. Ford F150
- Tier supplier/processor: Mitchell Plastics/Mitchell Plastics
- Material/process: Hostaform XGC15-LW01 and SlideX C0313 XAP POM, Celstran LFT-PP, HushlloyPC + ABS, PP/ABS, POM, GF PP/ABS, PC + ABS/ injection molding
To offer truck owners a weather-safe workspace inside the vehicle, a multipurpose, multiposition flat work surface on the back side of the middle front jump seat (on models with bench seats) can be used for writing, computer work, etc., while leaving access to cupholders and power to recharge electronics. The unit offers 121 lockable positions every 4.5 and stands up to rough customer use, yet stows away when no needed. Plastic is used on ≈95% of the assembly. Four patents have been granted on the design.
Work Surface Fold Out Armrest
- OEM make and model: 2021 Ford Motor Co. Ford F150
- Tier supplier/processor: Motus Integrated Technolgy/Motus Integrated Technology
- Material supplier/toolmaker: BASF Corp./Lamko Tool & Mold Inc.
- Material/process: Ultramid B3EG6 Nylon 6 30% GF/injection molding
This foldout work surface with injection molded double-pivot hinge produces a completely flat 56 x 34-centimeter work surface that deploys along the center console but stores in the armrest. A new two layer ultrasoft-touch paint system on the ABS panel provides pleasing haptics. Versus a metal piano-style hinge, the plastic hinge is 30% lighter and an estimated 15% less costly.
Category: Chassis/Hardware
Composite Tunnel Reinforcement
- OEM make and model: 2021 Stellantis Jeep Grand Cherokee L
- Tier supplier/processor: L&L Products Inc./L&L Products Inc.
- Material supplier/toolmaker: BASF Corp./Muiltiple
- Material/process: Elastocoat, Ultramid 74850, 8350 PUR, PA/pultrusion, injection molding, extrusion
Replacing a multipiece stamped and welded ultra-high-strength steel (UHSS) assembly with a hybrid composite construction consisting of a PUR pultrusion (80% FVF fiberglass) injection overmolded with high-impact GR PA6 and integral mounting hardware, this tunnel reinforcement reduced component mass 40% and subsystem weight another 20%, lowered systems cost 2.9% and tooling costs 18.5%, while meeting or exceeding all functional requirements. The application featured new materials, new simulation tools and a new method for mechanically bonding thermoset and thermoplastic composites with integral hardware. Although lightweight, the structure carries high loads, and is easier to assemble.
Multi-Material Rear Leaf Spring
- OEM make and model: 2021 Ford Motor Co. Ford F150
- Material supplier/toolmaker: Hexion Inc., SGL Carbon/not available
- Material/process: EPIKOTE Resin TRAC 06150, EPIKURE Curing Agent TRAC 06150, HELOXY Additive TRAC 06805/high pressure transfer molding (HP-RTM)
This hybrid rear leaf spring combines a high-strength steel main pack plus an HP-RTM fiberglass-reinforced epoxy composite helper that reduces mass 30% while providing the same stiffness and durability as a conventional steel leaf spring system. Additional benefits include increased payload capability, lower part count, decreased interleaf friction, smoother engagement, lower noise and lower carbon footprint.
Active Tuned Mass Module
- OEM make and model: 2021 Stellantis Ram 1500
- Tier supplier/processor: Hutchinson SA/not available
- Material supplier/toolmaker: BASF Corp./not available
- Material/process: Ultramid A3ZG3 BK23325 PA66+IM+GF/low-pressure and high-pressure injection molding
This drop-in solution for reducing engine vibration with any “cylinder on demand” methodology provides closed-loop vibration control. Versus passive mass dampers that are largely metal, the new system offers greater design flexibility, is tunable to a wider range of low-frequency vibrations, reduces mass 27%, improves fuel efficiency >1%, simplifies assembly and increases occupant comfort. The composite housing and bracket were key to the success of the device.
