Supercharging WMG’s Energy Innovation Centre
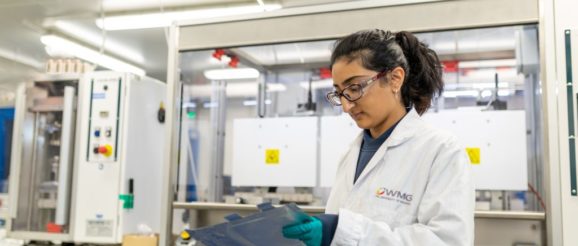
WMG’s Energy Innovation Centre (EIC) was already one of the biggest, most ground-breaking battery research labs in the UK. But, now, thanks to £20m of investment received via the Government’s Energy Research Accelerator (ERA) programme, it has been able to dramatically improve its capacity and capabilities. This has catapulted the EIC into an entirely different league — one which will ensure the UK stays at the forefront of pioneering energy research.
The state-of-the-art EIC facility, based at WMG, University of Warwick, opened in 2016 at a cost of £50m to support the development of cheaper, higher energy density, safer batteries and provide knowledge in three key areas: energy storage, energy management and complex electrical systems. It works with a variety of industrial partners — everyone from automotive manufacturers to high-end motorsport supercar manufacturers, technology firms and aerospace companies.
The extra £20m funding awarded three years ago, enabled a range of new equipment and facilities to launch at the EIC in June this year. These include new laboratories, a dry room for cell assembly, equipment for characterisation work at cell, module and pack levels, innovative charging infrastructure and second-life evaluation facilities, a material scale-up line and the UK’s first openly accessible 1MW pack test facility to support larger testing projects for motorsport and aerospace companies.
Mark Amor-Segan, Principal Engineer, Energy Innovation Centre, likens this expansion to putting the last piece of a jigsaw in place.
“We already had a reputation as a centre of excellence and a leader in battery research,” he says. “But the ERA funding has enabled us to link all the different parts of the process that are involved in developing an energy storage system, so that we can present an entire service to our industrial partners.”
Crucially, it also means the EIC can do things that other battery research centres can’t.
“We now have 20 different laboratories working side-by-side,” says Mark. “We have electro-chemists working with thermal-modelling experts and mechanical engineers working with power electronics and motor specialists. Having all these different disciplines under one roof within the same group is absolutely pivotal to moving the whole energy storage agenda forward.”
Professor Martin Freer, Director of the Energy Research Accelerator, said:
“The aim of ERA funding is to leverage industrial co-investment. That’s exactly what the Energy Innovation Centre does. It’s a dynamic and professional organisation which has been incredibly successful. It has worked with industry to drive technology to market and develop advanced processes for manufacturing batteries and second-life electrical energy storage.
“For example, part of the challenge of manufacturing is that batteries are made of cells which then have to be assembled into packages. To be able to do that in a reproducible way so that none of those cells are lost is highly problematic — but EIC scientists have developed a technique for doing just that. Other research the EIC is involved in includes inductive charging, where electric vehicles automatically charge while parked over a pad at the traffic lights, or in a car park or loading bay. That type of innovation is going to drive the electric vehicle sector in the years ahead.”
Mark Amor-Segan admits that battery science needs to speed up to get to where the world needs it to be if we are to move to a low emissions future. The ability to understand why batteries fail is a key part of this.
“It has been very difficult to predict the chemical behaviour of battery cells and how they age and degrade,” he says. “In fact, a lot of battery technology is developed through empirical methods, which is basically trial and error. But now, with the ERA investment allowing us to link all the different parts of the process together, we can more easily understand why a battery fails.”
“Our aim in the years ahead will be to model a recipe in a computer, build a prototype cell, then test it to confirm the model is correct. As part of the ERA investment, we now have a new mechanical testing centre which, for the first time, will allow full mechanical testing of live lithium-ion batteries — such as torsion, twist and fatigue-type testing — at a range of states of charge and cycling conditions. That’s a fantastic capability that will give us a whole new data set which will help to improve those models and simulations.”
Mark finds it reassuring that the UK Government and funding bodies are investing so much money into energy storage technologies.
“The ERA funding has certainly helped push us over the finish line,” he says. “We now have everything we need to move forward. We’ve had a battery facility at WMG for over a decade, so completing the picture is very satisfying.”
Find out more about WMG’s capabilities here.
Read the rest of the latest HVM Connect issue here.
The post Supercharging WMG’s Energy Innovation Centre appeared first on High Value Manufacturing Catapult.