Timber innovation center a chance to reinvigorate rural town | HeraldNet.com
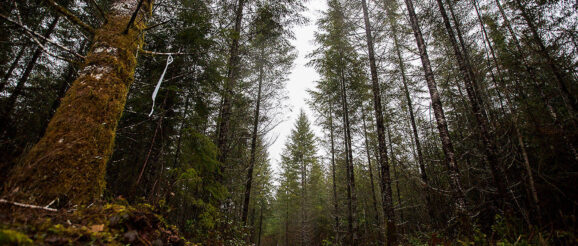
DARRINGTON — From the single-runway airport on the edge of town, nearby Gold Mountain was barely visible through sheets of rain.
Locals call the mountain “Gold Hill” because it’s a small mound compared to the rugged North Cascades peaks visible from town on a clear day.
“Welcome to Darrington,” Mayor Dan Rankin said with a laugh as he sloshed through ankle-deep puddles on property alongside the airport and next to the cemetery. “You deal with a lot of this, but it’s worth it to live here.”
The 94-acre wooded lot is the potential site for a timber innovation center that could bring 100 jobs, and more down the line, to Darrington.
For seven years, Rankin worked with county and state officials alongside environmental nonprofit Forterra to develop the Darrington Wood Innovation Center, a campus to house advanced wood manufacturers and promote education and conservation.
Rankin hopes the center will bring economic stability to Darrington, a rural town depreciated by a decline in the timber industry.
Since the late 1980s, Darrington lost about 90% of its timber-associated jobs, according to the Glacier Peak Institute. A massive reduction in access to timber on public land and environmental concerns like Spotted Owl habitat contributed to that decline. Automation in the timber industry also eliminated some jobs, Rankin said.
Darrington has the lowest average household income in all of Snohomish County at $44,583, according to the Economic Alliance Snohomish County.
Rankin started searching for ways to rejuvenate the town after the Oso slide — a tragedy that devastated his already-struggling community.
That’s when he and a handful of other community leaders discovered mass timber. It’s a strong, low-carbon alternative to concrete and steel built by sandwiching multiple solid wood panels together. While used in Europe and in Canada since the 90s, the technology is mostly new to the United States.
Seeing an opportunity for his timber community to plug into the manufacturing and construction world, Rankin started learning everything he could about a type of mass timber called cross-laminated timber (CLT).
At the same time, environmental nonprofit Forterra and Washington state looked at how the material could benefit the building industry and bring life to rural towns.
An access road leads into plot of land located in north Darrington that could potentially be used to build a 30-acre Wood Innovation Center, which will house CLT manufacturing and modular building companies. (Olivia Vanni / The Herald)
The future of timber
Rankin first envisioned the Wood Innovation Center in 2014.
He dreamt of an all-encompassing campus where manufacturers partnered with universities to invest in wood technology and innovation while training a skilled workforce.
“I want to see a job base that allows people to live, work and play right here at home where they don’t feel like they have to commute out of the valley to have successful and meaningful work,” Rankin said.
A path forward took shape with the help of Forterra and Linda Neunzig, the county’s agriculture coordinator.
It took them a year to build out a business plan, with help from a Department of Commerce grant that paid for feasibility studies.
The grand total for the first phase of the center came to $8.14 million.
“Small town mayors don’t deal with eight million dollar projects often,” Rankin said.
In early 2019, the project received a $2 million state grant.
That was the tipping point, Rankin said.
“We’ve worked so hard to make this happen,” Neunzig said. “We pinch ourselves that we’re really there.
Another key piece fell into place earlier this month when the state Department of Natural Resources transferred 3.75 acres of land to the Town of Darrington to make way for an entrance to the center.
“The Darrington Wood Innovation Center represents the future of forest products in Washington state,” Commissioner of Public Lands Hilary Franz said.
There’s still another $6 million of grant funding in flux. If that money comes through, Rankin said they plan to break ground later this year.
Phase one develops the innovation portion of the center. About 30 acres will host a CLT manufacturer as well as an adjoining modular construction facility using the CLT to build multifamily housing throughout the region. That phase is expected to provide 100 jobs, Rankin said.
