The Next Generation of Building: Walbridge Director of Technology Innovation Speaks
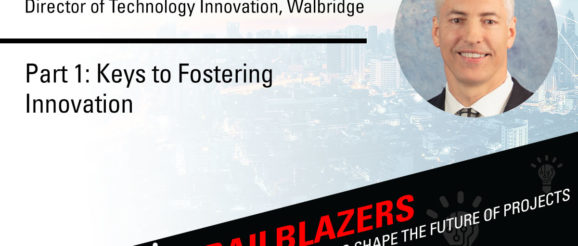
For this installment of our innovation-focused “Trailblazers” blog series, we sat down with John Jurewicz, director of technology innovation for Walbridge Building Design and Construction, to discuss his professional background and views on innovation.
Dr. Burcin Kaplanoglu, senior director of industry strategy and innovation for Oracle Construction and Engineering, led the conversation.
BK: What is your current role, and how has your career evolved since you started in the industry?
JJ: My current role is director of technology innovation. It crosses both optimizing the tech we currently have while watching what new innovations are coming at us.
I was originally licensed as an architect in 1990 but played with super computers and digitized everything in CAD. I also worked as a superintendent with survey equipment and as a project manager before things evolved into design build—designing and building things like radar stations and equipment.
My work was often something beyond just the building itself. In the mid ‘90s I learned early on the value of coordination modeling the systems inside the building.
In the case of radar facilities and air traffic control buildings, we often digitally modeled then built physical mockups to simulate what was about to happen for the FAA and the Air Force. How you placed equipment and cable tray along with erection sequencing was very complicated. This experience would later be invaluable to me.
Walbridge and Industrial Design-Build
Fast forward to my last few years working at industrial design-build contractor Walbridge. It’s much more about what’s going on inside the building than the building itself, including confirming the plant is kept up and running through multiple phases of new work.
The building itself is simply protecting very expensive equipment from the rain—equipment that generates a lot of money. More sophisticated technology is used inside the plant compared to the exterior.
It’s not just how advanced technology improves productivity, safety, efficiency, or the of a building; it’s also how you can most efficiently create the structures for production, whether it’s an assembly line or manufacturing. It’s really the next generation of building.
BK: What are the biggest challenges to innovation, and how did you resolve them?
JJ: Meeting expectations is one of the greatest challenges. A lot of people on the vendor’s side often sell what the software is going to do. There are these built-up expectations that the software, the systems, or the processes they’re going to deploy are truly there.
Most of the time, anyone who has deployed technology realizes that it isn’t all there because there are little bugs or integration problems that must be solved first. That’s typically outside of the vendor’s control.
It’s usually getting all the data organized in your house—or maybe the owner’s house—so that you can deploy these cool new technologies.
These technologies already work, it’s just that the culture—the organization of people—hasn’t caught up yet. We haven’t thought through what this all means. The greatest challenge is often the sociological aspects of trying to deploy technology and how the culture should change to become more optimal.
BK: How can organizations create a culture of innovation?
JJ: How do you foster new ideas? We try to encourage and remove the barriers to try new concepts. These are usually applications people haven’t thought of, combining two different solutions or using solutions that do a certain thing we like in a new way.
We get buy-in from the people funding this by taking it in steps. First, you must build credibility. This is usually getting teams to agree that this is the right thing to do and showing operations where the value is by taking it beyond the sales talk.
After you get buy-in, you must offer proper support and follow up by taking things past demonstrations and teaching people how to use it. After a pilot with champions, we try to take it out further to the organization, although this takes more effort to spread across multiple jobs.
Building credibility amongst the operations side—with the people who are already controlling money and resources—to show that innovative technology is more efficient or optimal is the greatest way to build credibility. This is what fosters growth and trying new things.
BK: What challenges have you faced so far in terms of implementation and how did you tackle them?
JJ: We’re currently facing a lot of demands to see if modular or offsite construction makes sense. The way I’ve personally tackled this is to break apart chunks of models that are provided either in-house or by outside partners and make the models more constructible.
The models become more valuable because you’re doing this off-site, out of harm’s way in an environmentally controlled facility. You’re thinking through delivery in an entirely different fashion. You’ve got chunks of the building being delivered, and that doesn’t always work with viaducts and bridges.
You’re using these model chunks to think through rigging and installation—the logistics of how you’re going to bring all this premade stuff to the site.
Obstacles to preassembly and prefabrication
If you’re pre-welding with robots, weldments can be done much more accurately with an automated welding machine. However, you need to think: “Where do I need power, how am I going to build temporary facilities to pre-make the pipe, and what are the maximum ranges of delivery that will allow me to still ship and install it effectively while reviewing the safety aspects.”
For preassembly, when does it make sense to prefabricate? The question also arises, “Why don’t we just do it the old way? Why does this new approach save that much more time?” If it doesn’t save time, maybe you should do it the old way.
But then you realize sweating copper in the middle of a dust storm is hard to do. You’ve got to build a tent. Finding temporary enclosures sometimes closer to the job site is a viable alternative.
When you’re doing modular construction, you must think fluidly and have an open mind.
BK: What emerging technologies do you see representing the best opportunities, and what other technologies do you see helping us the most?
JJ: Within the past three months we’ve noticed people agreeing that they can’t conquer the world with sensor technology by building another proprietary database; they must build things on an open platform.
We’ve seen progressive movements in not just making construction trailers smart or the job site smart, which is always usually related to getting bandwidth out there early. It’s more about putting the infrastructure in place earlier that will then benefit the owner running the whole building later.
Sensor and laser technologies
Sensor technology has a dual purpose beyond helping you create the building smarter, faster, and more optimally. The greater value is for the owner who’s paying the general conditions for those sensors.
Sensor technology helps them track their workers and where things are, including long-term in the building itself. This is a trend that we are paying close attention to.
The cost of sensors is also dropping, and even the cost of automating things. For example, South Korea has new technology that hooks up to any light switch, making it easier to deploy a smart building even when you’re retrofitting existing legacy systems.
The ball is rolling so fast and there’s so much momentum that it won’t stop and go backwards. That’s what I find fascinating. You can just see everything that’s going to evolve, especially with this innovative—what I’ll call “millennial thinking”—of, “Well, why don’t we just do it this way?”
Read other Trailblazer stories:
Stay tuned for Part II of our interview with John Jurewicz, in which he explores the value of machine learning and the future of technology.