Why the U.S. needs a bold, long-term innovation strategy
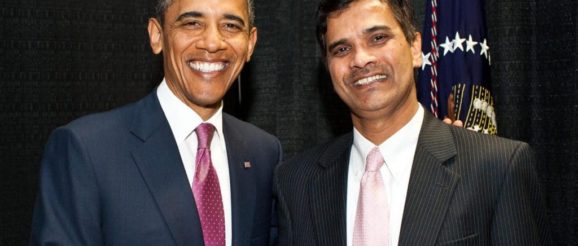
A conversation between Smart Manufacturing Editor in Chief Brett Brune and Sridhar Kota, professor of mechanical engineering at the University of Michigan and Executive Director of MForesight.
Sridhar, please first describe MForesight.
MForesight: The Alliance for Manufacturing Foresight is a federally funded, national consortium. It’s an independent national think-and-do tank on emerging technologies and advanced manufacturing. We serve as the voice of the advanced manufacturing community and inform industry practitioners, academic researchers and government decision makers about opportunities in emerging technologies and cross-cutting challenges in advanced manufacturing. Our singular focus is to enhance U.S. manufacturing competitiveness.

And you were part of the Obama administration?
I was the first assistant director for advanced manufacturing in Obama’s first term from 2009-12. In that role, I initiated and championed the idea of creating the manufacturing innovation institutes, modeled after German Fraunhofer Institutes. I also orchestrated the National Robotics Initiative, and the National Digital Design and Manufacturing initiative.
MForesight has conducted roundtable discussions in many cities on “grand challenges” in manufacturing. What is the grand challenge?
For the past two decades, we have seen the paradigm of “invent here and manufacture there”—cell phones, solar panels, flat panel displays and lithium ion batteries, for example. And production has been shifting overseas for the last few decades to reduce labor costs. In doing so, we lost our fundamental production skills and capabilities. Once the manufacturing is gone, we lose our engineering and manufacturing know-how. U.S. manufacturers are now steadily establishing R&D activities offshore, just to be close to the factories where the new products and processes are being developed. This “invent here, manufacture there” paradigm has now reached its logical conclusion of “invent there, manufacture there.” That is the grand challenge.
Some people claim we are a “knowledge economy” and we should focus on innovation and services because that is where the country and the world is heading. Some people in this camp might ask, “Why invest good money after bad? Why not let other countries like China focus on manufacturing and we focus on innovation?” What would you say to that?
Manufacturing and innovation are very intricately linked. If you don’t manufacture today’s high-tech products, you lose the ability to innovate next-generation products. We learned that the hard way. For instance, because we did not invest in manufacturing flat panel displays in the ’90s, now we don’t have the manufacturing know-how to innovate and manufacture next-generation flexible displays or flexible solar cells? And, in fact, manufacturers and investors are now touting that innovation happens faster in China. So the issue has become not just the manufacturing economy but also the knowledge economy. And we seem to be losing ground on both counts. So the critical thing is, process innovations are needed to manufacture at scale. And that fuels more innovation and provides a feedback loop for next-generation products and research.
So you cannot separate technological innovation from manufacturing. And of course, folks who don’t see the difference between computer chips and potato chips simply don’t get it.
And when you talk about services, we have an $800 billion deficit in goods and a $200 billion surplus in services. We can do the math. And how many services in R&D can you do to offset the deficits in manufacturing?
National security is another compelling reason we should really gain leadership in industries of the future. We are already increasingly relying on foreign suppliers for our defense. In fact, the 2012 Senate Armed Services Committee report stated that, at that time, we had 1,800 cases of suspected counterfeits, involving more than one million parts, in our military supply chain. So this is not a good trend for a developed country or even the knowledge economy.
Your June report titled “Manufacturing prosperity: A bold strategy for wealth and national security” brings up the topic of wealth security. Can we realistically create jobs and wealth in the US given the stiff competition from low-wage countries and automation?
