The refining and petrochemical industries: 170 years of innovation
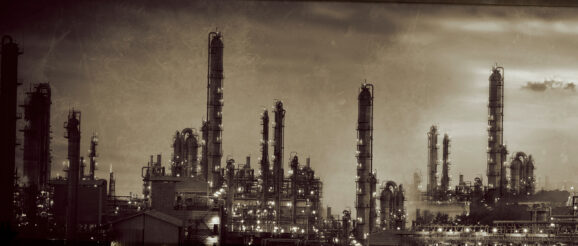
vadams Blog site The fuel and petrochemical manufacturing industries have actually come a long method from the basic thermal stills utilized to produce kerosene in the 19 th century to today’s advanced, high-tech and intricate facilities that assist supply America– and the world– with the fuels, petrochemicals and items that all of us rely upon every day.
Throughout their 150-year history, these markets have established a culture of development, resourcefulness and grit that has helped them continue to develop and prosper throughout financial expansions and to survive world wars, financial contractions and massive shifts in consumer behavior.
The birth of the markets
The refining market was developed when developers took a look at what was thought about useless unrefined oil and turned it into a lighting replacement for whale oil. In the more than a century considering that then, the refining and petrochemical industries have actually continued to create brand-new methods to repurpose and make each drop of oil and gas into products that underpin practically every element of our modern lives– from transport fuels that keep us relocating to vital individual protective equipment (PPE) and medical products.
19th Century
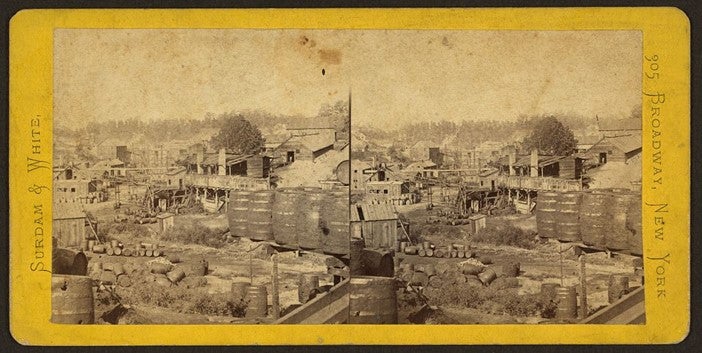
Key dates:
1855: A Connecticut refiner distills petroleum to get tar, naphthalene, fuel and numerous solvents.
1862: First internal combustion car is developed
1862: John D. Rockefeller financial resources his very first refinery
1879: Thomas Edison patents the incandescent light bulb
1880s U.S.-based Standard Oil produces kerosene and ships it around the world
1900s– 1930s
As new modes of transportation established, refiners developed new sort of fuels– including gas, diesel and jet fuel– to enhance the efficiency of various engines and configurations. Creators also utilized petroleum to establish lubricants and waxes that assisted a range of produced items work more effectively.
By 1910, need for auto fuel overtook kerosene demand. Refineries began using thermal splitting, found by an engineer at Standard Oil– the predecessor to ExxonMobil, Chevron and Marathon Petroleum– to produce more gas. Catalytic splitting was consequently developed in the 1920s, which enabled higher-octane items.
World War I further heightened fuel demand, as the U.S. military released aircraft, ships and armored automobiles. And the increasing use of trucks, buses, vehicles and tractors kept fuel demand rising after the war ended.
During this time, need occurred for other non-fuel items made from petroleum. These products, referred to as petrochemicals, ended up being crucial for commercial processes and crucial foundation for lots of products utilized in daily life. A number of products still typical today– including Styrofoam (produced from the petrochemicals ethylene and benzene), PVC (developed from ethylene), plastic cling wrap and isopropyl alcohol (created from propylene)– were created during the first half of the 20th Century.
|
Secret dates:
1902: The National Petroleum Association– the precursor to the American Fuel & & Petrochemical Manufacturers– is founded
1913: Thermal cracking is invented
1920: Isopropyl alcohol produced at Requirement Oil’s Bayway, New Jersey, plant is the very first commercial petrochemical
1940s: Styrofoam and Saran-wrap are established
Fledgling industries get nationwide prominence
1940s
The 1940s saw an acceleration in petrochemical and refining technologies and the scaling of their operations, largely driven by these markets’ crucial role in enabling Allied triumphes in The second world war.
Using catalytic cracking of heavy oils, alkylation, polymerization, and isomerization made it possible for the U.S. petroleum industry to make higher-performance fuels and meet the Allies’ need for air travel, truck, jeep, bike, and tank fuels in addition to providing lubes for Allied weapons and equipment. The petrochemical industry, meanwhile, was crucial in creating artificial rubber for lorry tires (produced from butadiene), TNT (made from toluene), polyvinylidene chloride liners for battle boots (made from ethylene), insulation for radar and undersea cable televisions (ethylene again), amongst lots of other items.
