Time for Innovation | Human-Centered Change and Innovation
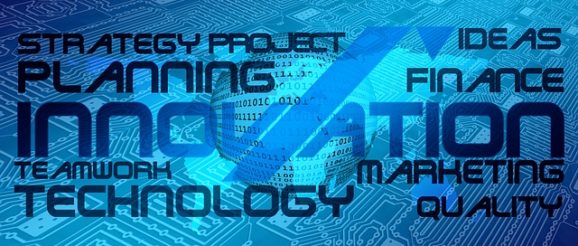
GUEST POST from John Bessant
Why keeping an eye on the clock matters in the world of bright ideas
On 29th September 1707 a fleet of 21 ships under the command of Admiral Cloudesley Shovell was returning from Gibraltar where it had been supporting action during the long-running war with the French. Crossing the Bay of Biscay the weather grew worse and they were struggling to make their home port of Plymouth in the south-west of England. At around 6pm they believed they were in safe waters but in fact were heading on to the rocks near St Agnes’s Bay in the Scilly Islands — fifty miles west of where they thought they were. Four ships were lost in the disaster including HMS Association, the flagship of the fleet which carried Sir Cloudesley and over 1400 other sailors to their deaths. It was one of the worst naval disasters to befall the British Navy.
And an avoidable one. The problem — which urgent follow-up enquiries highlighted — was familiar. The ships were lost because the experienced seamen steering them didn’t know where they were. Navigating the rocky coastline with hidden shelves and shallows depended on accurate awareness of position — but the methods available at the time weren’t up to it. Depth soundings could help but the key missing ingredient was an accurate measurement of longitude. For which they needed a reliable timepiece on board; despite an array of clocks and pocket watches the technology wasn’t good enough to maintain an accurate sense of the time relative to the Greenwich clock on which all naval longitude is based. Time slipped away — and with it any clear sense of where they were.
Cue one of many early innovation contests — attempts at crowdsourcing a good solution to the problem as fast as possible. The British government offered a huge prize of £20,000 in 1714 equivalent in today’s money to around £3m) to anyone who could construct a clock that would enable sailors to calculate their longitude at sea with an accuracy of within half a degree. It was famously won by John Harrison, a carpenter by trade who spent over twenty years working on the problem, producing four models of chronometer each improving on the previous one. His H4 model finally achieved the accuracy and reliability required and he duly won the prize. More important he — and the many others working on the problem — changed the face of seaborne navigation forever.
We’re used to thinking about the Industrial Revolution in terms of Britain as the ‘workshop of the world’, driven by a steady stream of manufacturing technology innovations coming from men like Arkwright, Wedgwood, Boulton and Watt. But we should add the clockmakers to that list; without them the workshop of the world would not have been able to get its wares reliably to anywhere but the closest markets. Their innovation heralded the first wave of globalisation in world trade and we’re still building on that legacy.
Nor was their effort confined to seaborne navigation in its impact; with reliable clocks it became possible to standardise time itself. Prior to 1880 different cities in the UK kept different versions of time, each geared to a local standard timepiece. But the introduction of standardised time, all linked to Greenwich Mean time allowed for important shifts like the expansion of railways with trains running on a clear and predictable timetable.
Time is in many ways a key part of the enabling infrastructure, a foundation on which so much innovation can be built. Like today’s internet it enables things to happen which would not have been possible before — and in similar fashion the early days spent innovating towards a reliable infrastructure represent an important but often neglected innovation history.
So time deserves credit as a macro-level innovation enabler — but it also has an impressive history at the micro-level in terms of its innovation impact. In 1909 Frederick Taylor published his book on ‘The principles of Scientific Management’ which became, (in the view of the 2001 members of the Academy of Management) the most influential book on management ever. His principles laid the foundations for the ways in which factories and later many service businesses were constructed and operated and paved the way for Henry Ford’s mass production model. At heart the approach involved applying rigorous engineering principles to the flow and execution of activities throughout a process and they still underpin much of the industrial engineering curriculum today.