Let’s look at Germany. It is not a low-wage country: Wages in Germany are 40% higher than in the U.S. And they have stricter regulations. Their energy costs are significantly higher than ours. Somehow, Germany continues to have about $200 billion surplus in manufacturing compared with our $800 billion deficit.
By the way, Germany is also competing with the same low-wage countries that we do. And when it comes to automation, Germany has more robots per worker than us. It’s the same story with Japan and South Korea. Those two countries also have very robust manufacturing economies, create surpluses in advanced manufacturing, and they certainly have more automation than we do. When it comes to advanced manufacturing, these countries continue to have a strong, robust manufacturing sector, but we don’t.
The U.S. government invests about $150 billion in science and technology annually—significantly more than what other countries are investing in research. What else could the government do to create manufacturing jobs?
The U.S. government does an excellent job investing in basic research and science and technology. And, as you mentioned, we invest significantly in that area. And we still lead the world when it comes to scientific discoveries, inventions, publications and citations. But while being the best in the world in science is certainly critical it’s not sufficient to survive in the global economy because science is not engineering.
We need to build a national infrastructure in engineering and manufacturing R&D that parallels our scientific infrastructure. We should continue to invest in basic research for sure, but there is a need to invest in translational research. And that is the government’s role. And that is because, our private sector, while obsessed with short term profit, has very little appetite for long term investments and translational R&D that is needed to mature nascent-but-promising ideas developing from our tax-payer-funded basic research at our universities and federal labs.
And that would be the situation with venture capital, right?
Absolutely. We have very strong venture capital community, but much of that money goes into software and biotech. That’s all well and good. But the point is, less than 4% of VC funding in the U.S. is directed toward hardware. That’s a market failure that the government needs to address.
Moreover, investing in basic research and leaving everything else to the magic hand of the free market has not worked for decades. And some insist that we should not be picking winners and losers, but we are letting other nations pick our winners.
Industry executives and research organizations are willingly giving away our advanced technologies to other countries because they have ability, the know-how, the money, and are willing to take risks to invest and scale these technologies.
We cannot continue to ask American taxpayers to subsidize R&D for other countries. We should continue to do the good things we are doing in basic research. But the government also needs to step in and invest in translational R&D. It is critical that the government has a strategy on what to do with the promising results from its investment in basic research. And not just the federal government; states also can play a role.
What are the gaps in our innovation ecosystem and how do we fix them?
As I said, manufacturing and innovation are intricately linked—in a cycle of innovation.
Think of the cycle of innovation as a baseball diamond. Through government’s investment in basic research you get to the first base of scientific discoveries and engineering inventions. Second base is where you create startups and develop prototypes to mature promising technologies. Third base is the scale up to pilot production. And home base is manufacturing at scale.
The government invests in basic research to get you to first base—and leaves the rest to the free market. And that’s how we hit singles, sometimes doubles. But that’s not enough to score. You’ve got to go around a complete circle to score a run to get a return on investment.
There are at least four innovation gaps.
The first one is, nearly 50% of our engineering graduate students across the nation are foreign students. That’s great but nowadays they are increasingly returning to their home countries. It’s unfortunate that we are losing the talented people to whom we provide a great education and research experience in emerging technologies. So, one of the recommendations we made in our report is to increase the fellowships for qualified domestic graduate students at the universities.
Another gap is more and more of our talented faculty in science and engineering are being attracted to Asia, particularly China, to set up research labs. This often happens after a faculty member has established a strong program in the cutting-edge research funded by one or more federal agencies. But what happens is, once the technology is proven, the funding dries out. So you can’t blame them for setting up advanced research labs overseas, in countries willing to invest to further develop the technology.
Now when you come to the startup, to the second base, only a small fraction of our basic research leads to promising discoveries and inventions that are demonstrated at labs here. So in the next step you create a start-up. But, again, it’s very difficult to get funding for startups. The result is that many of our discoveries and inventions are languishing in our university tech-transfer offices. Funding dries up and then the researchers move on to the next topic.