National Archives and Records Administration |
The U.S. supplied a tactical advantage to the Allies since it produced 60 percent of the world’s petroleum, but the predominant use of delivering to carry oil and fuels left the country vulnerable to German U-boats– which patrolled the Atlantic in an effort to keep those crucial fuels from reaching the battlefield. In order to reduce this risk, the U.S. government-funded the longest and biggest pipeline produced up till that point: the War Emergency situation Pipeline ranged from Baytown, Texas, to Linden, New Jersey.
Continued innovation likewise drove the increasing adoption of petrochemicals in customer items. These items would appear with increasing frequency on shop racks till customer items without some petrochemical application ended up being the exception and not the guideline.
Key dates:
1940: Requirement Oil develops catalytic reforming to produce greater octane gasoline and creates toluene for TNT
1940: First tire from synthetic rubber produced in U.S.
1940: Women’s nylon stockings are very first offered commercially in the U.S.
1941: Dow researcher creates Styrofoam
1942: Inventors at Exxon establish fluid catalytic breaking, a process that now produces the majority of the world’s gasoline
1942: Polyester resins are introduced
1942-43: War Emergency Pipelines that link Texas and New Jersey built to move petroleum and refined products to sustain war efforts
The 1950s and 60s
The post-war era brought unparalleled prosperity to Americans. A national interstate system, the increase of the residential areas, and the increasing cost of lorries all combined to propel automobile ownership to excessive brand-new heights, while air travel took off as an available method to take a trip the world. At the same time, petrochemicals allowed the widespread usage of luxuries and benefits– consisting of brand-new synthetic material clothing, home furnishings, and accessories.
To fulfill this progressively different customer need, the refining industry continued to end up being advanced and complex. Many centers started utilizing hydrocracking, which allowed for a broader variety of final result.
As the industries expanded, so did the transport systems to manage feedstocks and completed products. The building of what is now termed “midstream infrastructure”– the system of pipelines, ports, railways, highways and storage systems required to carry America’s energy materials from producer to consumer– echoed the building of the interstate highway system. The midstream petroleum transportation system made it possible for refineries to combine and benefit from economies of scale given that they could now efficiently transport petroleum and natural gas– in addition to the fuels and other products they produced– throughout the country.
The intensely competitive nature of the fuel and petrochemical industries throughout this time made development a vital. As a result, significant corporations produced advanced research study and advancement departments, where researchers created new items including crafted polymers, block copolymers, a broader range of polyesters and polyurethanes and numerous molecular weight polyethylenes, all from the very same six base petrochemicals– as well as preparing for developments such as the lithium-ion battery.
Key dates:
1950: Benzene is produced from petroleum
1954: Polyisoprene rubber– an essential part in numerous medical devices– is established
1954: Artificial zeolites, which further advance the cracking procedure, are developed
1960: OPEC is developed
1965: Kevlar is invented
1968: Man-made fibers outsell natural fibers in the United States
1968: Ziploc bags are presented
1970s, 1980s, and 1990s
Like other manufacturing sectors, the fuel and petrochemical industries suffer throughout financial slumps and durations of geopolitical chaos, especially those like the 1973 oil embargo that result in oil cost shocks. Geopolitical turmoil had impacted oil costs for much of the 1970s, leading to repeated fuel rationing and preventing financial development.
The high oil prices of the 1970s were quickly followed by an oil excess in the 1980s, as the world rebounded from the oil embargo and refiners and petrochemical business found themselves adapting to face significantly various market conditions.
Refinery in Lake Charles, LA. Credit: Phillips 66 Historical Archives |
Increased vehicle fuel performance, among other factors, resulted in decreased demand just as new, non-OPEC extraction tasks started producing considerable amounts of oil in Siberia, the North Sea, Alaska and the Gulf Coast.
The resulting market conditions led to comprehensive combination in the U.S. refining industry, with the number of refineries reducing from 319 in 1980 to 205 in 1990. A lot of the refineries that closed were little, independent operations that lacked the processing versatility of their bigger competitors. The refineries that survived continued to purchase ever-more-complex and sophisticated processing abilities.
The chaos continued in the 1990s, when the refining market went through another challenging economic contraction, changing again through comprehensive mergers and acquisitions. The industries as an entire became leaner and more resistant, better able to weather a variety of market and supply conditions.
This prolonged duration of uncertainty and transition assisted strengthen qualities that still mark the fuel and petrochemical industries today: flexibility, optimism, psychological toughness and a continuous focus on innovating to meet the next difficulty.
