The Technology Behind Bigger Innovation
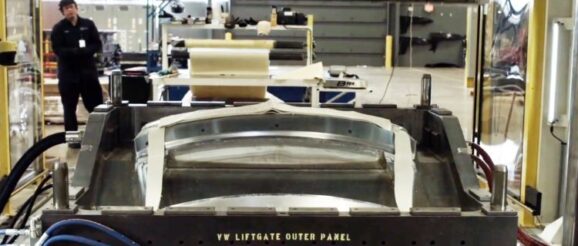
When chemical company BASF’s Performance Materials division wanted to develop a prototype for a new part over 10 feet in size, it knew compression molding would be the ideal production method. A compression molding press has the potential to support a fully-automated manufacturing process within a customer’s plant. But BASF pondered how to get an entirely new component ready for full-scale testing and validation without a customer risking the expense of an unproven technology.
“We first approached this as chemists. We have extensive knowledge about process and application, but making prototypes this big presented issues,” explains Staci Wegener, market segment manager of infrastructure at BASF Corporation. Wegener isn’t able to reveal too many details about the unique part under development, but did share that its size would have been a hindrance without the support of IACMI – The Composites Institute’s Scale-Up Research Facility (SURF) in Detroit, which conducts research and development on lightweighting vehicle structures and is managed by Michigan State University (MSU).
“We explored other options where we could make a prototype, but the size of the press that SURF has in their facility is really unique,” says Wegener. “I don’t think there are too many presses of that size available for this sort of application.”
The machine Wegener is referring to is a 4,000-ton hydraulic compression molding press from Schuler, which can perform closed mold infusion and thermoplastic forming in addition to compression molding. The press employs four double-acting cylinders to provide greater parallelism control for improved surface features, helping to ensure high-quality manufactured parts. Equally as important for BASF’s application, the press features a clamping surface of 142 x 94 inches and a daylight of over 8 feet for larger applications.
“SURF is helping us scale up from lab-scale-size parts to full-scale prototypes without us investing millions of dollars investment into true technology production equipment,” says Wegener. “This will speed up the path to commercialization.”
Filling a Gap
The 50,000-square-foot SURF is the only facility of its kind in the United States, and the team behind it has worked to quickly establish an operation that can match the decades of production experience behind overseas research centers. The vision for an innovation center of this type in the U.S. has been around since at least the early 2000s, when automotive industry researchers began looking for space to work on full-scale product development and testing. With support from the U.S. Department of Energy Advanced Manufacturing and Vehicle Technologies Offices, the Michigan Economic Development Corp. and a number of industry partners, SURF was born and research officially began in 2016.
The post The Technology Behind Bigger Innovation appeared first on Composites Manufacturing Magazine.