Automation vs. Innovation
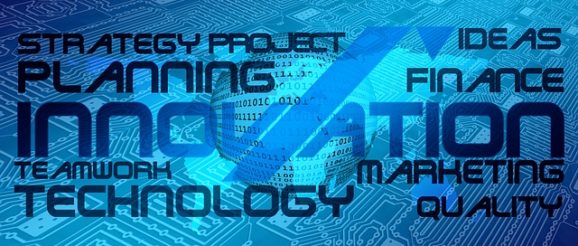
We don’t yet know how to make computer software that is as flexibly smart as human brains. So when we automate tasks, replacing human workers with computer-guided machines, we usually pay large costs in flexibility and innovation. The new automated processes are harder to change to adapt to new circumstances. Software is harder to change than mental habits, it takes longer to conceive and implement software changes, and such changes require the coordination of larger organizations. The people who write software are further from the task, and so are less likely than human workers to notice opportunities for improvement.
This is a big reason why it will take automation a lot longer to replace human workers than many recent pundits seem to think. And this isn’t just abstract theory. For example, some of the most efficient auto plants are the least automated. Read more about Honda auto plants:
[Honda] is one of the few multinational companies that has succeeded at globalization. Their profit margins are high in the auto industry. Almost everywhere they go — over 5 percent profit margins. In most markets, they consistently are in the top 10 of specific models that sell. They’ve never lost money. They’ve been profitable every year. And they’ve been around since 1949. …
Soichiro Honda, the founder of the company … was one of the world’s greatest engineers. And yet he never graduated college. He believed that hands-on work as an engineer is what it takes to be a great manufacturer. …
One of the early Formula Ones, Honda was embarrassed because the car they put out went up in flames. … Soichiro … he went back to the man who designed it and interviewed him. This guy had never tested these pistons, had never talked to race car engineers, never been on the ground to test pistons in the conditions they would, never even talked to race car drivers to find out how the car felt. He didn’t go to the spot, as Honda would put it. That kind of intellectual or design laziness really bothered him. And he embarrassed this man completely. He made him go around and apologize to everyone in the company one after another, holding the burnt piston. Now this man, however, also went on to design the next year’s cars, and those cars came in first place. And this man became head of Honda in North America. …
Honda believed that you have to argue all the time. You have to see both sides of every issue. Most companies have a difficult time with this. … I’ve been at factories where suddenly you see a group of workers standing together and not so much yelling but talking over each other. … They argue over every little piece of why it’s not fitting right, what they’ve seen in other places, what they could do better. …
So today the thing that stands out is that Honda can make any number of cars on the same assembly line, one after another. They can have a Civic and then an Odyssey or Pilot follow on the same assembly line. No one else has a flexible assembly line like that. … every time Honda does something, like build a factory, they’re building from scratch. Again, it’s on the ground: Go look at what we’ve been doing. Learn from it. Then build something else. … The Lincoln, Ala., plant, … is one of the most productive and flexible auto plants in the world. Uniquely, instead of setting up assembly line stations, where one person puts in the dashboard, the next station will put the radios in, and the next one will put the steering wheel in, at Honda they have zones of workers, so the zones put in five or six things. ..
Because of the flexibility, they are one of the least automated factories. Because they need human beings to work on these cars. If you’re going to have a robot put in a dashboard that has differences from one car to the next, you have to change the arms of the robot for every car. That can take hours.
Some would say that Honda not being automated and having more workers would hurt productivity. But it just shows what they make up for in flexibility. Again, their profit margins are better than anyone in the industry.
They do automate things once they feel like it has become a commodity. But once you automate, you can never improve anymore. A robot will never tell you, “Hey, I could do this better.” …
In most [firms] R&D, design, engineering, all of those critical aspects of the vehicles are still determined at the home office. Honda sets up an autonomous subsidiary operation wherever it goes. So, Honda China, Honda of North America, Honda Europe are each independent. … Quickly, they’re running on their own and developing cars and designs for the local market. … Each market determines for itself which cars it’s going to sell, which new designs they want to make. How they’re going to run their operations. How they’re going to build their factories. …
Around every major factory they have a research and development team and an engineering team. So that if they need something designed, or if they make a new model, and the factory is beginning to produce it, the R&D team is right there through the whole process of the production of the car. In most companies, R&D designs the car and it gets passed to manufacturing and R&D is out of the process. …
Honda doesn’t want their suppliers to be exclusive to Honda. That would only create a sense of “give Honda what it wants.” What Honda wants instead is to get new ideas all the time — not the ideas they know about but the ideas they haven’t thought about yet. (more)