Plug-in Hybrid EV Battery Cover
- OEM make and model: 2021 Honda CR-V pHEV
- Tier supplier/processor: SANKO GOSEI/Minghsiang
- Material supplier/toolmaker: SABIC/S-VANCE Ltd.
- Material/process: SABIC FR PPc H1030 PP/injection molding
This is said to be the first thermoplastic solution for a battery cover that meets stringent new fire safety requirements that went into effect earlier this year in China. The non-halogenated FR 30% GR polypropylene copolymer (PPc) is 40% lighter than the outgoing metal solution, offers inherent electrical insulation, seals against moisture intrusion and will not corrode. The 1.6-meter-long injection molded part is 2.0 millimeters thick and reduces cost and mass, increases safety,and contributes to extended driving range and sustainability.
Folding Shifter
- OEM make and model: 2021 Ford Motor Co. Ford F150
- Tier supplier/processor: SL America/Daeoh Science
- Material supplier/toolmaker: Solvay SA/Daeoh Science
- Material/process: Amodel A-1130 FW PPA+GF 30%+PTFE/overmolding
This folding console gear shifter is key to the function of another application, the flat work surface. The shifter stows with the push of a button. Novel park-by-wire technology provides automatic return-to-park function. The plastic/metal hybrid features sintered metal gears overmolded with 30% GR PPA with PTFE, which reduced mass, noise, CLTE and friction.
Category: Environmental
Positive Crankcase Vent Tube
- OEM make and model: 2018 General Motors Co. Small Black CSS Engines
- Tier supplier/processor: dlhBOWLES/dlhBOWLES
- Material supplier/toolmaker: Arkema/not available
- Material/process: Rilsan HT CESV Black P0101 TL PPA/exrtrusion and thermoforming
This is reported to be the first use of PA11 produced from monomer derived from castor bean oil in a positive crankshaft vent tube. The bio-monomer based resin provides high thermal stability (1,000 hr at 160°C), chemical resistance and flexibility. Castor beans are grown in soil that supports little else, providing an additional income source for poor farmers in India without competition with food/feed crops or deforestation. Versus steel/rubber assemblies, the PA11 vent tube is 50% lighter, $5/part less costly and more flexible, facilitating assembly, while helping decarbonize the supply chain.
Headlamp Housing
- OEM make and model: 2020 Ford Motor Co. Lincoln Continental
- Tier supplier/processor: Varroc Lighting Systems/Varroc Lighting Systems
- Material supplier/toolmaker: Competitive Green Technologies/Varroc Lighting Systems
- Material/process: CGTECH BCR CGTECH BCR-HMS30-40 PP/injection molding
In this PP headlamp housing, 20% biochar from coffee chaff replaced 40% talc while offering better mechanicals (including better impact strength), higher HDT, tighter dimensions, lighter weight (SG 17% lower), no odor/outgasing and a lower carbon footprint — meeting or exceeding all of Ford’s performance requirements. Additionally, cycle time was lowered, cost was reduced, 25% less energy was required to manufacture the headlamp housing and no modifications were needed to existing tooling on this drop-in application.
Wiring Harness Clip
- OEM make and model: 2021 Ford Motor Co. Ford Bronco Sport
- Tier supplier/processor: Lear/HellermannTyton North America
- Material supplier/toolmaker: DSM/HellermannTyton North America
- Material/process: Akulon RePurposed PA6 PA6/melt compounding, injection molding
These 15% GR rPA6 wire-harness clips are injection molded from 100% PCR ocean plastics. Ghost gear (fishing nets) are collected by fishermen in the Indian Ocean and Arabian Sea, providing jobs, more sustainable livelihoods and healthier marine life. The material provides comparable performance to petroleum-based prime resin at 10% cost savings, lower energy, improved supply-chain stability and LCA benefits. No tooling changes and minimal process changes were needed for this drop-in change.