So, we recommend investing an additional 5% of our basic research funds into what we call translational research centers. These are university-affiliated centers but run privately by experienced engineers and business leaders—to work with small and medium-sized companies to develop and commercialize the technologies coming out of our research labs.
Finally, even for the ones who make it through the startup phase, there’s another gap when it comes scaling up. There are many examples where the technology is ready for full scale manufacturing and the right thing to do is to go to South Korea, Japan or China because that’s where the manufacturing know-how is. That’s where the equipment, skills and talent are. So we have very few, if any, that are being scaled in this country.
The report (tinyurl.com/mfgProsperity) calls for a significant investment in engineering and manufacturing research, as you’ve noted. How much does it cost if we implement all four recommendations? And is there really an appetite for more government spending in this political and budget climate?
Yes. Our government invests significantly in basic research and not very much in engineering and manufacturing R&D. And science is not engineering; there’s a big difference. Engineering is what turns an abstract idea into a tangible product. So in fact what we perceive as rocket science is actually rocket engineering.
Going back to Germany as an example, the German government invests about six times as much as we do in a particular category called industrial production and technology. This is engineering and manufacturing research. Even though Germany’s total science and technology budget is about a quarter of what we spend, in this particular area, they invest six times as much as we do. And you see similar investment trends in Japan and South Korea.
So when you talk about investing $150 billion here in science and technology, about 5 percent of that should be a reasonable number to invest in engineering and manufacturing R&D.
That’s like an insurance policy to make sure the great ideas that are coming out of our research will trickle down to help the economy and national security. So it may cost $7 billion a year in investments in engineering and manufacturing R&D across the board. According to recent estimates, we are losing about $2 billion-$3 billion a year to China alone in trade deficits and IP theft.
We need to make that serious investment—if we are serious about leadership in future technologies and in national security, in engineering and manufacturing R&D.
There should be an appetite for this because manufacturing is one of the few topics that actually has bipartisan support. We need bold steps and investments that are proportional to the challenges we are facing right now. Other nations have big ideas, big strategies. They are not standing still. So the onus is really on us.
Your report discusses creating demand, not just supply. How do we do that in a democratic society?
Going back to the scale-up challenge, our government in general, and the Department of Defense in particular, can serve as early adopters. We have done this before. That’s what enabled us to kick-start the aerospace industry, semiconductor industry, computers, the internet and GPS, just to name a few. And we can do it again.
If you have a promising battery technology that, let’s say, meets DoD requirements, and if they are willing to buy half a million of your first batteries, you can take that letter to the bank and raise capital and then start pilot production to fine tune your manufacturing processes and ultimately commercialize.
That’s the kind of thing we’ve got to do. We need a strategy and coordination across the federal government to bring to bear the investments we are already making in R&D, in startups, in early adoption, in loan guarantees and export support.
Companies are rightly concerned about the lack of a skilled workforce in the U.S. How severe do you see this shortage as being, and how do we fix that?
We see time and again something like 600,000 unskilled positions in manufacturing fields because the baby boomers are retiring and millennials show declining interest in manufacturing. And some claim there likely will be two million jobs openings in the coming years looking for skilled workers.
To me, it’s not clear if employers are unable to find production workers and engineers at wages they are willing to pay, or if there simply are not enough skilled workers available to fill these positions. If it’s the former, you can increase the salaries to attract workers. It’s something the oil and gas industry has done. On the other hand, if there are just not enough skilled workers, I think the private sector should really reinstate what they have done before: training programs, internships, apprenticeships within their organization and attractive salaries. And the employers who are willing to take the long road should work with local universities and community colleges and establish the needed curriculum and create the demand for graduates of such programs. Some progressive companies are already doing this. But others should follow suit.
How are translational research centers different from manufacturing innovation institutes that came about under the Obama administration?
