The chip shortage could lead to an era of hardware innovation – Stacey on IoT | Internet of Things news and analysis
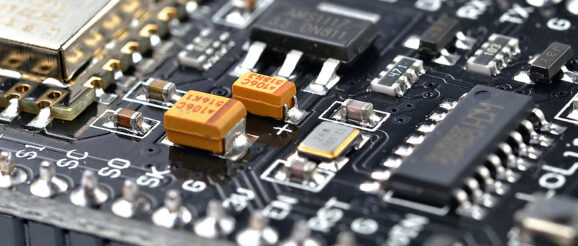
It’s bad out there for customers of electronic parts and components. The semiconductor shortage is so severe it’s being covered by mainstream media; meanwhile, various politicians have tasked their aides with looking at the global supply chain. Indeed, in the short term, the dearth of chips is already leading to product delays, companies redesigning their parts, and higher device prices. But over the long term, it could usher in a complete rethink of the way electronics parts are designed.
Peggy Carrieres, VP of global sales development and supplier enablement at Avnet, told me she expects the shortage to contribute to engineers reducing the number of physical components used and turning instead to software to handle functions that had historically been done in hardware. The shortages tied to the pandemic are an accelerator for this shift, but it has been happening for years as the industry adjusts to the end of Moore’s Law and the ability to eke out more performance at lower costs.
I had reached out to Avnet because I was interested in what it was seeing from its customers as the chip shortage dragged on. Avnet is a distributor, so it acts as a middleman between electronics components suppliers and the end customers of those parts. Someone building a new electronic device could work with Avnet to source the parts from an existing design, for example, or to build a design out of available parts that fit within a specific price.
Either way, Avnet is positioned in the middle of the chip shortage, and so is seeing the effects from both sides. Carrieres, who prior to Avnet spent years planning demand and handling pricing at chip firms including On Semiconductor and Freescale, said the pandemic hit at the beginning of what was expected to be a growth year for the semiconductor industry after relatively flat sales in 2018 and 2019. What happened instead was a perfect storm of trends that she expects will have a ripple effect beyond the chip industry itself to include all the industries that use chips.
Electrification of vehicles and the internet of things were two driving forces behind the resurgence of chip sales heading into 2020. That’s because electric cars require a lot more computer and chip-based components than those powered by gas, while the IoT is adding silicon to devices that historically haven’t required chips. “I saw a design the other day of a lightbulb with 12 components,” said Carrieres. “[My team] asked me if this was an idea, and I had to tell them that it was a real product.”
So not only was demand expected to be up for 2020, but the chip industry was ready for it. Then the pandemic hit, and automakers put the kibosh on new production as they worried about the impact of COVID-19. The chip companies were initially undaunted, and simply switched production to other buyers. But the added combination of weather events, sick workers, and fires contained supply anyway.
Meanwhile, consumer demand for smarter products ramped up. Many people felt compelled to invest in new computer gear, lights, and cameras for their Zoom setups at home, and some even bought new homes that they wanted to make smart. As for the automotive companies, they quickly realized that demand wasn’t dropping, so they tried to ramp up production. But without chips — the underlying building block of any “smart” product — those companies were forced to wait, which explains why it’s a great time to sell your used vehicle and why you can’t get a rental car right now.
On the automotive side, as cars go electric and get smarter features that lead to autonomous driving, the nature of the companies that supply the auto industry are changing. There’s room for new startups and new ways of doing things. More of the car’s features are accessed using a touchscreen as opposed to a knob or button, for example, which turns components that once were hardware into a software program. And now, in light of the chip shortage, suppliers to the automotive industry are going to be looking for more ways to turn something that used to be an electronic part into software.
Finally, there’s a third shift happening that will change the market for both chips and hardware going forward. Costs are rising. Labor costs are creeping higher because it costs more to protect workers from COVID. Plus, in many manufacturing industries, there aren’t a lot of new workers coming in to replace those that are not returning. Meanwhile, material costs are rising because labor and shipping costs are rising. Finally, because Moore’s Law is slowing down the economics of the chip industry are changing.
For decades, advances in the manufacturing process meant that chip makers could double the number of transistors on a chip (transistors dictate performance) every 18 months to two years. This was known as Moore’s Law, after Intel co-founder Gordon Moore. Moore’s Law meant that every two years or so a new generation of computers got more powerful. It led to falling prices for memory, CPUs, and even basic GPUs.
But it’s becoming harder to eke out those performance gains. Plus, there are many products, such as power management chips or timing chips, that don’t benefit from Moore’s Law. So as the fundamentals of chip economics change, suppliers will have to adapt. Carrieres expects some chip companies to assess their product lines and eliminate older ones with low margins. At the same time, she said that many engineers and designers will also see shortages in certain parts and so will design them out of their products entirely.
They may choose to integrate more functions into a newer, specialty chip or handle something in software that used to depend on hardware. Chipmakers that can build these integrations and this software will have an advantage. It opens up opportunities for startups that want to tackle this problem as well. If I were in the VC world, I’d be taking meetings with startups and engineers who are trying to consolidate more hardware into a single system on a chip or do away with it altogether.
These are tough times for chip companies and for the growing number of industries that rely on their wares. But that pressure usually leads to real innovation, which is exactly what we need right now.