Realizing a resource-autonomous circular economy through material innovation – The European Sting – Critical News & Insights on European Politics, Economy, Foreign Affairs, Business & Technology – europeansting.com
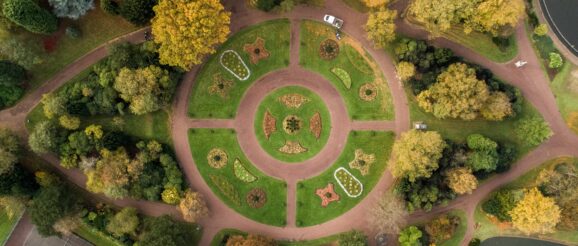
This article is brought to you thanks to the collaboration of The European Sting with the World Economic Forum.
Author: Nobuyoshi Yamasaki, Founder and Chief Executive Officer, TBM
- In March 2023, the Japanese government announced its Resource-Autonomous Circular Economy growth strategy to efficiently use natural resources and maximize recycling.Developing a new circular economic model focusing on resource autonomy will enable a stronger domestic industry in Japan by creating new industries and employment.The private sector, governments and academia must collaborate in technology-driven innovation to establish the circular economy as a growth industry worldwide.
In March 2023, Japan’s Ministry of Economy, Trade and Industry (METI) announced its Resource-Autonomous Circular Economy growth strategy to efficiently use natural resources and maximize recycling.METI switched to this circular economy growth strategy because the conventional ‘linear’ economic model places a heavy burden on the environment. Reducing greenhouse gas emissions through resource circulation is also a common goal and a global effort driven by the Paris Agreement.Japan has historically been poor in natural resources, but the supply constraints on goods and resources triggered by COVID-19 and the Russian-Ukraine war have highlighted the urgent need to secure stable resources within Japan or neighbouring regions.Efficiently recycling natural resources is the key to solving this issue. Developing a new circular economic model focusing on resource autonomy will realize a stronger domestic industry by creating new industries and employment. And, it will improve competitiveness in the global market
Creating a 3R + Renewable enabling society
Japan is looking to develop an efficient circular economy model through a collaboration between the manufacturing and recycling industries. The idea is to realize a 3R (reduce, reuse, recycle) + Renewable-enabling society. The focus is on developing resource-saving technologies and renewable materials, recyclable design and carbon recycling technology, such as carbon capture and utilization (CCU).One of the candidates for resource-saving technology and recyclable materials is LIMEX, a new limestone-based material developed by Japanese unicorn company TBM. Unlike petroleum, limestone is an abundant natural resource that can be sourced locally worldwide, including in Japan.
What is the World Economic Forum doing on manufacturing and supply chains?
The World Economic Forum Centre for Advanced Manufacturing and Supply Chains assists leaders from the public and private sectors in accelerating the adoption of inclusive technology. It focuses on fostering innovation, sustainability, and employment. Here are some examples of the impact delivered by the centre:The Global Lighthouse Network: This network unites 114 advanced manufacturing factories from various industries, enabling them to scale innovations. It also facilitates learning and collaboration opportunities.Circular value chains: The centre actively supports manufacturers in incubating new pilots that reinforce trust in circular value chains. It launched initiatives to strengthen the authentication of fashion products in second-hand markets and help companies reduce their carbon footprint by facilitating data exchange across supply chains.Resiliency: In partnership with Kearney, the centre has developed the Resiliency Compass. This tool offers a comprehensive set of measures to guide companies in navigating supply chain disruptions and enhancing resilience across their manufacturing and supply systems.Contact us for more information on how to get involved.
