Where Ideas Meet Impact: How Dal researchers spun a bioengineering discovery into a medical industry innovation
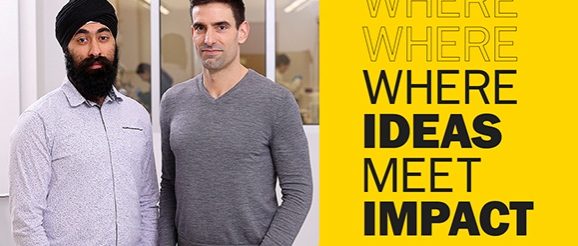
The snapshot
3DBioFibR Inc. formed three and a half years ago, spun out of research conducted in Dalhousie’s School of Biomedical Engineering with support from Dal Innovates. The company’s technology, a bold new approach to tissue engineering, is making it a go-to in the burgeoning medical research sector. The idea
3DBioFibR’s technology has its roots in the work of Dr. John Frampton, Dalhousie’s Canada Research Chair in Cellular, Biomaterial and Matrix Interaction. Dr. Frampton invented a technique for manufacturing protein fibres used as scaffolding to build cellular structures. Like the rebar in a concrete building, the fibers provide an underlying framework that cells latch onto to artificially manufacture structures for use in the human body. His initial protein fibers were encouraging but they didn’t contain enough collagen to be clinically successful. Collagen is the most abundant protein in the human body. Dr. Frampton knew that incorporating it in his fibers would allow him to vastly improve how cells bond to them. Collagen fiber being made. (Photo provided) He recruited fellow Dal researcher Dr. Laurent Kreplak and graduate student Gurkaran Chowdhry to pursue the idea. Together the team built on Dr. Frampton’s fiber creation technique to finetune it and were incredibly successful – upping the collagen content from two per cent to 100. Moreover, they developed the first fully automated manufacturing system to produce collagen fibers, laying the groundwork for translation to a commercial system. The innovation meant their new material could become extremely useful in supporting the creation of biomedical structures such as nerves and the c-shaped pieces of cartilage that cushion joints, among many other potential applications. A close-up look at a scaffold of collagen fibers. (Provided photo) “The goal is for it to act like a structural support for living things to attach to and grow on,” Chowdhry explains. “It was something that had potential. The next challenge became, can we do it at scale to actually service an industry?” In other words, how would they turn this novel medical technology into a company? The challenge For Chowdhry, that broad question was answered in part with the help of two Dal Innovates programs, now known as Lab2Market Discover and Lab2Market Launch. “My undergrad was in physics, my master’s was in physics, so business strategy is not something I had a lot of exposure to. The last business course I took was Grade 11 accounting. So, it was nice to wrap my head around those ideas,” he says. “It was really helpful to learn how to conduct a customer discovery interview and really understand what your customer’s needs are,” he says. Chowdhry now serves as the company’s Director of Business Development. Dr. Frampton is Chief Scientific Officer, while Dr. Kreplak remains heavily engaged as a technical advisor. The team took on the name 3DBioFibR, and experienced biotech entrepreneur Kevin Sullivan as CEO. Day-to-day, Chowdhry focuses on commercial and product strategy, including forecasting cash flow, sales, and the cost of goods. In doing so he relies on many of the principles he first learned in Lab2Market Launch. He says 3D BioFibR also benefited from its participation in Creative Destruction Lab – Atlantic, an objectives-based program for massively scalable, science- and technology-based companies hosted at Dalhousie. Chowdhry and the team learned how to pitch the company, secured an investor, and received advice on everything from strategy to IP to product development and marketing. “It provided a way to pressure test things in a safe environment,” he explains. “It’s a room full of people who’ve been there, done that. You consistently get your assumptions tested and get feedback from people who have a pedigree.” The solution As a result of that advice, 3DBioFibR has positioned itself as a biomaterial manufacturing company that can supply many different biomedical customers. Chowdhry uses the examples of Gore-Tex and Intel to explain his company’s strategy. Gore-Tex does not make clothing, but its material is used by many other companies to produce everything from gloves to boots. Intel doesn’t make computers but its chips power countless PCs. Likewise, 3DBioFibR’s collagen fibres can potentially be used by an array of biotech manufacturers. In June 2023, in a significant step forward, the company signed a development deal with ReNerve, an Australian biotech outfit. 3DBioFibR has developed a prototype for ReNerve that will hopefully – pending tests – be used to help drive nerve regeneration. 3DBioFibR’s collagen fibres would act as a “cell migration highway” in bridging severed nerves. “With our technology, we can make these collagen fibres at scale, with over 3,600 times the throughput of any competing technologies,” Chowdhry notes. “We can do 1,000 metres a second. And we can match the structure of native collagen so that cells can recognize and attach to the material in the way that they do in the body. The tissue engineering industry is all about creating these tissue constructs that can be eventually implanted into a human being.” The impact According to Chowdhry, the tissue engineering industry is a $26-billion market, with companies and researchers pursuing applications spanning hair follicle regeneration, orthopedics, meniscus repair, and corneal, liver, and heart tissues, and even artificial ears. 3DBioFibR’s product ready for market. (Provided photo) “Essentially the industry is trying to create implantable lab-grown tissue to put into a human for every potential condition,” he explains. “Anything in your body you can think of, there’s at least one group working on creating it with implantable tissue.” According to Chowdhry, 3DBioFibR’s technology is “agnostic” in terms of the tissue types it can pair with; it could potentially be used throughout the industry. 3DBioFibR now has 12 employees and manufactures its collagen fibre at its facility in The Labs by Invest Nova Scotia on Dalhousie campus. The company has raised three rounds of funding totalling $3.7 million and plans to pursue a Series A round in 2024. “We think our biomaterial will enable many new technologies to get to the next stage. So, the goal is to stay hyper-focused on improving production, quality, and efficiency, and by doing so, make the biggest impact across tissue engineering,” Chowdhry concludes. “Our fibres will hopefully help these technologies get closer to the clinic — that’s really the goal of the business.” Comments comments powered by Disqus