The institutes are meant to fill the gap between the basic and applied research. The private sector, at least in the manufacturing sector, mostly invests in incremental innovation or product development, what they call applied research, and rightly so to make the product more competitive. Industry has little appetite for long-term investment in translational research to take the emerging technologies to the next step beyond university labs. So, the focus of manufacturing institutes and the proposed translational research centers is in translational R&D.
The manufacturing institutes specialize in a particular emerging technology like flexible electronics. Their purpose is to make sure the technology readiness levels are there and then to establish the knowledge, skills, infrastructure and the supply chain needed to anchor manufacturing of the technology in the U.S.
The translational research centers the report recommended are more distributed. They are broader in scope but much smaller in size. These non-profit entities are affiliated with one or more universities working on a wide variety of ideas coming out of university labs. They will choose which technology ideas to invest in to demonstrate prototypes, etc., to reduce technical and market risks.
What is the impact of robotics and automation and on the loss of manufacturing jobs in the U.S.?
We lost more than five million jobs in the last decade in this country. We did not lose them because of robots or automation. We lost them because of offshoring. Since the 1970s, robots have substituted for workers in performing routine and codifiable, structured tasks. These are low-skilled, repetitive tasks. Automation will continue to evolve as it has since the ’70s. The dull, dirty and dangerous jobs were automated back in the ’80s and ’90s. And whatever was remaining, they were off-shored in the last two decades.
But the new generation of robots are not really caged and fenced like the ones in automobile painting and assembly areas. They are working side by side with humans. They are easier to deploy and less expensive. And if you deploy these robots sensibly, you can certainly enhance productivity of human operators, and you can create new opportunities for businesses.
Compared with advanced manufacturing nations like South Korea and Germany, if you look at robot density, for every 10,000 manufacturing workers, we have shy of 200 robots. Germany has 300. Japan has well over 300. South Korea has 630. So these countries, which have strong, advanced manufacturing sectors, have more robots than we do.
How do you see smart manufacturing making the U.S. manufacturing sector more competitive, other than the robots?
Smart manufacturing is an “umbrella” concept. It includes a number of things in addition to robotics and automation: modeling and simulation, data analytics, virtual and augmented reality, and integrated communication networks for collaborative systems within a single organization and with your suppliers and customers.
A simple definition of smart manufacturing would be any time decisions that are informed by data. Emerging digital technologies, such as vibration, temperature, and load sensors, make collecting the data needed to inform decisions much easier. But that data needs to be analyzed and presented in accessible formats (often called dashboards) in real time. Small firms with just one plant can take advantage of this technology, particularly since it keeps getting cheaper.
In companies with multiple plants that want to connect with suppliers, communication networks can share data and analytics—and respond rapidly. As machine intelligence improves and proliferates, these responses will be made autonomously, based on overarching business objectives. The results will be less waste, faster response to shifting customer demand and lower cost with more variety.
Other technologies, such as virtual and augmented reality, applied to product and facility design, will be used for maintenance and training and make factory jobs even more attractive.
Many of these technologies are available now, while others will continue to be developed and improved. But, like robotics, the U.S. cannot afford to be left behind.
While the large OEMs are making the necessary investments—some more than others—it’s really important for small and medium-sized manufacturers to adopt these technologies. These companies need to be aware of what can be done, to understand how affordable many of these technologies have become and to know the benefits to their operations.
In fact, MForesight is starting a new project, targeting small and medium-sized manufacturers.
We’ve been told there’s a gap in the information appropriate for and available to this group, so we will fill it. Our plan is to define the buzzwords, make the technology understandable, describe how smart manufacturing can alleviate the pain points typically found in these factories and tell them about the resources available to help them adopt and embrace the technologies that are appropriate to their situation.
Most of their information now comes from someone trying to sell them something. MForesight can provide honest, unbiased information that we hope will accelerate the pace of implementation.