Technology, innovation drive local manufacturers to become smarter, more data-driven enterprises
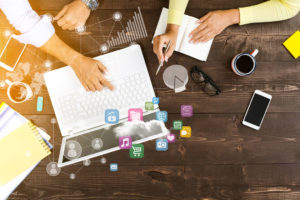
By Chris Yarrow
Co-founder and managing partner, The Hiring Group
The marketplace of the 21st century is evolving into one of merging national markets, fragmented consumer markets, and rapidly changing product technologies.
Manufacturing is a key part of the DNA of the Upstate, but manufacturing is no longer just about making physical products. Technology and innovation are driving local manufacturers to become smarter, more data-driven enterprises.
The demand for highly skilled manufacturing engineers and technical workers continues to rise as technology, automation, and more advanced manufacturing practices are adopted.
Hiring for these critical positions is challenging, especially for the companies with deeply ingrained processes and industrial-focused environments. Here are several key considerations for manufacturers that are impacting recruiting, hiring, and culture here in the Upstate.
The modern workforce
Upstate manufacturing organizations must re-evaluate their hiring and retention strategies to effectively compete in the high-demand hiring marketplace.
An entire generation of engineering and technical talent is moving toward retirement, which means manufacturers must attract and hire new talent to fill in the skills gap or chance losing years of knowledge capital. In the Upstate, companies face this reality as demand for highly skilled IT and engineering resources is driving more competitive job offers, richer benefits, and more perks overall.
Manufacturing organizations must not only align their hiring strategies to attract and hire the best and brightest, but also add programs that focus on continued development. Today’s technical and engineering workforce is eager to work on new, challenging projects that are tied to key corporate initiatives. Companies that implement programs to expose employees to cutting-edge technologies are at an advantage when it comes to recruiting the top IT and engineering resources.
Automation, tech and data are king
Technology and the digital transformation are changing the manufacturing landscape here faster than ever before. For manufacturers, investing in technology and data solutions delivers several benefits to all levels of the company. As knowledge and insight are gleaned by engineers, data scientists, and analysts from manufacturing systems, production-based workers in these companies also gain access to it.
Digital manufacturing affords more flexibility than conventional, linear approaches by allowing companies to plan and develop in tandem. Companies can quickly identify product shortfalls and address production changes to course correct immediately. Agile technologies, robotic automation, and 3D modeling solutions enable companies to configure and reconfigure operations faster at a lower cost. To leverage these innovations, companies should invest in training their existing workforce and continue to build a data-focused enterprise.
Compliance: Everyone’s responsibility
Across the globe, regulatory and security compliance remains a critical priority. The Upstate is no exception, as organizations face severe financial or operational penalties if found to be in violation. The need for compliance and documentation teams in manufacturing organizations continues to increase as companies strive to lower costs linked to penalties.
In addition to regulatory compliance, IT and data-security compliance for manufacturers also poses a great risk. According to a recent study by the Ponemon Institute, the average cost of a data breach globally is $3.86 million. For Upstate manufacturers, having resources and standards in place to protect enterprise data is critical, which means investing in IT and data security professionals to manage these business requirements to circumvent the risk of data breaches.
The future looks bright
The future of manufacturers here in the Upstate of South Carolina is bright. Technology and innovation are helping these companies improve their businesses to plan, build, produce, and distribute their products at a higher quality and more efficiently than ever before.
To stay ahead, local manufacturers should consider establishing new or updated methods to attract the most qualified, highly technical talent and keep them engaged and loyal. Leveraging technology and data to share across the organization will continue to bring shared value at all levels of the enterprise. Having the insight and visibility into people, processes, and technology will help these companies drive production, while also mitigating risk and driving overall productivity and revenue generation.
—
Chris Yarrow is a co-founder and managing partner of The Hiring Group (), a technical staffing and recruiting firm with clients across the U.S. Yarrow and his business partner, Brooks Israel, established The Hiring Group in 2014 and have become one of the nation’s fastest-growing staffing companies. The Hiring Group was recently named No. 130 on the Inc. 5000 list of fastest-growing businesses in the U.S. and was also named one of the 2018 South Carolina’s 25 Fastest Growing Companies.