Category: Industry Solutions for COVID-19
Ventilator Main Chassis Production
- OEM make and model: 2020 General Motors Co./Ventec Life Systems V+Pro Emergency Ventilator
- Tier supplier/processor: HiTech Mold & Engineering Inc./HiTech Mold & Engineering Inc.
- Material supplier/toolmaker: SABIC/HiTech Mold & Engineering Inc.
- Material/process: Lexan 500R 10% GF PC/injection molding and threaded insert assembly
In less than 18 days, the team sourced materials, built tooling, brought dimensional quality into spec, automated installation of 48 brass insert nuts (verified by vision systems), converted a manufacturing facility, trained a workforce and scaled up production of tight-tolerance ventilator chassis components from thousands/year to thousands/week, eventually delivering 30,000 over 154 days. Whereas the previous supplier had struggled to meet accuracy, FTQ was raised to 98.7 at faster production times.
Energency Ventilator
- OEM make and model: 2020 General Motors Co./Ventec Life Systems V+Pro Emergency Ventilator
- Tier supplier/processor: Cascadia Custom Molding/West Michigan Molding Inc.
- Material supplier/toolmaker: Avient Corp./Proper Group International Inc.
- Material/process: Versollan OM1262NX-1 TPE/injection molding
The team developed a unique TPE — offering modified flow, high adhesion to the PC/ABS substrate and excellent chemical resistance — and shipped it within 24 hours. High-cavitation tooling was rapidly produced to ensure sufficient supply. A solid supply chain was established that met demand throughout 2020.
Warpage Correction in Ventilator O2 Bracket
- OEM make and model: 2020 General Motors Co./Ventec Life Systems V+Pro Emergency Ventilator
- Tier supplier/processor: PTI Engineered Plastics/PTI Engineered Plastics
- Material supplier/toolmaker: Victrex PLC/PTI Engineered Plastics
- Material/process: Vitrex 450FC30 PEEK/injection molding
In less than one week, the PEEK resin was fully characterized for CAE material cards and tooling for a key ventilator component was redesigned using mold morphing/windage techniques to address warpage issues that had previously required post-mold fixturing and machining. New tooling was produced and first parts were shot nine days later. This allowed the team to hold extremely tight tolerances without post-mold countermeasures. This enabled production to be scaled from thousands/year to thousands/week to meet high demand. Costs were reduced 30-40% by eliminating post-mold machining.
Ventilator Diaphragm
- OEM make and model: 2020 Ventec Life Systems V+Pro Emergency Ventilator
- Tier supplier/processor: Ventec Life Systems/Lumenflow Corp.
- Material supplier/toolmaker: Wacker Chemical Corp./2K Tool
- Material/process: Elastosil LR 30003/50 Silicone Rubber/liquid silicone injection molding
The team used its automotive skillset to retrofit processing equipment to switch from optical-grade silicone to conventional liquid silicone rubber, solve a void issue, build new tooling in just 19 days, and ramp up production of a critical ventilator diaphragm from 1,000/year to 4,000/week.
Powered Air Purifying Respirator
- OEM make and model: 2020 Ford Motor Co. Limited Use PAPR
- Tier supplier/processor: Ford Motor Co./Denso Corp.
- Material supplier/toolmaker: Asahi Kasei America Inc., Celanese/ 3Dimensional Services, Protolabs
- Material/process: PPTD40, POM Asahi P-40TC-1102 NT101, Celanese M90 CF2001 PolyPro, POM/injection molding
The team produced what is said to be the first all-plastic PAPR, converting previously metal components to plastic to reduce mass and costs and improve user comfort for this personal protective equipment (PPE_ used by medical workers caring for COVID-19 patients. The lighter, more efficient design improved battery life, enabling workers to complete a 12-hour shift without needing to recharge the battery. NIOSH certification was achieved in just three days on the first try. Production was increased to 8,500 units/week from the 650/week the previous supplier achieved. All profits from sales were donated to COVID-19 relief funds and four patents are pending on the unit.
