Techtextil & Texprocess Innovation Awards highlight relevant textile industry trends
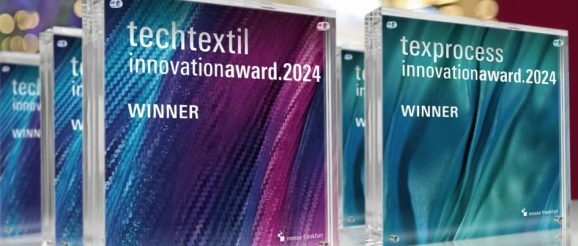
Techtextil & Texprocess Innovation Awards highlight relevant textile industry trends At this year’s Innovation Awards at the Techtextil and Texprocess textile fairs, which are taking place in Frankfurt, Germany until Friday, a total of 15 winners in eight categories were honoured on Tuesday for pioneering research and new products, processes or technologies. The award winners were selected by juries of internationally renowned experts. The awards are regarded in the industry as an important indicator of relevant trends in the textile industry worldwide, which this year include hemp leather, a textile pump integrated into clothing, self-cooling textiles, effective, chemical-free garment cleaning, AI-supported textile recycling and others. The winner in the “New Technology” category of the Techtextil Innovation Awards is a new type of coating for self-cooling textiles from the German Institutes of Textile and Fibre Research Denkendorf (DITF). It makes it possible not only to keep out sunlight indirectly (such as sunshades or awnings) and actively cool the fabric itself, but also to reflect sunlight and re-emit heat energy. “Our tests show that this allows textiles to be cooled to below the ambient temperature,” said Cigdem Kaya, team lead barrier textiles at the DITF’s Competence Center Textile Chemistry, Environment & Energy. This will pay off for clothing, but also for cooling textiles, as the demand for cooling energy in cities increased by 23 percent between 1970 and 2010, according to Kaya. Fans and air conditioning systems provide cooling, but the latter in particular consume a lot of electricity: “Textiles that actively cool and do not require electricity could become a real alternative on building façades and roofs,”, added Kaya. Smart textile pump keeps garments dry In the same category, Swedish company LunaMicro also scored points with an intelligent textile pump, which is a multi-layered, porous textile connected to a small battery. It is incorporated into an item of clothing and actively transports liquids such as sweat from the inside of the garment to the outside while it is being worn, keeping the wearer dry on the inside before they start to feel wet. The innovation will soon be used in outdoor and protective workwear as well as in personal protective equipment (PPE). Vegan leather “LOVR” made from hemp waste German biotech start-up Revoltech won in the category “New Concept” and convinced the jury with its vegan, fully recyclable leather substitute made from hemp waste taken from industrial hemp cultivation. The material called “LOVR” (an acronym for “leather-like, plastic-free, vegan, residue-based“) is the “world’s first truly circular leather substitute” according to Revoltech, because vegan leather alternatives have often had two problems in the past: either they have not been purely plant-based because they contain petroleum-based components, or they are grown in laboratories and are therefore difficult to scale, explains Lucas Fuhrmann, co-founder and CEO of Revoltech. LOVR, however, combines scalability and 100 per cent compostability: “It is a truly circular material that will fundamentally change the market for traditional leather and artificial leather,” believes Fuhrmann. It is already being used for shoes and in a concept car from car maker KIA. Moreover, it will soon be used in upholstered furniture, car interiors and clothing. Greater sustainability in the textile-care sector One of the three Texprocess Innovation Awards in the category “Economic Quality” was awarded to German textile care specialist Veit for its patented compact finisher “CF20 DesFin”, which was developed jointly with wfk – Cleaning Technology Institute. It was designe designed to eliminate odours, mould, stains and pathogens from garments without the use of chemicals. This technology could be useful for clothing logistic companies, online retailers, laundries and dry cleaners. “Clothing from returns or goods transported over long distances by ship can be disinfected, deodorised and ironed at the same time without chemicals using the new compact finisher,” states Christopher Veit, managing director of Veit, which counts Hugo Boss and Zara among its customers. The technology has been presented to a broad international audience of trade visitors for the first time at Texprocess. AI-assisted textile recycling Belgium company Valvan received one of the two Texprocess Innovation Awards in the category “Digitalisation + AI” for its AI-assisted machine Trimclean that automatically recognises and removes non-textile parts from old garments, to increase the textile recycling rate. According to Jean-François Gryspeert, sales & business developer at Valvan, the sorting software makes use of benefits from recent advances in the field of artificial intelligence (AI): “We use AI in combination with a special camera to better separate fabric parts from non-textile parts.” This works so well that, unlike other solutions, Trimclean can even remove patches, seams and prints. “The AI technology making Trimclean possible did not even exist a few years ago,” says Gryspeert. New measurement method for better-fitting bras The second award in this category went to the Institute of Textile Machinery and High-Performance Material Technology (ITM) and the Chair of Development and Assembly of Textile Products at TUD Dresden University of Technology for a new evaluation method for body scans using 4D scanning technology. It is designed to make it possible to measure soft body parts such as the female breast in motion and not, as is the case with many 3D body scanners, only when the person is stationary. According to ITM, this allows the creation of dynamic 4D body scans that are much more accurate and can also be compared digitally. “In future, clothing manufacturers could use 4D body data such as this to develop, among others, more individualised bras with improved wearing comfort, as well as saving time and costs during product development,” is the verdict. “World novelty for decorative and ornamental seams” Industrial sewing machine manufacturer Dürkopp Adler from Germany won the Texprocess Innovation Award in the category “Innovation for quality improvement’ for a CNC sewing automat with rotating sewing kinematics for medium heavy industrial sewing applications. According to the company, this is a “world novelty for decorative and ornamental seams”, which was officially launched at Texprocess. “It is the first CNC system of its kind that permits perfect sewing in all directions,” adds Sebastian Kinnius, head of product management and marketing at Dürkopp Adler. The “911 Resolve” eliminates the need for additional machines in the production process, thus improving resource efficiency and saving energy. Automotive suppliers, manufacturers of high-quality leather goods and technical textiles, for example, will be able to sew car seats and interiors, airbags, medical bandages, filters and handbags with greater precision and quality. Machine sewing for everyone Another prize in this category went to Juki Central Europe for its innovative industrial sewing machine “DDL-10000DX”, which makes sewing processes in garment production easier, particularly three-dimensional sewing, which previously dependent on the handling skills of individual operators. A special conveyor belt supports the operating personnel in handling the machine and facilitates the feeding of the fabric for all types of materials and patterns, so that anyone can now master sewing. Automated sewing Another prize in the category “Economic Quality” went to Danish company Mikkelsen Innovation for „FastSewn“ – patented technology that enables digitally controlled automatic sewing and cutting from rolls without pre-cutting on a single platform and thus avoids frames and templates having to be loaded and off-loaded manually. Two-dimensional textile products like industrial filters or custom pillows are automatically transported to a flatbed sewing system, which is designed to enable the joining of any contours – even complex ones. „The system is also able to laser cut the sewn patterns at the same time further reducing handling,“ says Steve Aranoff, business development director at Mikkelsen Innovation. According to Aranoff, FastSewn is initially targeting the production of airbags, car seats and sewn furniture parts and is currently presented for the first time in full size at Texprocess.