The next phase involves building out an additional 30 acres to include education and wood innovation, although there are no solid plans for how to achieve that yet. They are partnering with Washington State University to investigate how the Snohomish County Extension could fit into those plans, Rankin said.
“My dream would be to have university and state college involvement in wood technology and environmental education,” Rankin said. “To be able to provide an outdoor, real-time, in-the-woods classroom is an opportunity that not everybody has.”
The remaining 30 acres will be preserved for environmental conservation, with access to Whitehorse trail and Whitehorse County Park. That piece is funded by a $140,000 grant from the Snohomish County Conservation futures program.
Legos on steroids
CLT has rapidly gained popularity as a building material in North America.
It was first patented in the United States, and industrialized in Europe in the early ’90s, said Bernhard Gafner, a partner at Aspect Structural Engineers. He built one of the first CLT buildings in North America in 2008.
The material is created by laying boards together in perpendicular layers and securing them with glue. Panels can be up to 60 feet long and 10 feet wide, with anywhere from three to 11 layers of wood.
It’s a lot like plywood, but using lumber instead of veneer, Rankin said.
After the panels dry, they’re manufactured into pieces that fit together to make a building.
Up until this past year, U.S. building codes capped buildings constructed with mass timber at five to six stories. But the most recent building codes rolled out in 2020 allow up to 18 stories.
Researchers herald mass timber, and specifically CLT, as one of the most promising new building materials — it’s environmentally friendly as well as fire and earthquake-resistant.
With CLT, renewable timber can take the place of steel and concrete, materials made by burning fossil fuels.
CLT buildings still use steel fasteners and concrete foundations, but the need for traditional materials is greatly reduced.
Timber also doesn’t release carbon when it’s harvested, instead sequestering the gas inside lumber.
CLT also requires fewer resources in the construction process. It’s lighter to transport and takes less time to assemble, Rankin said.
“Everything is reduced,” he said.
CLT is prefabricated into large components that fit together even before they reach a construction site. So when they arrive, it’s like putting together a Lego set on steroids, Rankin said.
That reduces the cost of labor, making CLT an ideal material for affordable housing, Gafner said.
Because the panels are one piece, they’re more fire-resistant than traditional wood framing. The CLT will char on the outside, like a big log in a bonfire, but it won’t catch fire as quickly as smaller pieces of wood.
It’s also relatively easy to manufacture CLT in accordance with seismic codes, Gafner said.
Wood in general performs well in earthquakes because it’s flexible.
CLT is constructed with relatively minimal lumber, Rankin said.
According to a University of Washington, Washington State University and Forterra projection, the demand for lumber to manufacture CLT panels over the next 15 years represents less than 1% of the annual Pacific Northwest timber harvest.
Rankin said he’s dedicated to ensuring the center’s lumber is harvested sustainably — that’s something Forterra is invested in as well.
In the context of mass timber, that means harvesting timber “without interrupting ecological corridors to the extent that the harvest becomes detrimental to the long-term conservation of our diversity,” Toby Levy, vice president of real estate transactions at Forterra, said. “Then we have used our natural resources in a way that contributes to a climate change solution.”
Rankin also hopes the center will help close the urban-rural divide and give a “farm to table” twist to timber.
“Everyone knows their flour comes from farms and their wood comes from rural areas,” he said. “But having this created in a small community and erected in urban areas draws that connection a little bit closer.”
There are still a few hurdles to clear before the center is a done deal. Darrington needs to close on the 94 acres currently owned by Grandy Lake Timber company, a deal that hinges on final approval of a $6 million federal grant. But even if just half what he envisions comes to fruition, Rankin said the center will transform the outlook for many in Darrington and chart a road map for other rural towns.
“My dream is to have job diversity in our community where there are all levels of employment and all levels of mobility to be able to move in (this) industry through forestry, timber extraction and manufacturing,” he said. “All of those things begin to offer not only our community but the surrounding communities a place to grow in knowledge and as individuals.”
Julia-Grace Sanders: 425-339-3439; [email protected]; Twitter: @sanders_julia.
Talk to us
Darrington Mayor Dan Rankin stands alongside land in north Darrington that could potentially be used to build a 30-acre Wood Innovation Center. (Olivia Vanni / The Herald)