Flexible Air Breathing Tube for Powered Air Purifying Respirator (PAPR)
- OEM make and model: 2021 Ford Motor Co. Powered Air Purifying Respirator
- Tier supplier/processor: TI Fluids Systems/Flexaust
- Material supplier/toolmaker: Celanese, AT Polymers, TechmerPM, INEOS Styrolution Group GmbH, DuPont/not available
- Material/process: EVA, LDPE, PE, ABS, PA6/6/thermoforming and injection molding
To meet NIOSH certification requirements, the team used automotive tools to deliver on all project objectives in less than 30 days. A new breathing tube design was developed where one size fits bodies ranging from 5th percentile female to 95th percentile male in a variety of postures. The design features quick connects to ensure a robust connection and offers 25% greater airflow but consumes 24% less current for extended battery life. It also is lighter and eight dB quieter. The team delivered 42,000 breathing tubes during the program.
PPE Production Through #TyvekTogether and Project Airbridge
- OEM make and model: Not applicable
- Tier supplier/processor: Not applicable/not applicable
- Material supplier/toolmaker: DuPont/not applicable
- Material/process: Tyvek/not applicable
Two different programs — Operation Airbridge and #TyvekTogether —dramatically increased production capacity for hospital gowns and coveralls for healthcare workers and first responders. Additionally, a new fabric was formulated in just three weeks to optimize use and increase downstream production. Idle capacity and resources at 15 U.S.-based partners were used. In total, the team produced and shipped 17.6-million garments to replenish the National Stockpile.
Multi-Use Isolation Gown
- OEM make and model: 2020 Ford Motor Co. Isolation Gown
- Tier supplier/processor: Joyson, Windsor/not applicable
- Material supplier/toolmaker: Highland Industries, Aunde/not applicable
- Material/process: Nylon 6,6, Polyester/weaving, coating, sewing
Responding to the scarcity of PPE early in the pandemic, the team repurposed airbag and seat trim materials and used idle cut and sew facilities to produce 50 times the washable isolation gowns for frontline workers. Two different fabrics were developed and approved in less than two weeks (PA6/6 with silicone coating and PET with paraffin/C6 fluorocarbon coating) and gown designs were modified to prevent sleeves from riding up when workers were gloved. A total of 1.32-million gowns have been shipped to date. Efforts were made to reduce gown cost to health-care providers.
Apollo PPE Face Shield
- OEM make and model: 2020 Ford Motor Co. PPE face Shield
- Tier supplier/processor: Troy Design Mfg/Placon
- Material supplier/toolmaker: Ex-Tech/Placon
- Material/process: PET APET & RPET PE/die cutting and rotary cutting
This is reported to be the first time this type of PPE equipment has been produced at extremely high volumes. Within two days’ time, the team developed its first clear face shields and within 13 days, 1.1 million units had been produced and delivered. To address supply constraints and potential failure modes, material was changed from RPET to APET and pushpin attachments replaced stapling. Supply streams and manufacturing teams were capacitized to more than five million pieces/week. In total, over 21 million units were shipped to protect frontline workers.
Acteev Technology
- OEM make and model: Not available
- Tier supplier/processor: Not available/not available
- Material supplier/toolmaker: Not available/not available
- Material/process: Not available/spunbond and meltblown nonwoven media; continuous filaments, monofilaments and staple fibers; molded applications
A new low-odor fabric introduced in Nov. 2019 was repurposed to produce washable and reusable nonwoven face masks for the pandemic. Key to the material’s efficacy is the fact that zinc ions are embedded in the polymer matrix during polymerization, so the antibacterial treatment doesn’t wash or wear off and remains active for the life of the product. The technology also can be used for knits, woven fabrics and engineering plastics and is covered by more than 100 patents to date.