Key dates:
1973-74: Oil embargo
: Cost and allotment controls for locally produced crude and fuel ends
1986: Crude oil price collapse
1989: EPA sets seasonal fuel volatility limits on fuel
1989: Fall of the Berlin Wall
1990: The Iraqi invasion of Kuwait drives oil rates from $21 a barrel in July to over $40 a barrel in October
Industries accept globalization
2000s and 2010s
In 1970, the U.S. production of petroleum balanced 9.6 million barrels daily. By 2007, U.S. unrefined oil production had actually declined to 5 million barrels each day. However the extensive adoption of hydraulic fracturing technology in the United States halted the decrease in U.S. crude oil production, modifying the nation’s increasing reliance on imports of oil and gas. It turned the United States into a significant gamer in the global energy markets and the leading exporter of liquid petroleum items. The so-called shale transformation also provided U.S. petrochemical producers with increased access to economical feedstocks, which they used to develop the chemical foundation that make it possible for the manufacturing of a broad range of customer products increasingly required by an ever-growing worldwide middle class looking for the conveniences of a modern-day standard of life. We are now one of the lowest-cost producers of ethylene on the planet.
U.S. refineries also benefitted from globalization, utilizing their complex centers to transform low-value petroleum imported from trade partners into highly desirable refined products that were offered both domestically and abroad.
These market expansions were accompanied by ongoing improvements in ecological performance. Facility emissions of hazardous air pollutants fell 66 percent from 1990 to 2013. And as of 2016, refinery emissions for the 6 criteria contaminants are down nearly 70 percent compared to 1990.
And fuel and petrochemical manufacturers are continuing to innovate to meet future challenges. Petrochemical business have invested substantially in molecular recycling technology, which allows plastics to be repeatedly recycled, in addition to releasing initiatives to minimize mishandled plastic waste. Business are researching new methods to capture carbon at facilities and developing new engine oils that minimize friction and increase gas mileage. They are likewise creating more resilient, lightweight and environmentally-friendly answers to the world’s requirement for hygienic packaging, safe transport and next-generation medical solutions.
U.S. refiners invested over $100 billion to make their facilities amongst the most efficient and complex in the world, placing themselves to provide the cleaner fuels required by today’s consumers. And petrochemical companies invested $185 billion from 1988– 2018 to assist more effectively meet the world’s need for their products.
In an effort to deliver still higher-performing and lower-emission fuels to American motorists, AFPM for the last numerous years has actually promoted for a high-octane 95-RON fuel performance requirement. This 95-RON standard would deliver substantial efficiency improvements in brand-new automobiles, yielding significant reductions in carbon emissions throughout the automobile fleet. When coupled with autos enhanced for such fuel, 95-RON can provide a 3– 4 percent fuel performance gain and have the carbon-reduction equivalency of taking numerous countless cars off the roadway each year. This 95-RON fuel might be sold using the nation’s existing fueling infrastructure, not needing the significant investments required for electric automobile charging stations and infrastructure – and it is suitable with automobiles on the road today.
Key Dates
2010: Occidental Petroleum opens its Century carbon capture plant in Texas
2015: Congress raises oil export restriction
2016: AFPM starts promoting for a 95-RON fuel standard
: World’s very first commercial direct air capture carbon capture facility opens
2019: The United States ends up being a net energy exporter
2019: INEOS produces virgin polystyrene from recycled styrene monomers, offering practical proof of the molecular recyclability of polystyrene
: Eastman announces the capability to molecularly recycle polyester and complex plastics
2020 and beyond
Like lots of other industries, fuel and petrochemical producers have faced extraordinary difficulties in 2020. These markets– considered “critical” by the Department of Homeland Security– are integral parts of the effort to combat the COVID-19 pandemic.
Our markets continue to provide everything from the fuel required by emergency lorries to the petrochemicals used in PPE and hand sanitizer, in spite of substantial market disruptions and obstacles. Companies have demonstrated their versatility and dedication by rotating to ramp up in record time, fulfilling the requirement for frontline equipment important for the battle versus COVID-19.
Our industries have actually seen their reasonable share of tough times over the past century, we continue to offer the energy that is the lifeblood of the U.S. economy. And our industries support 3.5 million highly skilled, particularly well-paying tasks throughout all 50 states. Industry payment is approximately two to three times that of the average for U.S. employees.
Fuel and petrochemical makers likewise significantly contribute to the tax base. In 2018, our industries contributed over $60 billion in federal taxes and almost $70 billion in state and regional taxes– making it possible for the funding of necessary services at the state and local levels.
And the economic benefits provided by our industries won’t disappear anytime soon. The U.N. estimates that the world’s population will grow by 2 billion people in the coming years, and access to affordable energy will stay crucial to human development. The U.S. Energy Info Administration states international energy usage will increase by almost half by 2050 and that petroleum will provide more than three-quarters of international transport energy consumption.
Even as brand-new innovative energy innovations come online, the jobs we offer will continue to be important. A current survey by NATBU discovered that oil and natural gas jobs are viewed as using better pay, benefits and profession opportunities than eco-friendly jobs. And despite the current economic recession, business are continuing to buy internships, apprenticeships and efforts to diversify the workforce, positioning them for obstacles and opportunities ahead.
That’s one of the reasons the industries have actually invested greatly in cleaner fuel production, molecular recycling, plastic waste decrease efforts, and more effective and eco-friendly production methods: We understand we’ll our important products will be trusted for, and we wish to continue to make the world a better location.