How REMADE could drive innovation in circular manufacturing techniques
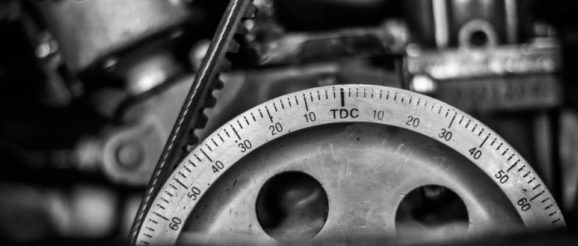
The challenges involved in converting the global economy from linear to circular processes and consumption habits are massive, multi-faceted and multi-dimensional.
Considering the technological, policy, marketing, logistical and infrastructural innovations that will be required, it is clear that the solutions will be bigger than any one player — or even any one group of industry-specific collaborators — can orchestrate. Such a monumental challenge requires a monumental effort.
The REMADE Institute is one such effort, funded with $70 million from federal funding sources and $70 million from its various members. Composed of 26 universities, 44 companies, seven national labs and 26 industry trade associations and foundations, it’s the largest and most comprehensive effort (at least in the United States) focused primarily on addressing the changes required to retool remanufacturing processes for the circular economy.
That includes finding ways of expanding the list of recyclable materials and improving the efficiency with which they can be extracted and reprocessed, as well as improving processes for remanufacturing products from recycled cores, which is what the products are called when they are returned at the end of their life.
REMADE is also looking for ways to reduce industrial greenhouse gas emissions, which today comprise 21 percent of the global total, making it the third largest sector.
While many of these issues are being addressed by individual companies as well as consortia such as Project Effective in Europe, the REMADE Institute intends to engage a broader scope of players in its endeavor to “dramatically reduce the embodied energy and carbon emissions associated with industrial-scale materials production and processing.” Participating companies include Caterpillar, John Deere, Alcoa, Davies Industries, Unilever, Nike, First Solar and Michelin.
The institute (the name derives from the phrase Reducing EMbodied-Energy and Decreasing Emissions ) is specifically charged with finding new and less expensive ways to reuse, recycle and remanufacture metals, fibers, polymers and electronic waste. Here are some of its specific targets:
- Reduce primary feedstock consumption in manufacturing by 30 percent
- Achieve 25 percent reduction in embodied energy of targeted materials
- Achieve cost parity for secondary (recycled) materials
- Improve energy efficiency of secondary material processing by 30 percent
- Increase the size of the remanufacturing industry by 100 percent
Just how big is the remanufacturing segment today? REMADE CEO Nabil Nasr, who also is the director of the Golisano Institute for Sustainability at the Rochester Institute of Technology (RIT), said remanufacturing generated $43 billion in 2012. It employs 180,000 people.
In developing the institute’s operating structure, the team chose not to organize activities by material types. Instead, it opted to focus on how to transition processes in these five functional areas:
- Systems analysis and integration
- Design for reuse/disassembly
- Manufacturing material optimization
- Remanufacturing and reuse
- Recycling and recovery
In a sense, this is a new industry with new processes and requiring new equipment and new skills. So the early-stage research prioritized by REMADE is intended to provide a proving ground that ultimately can grow these new disciplines and capabilities to levels commensurate with conventional manufacturing practice.
At the administrative level, the institute operates as a grant-maker, soliciting proposals from within its membership that are focused on offering solutions relevant to each of the five functional areas listed above. Selected proposals receive funds, as well as oversight resources.
Twenty selections from the first round of 106 proposals recently were chosen to receive funding. A few examples help to illustrate the kinds of efforts that REMADE is supporting:
- A framework for managing end-of-life solar technologies: Given that the first solar installations will be approaching the end of their useful life in the near future, it’s not too soon to consider how these materials will be managed when those installations are replaced or deconstructed. A project backed by University of Pittsburgh, University of California, Irvine, First Solar and the National Renewable Energy Laboratory is exploring a new solar design framework that will incorporate material recovery from the outset.
The use of collaborative teams from academia, industry and the national labs improves the chances of developing solutions with broad applicability. “Local optimization does not always lead to global optimization,” Nasr said. “Here, we’re comprehensively looking at the whole system and defining broad goals. Before this, you wouldn’t see people working in recycling technology, and manufacturing and design, all working on the same projects.”
What’s in it for the companies?
Caterpillar has been in the business of remanufacturing for over 20 years. Today, it remanufactures some 2 million components annually, which equates to some 148 million pounds of iron across a broad range of parts ranging from flywheels to fuel injectors to complete engines, according to the company’s website. Caterpillar recognizes that a lot more recoverable value can be gained from an old engine by tearing it down and rebuilding it, and adding new components where needed, than in simply melting it down and starting over from scratch. The result is considerably less resource usage and better value all the way around.
Over the 20-plus years, the company’s ability to recapture value from remanufactured items has continued to grow. One of REMADE’s funded projects — in which Caterpillar is participating along with RIT and CoreCentric, a company that specializes in “reverse logistics supply chain service solutions”— is called “Condition Assessment of Used Electronics.” The aim of the project is to expand upon the ability to assess electronic parts being returned for their remaining useful life, using automation. This could help Caterpillar expand the portfolio of parts that it effectively can recover.
SunnKIng, a western New York company that specializes in collecting, processing and redistributing electronic equipment at its end of life, is also working REMADE to rethink its business model. Matt Plummer, environmental, health and safety compliance manager for SunnKing, said the company began life by identifying usable items and selling them on eBay. From there, the organization evolved into a repair facility with extensive sorting capabilities. Today SunnKing recycles 25 million pounds a year, including a significant amount of toxic metals and other dangerous substances. It’s a private company performing a largely public service.
The business model is a challenging one, especially given the continually fluctuating prices of commodities such as metals. SunnKing’s REMADE project is called “Evaluation of Logistics Systems for Collection, Reprocessing, and Production of Secondary Feedstocks from e-Waste.” Under the initiative, SunnKing will partner with Idaho National Lab, which has done extensive work on e-waste recovery. The processes they develop could allow companies such as SunnKing to operate far more efficiently, according to the institute.
Through projects such as these, REMADE is poised to make substantial contributions to the science and art behind the circular economy. With four years remaining in its DOE grant (after which the organization intends to become self-sustaining), you can expect to see much more.