LIMEX is made from inorganic materials, calcium carbonate (CaCO3) derived from limestone is its main ingredient, making up more than 50% of its weight; other components include conventional or biomass-based resins and additives. Compared to plastic products, products made with LIMEX, such as bags and packaging, can reduce the consumption of petroleum and greenhouse gas emissions over the entire life cycle – from raw material procurement to disposal or recycling processes – when put through a life cycle assessment. In addition, LIMEX can be used for industrial applications, such as adhesive labels and construction materials, when formed into sheets.Moreover, compared to paper, LIMEX sheets use no wood pulp as a raw material and LIMEX is manufactured using approximately 97% less water.Many countries are not blessed with oil reserves, they depend on imports for plastic and do not have water resources for paper production. As limestone can be sourced even in such countries, local production of LIMEX is possible. LIMEX, therefore, can create new industries and distribute wealth in those countries. LIMEX, which realizes a compact supply chain using locally accessible limestone, has been introduced at international conferences, such as COP, G20 and G7, and can potentially contribute to creating a Resource-Autonomous Circular Economy model.
Nationwide efforts for technology-driven innovation
TBM also operates one of Japan’s largest mechanical recycling plants in Yokosuka City, for recycling LIMEX and plastic products. With TBM’s experience in developing and manufacturing new materials and the recycling business, TBM is calling out that cooperation between the manufacturing and recycling sectors is essential for efficient resource circulation.It is difficult, however, for individual companies alone to change the whole of society. Many products are still not designed to be easily recycled. The government needs to focus on creating rules that encourage recycling-conscious design. Initiatives supporting national policy and collaboration among government, academia and cross-industrial sectors will become increasingly significant.
Another example of the need for collaboration regarding resource circulation and technology development is CCU. CCU is a technology that captures CO2 and utilizes it as raw material for production. It is a solution for realizing carbon neutrality and also aligns with the concept of a Resource-Autonomous Circular Economy, by recycling locally emitted CO2 into a new material.Potential applications for CCU include chemicals, fuels, minerals and concrete. Of these, concrete is expected to be the closest to commercialization. The cement industry is Japan’s third-largest CO2 emitting industry, after power generation and steel, accounting for 4.5% of total domestic CO2 emissions. The industry is planning to produce CaCO3, the raw material for concrete, by synthesizing the collected CO2 with calcium.This should not be closed to a single industry or sector. In its Basic Policy for the Realization of GX (Green Transformation), the Japanese government is promoting the development of a wider range of products, other than concrete, using CaCO3 derived from CO2.LIMEX could be one of these new applications, as LIMEX is also made from CaCO3. In the near future, LIMEX will be made not only from CaCO3 derived from limestone, but also from CaCO3 derived from CO2 and it will evolve into a material with a lower environmental impact.
Private sectors, governments and academia must collaborate in technology-driven innovation beyond conventional waste management and environmental measures to establish the circular economy as a growth industry and not just a concept.
At the same time, the manufacturing industry must design a recycle-oriented business and be responsible for the end life of its products. While, the recycling industry must transform its business model to a ‘resourcing industry’, not only to simply recycle waste, but also to stably supply high-quality recycled materials through collecting various used products widely. This business model transformation is the path to establishing an
In March 2023, Japan’s Ministry of Economy, Trade and Industry (METI) announced its Resource-Autonomous Circular Economy growth strategy to efficiently use natural resources and maximize recycling.METI switched to this circular economy growth strategy because the conventional ‘linear’ economic model places a heavy burden on the environment. Reducing greenhouse gas emissions through resource circulation is also a common goal and a global effort driven by the Paris Agreement.Japan has historically been poor in natural resources, but the supply constraints on goods and resources triggered by COVID-19 and the Russian-Ukraine war have highlighted the urgent need to secure stable resources within Japan or neighbouring regions.Efficiently recycling natural resources is the key to solving this issue. Developing a new circular economic model focusing on resource autonomy will realize a stronger domestic industry by creating new industries and employment. And, it will improve competitiveness in the global market
Creating a 3R + Renewable enabling society
Japan is looking to develop an efficient circular economy model through a collaboration between the manufacturing and recycling industries. The idea is to realize a 3R (reduce, reuse, recycle) + Renewable-enabling society. The focus is on developing resource-saving technologies and renewable materials, recyclable design and carbon recycling technology, such as carbon capture and utilization (CCU).One of the candidates for resource-saving technology and recyclable materials is LIMEX, a new limestone-based material developed by Japanese unicorn company TBM. Unlike petroleum, limestone is an abundant natural resource that can be sourced locally worldwide, including in Japan.