Its impact was huge — for example in Ford’s Highland Park factory where he began experimenting towards the model using Taylor’s ideas, the productivity gains were stunning. In the first assembly line, installed in 1913 for flywheel production for the Model T, the assembly time fell from 20 man minutes to 5. By 1914 three lines were being used in the chassis department to reduce assembly time from around 12 hours to less than 2.
Key contributors to enabling this to happen were an American couple, Frank and Lilian Gilbreth. They worked on what became known as ‘time and motion study’, analysing and breaking down work processes into individual motions, and then eliminating unnecessary motions to improve efficiency. (They also followed in the above illustrious tradition of creating reliable timepieces, in their case developing the micro-chronometer, a clock that could record time to the 1/2000th of a second).
The image of stop watches and clipboards goes back to their influence — and while (like Taylor) their work often receives a negative press (think Charlie Chaplin in the film ‘Modern Times’ in which he is literally caught up in the machine and under enormous time pressure), the reality is that the Gilbreth’s enabled major improvements not just in productivity but in working conditions and employee satisfaction.
They were early but key figures in what later became ‘lean thinking’ — essentially reducing unnecessary waste, especially in movement. Ergonomics owes a lot to their measurement approach which charmingly gave us a unit of measurement — the ‘therblig’ (Gilbreth spelled backwards) which they applied to analyse a set of 18 elemental motions involved in performing a task in the workplace. These elements include movements such as reach, move, grasp, release, load, use, assemble, and disassemble, as well as unnecessary ones like hold, rest, position, search, select, plan, unavoidable delay, avoidable delay, and inspect.
Paying attention to detail, especially around the time taken to carry out a task, and then redesigning it to reduce wasteful effort, movement, queuing, temporary storage, etc. lies at the heart of another revolutionary process innovation — lean thinking. Pioneered in Japanese factories during the post-war years lean is essentially a focus on waste elimination through the application of core principles and key tools. Amongst the ‘seven deadly wastes’ which lean focuses on is time — and not surprisingly the toolkit which emerges from that places a premium on reducing unnecessary expenditure of that precious commodity.
For example one of the early challenges to the emerging car industry was set-up time. With giant machines capable of pressing a piece of steel into the required shape the ability to make different models depends on how quickly those presses can be set-up for a new job. In the early days this typically took up to a day to reset; now (using the widely-applied techniques originally pioneered by Shigeo Shingo and captured in his excitingly titled book ‘Single minute exchange of die — the SMED system’) that time is routinely counted in single minutes.
The implications of this reach far beyond the car factory. Anywhere where rapid changeover of a key resource is needed can benefit from the approach — and has done. Formula 1 pitstop teams can ‘reset’ an entire car with new tyres, fuel and many other changes within seconds. Hospital operating theatres can maximise the productive (and life-saving) time for operations by applying the principles to changeovers. And the revolution in short-haul flying which we have seen in recent decades owes a great deal to the simple performance metric of turnaround time — how fast can a plane land, empty , be cleaned, refuelled and refilled with passengers and take off again? Southwest Airlines have held the crown for years with turnaround times typically around 15 minutes.
Saving time is at one end of an innovation spectrum — it’s worth looking at because wasted time adds no value and saving it enhances productivity. But there’s another end of this spectrum, one which William McKnight discovered in his work at 3M in their early years. It’s all about spending time.
Innovation is about ideas and sometimes coming up with the good ones , the ones which may offer a whole new angle on a problem, needs time for the innovation to incubate. He observed that by giving people a sense of having a little extra time in which they could play around paid off for the company. His 15% policy did just that, giving people the sense that they have time to think and explore without needing to show productivity — the opposite of the tightly-controlled time of the Gilbreths.
(In reality this didn’t cost much in the way of lost productivity since McKnight observed that 15% of a working day, is taken up with coffee and tea breaks, lunch and other time. Plus people don’t religiously take their 15% and then stop thinking about their innovation; most give much more of their own thinking time for free!)