Category: Materials
Composite Roof Receivers
- OEM make and model: 2021 Stellantis Jeep Wrangler and Jeep Gladiator
- Tier supplier/processor: Stellantis/not available
- Material/process: KyronMAX S-4330 PPA w /30% USCF/injection molding
Six brackets for removeable hardtop and soft top roofs were converted from investment cast steel to 30% ultrashort carbon fiber (USCF)-reinforced PPA, providing comparable part strength while reducing costs 38% and mass 79%. Powder coating was eliminated and scratch and mar improved while providing a weatherable, MIC, Class A finish that allowed for mid-program replacement and backwards service compatibility. The USCF composite molds like neat polymers but outperforms LFT materials, is fully recyclable, and has a lower carbon footprint than metal/alloy parts. Direct-drop valve gates and T-nut fasteners also were key enablers.
Electric Drive Unit Mount Bracket
- OEM make and model: 2022 General Motors Co. Cadillac LYRIQ
- Tier supplier/processor: DTR Automotive Corp./not available
- Material supplier/toolmaker: DuPont Mobility & Materials/not available
- Material/process: PA/injection molding
A new PA resin formulated for enhanced damping/NVH without loss of mechanical properties was developed for the EV’s drive unit mounting brackets. This enabled the structural support brackets to be tuned, along with elastomeric bushings, to provide broad vibrational filtering, while reducing mass 34% and costs 19.5%. The material must provide stable performance under high stresses and varying ambient and loading conditions.
Speckled Plastic Door Trim
- OEM make and model: 2021 Ford Motor Co. Ford Maverick
- Tier supplier/processor: IAC Group/IAC Group
- Material/process: Hostacom TRC 483N NA TPO/injection molding mold in color
Careful part design and tooling considerations, coupled with a uniform-distribution carbon fiber-based speckled filler provides a unique appearance for interior TPO parts versus solid colors. This eliminates the need for stiffer polymers required for painting/filming, eliminates paint’s environmental impacts, reduces costs $12/vehicle and saves $400,000 in painting/filming equipment avoidance. Only a single tool is needed for both solid and speckled colors on the program.
Graphine Reinforce Brake Lines
- OEM make and model: 2020 Ford Motor Co. Ford Explorer
- Tier supplier/processor: Martinrea International Inc./Eagle Industries Inc.
- Material supplier/toolmaker: Nanoxplore, XG Sciences/Martinrea International Inc., Eagle Industries Inc.
- Material/process: EagleZorb SA-04G PA612, PU Foam/mold foaming and extrusion
Advanced coating technology featuring graphene-enhanced PA 6/12 has been used to significantly improve the abrasion and corrosion resistance, thermal performance and NVH of brake lines. Whereas metal was exposed after only 8,000 cycles when a PA 6/12 coating was used alone, the graphene enhanced coating showed no exposed metal after 400,000 cycles, eliminating the need for additional protective coatings. Tube outer diameter did not change, although total tube weight was reduced 25%.
Category: Process/Assembly/Enabling Technologies
Active Air Intake Maniufold Holder/Tuning Plates
- OEM make and model: 2021 Nissan Frontier
- Tier supplier/processor: Mahle GmbH/MacLean-Fogg, EPC
- Material supplier/toolmaker: BASF Corp./KTM Industries Inc.
- Material/process: Ultramid B3WG6 PA6 GF30%/injection molding
Replacing multicomponent metal/plastic interfaces that made precision tuning and balancing of the door train for active air intake modules more difficult, this single-piece injection molded tuning plate not only held demanding tolerances (±0.025 millimeters) and offered 0.040-millimeter adjustments, but also reduced mass 12% and cost 10% while improving performance. Key innovations were the use of a low-wear 30% GR-PA6 resin that molds very flat, use of 10 tuning pillars each per left and right plates for precision balancing, cavity pressure sensors for exacting process control and data-driven micro-processing adjustments.