What is the World Economic Forum doing on manufacturing and supply chains?
The World Economic Forum Centre for Advanced Manufacturing and Supply Chains assists leaders from the public and private sectors in accelerating the adoption of inclusive technology. It focuses on fostering innovation, sustainability, and employment. Here are some examples of the impact delivered by the centre:The Global Lighthouse Network: This network unites 114 advanced manufacturing factories from various industries, enabling them to scale innovations. It also facilitates learning and collaboration opportunities.Circular value chains: The centre actively supports manufacturers in incubating new pilots that reinforce trust in circular value chains. It launched initiatives to strengthen the authentication of fashion products in second-hand markets and help companies reduce their carbon footprint by facilitating data exchange across supply chains.Resiliency: In partnership with Kearney, the centre has developed the Resiliency Compass. This tool offers a comprehensive set of measures to guide companies in navigating supply chain disruptions and enhancing resilience across their manufacturing and supply systems.Contact us for more information on how to get involved.
LIMEX is made from inorganic materials, calcium carbonate (CaCO3) derived from limestone is its main ingredient, making up more than 50% of its weight; other components include conventional or biomass-based resins and additives. Compared to plastic products, products made with LIMEX, such as bags and packaging, can reduce the consumption of petroleum and greenhouse gas emissions over the entire life cycle – from raw material procurement to disposal or recycling processes – when put through a life cycle assessment. In addition, LIMEX can be used for industrial applications, such as adhesive labels and construction materials, when formed into sheets.Moreover, compared to paper, LIMEX sheets use no wood pulp as a raw material and LIMEX is manufactured using approximately 97% less water.Many countries are not blessed with oil reserves, they depend on imports for plastic and do not have water resources for paper production. As limestone can be sourced even in such countries, local production of LIMEX is possible. LIMEX, therefore, can create new industries and distribute wealth in those countries. LIMEX, which realizes a compact supply chain using locally accessible limestone, has been introduced at international conferences, such as COP, G20 and G7, and can potentially contribute to creating a Resource-Autonomous Circular Economy model.
Nationwide efforts for technology-driven innovation
TBM also operates one of Japan’s largest mechanical recycling plants in Yokosuka City, for recycling LIMEX and plastic products. With TBM’s experience in developing and manufacturing new materials and the recycling business, TBM is calling out that cooperation between the manufacturing and recycling sectors is essential for efficient resource circulation.It is difficult, however, for individual companies alone to change the whole of society. Many products are still not designed to be easily recycled. The government needs to focus on creating rules that encourage recycling-conscious design. Initiatives supporting national policy and collaboration among government, academia and cross-industrial sectors will become increasingly significant.
Another example of the need for collaboration regarding resource circulation and technology development is CCU. CCU is a technology that captures CO2 and utilizes it as raw material for production. It is a solution for realizing carbon neutrality and also aligns with the concept of a Resource-Autonomous Circular Economy, by recycling locally emitted CO2 into a new material.Potential applications for CCU include chemicals, fuels, minerals and concrete. Of these, concrete is expected to be the closest to commercialization. The cement industry is Japan’s third-largest CO2 emitting industry, after power generation and steel, accounting for 4.5% of total domestic CO2 emissions. The industry is planning to produce CaCO3, the raw material for concrete, by synthesizing the collected CO2 with calcium.This should not be closed to a single industry or sector. In its Basic Policy for the Realization of GX (Green Transformation), the Japanese government is promoting the development of a wider range of products, other than concrete, using CaCO3 derived from CO2.LIMEX could be one of these new applications, as LIMEX is also made from CaCO3. In the near future, LIMEX will be made not only from CaCO3 derived from limestone, but also from CaCO3 derived from CO2 and it will evolve into a material with a lower environmental impact.
At the same time, the manufacturing industry must design a recycle-oriented business and be responsible for the end life of its products. While, the recycling industry must transform its business model to a ‘resourcing industry’, not only to simply recycle waste, but also to stably supply high-quality recycled materials through collecting various used products widely. This business model transformation is the path to establishing an