Breakthroughs (of which 3M has many to be proud of) come more frequently if people have time to think — which is why the approach has been successfully adopted by many other organizations. Google, for example, links many major innovations like Gmail to allowing their engineers to spend 20% of their time on their own projects.
There’s another reason why time pressure shouldn’t always be too strong in the innovation area. By its nature innovation is uncertain — which means that we need to experiment and things will go wrong which need time to explore and fix. But sometimes the project level pressure is too strong — prestige, racing the competition, the need to meet performance targets — there are plenty of culprits turning the temporal screws. Think about the fateful Challenger space shuttle explosion back in 1986 which eventually was blamed on a faulty O-ring seal. But importantly — as the Rogers commission of enquiry commented later — it wasn’t the component which was the problem but the system which put so much pressure on the engineers to push past it and press ahead.
That’s sadly not a new tale; the novelist Nevil Shute spent much of his early life working in the aircraft industry and had first hand experience of the race to design an airship. In response to the German dominance with their Zeppelin designs in the 1920s the British government pushed for a challenger and backed two projects, the R-100 which was built on a shoestring by Shute’s company and the other the R-101 which was built with government resources. The latter had all the advantages of unlimited resources and budget but that came with enormous political pressure to get the job done — and fast.
Sadly on a test flight in 1930 the R101 ploughed into a French hillside killing all on board. Once again the enquiry found that the engineers had been pushed to cut corners and ignore safety concerns; Shute and his fellow engineers had enormous sympathy for the difficult situation in which their R101 colleagues had found themselves. As he describes in his book ‘Slide Rule’
‘The R101 team was working under impossible conditions; they had to design and build an airship that was larger and more complex than anything ever attempted before. They had to meet unrealistic deadlines and specifications imposed by the government. They had to cope with constant changes and revisions to their plans. They had to deal with political interference and public scrutiny…… they were doomed to fail’.
It would be good to think we’ve finally learned this lesson — but the 2022 well-researched Netflix documentary ‘Downfall’ which charts the disastrous history of the Boeing 737-Max points once again at the same kind of time pressure as being responsible for pushing too far too fast.
There are many more places where we can see time playing a role as a key innovation enabler or shaper. For example the challenge to board-level patience in the face of the long slow haul towards bringing innovation impact at scale. Evidence shows it takes a long time to move from pilot success to widespread impact. As Ray Croc (the architect behind the scaling of McDonalds) pointed out, ‘I was an overnight success all right, but 30 years is a long, long night’.
So providing support and commitment over the long-haul is going to be as important as having an innovation team with a clear vision and strategy to undertake the expedition. Not for nothing does the term ‘patient money’ first appear in the findings of the famous Project Sappho study back in the 1970s which looked at factors affecting success and failure in innovation.
Or the challenge of innovation timing — we hear a lot about ‘first mover advantage’ and it would be easy to think that speed is always the key factor. But being too early is often as risky as being too late; pushing untried innovations into the market too soon can sometimes mean being cut by the bleeding edge of technology. And sometimes the innovation is so far advanced it has to wait for the wider infrastructure or for the social or political climate to catch up. Shai Agassi’s vision for making the world a better place through his electromobility solutions is a good example. The collapse what had been one of the world’s biggest start-ups came ten years before the underlying idea (of battery swap technology for electric vehicles) found widespread acceptance in niche markets like city taxi networks in China.
Time is a precious commodity which, used wisely, is a key part of the innovation story. So when you glance at your watch or the little clock running in the corner of your computer screen spare a thought for the innovators, thousands of them over the centuries, who solved the problem of measuring it reliably and accurately.
Additional Image Credit: Wikimedia Commons
You can find a podcast version of this here and a video version here
And if you’d like to learn with me take a look at my online course here
Sign up here to join 17,000+ leaders getting Human-Centered Change & Innovation Weekly delivered to their inbox every week.