Thick Lightbar Development
- OEM make and model: 2021 General Motors Co. Cadillac Escalade
- Tier supplier/processor: Valeo Lighting Systems/Valeo Lighting Systems
- Material supplier/toolmaker: Covestro LLC/Windsor Mold Group
- Material/process: Makrolon LED PC/multi-cavity, multi-shot injection molding
This challenging 780-millimeter-long and 18-millimeter-thick transparent-red light blade for rear taillamps functions offers a unique appearance and homogeneous lit appearance. Keys to making the patented application work were advanced simulation tools for design and functional optimization and warpage control; complex runner, parting line, shutoff valves and multi-shot injection process control; plus a custom-formulated optical-grade of PC that helped manage quality, cost and molding capacity and met all legal rear-lighting requirements. Despite technical challenges, program timing was reduced by three months and $250,000 in prototype tooling was avoided through virtual prototyping.
Liftgate Inner
- OEM make and model: 2021 Ford Motor Co. Mach-E
- Tier supplier/processor: Plastics Omnium/Plastics Omnium
- Material supplier/toolmaker: SABIC/Omega Tool Corp.
- Material/process: STAMAX 40YM240 PP-LGF-40%/injection molding
This MIC LFT-PP injection molded liftgate features a clamshell design with integral interior trim integration and reinforcements plus styling flexibility that allows for design studio changes. Versus steel designs, the composite offered 35% cost and 15% mass savings and a lower carbon footprint. A high-flow copolymer filled the design featuring wall thicknesses that varied from 2.0 to 4.5 millimeters. A six-axis robot inserted metal reinforcements for overmolding and removed parts. The highly controlled process used sequenced hot runners with PSP sensors and a part-presence sensor for overmold stamping.
Fabric Wrapped Speaker Grille
- OEM make and model: 2021 Ford Mustang Mach-E
- Tier supplier/processor: Grupo Antolin/Williamston Products Inc.
- Material supplier/toolmaker: Trinseo/Toolplas Systems Inc.
- Material/process: Magnum 3325 MT ABS/injection molding
To achieve the desired look for a series of fabric-wrapped speaker grilles on IP and doors, a number of technical challenges needed to be overcome, including finding the right size speaker holes as well as fabric and adhesives that did not interfere with sound performance yet met customer abuse, cleaning and FR requirements and other auto industry performance standards. In the end, appearance, audio performance and assembly requirements were met for this industry-first fabric wrapped speaker grille application.
Hybrid Fleece Technology
- OEM make and model: 2021 General Motors Co. Chevrolet Tahoe & Suburban, Cadillac Yukon & Escalade
- Tier supplier/processor: IAC Group/IAC Group
- Material supplier/toolmaker: Carver Non-Wover Technologies LLC, Celanese/Persico SpA
- Material/process: NF PP Mat, Celstran NF PP, PP-GF PP/injection molding
Panels of compression moldable natural fiber/PP hybrid fleece with up to 25% recycled PP plus an injection moldable LFT-PP substrate are being used for a variety of interior panels (e.g., door carriers, uppers, bolsters and armrests; IP substrates, top pads and mid-panels; and hard trim). Versus injection molded plastic panels, mass was reduced 50%, numerous secondary operations including welding, adhesive application and insert molding were eliminated, and renewable materials were used in a single efficient process producing 320,000+ car sets/year. The first use of non-contact IR heating in North America supports fast cycle time.
Category and Grand Award winners selected from among these finalists during the Blue Ribbon judging by a group of journalists, academics and retired industry chief engieers will be announced on November 10, 2021 during the 50th annual SPE Automotive Innovation Awards Gala at Burton Manor in Livonia, Michigan.
A Vehicle Engineering Team Award (VETA) will also be presented to recognize automotive designers and engineers, tier integrators, materials suppliers, toolmakers and others whose work in research, design, engineering and/or manufacturing has led to significant integration of polymeric materials on a notable vehicle. A Lifetime Achievement Award will also be presented to honor a person who has made significant contributions to the industry.